Skład Płyty Fundamentowej: Materiały i Budowa Warstw
Zastanawialiście się kiedyś, co właściwie stanowi solidną bazę dla waszego przyszłego domu? Co sprawia, że budynek stoi niewzruszenie przez dziesięciolecia? Sercem tej stabilności, zwłaszcza w nowoczesnym budownictwie, często okazuje się płyta fundamentowa. Na pytanie Z czego składa się płyta fundamentowa, odpowiedź w skrócie brzmi: to przede wszystkim wytrzymała konstrukcja z żelbetu, spoczywająca na odpowiednio przygotowanych warstwach gruntu.
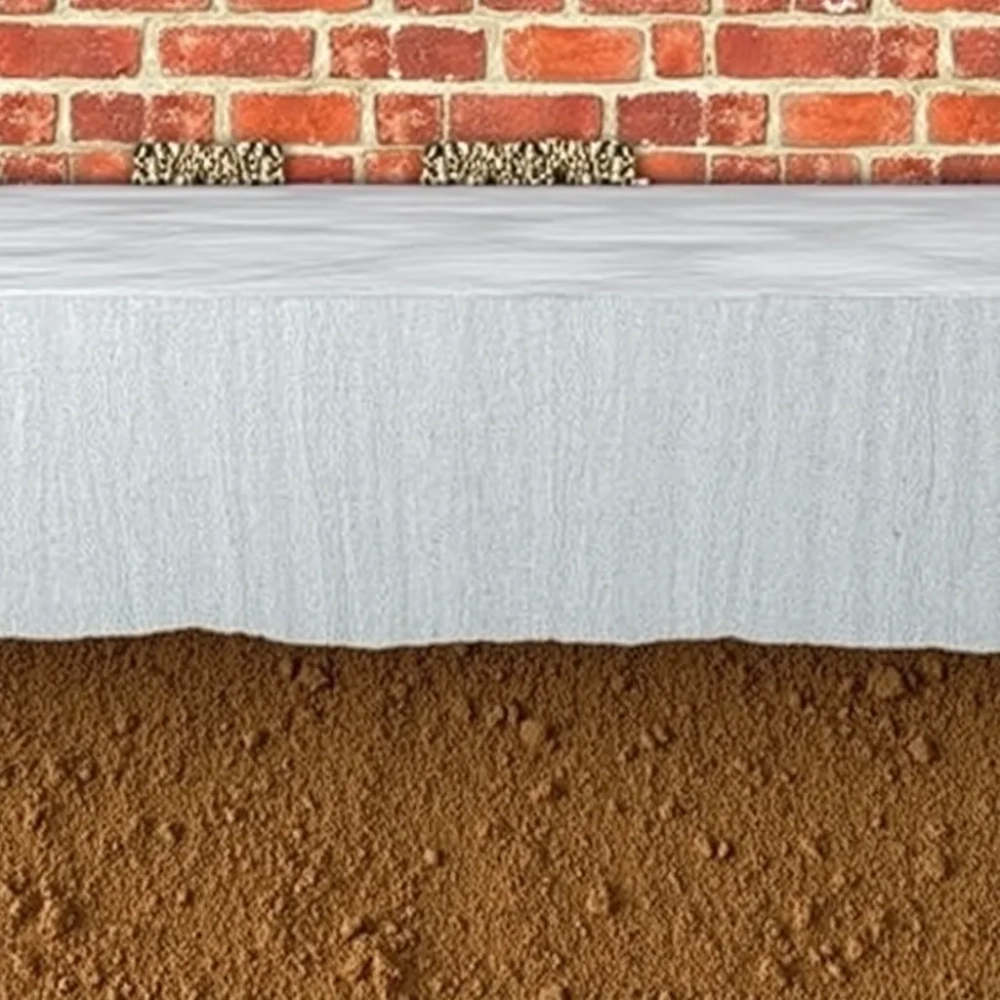
Analizując proces budowy, szybko dostrzegamy, że płyta fundamentowa to nie tylko monolityczny blok betonu. To raczej złożony system warstw i materiałów, których każdy element pełni kluczową rolę. Przyjrzyjmy się danym, które pomagają zrozumieć, jak poszczególne składowe wpływają na finalną konstrukcję.
Element/Warstwa | Typowy materiał | Orientacyjna grubość (cm) | Szacunkowy udział w kosztach materiałów (%) | Uwagi |
---|---|---|---|---|
Warstwa zagęszczonego kruszywa (podbudowa) | Pospółka, żwir, piasek z dodatkiem cementu (stabilizacja) | 20-40 | 10-15 | Wymaga wysokiego stopnia zagęszczenia (min. Is = 1.0) |
Warstwa chudego betonu ("chudziak") | Beton klasy C8/10 (B10) | 10 | 5-8 | Wyrównanie, ochrona termo/hydroizolacji |
Termoizolacja pod płytą | Polistyren ekstrudowany (XPS) | 10-30+ | 20-35 | Grubość zależna od standardu energetycznego budynku |
Hydroizolacja | Geomembrany HDPE, papy termozgrzewalne, folie kubełkowe | 0.1 - 0.5 (położona) | 5-10 | Ochrona przed wilgocią i wodą gruntową |
Płyta żelbetowa (beton konstrukcyjny) | Beton klasy min. C25/30 (B30) | 15-40+ | 25-40 | Grubość zależna od obciążeń i rozpiętości |
Płyta żelbetowa (zbrojenie) | Pręty stalowe (np. B500SP), siatki zgrzewane (np. Q335) | (Rozłożone w 1 lub 2 warstwach) | 15-20 | Typ i ilość zależne od obliczeń statycznych |
Patrząc na przedstawione dane, od razu widać, że płyta fundamentowa to przedsięwzięcie wielowymiarowe, gdzie materiały izolacyjne i podbudowa stanowią znaczący udział w strukturze i kosztach, dorównując, a czasem przewyższając udział samego betonu konstrukcyjnego czy stali zbrojeniowej. To pouczający przykład, że skupienie się wyłącznie na samym betonie w opisie "z czego składa się płyta fundamentowa" byłoby poważnym uproszczeniem, ignorującym krytyczne aspekty stabilności i izolacyjności.
Dopiero pełne zrozumienie roli każdej z tych warstw, od najniższej, czyli odpowiednio przygotowanego gruntu, przez izolacje, aż po zbrojony beton na górze, pozwala docenić inżynieryjną złożoność tego elementu. Każdy krok w procesie budowy płyty fundamentowej musi być precyzyjnie zaplanowany i wykonany, ponieważ błędy na tym etapie są niezwykle trudne i kosztowne do naprawienia, mając bezpośredni wpływ na trwałość i komfort użytkowania całego budynku.
Warstwy przygotowawcze pod płytę fundamentową
Zanim na plac budowy wjedzie pierwsza betoniarka z mieszanką na płytę fundamentową, dzieje się wiele. Podstawą, dosłownie i w przenośni, są odpowiednie warstwy przygotowawcze. Można powiedzieć, że to jak budowanie gładkiej, mocnej autostrady, na której stanie cały dom – bez solidnej bazy wszystko inne może się zawalić.
Pierwszym, absolutnie krytycznym etapem jest odpowiednie przygotowanie podłoża gruntowego. Często wymaga to zdjęcia wierzchniej, urodzajnej warstwy ziemi (humusu), a następnie pogłębienia wykopu do poziomu nośnego gruntu, wolnego od zamarzania – w Polsce to zwykle kilkadziesiąt centymetrów, zależnie od regionu i strefy przemarzania.
Po ukształtowaniu dna wykopu, kluczowe staje się zagęszczenie gruntu rodzimego. Jeśli nośność naturalnego podłoża jest niewystarczająca lub zróżnicowana, konieczna jest wymiana części gruntu na lepszy materiał lub zastosowanie stabilizacji, na przykład przez dodanie cementu i intensywne zagęszczanie mechaniczne wibratorami płytowymi lub wałami. Osiągnięcie wymaganego stopnia zagęszczenia (np. wskaźnik zagęszczenia Is > 1,0 dla gruntów spoistych) jest weryfikowane badaniami geotechnicznymi, co bywa momentem prawdy na każdej budowie.
Następnie, na tak przygotowanym i zagęszczonym gruncie układa się podbudowę z materiałów sypkich – najczęściej jest to odpowiednio uziarnione kruszywo, jak żwir lub mieszanka piaskowo-żwirowa. Warstwa ta ma za zadanie równomiernie rozłożyć obciążenia z płyty na większą powierzchnię gruntu rodzimego i często służy jako drenaż, odprowadzający wodę pod płytą. Jej typowa grubość wynosi od 20 do 40 cm.
Ważne jest, aby tę warstwę kruszywa również starannie zagęścić – często warstwami po 10-15 cm, stosując kilkukrotne przejścia sprzętu zagęszczającego. Mówimy tu o precyzji inżynierskiej; niedostateczne zagęszczenie spowoduje późniejsze osiadanie podbudowy, co może doprowadzić do zarysowań, a nawet pęknięć w płycie fundamentowej. Koszt kruszywa to średnio 60-100 zł za tonę, a na standardowy dom o powierzchni 120m² podbudowa grubości 30 cm może wymagać ponad 50-60 ton, co daje znaczący koszt materiału, rzędu 3000-6000 zł, nie licząc pracy sprzętu.
Na warstwie zagęszczonego kruszywa często układa się warstwę chudego betonu, potocznie nazywanego "chudziakiem". Ten element, zwykle o grubości 10 cm, nie pełni funkcji nośnej w sensie przenoszenia obciążeń budynku, ale jest nieoceniony jako czysta i równa powierzchnia robocza. Chroni on kolejne warstwy – izolację termiczną i hydroizolacyjną – przed uszkodzeniami mechanicznymi podczas prac budowlanych.
Chudziak wykonuje się zazwyczaj z betonu niskiej klasy wytrzymałości, np. C8/10 (B10). Jego ułożenie ułatwia precyzyjne rozmieszczenie zbrojenia oraz układanie materiałów izolacyjnych i hydroizolacyjnych, zapewniając, że folie nie zostaną przedziurawione przez ostre kamienie z podbudowy, a płyty termoizolacyjne będą leżeć idealnie płasko. Koszt chudziaka to około 250-350 zł za m³ betonu, więc dla 120 m² płyty o grubości 10 cm będzie to 12 m³ betonu, czyli około 3000-4200 zł za sam materiał betonowy.
Studium przypadku z życia: Widzieliśmy kiedyś budowę, gdzie oszczędzano na zagęszczaniu podbudowy i chudziaku, układając izolację bezpośrednio na słabo wyrównanym kruszywie. Skończyło się na uszkodzeniach płyt XPS podczas zbrojenia i zalaniem budowy po niewielkich opadach deszczu, bo folia ochronna nie miała gładkiej podpory. Oszczędność kilku tysięcy zamieniła się w dziesiątki tysięcy złotych strat i opóźnień. To najlepszy dowód, że warstwy przygotowawcze to nie opcjonalny dodatek, a fundament stabilności całej konstrukcji.
Dodatkowo, w niektórych przypadkach, na etapie podbudowy lub chudziaka wykonuje się poziomy drenaż opaskowy lub punktowe studzienki zbierające wodę gruntową, połączone z systemem odwodnienia działki. Zapobiega to podnoszeniu się lustra wody gruntowej i stałemu naciskowi hydrostatycznemu na spód płyty fundamentowej. Jest to szczególnie ważne na gruntach o niskiej przepuszczalności, jak gliny czy iły.
Podsumowując, przygotowanie podłoża to proces wymagający geotechnicznej wiedzy, odpowiedniego sprzętu i skrupulatności. Grunt, podbudowa z kruszywa i chudziak – te warstwy, choć ukryte po zalaniu płyty, mają fundamentalne znaczenie dla jej prawidłowego działania i długowieczności. Zaniedbanie tego etapu to prosta droga do problemów konstrukcyjnych w przyszłości. Na tym etapie decyduje się często o przyszłej stabilności budynku, zanim pojawi się beton i stal.
Pamiętajmy, że na etapie projektowania płyty fundamentowej kluczowa jest opinia geotechniczna. To geotechnik bada grunt, określa jego nośność gruntu, poziom wód gruntowych i na tej podstawie wydaje zalecenia dotyczące zakresu i metody przygotowania podłoża. Bez tej wiedzy, każde działanie na tym etapie jest jak loteria – można trafić dobrze, ale ryzyko kosztownego błędu jest bardzo wysokie. Właśnie dlatego doświadczenie projektanta konstrukcji idzie w parze z rzetelnymi badaniami gruntu.
Kruszywo używane do podbudowy powinno spełniać określone normy dotyczące uziarnienia i czystości. Najczęściej stosuje się pospółkę, czyli naturalną mieszankę piasku i żwiru, lub kruszywo łamane. Cena i dostępność mogą się różnić w zależności od regionu, ale zawsze warto pytać o dokumenty potwierdzające pochodzenie i parametry materiału, by uniknąć przywiezienia na budowę zanieczyszczonego czy niejednorodnego materiału, który utrudni lub uniemożliwi prawidłowe zagęszczenie.
Przygotowanie podłoża obejmuje również dokładne wytyczenie obrysu płyty fundamentowej. Odbywa się to za pomocą palików i żyłek lub profesjonalnego sprzętu geodezyjnego. Wymiary i geometria muszą być zgodne z projektem z dokładnością do milimetrów, ponieważ każdy błąd na tym etapie będzie miał wpływ na położenie ścian nośnych i innych elementów konstrukcyjnych wyższych kondygnacji. W praktyce, dobre wytyczenie to połowa sukcesu przed wylaniem betonu.
Warto również pamiętać o ewentualnym poprowadzeniu przez podbudowę lub chudziak niezbędnych instalacji podpodłogowych parteru, np. rur kanalizacyjnych, osłon dla instalacji elektrycznych czy wodnych, które będą wychodzić z płyty. Te przejścia muszą być zaprojektowane i wykonane szczelnie, często z użyciem specjalnych kołnierzy lub przepustów systemowych, aby w przyszłości nie stanowiły drogi wnikania wilgoci do wnętrza budynku. Lepiej pomyśleć o tym wcześniej, niż później kuć gotowy beton.
Wykonanie warstw przygotowawczych to praca brudna, wymagająca fizycznego wysiłku i zaangażowania ciężkiego sprzętu budowlanego. To etap, na którym widać, ile ziemi trzeba przemieścić, zanim pojawi się cokolwiek, co przypomina fundament. Czasem, patrząc na góry wykopanej ziemi i tony nawiezionego kruszywa, zastanawiamy się, jak wiele pracy kryje się pod prostym hasłem "przygotowanie podłoża".
Nie można zlekceważyć roli geomembran w ochronie podbudowy przed wilgocią pochodzącą z góry (np. opadami deszczu podczas budowy). Nawet tymczasowe przykrycie świeżo ułożonego kruszywa folią może uchronić je przed rozmoknięciem, co wymagałoby ponownego suszenia i zagęszczania, generując dodatkowe koszty i opóźnienia. Planowanie na budowie to też przewidywanie pogody.
Dobrze wykonana warstwa chudego betonu jest gładka i pozioma, idealnie nadająca się do klejenia płyt termoizolacyjnych lub układania membrany hydroizolacyjnej. Jej powierzchnia powinna być na tyle równa, by uniknąć powstawania pustek powietrznych pod izolacją, które mogłyby stać się mostkami termicznymi lub miejscami zbierania się wilgoci. To detale, które decydują o jakości końcowego produktu.
Kwestia drenażu pod płytą to temat na osobną dyskusję, ale warto wspomnieć, że na niektórych gruntach jest on absolutnie niezbędny. Nadmiar wody gruntowej pod płytą może obniżać nośność podłoża, a w przypadku mrozów – powodować wysadziny, czyli pękanie gruntu wskutek zamarzania wody i zwiększenia jej objętości, co prowadziłoby do uniesienia płyty i uszkodzenia konstrukcji. System drenażu to ubezpieczenie przed takimi problemami, szczególnie tam, gdzie poziom wód gruntowych jest wysoki.
Wreszcie, przed przystąpieniem do dalszych prac, wszystkie warstwy przygotowawcze, łącznie z chudziakiem, powinny zostać dokładnie oczyszczone z resztek gruzu, ziemi czy innych zanieczyszczeń. Czysta powierzchnia robocza to nie tylko estetyka, ale przede wszystkim zapewnienie prawidłowego ułożenia i działania kolejnych warstw, zwłaszcza delikatnej termoizolacji i hydroizolacji. To pokazuje, że diabeł tkwi w szczegółach, a staranność na każdym etapie się opłaca.
Żelbet: Beton konstrukcyjny i zbrojenie
Mówiąc o tym, Z czego składa się płyta fundamentowa, nie sposób pominąć jej rdzenia – żelbetu. To magiczne połączenie betonu i stali zbrojeniowej tworzy materiał o niezwykłej wytrzymałości, zdolny przenieść potężne obciążenia całego budynku na podłoże. To jest ten moment, kiedy na budowie pojawiają się armatura i ciężkie pojazdy z mieszanką betonową.
Sam beton konstrukcyjny to materiał o doskonałej wytrzymałości na ściskanie, ale znacznie gorzej radzący sobie z siłami rozciągającymi i zginającymi. Tutaj właśnie wkracza stal zbrojeniowa, która przejmuje te siły. W żelbecie beton i stal współpracują ze sobą dzięki zjawisku adhezji (przyczepności) oraz odpowiedniemu otuleniu prętów stalowych betonem, co chroni je przed korozją.
Do budowy płyt fundamentowych najczęściej stosuje się beton klasy C25/30 (dawniej B30) lub C30/37 (dawniej B37). Pierwsza liczba oznacza wytrzymałość charakterystyczną na ściskanie określoną na próbkach walcowych (w MPa), a druga na próbkach sześciennych. Wybór konkretnej klasy betonu jest ściśle powiązany z projektem konstrukcyjnym, który bierze pod uwagę przewidywane obciążenia oraz warunki środowiskowe (np. ekspozycja na wilgoć, mróz). Cena betonu klasy C25/30 to orientacyjnie 300-400 zł/m³, a C30/37 nieco więcej. Przy płycie 120 m² o grubości 20 cm, potrzeba 24 m³ betonu, co oznacza koszt rzędu 7200-9600 zł za sam beton.
Bardzo ważne są parametry betonu dostarczanego na budowę, nie tylko klasa wytrzymałości. Istotna jest również klasa konsystencji (tzw. slump), która określa "płynność" betonu. Zbyt suchy beton jest trudny w układaniu i zagęszczaniu, zbyt mokry może mieć obniżoną wytrzymałość i segregować się (rozdzielać na składniki). Często stosuje się domieszki uplastyżniające lub superplastyfikujące, które poprawiają urabialność betonu przy zachowaniu niskiego stosunku wody do cementu, co jest kluczowe dla wytrzymałości i trwałości betonu. Domieszki mrozoodporne są niezbędne przy betonowaniu w niskich temperaturach.
Drugim filarem żelbetu jest zbrojenie stalowe. Składa się ono z prętów stalowych (najczęściej o średnicach Ø10, Ø12, Ø16 mm, wykonanych ze stali klasy B500SP, charakteryzującej się wysoką plastycznością i wytrzymałością), siatek zgrzewanych (np. typu Q188, Q335 – oznaczenie typu Q335 oznacza siatkę o powierzchni przekroju drutów 3.35 cm²/mb w obu kierunkach), a także ze strzemion czy prętów dystansowych, tzw. "raków" lub "kóz", które utrzymują zbrojenie we właściwej pozycji w szalunku. Rodzaj i ilość stali określa projektant konstrukcji na podstawie obliczeń statycznych.
Typowy zakres zużycia stali zbrojeniowej w płycie fundamentowej to od 10 do 25 kg na metr kwadratowy powierzchni płyty. W przypadku prostych domów jednorodzinnych zbrojenie może składać się z dwóch warstw siatek zgrzewanych (np. Q188 lub Q257) umieszczonych w górnej i dolnej części płyty, z dodatkowymi prętami wzmacniającymi pod ścianami nośnymi. W przypadku większych rozpiętości, większych obciążeń czy specyficznej geometrii budynku, zbrojenie staje się znacznie bardziej skomplikowane i może wymagać zastosowania grubszych prętów oraz gęstszego ich ułożenia.
Montaż zbrojenia to precyzyjna praca. Pręty i siatki są układane zgodnie z rysunkami warsztatowymi, wiązane drutem wiązałkowym w miejscach krzyżowania się. Kluczowe jest zachowanie odpowiedniego otulenia zbrojenia, czyli minimalnej grubości warstwy betonu między stalą a powierzchnią płyty (zazwyczaj 5-7 cm na spodzie i 3-5 cm na wierzchu), aby chronić stal przed korozją. Służą do tego plastikowe lub betonowe podkładki dystansowe. Cena stali zbrojeniowej waha się, ale orientacyjnie to 4000-5000 zł za tonę. Zużycie 15 kg/m² na 120 m² daje 1.8 tony stali, kosztującą około 7200-9000 zł.
Po ułożeniu zbrojenia, instalacji elektrycznych i hydraulicznych przechodzących przez płytę, montuje się deskowanie krawędziowe. Może być ono tradycyjne (drewniane lub ze sklejki) lub wykonane ze stałych elementów traconych, np. z profilowanych płyt XPS, które dodatkowo izolują krawędź płyty. Staranność wykonania szalunku wpływa na kształt i wymiary gotowej płyty.
Wylanie betonu na płytę fundamentową to zwykle logistyczne wyzwanie. Beton dostarczany jest betonomieszarkami, a następnie pompowany na miejsce lub zsypywany bezpośrednio. Równomierne rozłożenie i zagęszczanie betonu są kluczowe dla usunięcia pęcherzy powietrza, które mogłyby osłabić konstrukcję. Stosuje się do tego wibratory do betonu, zarówno wgłębne (buławy), jak i listwy wibracyjne.
Proces pielęgnacji świeżego betonu po wylaniu jest równie ważny jak samo betonowanie. Przez kilka dni beton musi być chroniony przed zbyt szybkim wysychaniem (przez polewanie wodą, przykrywanie folią) lub przed mrozem. Prawidłowa pielęgnacja pozwala betonowi osiągnąć docelową wytrzymałość i zapobiega powstawaniu rys skurczowych. To tak, jak z pieczeniem ciasta – trzeba mu dać odpowiedni czas w spokoju, by stwardniało jak należy.
Cały proces – od ułożenia zbrojenia, przez deskowanie, po betonowanie i pielęgnację – musi być prowadzony pod nadzorem wykwalifikowanych pracowników i kierownika budowy. Każdy błąd, np. niewłaściwe otulenie, pominięcie fragmentu zbrojenia, niewystarczające zagęszczenie betonu czy niewłaściwa pielęgnacja, może skutkować osłabieniem konstrukcji płyty, a w najgorszym wypadku koniecznością wykonania kosztownych wzmocnień lub rozbiórki wadliwego elementu. Płyta fundamentowa to serce konstrukcji, na którym nie wolno oszczędzać ani w materiałach, ani w jakości wykonania. To, ile stali i betonu w nią włożymy i jak to zrobimy, przesądza o stabilności na lata.
Warto dodać, że przy projektowaniu zbrojenia bierze się pod uwagę nie tylko obciążenia pionowe od ciężaru budynku, ale również obciążenia poziome, momenty zginające oraz wpływ specyficznych warunków gruntowych, takich jak skurczliwość czy pęcznienie gruntów ilastych. Precyzyjne obliczenia statyczne pozwalają dobrać optymalne średnice i rozmieszczenie prętów oraz siatek, aby płyta działała jako monolityczna tarcza rozkładająca naprężenia.
Stal zbrojeniowa klasy B500SP charakteryzuje się specyficzną strukturą powierzchni (żebrowaniem), która zapewnia doskonałą przyczepność do betonu. Ważne jest, aby na budowę trafiała stal atestowana, z potwierdzeniem jej właściwości mechanicznych, ponieważ jakość zbrojenia ma bezpośrednie przełożenie na wytrzymałość całego elementu żelbetowego. Oszczędzanie na stali, kupując materiał z niepewnego źródła, jest niezwykle ryzykownym posunięciem.
Zagęszczanie betonu wibratorami nie jest tylko formalnością. Pozwala ono usunąć pęcherze powietrza (tzw. raki), które zmniejszałyby efektywny przekrój betonu i stanowiłyby miejsca łatwego przenikania wilgoci, prowadząc do korozji zbrojenia. Prawidłowe wibrowanie zapewnia, że mieszanka betonowa szczelnie otoczy każdy pręt zbrojeniowy, tworząc jednorodny, mocny element. "Patrzcie, żeby każdy pręt był otulony betonem jak kołderką" – często powtarza się na budowach, obrazowo wyjaśniając ten proces.
Poziom powierzchni betonu w płycie fundamentowej powinien być precyzyjnie wyrównany, ponieważ często stanowi on podłoże dla dalszych prac wykończeniowych parteru, takich jak ułożenie izolacji termicznej posadzki czy instalacji ogrzewania podłogowego. Niewielkie nierówności można skorygować jastrychem, ale znaczące odchylenia od poziomu mogą być źródłem problemów w dalszych etapach budowy. Tolerancje wykonawcze są ściśle określone w normach budowlanych i projektach.
Na tym etapie prac ważne jest również uwzględnienie wszelkich przejść instalacyjnych przez płytę, takich jak rury kanalizacyjne czy przepusty dla mediów (prąd, woda, gaz). Powinny być one zaprojektowane tak, aby minimalizować ryzyko powstawania mostków termicznych lub przecieków. Stosowanie systemowych rozwiązań zintegrowanych z izolacją i hydroizolacją jest najlepszym rozwiązaniem, zapewniającym szczelność i ciągłość warstw.
Koszt betonu i stali stanowi zazwyczaj największą pojedynczą pozycję w kosztorysie materiałów na płytę fundamentową, co naturalnie skłania do szukania oszczędności. Jednak doświadczeni budowlańcy i projektanci zgodnie twierdzą, że to nie jest element, na którym wolno i warto ciąć koszty. Inwestycja w beton o odpowiedniej klasie i atestowaną stal, ułożone zgodnie ze sztuką i projektem, zwraca się w postaci trwałości, bezpieczeństwa i spokoju na lata. W tej grze, „lepsze” nie jest wrogiem „dobrego”, jest po prostu koniecznością.
Termoizolacja i hydroizolacja – klucz do energooszczędności
Współczesna płyta fundamentowa, w przeciwieństwie do tradycyjnych ław, stwarza unikalną możliwość ocieplenia całego budynku od spodu, eliminując jeden z największych mostków termicznych – nieizolowaną posadzkę na gruncie. Można śmiało powiedzieć, że odpowiednia termoizolacja pod płytą jest kluczem do energooszczędności budynku, zwłaszcza w standardzie niskoenergetycznym czy pasywnym.
Termoizolacja pod płytą fundamentową jest najczęściej wykonywana z polistyrenu ekstrudowanego (XPS). Materiał ten, w odróżnieniu od zwykłego styropianu (EPS), charakteryzuje się znacznie wyższą odpornością na ściskanie (często 300-500 kPa lub więcej) oraz minimalną nasiąkliwością, co czyni go idealnym do zastosowania w warunkach gruntowych, gdzie panuje wilgoć i obciążenia od ciężaru budynku. XPS jest układany bezpośrednio na chudziaku lub na warstwie hydroizolacji.
Grubość izolacji termicznej jest kluczowa dla efektywności energetycznej i powinna być dobrana zgodnie z projektem, który uwzględnia wymagania danego standardu. Dla budynków niskoenergetycznych to często 15-20 cm, natomiast dla budynków pasywnych minimum 20 cm, a nierzadko 25-30 cm lub nawet więcej, układane w dwóch lub trzech warstwach "na zakładkę", aby wyeliminować mostki termiczne na stykach płyt. Współczynnik przewodzenia ciepła lambda (λ) dla dobrej jakości XPS wynosi około 0,033-0,035 W/mK. Im niższa wartość lambda, tym lepsza izolacyjność materiału.
Koszt płyt XPS do izolacji fundamentów jest znaczący. Cena za m³ XPS o standardowej gęstości to orientacyjnie 700-1000 zł, w zależności od producenta i specyficznych parametrów. Przyjmując średnio 20 cm grubości na 120 m² płyty, potrzeba 24 m³ materiału, co daje koszt w granicach 16 800 - 24 000 zł za samą izolację. Jak widać w tabeli z danymi, jest to jedna z droższych pozycji materiałowych, ale inwestycja ta przekłada się bezpośrednio na niższe rachunki za ogrzewanie przez cały okres eksploatacji budynku. Ocieplenie płyty fundamentowej jest jednym z najskuteczniejszych sposobów na walkę z ucieczką ciepła.
Równie ważnym, o ile nie ważniejszym z punktu widzenia trwałości konstrukcji, elementem jest hydroizolacja. Jej zadaniem jest uszczelnienie podbudowy i płyty od spodu przed wodą gruntową (zwłaszcza tą pod ciśnieniem) i wilgocią kapilarną podciągającą z gruntu. Uszkodzenie hydroizolacji może prowadzić do zawilgocenia płyty betonowej, a w konsekwencji do jej degradacji, korozji zbrojenia, a także do pojawienia się pleśni i grzybów w pomieszczeniach. Wykonanie solidnej i trwałej warstwy hydroizolacji pod płytą jest absolutnym priorytetem.
Stosuje się różne rodzaje materiałów hydroizolacyjnych. Jednym z najpopularniejszych są membrany kubełkowe z HDPE o wysokiej gramaturze (np. 500 g/m²) lub specjalistyczne geomembrany zgrzewane na łączeniach. Inną opcją są papy termozgrzewalne modyfikowane elastomerami (typu BARDZO S) lub grubowarstwowe, elastyczne powłoki bitumiczne (tzw. KMB). Wybór materiału zależy od specyfiki warunków gruntowo-wodnych na działce (np. czy mamy do czynienia z wodą pod ciśnieniem) i jest ściśle określony w projekcie. Cena materiałów hydroizolacyjnych waha się od 15 do 50 zł za m², w zależności od typu i grubości.
Prawidłowe ułożenie warstw izolacyjnych (termo- i hydro-) jest niezwykle ważne. Najczęściej spotyka się dwa schematy: hydroizolacja na chudziaku, a na niej termoizolacja, lub termoizolacja na chudziaku, a hydroizolacja na niej, przed betonowaniem płyty. Pierwszy wariant (hydro -> termo -> beton) lepiej chroni izolację termiczną przed wilgocią z gruntu, natomiast drugi (termo -> hydro -> beton) zapewnia lepszą ochronę płyty betonowej, zwłaszcza przed wodą pod ciśnieniem, pod warunkiem, że hydroizolacja jest wykonana z materiału odpornego na przebicie, jak geomembrana zgrzewana. Termoizolacja i hydroizolacja muszą tworzyć szczelną, ciągłą barierę wokół całej powierzchni płyty.
Szczególną uwagę należy poświęcić połączeniu hydroizolacji poziomej pod płytą z hydroizolacją pionową ścian fundamentowych lub cokołu. Jest to miejsce, gdzie najczęściej pojawiają się błędy wykonawcze prowadzące do przecieków. Musi być zapewniona ciągłość izolacji, często przez wywinięcie membrany lub papy na krawędź płyty i połączenie jej z późniejszą izolacją pionową ściany, co wymaga precyzji i zastosowania odpowiednich systemowych rozwiązań uszczelniających.
Montaż płyt XPS wymaga równego i czystego podłoża. Płyty układa się ściśle jedna przy drugiej, na mijankę (jak cegły w murze), aby ograniczyć mostki termiczne. Położenie płyt w dwóch warstwach z przesunięciem spoin eliminuje przenikanie zimna. Płyty powinny być dociśnięte do siebie, bez pustek powietrznych między nimi, a ich połączenia dodatkowo uszczelnione np. specjalną taśmą. Każde, nawet niewielkie uszkodzenie płyty izolacyjnej, może stać się mostkiem termicznym. Dlatego też chronienie ich przed nadepnięciem, rozlaniem betonu czy innymi zanieczyszczeniami podczas prac budowlanych jest kluczowe.
Geomembrany HDPE są układane w dużych arkuszach i zgrzewane na łączeniach za pomocą specjalistycznych zgrzewarek. Proces ten wymaga doświadczenia i kwalifikacji, a szczelność zgrzewów jest często weryfikowana metodami ciśnieniowymi. Wywinięcie membrany na krawędzi płyty (a właściwie poza jej obrys, na wysokość przyszłego cokołu) jest niezbędne do połączenia z izolacją pionową. Kubełkowe membrany hydroizolacyjne wymagają również starannego ułożenia, często z wykorzystaniem taśm uszczelniających na zakładach, choć nie tworzą one tak monolitycznej bariery jak zgrzewane geomembrany.
Ocieplenie i hydroizolacja płyty fundamentowej to inwestycje, które zwracają się w czasie eksploatacji budynku, zarówno poprzez oszczędności na ogrzewaniu, jak i brak kosztów związanych z naprawą szkód spowodowanych zawilgoceniem czy niską efektywnością energetyczną. Na budowie domu energooszczędnego czy pasywnego te elementy są traktowane z najwyższą starannością i są pod stałą kontrolą kierownika budowy oraz projektanta.
Patrząc na globalny trend wzrostu cen energii i zaostrzania wymagań dotyczących energooszczędności w budownictwie (jak standard WT 2021 w Polsce), dobrze zaizolowana płyta fundamentowa przestaje być luksusem, a staje się standardem. Inwestycja w solidne ocieplenie pod płytą (np. 20-30 cm XPS) i skuteczną hydroizolację to przewidywalny koszt początkowy, który chroni przed nieprzewidywalnymi, znacznie wyższymi kosztami eksploatacyjnymi i remontowymi w przyszłości. To po prostu klucz do energooszczędności i komfortu mieszkania, który raz wykonany poprawnie, służy przez dziesięciolecia.
Czasem na budowie, gdy układane są kolejne warstwy izolacji, widok ten może być dla laika zaskoczeniem – "Aż tyle styropianu idzie pod ten beton?". Tak, idzie. I to właśnie ten pozornie prosty materiał, chroniony przez solidną membranę hydroizolacyjną, w połączeniu z odpowiednio wykonanym betonem i zbrojeniem, tworzy zaawansowany technologicznie element, jakim jest nowoczesna płyta fundamentowa. To cichy bohater każdego energooszczędnego domu.