Skuteczna Naprawa Płyty Betonowej: Przyczyny i Metody
Spękania, odpryski, odsłonięte zbrojenie – oto cisi świadkowie upływu czasu, niszczący nasze betonowe konstrukcje. Gdy widok taki staje się codziennością, pilna staje się naprawa płyty betonowej. To nic innego jak precyzyjny proces przywracania strukturalnej integralności i estetyki zniszczonym elementom, zanim z małego problemu narodzi się poważne zagrożenie.
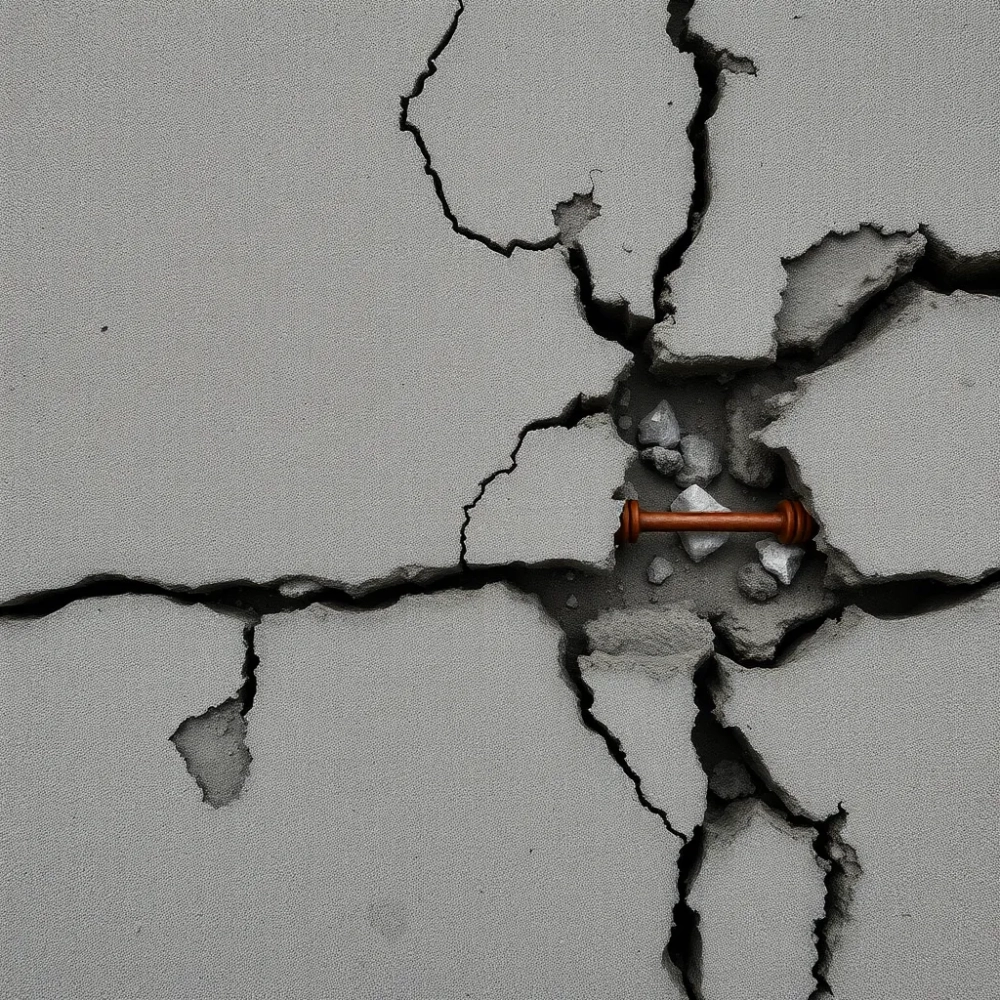
Złożoność uszkodzeń betonowych pchnęła ekspertów do pogłębionych analiz efektywności różnych podejść naprawczych. Analizowano między innymi zależność trwałości naprawy od typu zastosowanego materiału w kontekście charakteru uszkodzenia. Poniższa prezentacja danych ukazuje typowe korelacje obserwowane na przestrzeni lat ekspertyz.
Charakter Uszkodzenia | Rekomendowany Typ Materiału | Typowa Grubość Naprawy (mm) | Szacunkowa Średnia Trwałość Naprawy (lata) | Złożoność Aplikacji (skala 1-5) |
---|---|---|---|---|
Drobne pęknięcia (< 0.5 mm szer.) | Zaprawa cementowa z modyfikatorami lub żywica | Aplikacja powierzchniowa | 5-10 | 2 |
Odpryski bez korozji zbrojenia (głęb. do 20 mm) | Mineralna zaprawa PCC (polimerowo-cementowa) R2 | 10-20 | 15-20 | 3 |
Głębokie odpryski z korozją zbrojenia (> 20 mm) | Mineralna zaprawa PCC R3/R4 + system pasywujący stal | > 20 (wymaga warstw) | 20-30+ | 4 |
Ubytki w obszarze ruchu kołowego | Zaprawa szybkosprawna, o wysokiej wytrzymałości R4 | Minimum 30 (zalecane > 50) | 10-15 (przy odpowiedniej konserwacji) | 4-5 |
Te obserwacje jasno pokazują, że "jeden rozmiar dla wszystkich" nie działa w naprawach betonu. Wybór odpowiedniej technologii i chemii ma bezpośredni wpływ na długoterminowy sukces interwencji. Inwestycja w adekwatne rozwiązania, choć początkowo droższa, znacząco wydłuża żywotność konstrukcji, minimalizując ryzyko przedwczesnych awarii i kosztownych poprawek w przyszłości.
Dlaczego Płyty Betonowe Ulegają Uszkodzeniom? Główne Przyczyny
Choć beton uchodzi za symbol trwałości i wytrzymałości, nawet najsolidniejsze konstrukcje podlegają nieubłaganemu działaniu czasu i czynników zewnętrznych. Zrozumienie mechanizmów destrukcji to pierwszy krok do skutecznej naprawy i prewencji.
Jedną z fundamentalnych przyczyn uszkodzenia betonu jest jego wrodzona porowatość. Beton nie jest litą, nieprzenikliwą masą; w jego strukturze występują pory i kapilary, choćby na poziomie mikroskopowym. To właśnie te mikrodefekty stają się autostradami dla agresywnych substancji.
Nienaruszona powierzchnia betonu stanowi barierę, ale przenikanie wilgoci jest niemal nieuniknione w zmiennym klimacie. Wilgoć przenosi ze sobą rozmaite związki chemiczne z otoczenia. Jednymi z najbardziej destrukcyjnych są chlorki, często obecne w solach odladzających stosowanych zimą.
Gdy te agresywne substancje, w tym chlorki, dotrą przez sieć porów i mikropęknięć do zbrojenia, zaczyna się korozja stali. Reakcja elektrochemiczna przekształca stabilne żelazo w rdzę. Ten proces prowadzi do zwiększenia objętości materiału, ponieważ tlenki żelaza zajmują znacznie więcej miejsca niż czysty metal.
Ekspansja rdzy wywiera olbrzymi nacisk na otaczający ją beton, rzędu nawet 2 do 6 razy większego niż pierwotna objętość stali. Ten wewnętrzny nacisk jest jak dynamit, powoli kruszący beton od środka. Prowadzi to do powstania rys, odprysków i wreszcie do całkowitego rozsadzenia warstwy otuliny.
Kolejną kluczową kwestią jest grubość otuliny, czyli warstwy betonu osłaniającej pręty zbrojeniowe. Normy określają minimalne wymagania, zazwyczaj od 2 cm do nawet 5 cm lub więcej w środowiskach agresywnych, np. nad morzem. Zbyt cienka otulina dramatycznie skraca czas potrzebny czynnikom korozyjnym na dotarcie do stali.
To tak, jakby zbrojenie miało na sobie tylko cieniutką koszulkę zamiast pancerza w trudnych warunkach bojowych. Krótsza droga to szybsze utlenianie stali i wcześniejsze pojawienie się objawów korozji. Widoczne pęknięcia i nacieki rdzawe na powierzchni często wskazują na ten problem.
Inne czynniki, takie jak cykle zamarzania i rozmrażania wody uwięzionej w porach betonu, również przyczyniają się do zniszczeń. Woda zwiększa objętość po zamarznięciu o około 9%, generując ciśnienie wewnętrzne niszczące strukturę betonu. Skala zniszczeń zależy od stopnia nasycenia wodą i jakości samego betonu.
Nie można zapomnieć o agresji chemicznej z zewnątrz, np. kwasach lub siarczanach obecnych w zanieczyszczonej wodzie opadowej czy gruntowej. Te substancje mogą rozkładać składniki matrycy cementowej, prowadząc do utraty spójności i wytrzymałości betonu.
Uszkodzenia mogą wynikać także z niewłaściwego projektu mieszanki betonowej, na przykład zbyt wysokiego wskaźnika wodno-cementowego, co zwiększa porowatość i przepuszczalność. Podobnie, nieprawidłowe zagęszczanie betonu lub zbyt wczesne zakończenie pielęgnacji (np. brak utrzymywania wilgoci w początkowych dniach) skutkuje osłabieniem struktury.
Przykładowo, płyta balkonowa wykonana z betonu o słabych parametrach i niewystarczającej otulinie, dodatkowo wystawiona na działanie deszczu i mrozu, a zimą posypywana solą, to przepis na katastrofę w ciągu kilku do kilkunastu lat. Proces korozji zbrojenia jest wtedy brutalnie przyspieszony.
Dodatkowe obciążenia mechaniczne, jak przeciążenie, uderzenia czy wibracje, mogą inicjować lub poszerzać pęknięcia, ułatwiając penetrację agresorów. Zmęczenie materiału pod wpływem cyklicznie przykładanych obciążeń również odgrywa swoją rolę w degradacji konstrukcji.
Diagnostyka uszkodzeń wymaga niekiedy ekspertyzy, która pozwoli dokładnie określić pierwotną przyczynę lub zespół przyczyn. Odpryski w środku płyty mogą mieć inną genezę niż te na krawędziach czy wzdłuż linii zbrojenia. Bez tej wiedzy, naprawa może okazać się tylko chwilowym kamuflażem problemu, a nie jego trwałym rozwiązaniem.
Wnikliwe badanie betonu obejmuje nieraz analizę jego składu, stopnia karbonatyzacji (procesu obniżania alkaliczności betonu przez CO2 z powietrza, co redukuje pasywację stali) oraz obecności chlorków. To trochę jak medyczna diagnostyka – musisz znać chorobę, żeby dobrać lek.
Problem uszkodzeń betonu staje się coraz bardziej palący w starszych obiektach, projektowanych i budowanych w czasach, gdy wiedza o trwałości materiałów i agresywności środowisk zewnętrznych była mniej zaawansowana niż dziś. Czas weryfikuje wybory sprzed lat.
Szacuje się, że znaczna część kosztów utrzymania infrastruktury betonowej w Europie jest związana z naprawami uszkodzeń wywołanych korozją zbrojenia. Mówimy tu o miliardach euro rocznie, co podkreśla skalę problemu i wagę właściwej prewencji oraz skutecznych napraw powierzchni betonowych.
Karbonatyzacja, obniżając pH betonu (normalnie wysokie, ok. 12.5-13.5), likwiduje ochronną warstwę pasywną na stali. Stal staje się wówczas podatna na korozję nawet przy braku chlorków. Tempo karbonatyzacji zależy od porowatości betonu i wilgotności otoczenia.
Zbyt wczesne obciążenie konstrukcji, niewłaściwe podparcie deskowania czy błędy montażowe mogą prowadzić do zarysowań konstrukcyjnych już na etapie budowy. Te wczesne defekty stają się potencjalnymi punktami wejścia dla agresorów w przyszłości, akcelerując degradację.
Podsumowując, uszkodzenia betonu to często złożony proces wynikający z interakcji wad materiałowych, błędów wykonawczych i agresywnych czynników środowiskowych. Adresowanie tych pierwotnych przyczyn jest kluczowe dla trwałej i skutecznej naprawy betonu.
Przygotowanie Podłoża i Uszkodzonego Zbrojenia Do Naprawy
Można by pomyśleć, że najważniejsze w naprawie betonu jest zastosowanie drogiej, zaawansowanej zaprawy. Tymczasem, wiedzcie, że 80% sukcesu zależy od starannego przygotowania podłoża i zbrojenia. Zaniedbania na tym etapie to gwarancja porażki.
Dla powierzchni betonowych pozbawionych zbrojenia, gdzie wystąpiły nieduże uszkodzenia, proces zaczyna się od usunięcia wszelkich luźnych, spękanych lub słabych fragmentów betonu. Robi się to, skuwanie, aż do osiągnięcia tak zwanej „zdrowej” i nośnej warstwy. Usłyszysz różnicę w dźwięku przy opukiwaniu młotkiem.
Zdrowa warstwa to ta, która nie kruszy się, jest twarda i ma stabilną strukturę. To na niej nowa zaprawa naprawcza musi się trwale związać. Podłoże po skuwaniu powinno być szorstkie, profilowane, nigdy gładkie i "polerowane" – chropowatość zwiększa przyczepność mechaniczną.
Po usunięciu mechanicznie uszkodzonego betonu, absolutnie kluczowe jest staranne usunięcie kurzu, pyłu i wszelkich innych zanieczyszczeń, takich jak tłuszcze czy resztki farby. Kurz działa jak warstwa poślizgowa, całkowicie uniemożliwiając prawidłowe wiązanie zaprawy naprawczej z podłożem.
Czyszczenie przeprowadza się szczotkami (drucianymi lub ryżowymi), odkurzaniem przemysłowym lub, najlepiej, przedmuchując powierzchnię czystym, sprężonym powietrzem. Czasem stosuje się także mycie pod wysokim ciśnieniem, ale wtedy powierzchnia wymaga dłuższego czasu schnięcia przed dalszymi etapami.
Następnym krokiem jest odpowiednie przygotowanie wilgotnościowe podłoża. Suchy, chłonny beton wyciągnąłby wodę zarobową z świeżej zaprawy naprawczej zbyt szybko, uniemożliwiając jej prawidłowe nawodnienie i hydratację cementu. Skutek? Słaba wytrzymałość, pęknięcia skurczowe, brak przyczepności.
Dlatego, w zależności od porowatości i chłonności podłoża, należy je zwilżyć, czasem dość obficie wodą. Cel to osiągnięcie stanu nasyconego powierzchniowo suchego (SSD - Saturated Surface Dry). Podłoże powinno być wyraźnie ciemniejsze, wilgotne, ale bez stojącej wody i błyszczących "lusterek".
Gdy naprawy wymaga beton zbrojony z widocznymi miejscami korozji, zakres prac jest szerszy. Trzeba usunąć luźne fragmenty betonu wokół zbrojenia, odsłaniając je całkowicie w miejscu skorodowanym. Z reguły skuwa się beton przynajmniej 1-2 cm za pręt, do zdrowego, nośnego podłoża.
Odsłonięte zbrojenie, zwłaszcza jeśli jest skorodowane, musi zostać bezwzględnie oczyszczone z rdzy. Nawet niewielka warstwa rdzy uniemożliwia prawidłowe związanie zaprawy naprawczej ze stalą i prowadzi do wznowienia korozji pod nową warstwą betonu. To proszenie się o kłopoty.
Czyszczenie zbrojenia można przeprowadzić ręcznie (szczotka druciana, młotek z ostrym końcem) lub mechanicznie. Metody mechaniczne, takie jak szlifowanie szlifierką kątową lub piaskowanie/śrutowanie, są zdecydowanie bardziej skuteczne, zwłaszcza przy zaawansowanej korozji.
Celem jest uzyskanie czystej, metalicznie błyszczącej powierzchni stali, wolnej od luźnej rdzy, zgorzeliny czy innych zanieczyszczeń. Stopień czystości stali ocenia się według norm (np. stopień Sa 2 lub Sa 2.5 według norm ISO) – dąży się do usunięcia przynajmniej 95% rdzy.
Po mechanicznym usunięciu rdzy, stal warto oczyścić z rdzawych resztek i pyłu za pomocą czystego, sprężonego powietrza. Wszelki pył pozostawiony na powierzchni stali również osłabia wiązanie z przyszłą zaprawą.
Oczyszczona stal, zwłaszcza w agresywnych środowiskach lub gdy minimalna otulina jest trudna do zachowania, wymaga zabezpieczenia powłoką antykorozyjną. Jest to tzw. warstwa pasywująca lub sczepna na zbrojenie. Może to być specjalna farba antykorozyjna na bazie cementu, żywic epoksydowych lub innych systemów chemicznych.
Powłoka antykorozyjna ma za zadanie przywrócić alkaliczne środowisko wokół stali i chronić ją przed przyszłym dostępem wilgoci i agresywnych jonów. Pełni często także funkcję warstwy sczepnej, poprawiając adhezję zaprawy naprawczej do stali i podłoża betonowego. Typowe grubości takiej powłoki to 1-2 mm.
Należy ściśle przestrzegać zaleceń producenta dotyczących sposobu aplikacji powłoki antykorozyjnej i jej czasu wyschnięcia. Zastosowanie zaprawy naprawczej na mokrą lub nieprawidłowo utwardzoną powłokę może prowadzić do problemów z wiązaniem i ostateczną wytrzymałością systemu naprawczego.
Dopiero po pełnym wyschnięciu warstwy zabezpieczającej zbrojenie przed korozją i przygotowaniu podłoża betonowego (czyste, zwilżone SSD) można przystąpić do wypełniania ubytków zaprawą cementową. To świadczy o sekwencji i priorytetach – fundament musi być solidny.
Szczególną uwagę należy zwrócić na obszary styku starego i nowego betonu. Powinny być czyste, nośne i odpowiednio zwilżone. To tam najczęściej dochodzi do dekohezji, jeśli przygotowanie było niedostateczne. To punkt krytyczny naprawy.
W przypadku głębokich ubytków (>3-5 cm) rozważyć można także zastosowanie warstwy sczepnej na sam beton przed aplikacją zaprawy naprawczej. Jest to np. rzadka zaprawa cementowa (szlam) lub dedykowane grunty poprawiające adhezję. Zapewnia to dodatkową "rękojmię" prawidłowego związania.
Kompletne i metodyczne przygotowanie podłoża oraz zbrojenia to proces czasochłonny i wymagający precyzji. Może stanowić znaczną część czasu pracy w całym przedsięwzięciu naprawczym. Jednak każda minuta poświęcona temu etapowi zwróci się w postaci trwałości i niezawodności wykonanej naprawy. Oszczędności w tym miejscu są iluzoryczne.
Dobór Odpowiednich Materiałów Do Naprawy Betonu
Wybór materiałów do naprawy betonu to decyzja o kapitalnym znaczeniu, porównywalna do wyboru odpowiedniego leku w medycynie. Zastosowanie niewłaściwego preparatu, choć pozornie rozwiązuje problem, może prowadzić do szybkiego nawrotu uszkodzeń lub nawet pogorszenia stanu konstrukcji. Panuje tu pewien kanon.
Kluczowa zasada mówi, że materiały budowlane powinny być naprawiane przy użyciu materiałów, które posiadają zbliżone lub lepsze właściwości fizyczne i techniczne od oryginalnego materiału. Ta kompatybilność jest krytyczna, aby uniknąć naprężeń wewnętrznych i pęknięć.
Chodzi tu o takie parametry jak współczynnik rozszerzalności cieplnej, moduł sprężystości, skurcz (zarówno plastyczny, jak i wysychania) oraz wytrzymałość (na ściskanie, zginanie, rozciąganie). Materiały różniące się znacznie tymi cechami będą "walczyć" ze sobą pod wpływem zmian temperatury czy obciążeń, prowadząc do pęknięć na styku starego i nowego materiału.
Aby powłoka wypełniająca ubytek w powierzchni betonowej miała podobne właściwości do oryginalnego betonu i zapewniała odpowiednią trwałość, do naprawy betonu powszechnie zaleca się stosowanie zapraw mineralnych zawierających cement. To naturalne "pokrewieństwo" chemiczne i fizyczne jest ich ogromną zaletą.
W ramach tej grupy materiałów wyróżnia się różne rodzaje zapraw cementowych naprawczych. Podstawowy podział opiera się często na wytrzymałości i przeznaczeniu, często w odniesieniu do normy europejskiej PN-EN 1504, która definiuje klasy R1, R2, R3, R4.
Zaprawy klasy R1 (np. o minimalnej wytrzymałości 10 MPa po 28 dniach) i R2 (min. 15 MPa) przeznaczone są do niekonstrukcyjnych napraw, np. wygładzania powierzchni, uzupełniania drobnych ubytków, ale bez przywracania nośności elementu.
Zaprawy R3 (min. 25 MPa) i R4 (min. 45 MPa, czyli o wytrzymałości często wyższej niż pierwotny beton) to materiały do strukturalnych napraw powierzchni betonowych. Mogą przywrócić lub zwiększyć nośność uszkodzonych elementów konstrukcyjnych.
Powierzchni betonowych może zostać wykonana m.in. przy użyciu specjalistycznych zapraw, które znacznie wykraczają poza tradycyjne mieszanki cementu, piasku i wody przygotowywane na budowie. Współczesne technologie oferują produkty o ściśle kontrolowanym składzie.
Przykładem takiego materiału jest gotowa, sucha mieszanka, zawierająca precyzyjnie wyselekcjonowane kruszywa mineralne (np. kwarcowe o frakcjach dobranych do grubości naprawy, do 4-8 mm dla grubszych aplikacji), wysokiej jakości cement oraz szereg domieszek chemicznych. Typowe opakowania to worki po 25 kg.
Domieszki te pełnią kluczowe funkcje: poprawiają urabialność, ograniczają skurcz (np. przez zastosowanie domieszek pęczniejących lub redukujących ilość wody zarobowej), zwiększają przyczepność, redukują przepuszczalność dla wody i agresywnych jonów, a także mogą przyspieszać lub opóźniać czas wiązania.
Użycie takich gotowych mieszanek, dostępnych w postaci suchego proszku wymagającego jedynie dodania czystej wody w ściśle określonych proporcjach (np. 3-4 litry wody na 25 kg worka – to konkretne dane!), znacznie ułatwia i przyspiesza wykonanie prac. Eliminuje to błędy w proporcjach składników typowe dla mieszanek "budowlanych".
Oprócz zapraw na bazie cementu, w specjalistycznych zastosowaniach stosuje się także materiały żywiczne, np. zaprawy epoksydowe czy poliuretanowe. Charakteryzują się one bardzo wysoką wytrzymałością, niską przepuszczalnością i doskonałą adhezją, ale mają inny moduł sprężystości i współczynnik rozszerzalności niż beton, co wymaga starannego projektowania naprawy.
Żywice są często używane do iniekcji pęknięć (nawet o szerokości poniżej 0.1 mm), napraw elementów cienkościennych, posadzek przemysłowych narażonych na agresję chemiczną lub miejsc wymagających bardzo szybkiego utwardzenia. Ich koszt jest z reguły znacznie wyższy niż zapraw cementowych.
Przy wyborze materiału należy również uwzględnić sposób aplikacji – czy zaprawa będzie narzucana ręcznie (metoda "mokre na mokre"), czy pompowana, czy aplikowana metodą natrysku torkretowego. Na rynku dostępne są zaprawy o różnej konsystencji: plastyczne (do pacowania ręcznego), półpłynne (do zalewania) lub torkretowe.
Ważne jest też środowisko pracy i eksploatacji elementu. Materiały na zewnątrz muszą być mrozoodporne i odporne na warunki atmosferyczne. W przypadku elementów narażonych na działanie chlorków lub siarczanów, należy wybrać zaprawy o podwyższonej odporności chemicznej i niskiej przepuszczalności.
Niektóre zaprawy naprawcze zawierają także inhibitory korozji, które dodatkowo chronią zbrojenie. To kolejna warstwa zabezpieczenia, zwiększająca trwałość całej interwencji, szczególnie w miejscach, gdzie nie usunięto 100% rdzy.
Wybór odpowiedniego systemu materiałowego powinien być poprzedzony dokładną analizą stanu technicznego konstrukcji, rodzaju i przyczyn uszkodzeń oraz warunków środowiskowych. Nie ma tu miejsca na "na oko". Konsultacja ze specjalistą lub producentem materiałów jest zawsze dobrą praktyką.
Dostępne na rynku produkty często tworzą całe systemy naprawcze: od powłoki sczepnej/antykorozyjnej na zbrojenie, przez zasadniczą zaprawę wypełniającą, po ewentualną warstwę wyrównującą lub ochronną na wierzchu. Stosowanie materiałów z jednego systemu zapewnia ich wzajemną kompatybilność i często jest wymagane gwarancją producenta.
Koszt materiałów to tylko część całkowitego kosztu naprawy. W przypadku skomplikowanych uszkodzeń lub elementów konstrukcyjnych, koszt pracy i przygotowania podłoża może stanowić znaczną większość wydatków, nieraz przewyższając cenę samej zaprawy nawet 2-3 razy.
Ostatecznie, dobór odpowiednich materiałów do naprawy betonu to decyzja, która bezpośrednio wpływa na długowieczność i skuteczność przywrócenia pierwotnych funkcji płyty betonowej. To inwestycja w przyszłość konstrukcji, która powinna być podjęta świadomie i w oparciu o fachową wiedzę.
Metody Wypełniania Ubytków i Aplikacji Zaprawy Naprawczej
Kiedy podłoże jest wzorowo przygotowane – czyste, stabilne, odpowiednio zwilżone, a zbrojenie oczyszczone i zabezpieczone – nadchodzi moment kulminacyjny: aplikacja zaprawy naprawczej. To nie tylko mechaniczne wypełnienie pustki; to proces wymagający techniki, wiedzy o materiale i warunkach.
Pierwszym zasadniczym krokiem jest wypełnienie ubytków przygotowaną zaprawą. Sposób aplikacji zależy od rodzaju zaprawy (jej konsystencji – czy jest plastyczna, półpłynna, torkretowa) oraz od lokalizacji ubytku (powierzchnia pozioma, pionowa, stropowa).
Zaprawy o konsystencji plastycznej, określanej jako "mokra ziemia" lub lekko "plastelinowa", są zazwyczaj aplikowane ręcznie za pomocą kielni i pac budowlanych. Materiał jest "narzucany" i mocno wpychany w ubytek, warstwa po warstwie, w celu dokładnego wypełnienia całej przestrzeni i wyparcia powietrza. Jest to kluczowe, by uniknąć pustek i zapewnić pełny kontakt z podłożem i zbrojeniem.
Kompresja materiału jest niezwykle ważna, szczególnie w ciasnych przestrzeniach wokół zbrojenia. Dobre upakowanie zapewnia gęstość zaprawy, minimalizuje porowatość naprawy i maksymalizuje kontakt z podłożem, co przekłada się na wysoką wytrzymałość i trwałość naprawy.
W przypadku głębokich ubytków, zwłaszcza napraw wykonywanych w pozycji stropowej lub pionowej, stosuje się zazwyczaj metodę warstwową. Każdą warstwę (o typowej grubości 2-3 cm) należy mocno wcisnąć i zagęścić, a kolejną warstwę nakłada się dopiero po wstępnym związaniu poprzedniej (np. po kilku godzinach, zależnie od produktu), aby zapobiec obsuwaniu się materiału.
Zaprawy o konsystencji półpłynnej lub płynnej stosuje się zazwyczaj do napraw poziomych, zwłaszcza tam, gdzie trudno dokładnie zagęścić materiał metodą ręczną lub gdzie ubytek ma nieregularne kształty. Materiał jest wtedy "zalewany" lub pompowany w przygotowany otwór, często z użyciem szalunków. Ważne jest, aby wylewać materiał z jednej strony, umożliwiając wyparcie powietrza.
Choć zaprawy płynne są często określane jako samozagęszczalne, w praktyce delikatne wibracje (np. poprzez opukiwanie szalunków lub użycie specjalistycznego wibratora listwowego) mogą pomóc w dokładnym wypełnieniu wszystkich zakamarków i eliminacji pęcherzy powietrza. Należy to robić ostrożnie, aby nie doprowadzić do segregacji składników zaprawy.
Metody natrysku torkretowego, zarówno na sucho, jak i na mokro, to specjalistyczne techniki aplikacji, stosowane do naprawy betonu na większych powierzchniach, na przykład na ścianach oporowych czy w tunelach. Umożliwiają szybkie nanoszenie dużych ilości materiału z jednoczesnym silnym zagęszczeniem wskutek uderzenia o powierzchnię. Wymagają jednak specjalistycznego sprzętu i doświadczenia.
Po wypełnieniu ubytku, następuje proces wyrównania i wypoziomowania naprawianej powierzchni. Używa się do tego pacy, kielni lub innych narzędzi, aby doprowadzić nowo nałożoną zaprawę do lica otaczającego betonu. Celem jest uzyskanie jednolitej i gładkiej lub odpowiednio teksturowanej powierzchni.
Rodzaj wykończenia zależy od wymagań – może to być zacieranie na gładko metalową pacą, fakturowanie drewnianą lub styropianową pacą, a w przypadku powierzchni antypoślizgowych (np. na pochylniach) zastosowanie szczotkowania lub radełkowania. Ważny jest odpowiedni moment zacierania, gdy zaprawa zaczyna wiązać, ale jest jeszcze podatna na obróbkę.
Zaprawą naprawczą można z powodzeniem uzupełnić ubytki różnej wielkości, od płytkich łuszczeń po głębokie wyłomy odsłaniające zbrojenie. Można jej użyć do naprawić stabilne pęknięcia (po ich odpowiednim poszerzeniu, oczyszczeniu i sczepieniu) oraz inne uszkodzenia betonu, takie jak wykruszenia krawędzi czy zniszczone naroża.
Specjalistyczne zaprawy naprawcze stosuje się zarówno do napraw betonu wewnątrz budynku, gdzie liczy się brak pylenia i szybkie schnięcie, jak i na zewnątrz, gdzie materiał musi być odporny na zmienne warunki atmosferyczne, w tym cykle zamarzania i rozmrażania.
Niektóre systemy naprawcze, szczególnie klasy R4, są formułowane tak, aby sprostać dużym obciążeniom eksploatacyjnym, na przykład w obszarach narażonych na intensywny ruch samochodowy czy wózków widłowych (jak na posadzkach przemysłowych, parkingach czy na mostach). Wymagają one jednak nie tylko wysokiej wytrzymałości, ale także odporności na ścieranie i uderzenia.
Po zakończeniu aplikacji i wstępnym stwardnieniu zaprawy, absolutnie krytycznym etapem, niestety często zaniedbywanym, jest pielęgnacja. Prawidłowa pielęgnacja świeżej zaprawy cementowej jest niezbędna do osiągnięcia pełnej wytrzymałości i minimalizacji skurczu, który mógłby spowodować pęknięcia w nowej warstwie.
Pielęgnacja polega na zapobieganiu zbyt szybkiemu wysychaniu materiału. Można to osiągnąć poprzez przykrycie naprawionej powierzchni folią budowlaną (ogranicza parowanie), matami chłonnymi stale nasycanymi wodą, wilgotnymi workami jutowymi, czy też poprzez natrysk specjalistycznych preparatów do pielęgnacji betonu (tzw. curing compounds), tworzących na powierzchni tymczasową membranę.
Pielęgnacja powinna trwać przez co najmniej 3 do 7 dni, a w przypadku konstrukcji obciążonych lub w warunkach wysokiej temperatury i niskiej wilgotności – nawet dłużej. Pierwsze 24 godziny są najbardziej krytyczne dla hydratacji cementu. To ten etap decyduje o ostatecznej jakości "skóry" i "kości" naprawy.
Temperatura otoczenia podczas aplikacji i wiązania zaprawy ma również znaczenie. Zazwyczaj zaleca się prowadzenie prac w temperaturze od +5°C do +30°C. Zbyt niska temperatura spowalnia wiązanie, zbyt wysoka przyspiesza parowanie wody i może prowadzić do pęknięć. W skrajnych warunkach konieczne może być ogrzewanie lub chłodzenie obszaru naprawy.
Ważne jest, aby pamiętać o czasie otwartym zaprawy, czyli okresie, w którym materiał nadaje się do wbudowania. Przekroczenie tego czasu, zwłaszcza przez dolewanie wody do już częściowo związanej mieszanki, drastycznie obniża parametry końcowe. Należy przygotowywać takie porcje zaprawy, które zostaną zużyte w określonym przez producenta czasie, np. w ciągu 30-60 minut.
Wreszcie, umiejętne użycie narzędzi i ścisłe przestrzeganie instrukcji producenta materiału są tak samo ważne jak sam wybór produktu. Nawet najlepsza zaprawa nie zadziała prawidłowo, jeśli zostanie niewłaściwie wymieszana, zaaplikowana czy nieodpowiednio wypielęgnowana. To połączenie nauki i rzemiosła.
Metody wypełniania ubytków ewoluowały od prostego uzupełniania zaprawą do zaawansowanych, systemowych podejść. Wymagają nie tylko siły fizycznej, ale przede wszystkim wiedzy o procesach chemicznych zachodzących w materiałach i ich interakcji z podłożem i środowiskiem.
Tylko kompleksowe podejście, obejmujące wszystkie etapy – od dokładnej diagnostyki i przygotowania, przez świadomy dobór materiałów, po poprawną aplikację i rygorystyczną pielęgnację – gwarantuje, że naprawa płyty betonowej będzie trwała i przywróci elementowi jego pierwotną funkcjonalność i estetykę na długie lata.