Gotowe Zbrojenie Płyty Fundamentowej 2025: Kompleksowy Przewodnik
Zaczynając przygodę z budową domu, wielu inwestorów i wykonawców staje przed kluczowym wyborem dotyczącym fundamentów – serca przyszłego budynku. Jednym z nowocześniejszych podejść, które zyskuje na popularności, jest gotowe zbrojenie płyty fundamentowej. Ale co to właściwie oznacza w praktyce i dlaczego warto się nad tym pochylić? Krótko mówiąc, gotowe zbrojenie to prefabrykowane, czyli przygotowane poza placem budowy, elementy stalowe (siatki, kosze, strzemiona, pręty gięte), które wystarczy dostarczyć i ułożyć na miejscu zgodnie z projektem, eliminując znaczną część prac ręcznych związanych z cięciem i gięciem stali zbrojeniowej bezpośrednio na budowie. Brzmi jak oszczędność czasu i nerwów, prawda? Zanurzmy się głębiej w świat prefabrykowanych elementów zbrojeniowych i sprawdźmy, czy faktycznie warto postawić na to rozwiązanie.
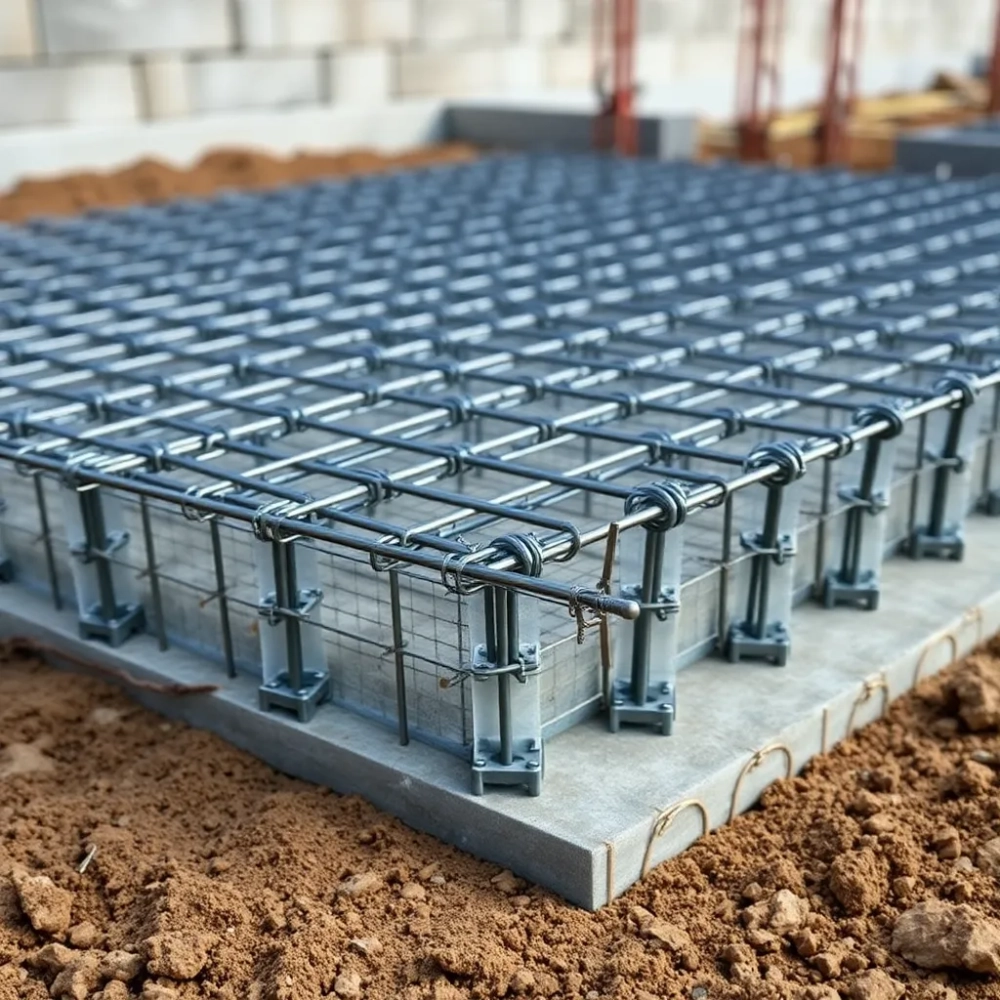
Decyzja o wyborze metody zbrojenia płyty fundamentowej ma znaczący wpływ na cały proces budowy, od harmonogramu prac po finalne koszty i trwałość konstrukcji. Analizując dane z różnych projektów realizowanych w ostatnich latach, widać wyraźne tendencje. Porównując standardową metodę "cięcie-gięcie-wiązanie na placu" z zastosowaniem gotowych elementów, szczególnie w przypadku płyt o regularnych kształtach, pojawiają się interesujące wnioski, które przedstawia poniższa tabela.
Parametr | Metoda Tradycyjna | Gotowe Zbrojenie | Różnica (%) / Komentarz |
---|---|---|---|
Czas montażu zbrojenia | 4-7 dni (dla ~100m²) | 2-4 dni (dla ~100m²) | Redukcja czasu o 30-50% |
Ilość roboczogodzin | Intensywne | Mniej intensywne | Potencjalnie 20-40% mniej |
Ilość odpadu stali | 5-10% | 1-3% | Znaczna minimalizacja |
Dokładność wymiarowa | Zależna od zespołu | Wyższa (produkcja w kontrolowanych warunkach) | Zwiększona powtarzalność |
Potrzeba miejsca na placu | Duża (składowanie, warsztat) | Mniejsza (gotowe pakiety) | Usprawniona logistyka |
Koszty bezpośrednie materiału | Zmienne (ceny prętów, siatek) | Zwykle wyższe (jednostkowo za kg) | Może być kompensowane mniejszym odpadem |
Koszty pośrednie (praca, sprzęt) | Wyższe | Niższe | Całościowa optymalizacja |
Analizując powyższe dane, staje się jasne, że gotowe zbrojenie wpływa diametralnie na dynamikę pracy na budowie. Redukcja czasu montażu to nie tylko szybszy postęp prac, ale także mniejsza ekspozycja odkrytego wykopu na zmienne warunki atmosferyczne, co jest kluczowe dla stabilności podłoża. Co więcej, mniejsza ilość odpadu stali to nie tylko korzyść ekologiczna, ale i ekonomiczna – kupujemy dokładnie to, czego potrzebujemy, minimalizując straty na placu budowy. To podejście przekłada się również na wyższą, przewidywalną jakość, ponieważ prefabrykacja odbywa się w warunkach fabrycznych, pod ścisłą kontrolą, co ogranicza ryzyko błędów, które mogłyby wyniknąć z ręcznego gięcia czy niedokładnego związania na budowie.
Zalety i wady gotowego zbrojenia do płyty fundamentowej
Podejmując decyzję o wyborze zbrojenia do płyty fundamentowej, stajemy przed klasycznym dylematem: co zyskujemy, a co ryzykujemy? Gotowe zbrojenie to niczym dwustronny medal, oferujący znaczące przyspieszenie i przewidywalność, ale niosący też pewne ograniczenia, które warto rozważyć z chłodną głową, zanim zlecimy produkcję.
Głównym, i często najbardziej kuszącym, atutem jest szybkość montażu gotowych elementów. Wyobraźmy sobie tradycyjny plac budowy, gdzie kilku zbrojarzy godzinami tnie, gięte i wiąże pręty według rysunków. Teraz zestawmy to z dostawą precyzyjnie wykonanych, spakowanych segmentów, które trafiają na docelowe miejsce niemal "klik i gotowe". Ta zmiana to nie tylko oszczędność dni, a czasem nawet tygodni w harmonogramie budowy, ale i realne pieniądze, które przestajemy wydawać na wynagrodzenie ekipy zbrojarskiej czy wynajem dodatkowego sprzętu na ten etap.
Kolejną niepodważalną zaletą jest powtarzalność i wysoka dokładność wymiarowa prefabrykatów. Produkowane w warunkach kontrolowanych, zgodnie z cyfrowymi projektami, elementy zbrojenia charakteryzują się precyzją wykonania nieporównywalną z pracą ręczną na budowie, często w trudnych warunkach pogodowych. To gwarantuje zgodność z projektem konstrukcyjnym, co jest fundamentem (nomen omen) bezpieczeństwa całej budowli.
Minimalizacja błędów ludzkich na placu budowy to efekt uboczny tej dokładności. Mniej ręcznych operacji cięcia i gięcia oznacza mniejsze ryzyko pomyłki w długości pręta, promieniu gięcia czy rozstawie strzemion. W branży, gdzie każdy szczegół ma znaczenie, a błąd w zbrojeniu może skutkować poważnymi konsekwencjami dla konstrukcji, ten aspekt jest wart swojej ceny.
Gotowe zbrojenie często pozwala również na optymalizację kosztów materiału poprzez znaczną redukcję odpadów. Gdy zbrojenie jest produkowane w fabryce, proces cięcia jest zoptymalizowany komputerowo, co minimalizuje ilość skrawków. Na budowie, nawet przy najlepszych chęciach, zawsze pojawiają się odpady, które potem trzeba utylizować.
Logistyka placu budowy staje się prostsza. Zamiast ton prętów luzem, które trzeba składować, sortować i przetwarzać, na plac trafiają gotowe, skatalogowane pakiety. Wymaga to mniej miejsca na składowanie i mniej czasu na organizację pracy na etapie zbrojenia, co jest kluczowe na ciasnych działkach.
Z drugiej strony mamy wady. Pierwszym i często odczuwalnym elementem jest wyższy koszt jednostkowy prefabrykowanych elementów zbrojeniowych w przeliczeniu na kilogram. Producent dolicza marżę za pracę, amortyzację maszyn i transport. To jednak widok tylko na jeden element układanki – niższe koszty pracy na budowie, mniejszy odpad i szybszy termin często rekompensują tę różnicę w całościowym rozliczeniu projektu.
Ograniczona elastyczność na budowie to kolejna wada. Gotowe zbrojenie jest produkowane pod konkretny projekt. Jeśli na etapie realizacji pojawią się nieprzewidziane zmiany w projekcie płyty, dostosowanie prefabrykatów może być trudne lub niemożliwe. Może to wymagać domówienia nowych elementów lub kombinowania na placu, co niweczy część zalet.
Wymagania transportowe i gabarytowe gotowych elementów bywają wyzwaniem logistycznym. Duże kosze czy segmenty mogą być trudne w transporcie, zwłaszcza na wąskich drogach dojazdowych lub na działkach z ograniczoną przestrzenią manewrową dla ciężkiego sprzętu, który często jest niezbędny do rozładunku i ułożenia dużych elementów zbrojenia.
Wymagana precyzja w projekcie to warunek konieczny. Zastosowanie gotowego zbrojenia wymaga bezbłędnego projektu wykonawczego zbrojenia. Każdy błąd projektowy, który ujawni się dopiero na etapie montażu prefabrykatów na budowie, jest trudny i kosztowny do skorygowania. To kładzie duży nacisk na etap projektowania.
Czas realizacji zamówienia prefabrykatów również może być potencjalnym problemem. W odróżnieniu od zakupu prętów z hurtowni "od ręki", gotowe zbrojenie wymaga złożenia zamówienia z odpowiednim wyprzedzeniem, często kilku tygodni, w zależności od producenta i skomplikowania elementów. Nie pozwala to na spontaniczne decyzje czy szybkie reagowanie na zmiany.
Podsumowując zalety i wady, można powiedzieć, że gotowe zbrojenie to idealne rozwiązanie dla projektów, gdzie kluczowe są czas, precyzja wykonania i minimalizacja prac na placu budowy. Wymaga jednak dokładnego planowania, bezbłędnego projektu i sprawnej logistyki. Jest mniej odpowiednie dla projektów o bardzo nietypowych, skomplikowanych kształtach lub tam, gdzie projekt może ulec zmianie w trakcie budowy.
Stosunek korzyści do potencjalnych trudności często przechyla szalę na stronę prefabrykatów, zwłaszcza w większych, powtarzalnych realizacjach, gdzie szybkość i pewność wykonania mają wymierną wartość ekonomiczną. Jak mówi stare budowlane porzekadło: "Lepiej trzy razy zmierzyć, a raz dociąć... albo zamówić gotowe, co już zmierzone i docięte jest idealnie".
Gotowe zbrojenie vs tradycyjne – kluczowe porównanie
Zmierzenie się dwóch podejść do zbrojenia płyty fundamentowej – klasycznego, realizowanego w całości na placu budowy, i nowoczesnego, wykorzystującego gotowe elementy – to niczym starcie mistrza rzemiosła z zautomatyzowaną fabryką. Oba mają swoje miejsce w budownictwie, ale ich wybór powinien być podyktowany specyfiką projektu, dostępnością zasobów i priorytetami inwestora czy wykonawcy. To nie jest po prostu wybór technologii, to wybór filozofii pracy.
Zacznijmy od czasu realizacji. W metodzie tradycyjnej, po dostarczeniu prętów i siatek na budowę, ekipa zbrojarska rozpoczyna mozolny proces odmierzania, cięcia i gięcia każdego pręta według rysunków. Następnie te pręty są układane i wiązane drutem wiązałkowym w docelowej pozycji w wykopie fundamentowym. Ten proces wymaga czasu, precyzji manualnej i często potrafi się dłużyć, zwłaszcza przy skomplikowanych lub gęstych układach zbrojenia. Łatwo o przysłowiową "spawę w piekle" z harmonogramem, gdy pogoda nie sprzyja lub ekipa natrafi na trudności.
Gotowe zbrojenie skraca ten etap drastycznie. Elementy (kosze, belki, maty specjalne) przyjeżdżają gotowe, certyfikowane, uformowane dokładnie według projektu. Zadaniem ekipy na budowie jest głównie ich ułożenie i ewentualne połączenie ze sobą w węzłach konstrukcyjnych, co jest o wiele szybsze niż tworzenie całej konstrukcji od podstaw. W typowym projekcie domu jednorodzinnego, etap zbrojenia płyty, który metodą tradycyjną trwałby 5-7 dni, z prefabrykatami może zamknąć się w 2-3 dniach, a nawet krócej przy sprawnym zespole i dobrej organizacji.
Przechodząc do kosztów – sprawa jest bardziej złożona niżby się mogło wydawać. Bezpośredni koszt zakupu gotowego zbrojenia, liczony za kilogram, jest zazwyczaj wyższy niż koszt zakupu prętów luzem. Jednak patrząc szerzej, musimy uwzględnić koszty pracy. Mniejsza ilość roboczogodzin potrzebnych na montaż prefabrykatów, mniejszy odpad stali, który trzeba by było kupić w tradycyjnej metodzie (naddatek materiału zawsze jest potrzebny na docinanie i błędy), a także przyspieszenie całego etapu, co oznacza szybsze przejście do kolejnych prac i uniknięcie przestojów, które generują koszty – to wszystko składa się na obraz całościowy.
Nierzadko okazuje się, że sumaryczne koszty gotowego zbrojenia, uwzględniając wszystkie pośrednie oszczędności, są porównywalne lub nawet niższe niż metody tradycyjnej, zwłaszcza w regionach z wysokimi kosztami pracy i na budowach o ograniczonym miejscu. W końcu czas to pieniądz, a każdy dzień opóźnienia na budowie może słono kosztować.
Jakość wykonania to kolejny punkt sporu. Metoda tradycyjna, choć pozwala na dużą elastyczność i dostosowanie do niestandardowych kształtów na bieżąco, w dużej mierze zależy od umiejętności, doświadczenia i staranności ekipy zbrojarskiej. Ręczne gięcie, niedokładne odmierzenie czy brak odpowiedniego naciągnięcia drutu wiązałkowego mogą prowadzić do niedociągnięć, które trudno później skorygować. Czy każde wiązanie jest wykonane poprawnie? Czy wszystkie pręty są na swoich miejscach?
Prefabrykacja odbywa się w kontrolowanych warunkach fabrycznych. Maszyny precyzyjnie tną i gięte pręty, a następnie są one spajane (np. przez spawanie punktowe lub automatyczne wiązanie) w powtarzalne elementy o wysokiej dokładności geometrycznej. Każdy element jest identyczny z kolejnym, co gwarantuje zgodność z projektem i eliminuje ryzyko "czynnika ludzkiego" w kluczowych miejscach konstrukcji. Kontrola jakości w fabryce jest standardem, czego nie zawsze można powiedzieć o placu budowy.
Elastyczność vs. Planowanie – tutaj przewagę ma metoda tradycyjna. Jeśli w projekcie płyty fundamentowej pojawią się nagłe zmiany wynikające z nieprzewidzianych warunków gruntowych, konieczności przeprowadzenia dodatkowych instalacji, czy zmiany układu pomieszczeń, metoda tradycyjna pozwala na względnie łatwe wprowadzenie korekt na placu budowy. Wystarczy dociąć lub dogiąć odpowiednie pręty.
Z gotowym zbrojeniem sprawa jest bardziej skomplikowana. Każda zmiana oznacza konieczność domówienia nowych elementów lub próby adaptacji istniejących, co bywa trudne i kosztowne. Z tego powodu gotowe zbrojenie wymaga idealnego projektu wykonawczego zbrojenia na długo przed rozpoczęciem prac, bez marginesu na "imprezowanie" na budowie. "Na oko to chłop w szpitalu umarł" – to powiedzenie doskonale oddaje, dlaczego precyzja w projektowaniu gotowego zbrojenia jest tak ważna.
Logistyka i organizacja pracy – tu znów punkt dla prefabrykatów. Mniej prętów luzem, mniejszy bałagan, mniejsze zapotrzebowanie na miejsce składowe, brak konieczności tworzenia warsztatu zbrojarskiego na budowie. Potrzeba jednak cięższego sprzętu (dźwigu lub koparki z osprzętem) do rozładunku i układania ciężkich, gabarytowych elementów. Tradycyjne zbrojenie wymaga jedynie podstawowych narzędzi ręcznych i wiązarki.
Podsumowując porównanie, gotowe zbrojenie do płyt fundamentowych to krok w stronę industrializacji budownictwa. To rozwiązanie dla tych, którzy cenią sobie szybkość, wysoką i przewidywalną jakość, optymalizację procesów logistycznych i redukcję pracy fizycznej na budowie, są w stanie zainwestować nieco więcej na początku i przede wszystkim mają projekt zbrojenia wykonany bezbłędnie i szczegółowo. Metoda tradycyjna pozostaje niezastąpiona tam, gdzie projekt jest bardzo nietypowy, zmiany są prawdopodobne, a elastyczność na budowie jest kluczowa. Ale przy standardowych płytach, gotowe zbrojenie często okazuje się być wyborem nowocześniejszym i, w ujęciu całościowym, efektywniejszym.
Rodzaje gotowego zbrojenia do płyt fundamentowych
Świat gotowego zbrojenia do płyt fundamentowych to znacznie więcej niż tylko "gotowe siatki". Choć maty zgrzewane stanowią bazę dla wielu płyt, prefabrykacja oferuje elementy dostosowane do specyficznych potrzeb konstrukcyjnych i geometrycznych, pozwalając na budowanie niemal każdej formy zbrojenia poza placem budowy. Zrozumienie dostępnych typów pomaga w optymalnym doborze rozwiązania dla konkretnego projektu, od prostego domu po bardziej złożone obiekty przemysłowe.
Najpopularniejszym typem, który stanowi ewolucję tradycyjnych siatek, są maty zgrzewane na wymiar lub zintegrowane z dodatkowymi elementami. Choć standardowe siatki Q i R są dostępne od ręki, producenci gotowego zbrojenia mogą dostarczyć maty o niestandardowych rozstawach prętów, różnej średnicy prętów w różnych kierunkach (tzw. siatki projektowane), a nawet zintegrowane z otworami na słupy czy przejścia instalacyjne. Eliminuje to potrzebę docinania i wiązania na budowie, a siatki przyjeżdżają idealnie pasujące do kształtu płyty. Typowe wymiary transportowe to np. 2.3x6m, ale można zamówić maty niemal w każdym rozsądnym rozmiarze transportowym.
Kolejnym kluczowym elementem są gotowe kosze i belki zbrojeniowe. Płyty fundamentowe często posiadają zgrubienia pod ścianami nośnymi, krawędziami, a także poprzeczne belki rozdzielcze. W metodzie tradycyjnej wymagają one precyzyjnego gięcia strzemion i prętów, a następnie ich żmudnego wiązania w przestrzeni wykopu. W prefabrykacji, te elementy dostarczane są jako gotowe kosze – trójwymiarowe, przestrzenne elementy, np. prostopadłościenne lub trapezoidalne belki, o określonych wymiarach i układzie prętów głównych i strzemion.
Długość gotowych koszy jest często ograniczona względami transportowymi, typowo do 12-13.5 metra. Szerokość i wysokość są dostosowane do wymagań projektowych płyty, np. kosz o wymiarach 30x40cm (szerokość x wysokość) dla zgrubienia brzegowego płyty o grubości 20cm. Ich montaż polega na ułożeniu we wskazanym miejscu i połączeniu z pozostałym zbrojeniem, np. matami.
Prefabrykowane elementy gięte, takie jak ugięte pręty zbrojeniowe (np. typu L lub U do wzmocnień narożników, krawędzi czy przejść), gięte pręty na strzemiona w niestandardowych kształtach, czy gotowe głowice słupowe (do przeniesienia obciążeń ze słupów na płytę), to kolejny segment. Zamiast giąć na budowie setki strzemion czy specjalistycznych prętów, otrzymujemy je gotowe, co zapewnia idealne wymiary i kształt, a także jednorodność w całej konstrukcji.
Dostawcy gotowego zbrojenia oferują również rozwiązania systemowe, które obejmują nie tylko zbrojenie, ale i akcesoria niezbędne do montażu. Mogą to być specjalistyczne dystanse (tzw. "spacery" lub "listwy") zapewniające odpowiednią otulinę betonową z dołu, podkładki dystansowe do utrzymania zbrojenia górnego we właściwej pozycji, a nawet gotowe szalunki tracone dla krawędzi płyty zintegrowane z izolacją termiczną.
Typowe profile prefabrykowanego zbrojenia mogą mieć średnicę od 6 mm do 40 mm i więcej, w zależności od obciążeń i wymagań projektowych. Wykorzystywana jest stal klasy A-IIIN (B500SP) lub A-IIIN (B500A), a rodzaj stali i średnice prętów są ściśle określone w projekcie wykonawczym zbrojenia. Koszt produkcji prefabrykatów jest często wyceniany indywidualnie na podstawie ilości i skomplikowania elementów, a także średnicy użytej stali – im większa średnica, tym koszt za kg prefabrykatu zazwyczaj jest wyższy.
Warto podkreślić, że wybierając gotowe zbrojenie, zamawiamy kompleksowe rozwiązanie "skrojone na miarę". Nie kupujemy komponentów, które trzeba na miejscu dopasować, ale system gotowych elementów. To jak budowanie z dużych klocków Lego, które pasują do siebie idealnie. To znacząco różni się od tradycyjnego podejścia, gdzie plac budowy jest niczym warsztat krawiecki, gdzie z dużego arkusza materiału (prętów) wycina się i formuje mniejsze elementy.
Znajomość tych rodzajów gotowego zbrojenia pozwala na świadomy wybór i dyskusję z projektantem czy producentem. Czy potrzebujemy tylko mat na wymiar? Czy może całe zbrojenie krawędziowe w formie gotowych koszy? A może skomplikowane gięte elementy do wzmocnień pod dużymi obciążeniami? Dobór odpowiednich typów prefabrykatów jest kluczowy dla maksymalizacji korzyści płynących z zastosowania tej technologii. Pamiętajmy, że każdy projekt jest inny i wymaga indywidualnego podejścia, a bogactwo oferty prefabrykatów pozwala dopasować rozwiązanie niemal idealnie.
Montaż gotowego zbrojenia płyty fundamentowej krok po kroku
Montaż gotowego zbrojenia płyty fundamentowej to proces znacznie szybszy i mniej pracochłonny od metody tradycyjnej, ale wciąż wymaga precyzji i dobrej organizacji. To moment, w którym całe wcześniejsze planowanie, precyzja fabrycznej produkcji i logistyka zbiegają się na placu budowy, aby "ułożyć się w całość". Dobrze przeprowadzony montaż to gwarancja trwałości i bezpieczeństwa całej konstrukcji budynku. Oto typowa ścieżka tego procesu.
Pierwszym, absolutnie kluczowym krokiem, jest dokładne przygotowanie podłoża i szalunku. Gotowe zbrojenie, w przeciwieństwie do prętów luzem, często jest ciężkie i mniej elastyczne w manewrowaniu. Podłoże (zagęszczony piasek, chudy beton, izolacja termiczna i przeciwwilgociowa) musi być równe, stabilne i czyste. Szalunki muszą być solidne i dokładnie ustawione, ponieważ gotowe kosze zbrojeniowe brzegowe lub krawędziowe belki zbrojeniowe opierają się często bezpośrednio o nie, a ich waga może spowodować przesunięcia lub odkształcenia szalunku, jeśli nie jest on odpowiednio zabezpieczony. Ten etap musi być zrobiony perfekcyjnie "na tip-top".
Następnie odbywa się dostawa i planowanie rozładunku. Elementy gotowego zbrojenia przyjeżdżają na plac budowy zazwyczaj w formie dużych paczek lub pojedynczych, gabarytowych elementów (np. długie kosze). Już na etapie zamówienia warto ustalić z producentem sposób i kolejność pakowania, aby na budowie można było elementy rozładować możliwie blisko miejsca docelowego ich montażu, w kolejności zgodnej z planem pracy. Idealnie, jeśli możliwe jest składowanie paczek tak, aby dostęp do nich był łatwy i nie kolidował z dalszymi etapami montażu.
Rozładunek i transport w obrębie placu budowy to często operacja wymagająca sprzętu. Duże maty, a w szczególności ciężkie kosze zbrojeniowe, nie są elementami, które ekipa przeniesie w rękach. Do rozładunku z ciężarówki i transportu w obrębie wykopu fundamentowego zazwyczaj używa się dźwigu samochodowego, koparki z osprzętem widłowym lub haka, a na krótszych dystansach i przy lżejszych elementach - wózka widłowego terenowego. Ważne, aby operacje te wykonywać ostrożnie, aby nie odkształcić delikatnych elementów zbrojenia podczas transportu.
Kolejnym kluczowym etapem jest układanie zbrojenia dolnego. Zaczyna się zazwyczaj od siatek lub koszy tworzących dolną warstwę zbrojenia płyty oraz belki krawędziowe i poprzeczne. Elementy są opuszczane w odpowiednie miejsca wykopu i układane na dystansach zapewniających odpowiednią otulinę betonową od spodu. Typowe dystanse dla płyt fundamentowych to "żabki", kostki betonowe lub listwy zbrojarskie o wysokościach 30-50 mm. Liczba dystansów musi być wystarczająca, aby utrzymać zbrojenie we właściwej pozycji pod własnym ciężarem i ciężarem poruszających się po nim pracowników.
Układanie zbrojenia górnego i elementów łączących to następny krok. Gdy zbrojenie dolne i belki nośne są na miejscu, montowane są elementy górnego zbrojenia – zazwyczaj siatki opierające się na wcześniej ułożonych koszach lub na specjalnych dystansach-podpórkach ("krótkich koszach" lub "jeżach"), które utrzymują górną warstwę zbrojenia w odpowiedniej odległości od dolnej. W tym etapie łączone są również gotowe kosze ze sobą oraz z siatkami – zazwyczaj przez związanie drutem wiązałkowym w punktach styku, zgodnie ze sztuką budowlaną i wytycznymi projektowymi.
Integracja instalacji i specjalistycznych elementów to równoległy lub kolejny krok. Przed zalaniem betonem, w obrębie zbrojenia muszą znaleźć się wszystkie niezbędne przejścia rurowe dla instalacji kanalizacyjnych, wodnych, elektrycznych czy grzewczych (np. podposadzkowej). Należy upewnić się, że otwory w zbrojeniu prefabrykowanym, jeśli były przewidziane, pasują do zaplanowanej trasy rur. Jeśli konieczne są dodatkowe przejścia, należy ostrożnie przepleść rury przez oczka siatek, nie przecinając prętów głównych, lub wzmocnić zbrojenie w ich okolicy zgodnie z zaleceniami projektanta.
Ostatnie sprawdzenia i korekty są kluczowe przed przystąpieniem do betonowania. Przed wejściem pompy do betonu, doświadczony wykonawca lub inspektor nadzoru powinien dokonać dokładnej inspekcji ułożonego zbrojenia. Sprawdza się poprawność ułożenia wszystkich elementów zgodnie z projektem, jakość wiązań, zachowanie odpowiednich otulin betonowych (zarówno od dołu, jak i od krawędzi oraz wewnątrz), czystość zbrojenia (brak błota, oleju) i brak odkształceń. Każdy pręt musi być na swoim miejscu – to absolutny imperatyw.
Finalnym etapem jest przygotowanie do betonowania. Zbrojenie jest gotowe, sprawdzone i zatwierdzone. Pozostaje tylko upewnić się, że szalunki są czyste, zabezpieczone (np. środkiem antyadhezyjnym) i gotowe na przyjęcie betonu. Ekipa powinna mieć przygotowane wibratory do betonu i plan wylewania, aby beton równomiernie wypełnił całą przestrzeń zbrojenia, otulił pręty i nie pozostawił pustek. Wibracja jest kluczowa dla zagęszczenia betonu wokół zbrojenia.
Montaż gotowego zbrojenia, choć zmechanizowany w fazie produkcji, wymaga na budowie wprawy, koordynacji i rygorystycznego przestrzegania zasad. Szybkość tego procesu jest imponująca, ale to właśnie dbałość o szczegóły na każdym etapie, od idealnie równego podłoża, przez delikatny transport elementów, po skrupulatne ostatnie sprawdzenie, decyduje o sukcesie i trwałości płyty fundamentowej. To nie wyścigi, to precyzyjny balet ciężkich elementów na placu budowy.