Ciepła Płyta Fundamentowa: Przekrój, Warstwy i Budowa (2025)
Zagadnienie ciepła płyta fundamentowa przekrój to nie tylko schemat na papierze, ale fascynująca mozaika starannie dobranych warstw, z których każda pełni kluczową rolę w budowaniu trwałości i efektywności energetycznej domu; krótko mówiąc, to wielowarstwowa konstrukcja betonowo-izolacyjna spoczywająca bezpośrednio na przygotowanym gruncie, stanowiąca solidną podstawę i termiczną barierę zarazem. Zrozumienie jej budowy wymaga zajrzenia pod powierzchnię – dosłownie. To nie tylko "kawał betonu", jak by się mogło wydawać laickim okiem. Przyznam, sam kiedyś tak myślałem, dopóki nie zgłębiłem tematu.
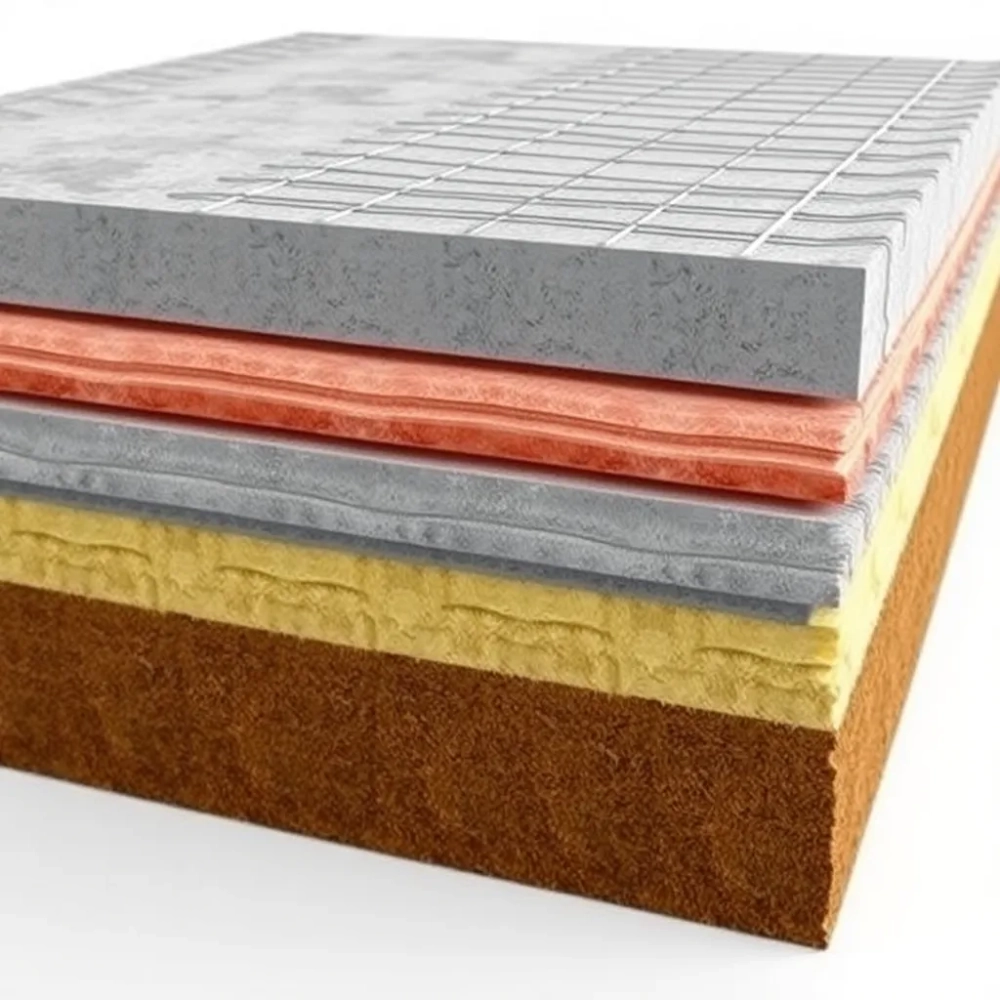
Przyjrzyjmy się bliżej faktom i liczbom, które często umykają w ogólnych dyskusjach o płytach fundamentowych. Różnice w grubościach materiałów i ich parametrach termoizolacyjnych potrafią radykalnie zmienić charakterystykę całej przegrody. Oto zarys typowych parametrów, z którymi spotykają się projektanci i wykonawcy na placu budowy.
Warstwa | Przykładowy Materiał | Typowa Grubość/Ilość | Orientacyjny Koszt (za jednostkę) |
---|---|---|---|
Podsypka/Podbudowa | Żwir/Kruszywo łamane 0-31.5 mm | 20 - 30 cm | ok. 40 - 70 zł/tona (z transportem) |
Izolacja Termiczna pod płytą | Polistyren ekstrudowany (XPS) λ≤0.035 W/mK | 2 x 10 cm (lub 25-30 cm w jednej warstwie) | ok. 350 - 500 zł/m³ |
Folia/Membrana hydroizolacyjna | Folia PE 0.5-1.0 mm / Membrana EPDM | 1 - 2 warstwy | ok. 5 - 15 zł/m² |
Płyta betonowa | Beton C25/30 | 15 - 25 cm | ok. 300 - 450 zł/m³ (gotowa mieszanka) |
Zbrojenie płyty | Stal zbrojeniowa B500SP (fi 10-14) | ok. 50 - 80 kg/m³ betonu | ok. 4 - 6 zł/kg (z prętów) |
Izolacja obwodowa (fartuch) | Polistyren ekstrudowany (XPS) | 10 - 15 cm | ok. 350 - 500 zł/m³ |
Te liczby to punkt wyjścia do głębszej analizy projektowej. Widzimy, że izolacja termiczna stanowi znaczący element kosztowy i grubościowy w całym przekroju płyty. Dokładny dobór parametrów każdego komponentu jest podyktowany obciążeniami projektowymi, lokalnymi warunkami gruntowymi i, co najważniejsze w przypadku "ciepłej" płyty, wymaganiami energetycznymi stawianymi budynkowi. Pamiętajmy, że to inwestycja na lata, a każdy centymetr izolacji i kilogram stali ma swoje uzasadnienie w przyszłej eksploatacji.
Podsypka, Izolacja Przeciwwilgociowa i Przygotowanie Gruntu pod Płytą
Zanim na budowie pojawi się pierwsza partia betonu, fundament przyszłego domu zaczyna się tworzyć znacznie głębiej – w gruntach, na których ma spocząć konstrukcja. To jest ten moment, gdy "kopanie w ziemi" nabiera zupełnie nowego wymiaru; to strategiczny etap, który wymaga precyzji geodety i twardej ręki operatora koparki. Wbrew pozorom, to właśnie tu rozstrzyga się spora część późniejszej stabilności i trwałości.
Pierwszym krokiem, absolutnie kluczowym, jest analiza podłoża gruntowego. Czasami geotechnik staje się na chwilę najbardziej zapracowanym człowiekiem na placu budowy. To on swoimi badaniami dostarcza danych o nośności, spoistości i poziomie wód gruntowych – informacjach tak ważnych, że błędy na tym etapie mogą zagrozić całemu przedsięwzięciu. Pamiętam projekt, gdzie zlekceważono badanie gruntu i skończyło się na konieczności wymiany ogromnej ilości ziemi na dowieziony materiał, co pochłonęło spore dodatkowe fundusze. Nigdy nie żałujcie kilku tysięcy na dobre badanie geotechniczne.
Usunięcie warstwy humusu jest kolejnym, pozornie prozaicznym zadaniem, ale absolutnie niezbędnym. Organiczna warstwa ziemi, często bogata w próchnicę, świetnie nadaje się do ogrodu, ale kompletnie nie do fundamentu. Jest niestabilna, podatna na procesy gnilne i osiadanie – wszystko, czego fundament nienawidzi. Trzeba ją zdjąć do warstwy nośnej, która da gwarancję, że za kilka lat dom nie zacznie osiadać nierównomiernie, niczym stary pancernik. Minimalna głębokość usunięcia humusu to zwykle 20-30 cm, ale na terenach o grubszej warstwie urodzajnej ziemi, może sięgać znacznie głębiej.
Następnie przychodzi czas na wyrównanie i zagęszczenie gruntu rodzimego pod planowany obrys płyty. Równa powierzchnia to podstawa do precyzyjnego ułożenia kolejnych warstw, a odpowiednie zagęszczenie zwiększa jego nośność i minimalizuje ryzyko osiadania. Na gruntach piaszczystych i sypkich często stosuje się metody dynamiczne, na przykład ubijanie gruntu ciężkim sprzętem, co jest widowiskowe, ale przede wszystkim skuteczne w zwiększaniu jego gęstości. Prawidłowe zagęszczenie powinno osiągnąć wskaźnik zagęszczenia Is minimum 0.95 dla większości gruntów nośnych.
Po przygotowaniu podłoża rodzimego, wykonuje się wykop pod fundament, zazwyczaj o głębokości około 30-50 cm, co pozwala na swobodne umieszczenie kluczowej warstwy - podsypki. Ta warstwa to nie tylko "coś, czym zasypiemy dziurę". Podsypka, często zwana podbudową, pełni wiele strategicznych funkcji. Jest drenażem, który odprowadzi wodę spod płyty, chroniąc izolację i konstrukcję przed jej negatywnym działaniem. Umożliwia również równomierne rozłożenie obciążeń z płyty na większą powierzchnię gruntu rodzimego, redukując punktowe naprężenia. Wyobraźmy sobie, że płyta fundamentowa to tort, a podsypka to talerz, na którym spoczywa – bez stabilnego talerza, tort może się zniekształcić lub pęknąć.
Materiał na podsypkę to zwykle czysty żwir, kruszywo łamane frakcji 0-31.5 mm, pospółka (naturalna mieszanka piasku i żwiru) lub nawet zagęszczony piasek stabilizowany cementem. Najważniejsze są jego właściwości filtracyjne i zdolność do zagęszczenia. Warstwa ta ma typowo od 15 do 30 cm grubości. Jej ścisłość, czyli poziom zagęszczenia, ma kolosalne znaczenie. Uzyskuje się ją poprzez mechaniczną wibrację zagęszczarkami płytowymi lub walcami, często z jednoczesnym nawilżaniem materiału, co ułatwia przesuwanie ziaren i osiągnięcie optymalnej gęstości objętościowej. Wskaźnik zagęszczenia podsypki również powinien wynosić minimum 0.97.
Nad podsypką pojawia się niezbędna bariera – izolacja przeciwwilgociowa. To pierwsza linia obrony przed podciąganiem kapilarnym wilgoci z gruntu, co jest jednym z najgroźniejszych wrogów każdej konstrukcji budowlanej. Wilgoć w konstrukcji to potencjalne pleśnie, grzyby, osłabienie materiałów, a w zimie – przemarzanie i destrukcja. Tutaj najczęściej stosuje się wytrzymałe folie z polietylenu (PE) o grubości od 0.5 mm do nawet 1.0 mm, układane z zakładami min. 15-20 cm i szczelnie klejone taśmą. Czasem stosuje się specjalistyczne membrany bitumiczne lub z tworzyw sztucznych, np. EPDM. Dobrze wykonana izolacja przeciwwilgociowa jest absolutnym must-have i "oszczędzanie" na niej to proszenie się o kłopoty. Jej prawidłowe ułożenie z wywinięciem na boki pod przyszłą izolację obwodową i płytę to standard. Pamiętajmy o staranności w miejscach newralgicznych, np. wokół przejść instalacyjnych.
Dodatkowym, często pomijanym przez inwestorów, ale bardzo rozsądnym rozwiązaniem, jest system drenażu opaskowego wokół płyty. Choć sama płyta z odpowiednią izolacją hydroizolacyjną stanowi barierę, gromadząca się wokół niej woda opadowa lub gruntowa (zwłaszcza przy wyższym poziomie wód) może z czasem znaleźć słabe punkty. Drenaż, czyli układ perforowanych rur ułożonych w obsypce filtracyjnej (np. żwirowej) i odprowadzających wodę np. do studni chłonnej czy kanalizacji deszczowej, zapewnia stałe obniżenie poziomu wody wokół fundamentu. To proaktywna ochrona, która w mojej ocenie zawsze się opłaca, zwłaszcza na terenach o mniej korzystnych warunkach gruntowych lub przy planowaniu podpiwniczenia (choć przy płycie fundamentowej podpiwniczenie jest rzadkością). Koszt drenażu opaskowego to dodatkowe kilka-kilkanaście złotych na metrze bieżącym obwodu budynku, co jest niewielkim wydatkiem w porównaniu do potencjalnych kosztów napraw związanych z zawilgoceniem.
Prawidłowe przygotowanie gruntu i wykonanie podsypki oraz izolacji przeciwwilgociowej to fundament pod fundament. Choć prace te nie są spektakularne jak układanie betonu czy zbrojenia, ich solidność decyduje o długowieczności całej konstrukcji. Jak mawiał mój stary mistrz budowlany: "Fundament to jak korzenie drzewa. Jak korzenie zdrowe, to drzewo stoi latami. Jak nie, to byle wiatr je przewróci". Miał absolutną rację w swojej prostocie myślenia o konstrukcji.
Na tym etapie można także pokusić się o zainstalowanie systemu ogrzewania podłogowego już w samej płycie fundamentowej, co jest popularnym rozwiązaniem w przypadku "ciepłych płyt". Rury PEX (zwykle fi 16-20 mm), przeznaczone do dystrybucji czynnika grzewczego (ciepłej wody lub mieszaniny wody z glikolem), układa się na warstwie izolacji termicznej lub na siatce zbrojeniowej. Rozstaw rur jest uzależniony od wymaganego zapotrzebowania na ciepło w danym pomieszczeniu, ale typowo wynosi 10-20 cm. Taki układ pozwala na efektywne wykorzystanie akumulacyjnych właściwości betonu, który nagrzany oddaje ciepło do wnętrza budynku. Pamiętajmy o solidnym zamocowaniu rur do zbrojenia, aby uniknąć ich przesunięcia podczas wibrowania betonu – to częsty błąd początkujących ekip.
Położenie rur instalacyjnych (wodno-kanalizacyjnych, elektrycznych, centralnego odkurzacza) w chudziaku lub na izolacji termicznej przed wylaniem właściwej płyty betonowej to również standard na tym etapie. Wymaga to precyzyjnego rozplanowania wszystkich przebiegów instalacyjnych i wykonania odpowiednich peszli ochronnych lub izolacji technicznych dla rur, aby zapobiec ich uszkodzeniu podczas betonowania oraz zapewnić możliwość późniejszej wymiany (choć ta jest trudna). Przy instalacji kanalizacji należy pamiętać o odpowiednich spadkach rur – minimum 2% dla rur o średnicy 110 mm i 3% dla rur o mniejszych średnicach (np. 50-75 mm), aby zapewnić swobodny przepływ ścieków grawitacyjnie. Każdą instalację przed zalaniem betonem należy poddać próbie szczelności, ciśnieniowej lub wodnej, aby uniknąć przykrych niespodzianek po wylaniu płyty.
Podsumowując ten etap: przygotowanie podłoża to seria starannych, sekwencyjnych działań, które muszą być wykonane z należytą precyzją i dbałością o szczegóły. Nie ma tu miejsca na prowizorkę. Od badania gruntu, przez zdjęcie humusu, zagęszczenie podłoża, wykonanie podsypki filtracyjnej, ułożenie izolacji przeciwwilgociowej, po ułożenie instalacji i, jeśli przewidziano, ogrzewania podłogowego – każdy krok ma swoje uzasadnienie i krytyczne znaczenie dla końcowego efektu. To tutaj powstaje faktyczny punkt odniesienia dla całej późniejszej konstrukcji budynku. Myśl o tym jak o artystycznym dziele – płótno musi być idealnie przygotowane, zanim malarz nałoży pierwszą farbę. Tutaj „płótnem” jest nasz starannie przygotowany grunt, a „farbą” kolejne warstwy fundamentu.
Kluczowa Warstwa: Izolacja Termiczna w Płycie Fundamentowej
Mówimy o ciepłej płycie fundamentowej, a co czyni ją "ciepłą"? Odpowiedź jest prosta: jej izolacja termiczna. To nie żart ani gra słów, po prostu fakt techniczny. Ta warstwa, widoczna w przekroju płyty fundamentowej jako wyraźny element o znacznej grubości, stanowi serce całego systemu, jego ciepłochronne pancerz. Jej zadanie jest monumentalne: minimalizowanie ucieczki ciepła z ogrzewanego wnętrza domu do zimnego gruntu pod spodem. To dzięki niej stopa w skarpetce na parterze zimą czuje komfort, a nie chłodny podmuch z podłogi. Ile to ciepła potrafi uciec do ziemi? Wyobraźmy sobie tradycyjny fundament – to jak mieć dziurę w podłodze wcale nie tak małą, energetycznie mówiąc. Izolacja tę dziurę zamyka, i to szczelnie. Efekt jest taki, że zmniejszamy straty ciepła przez podłogę nawet o 15-20%, co realnie przekłada się na niższe rachunki za ogrzewanie przez dziesięciolecia. Czy warto w nią zainwestować? Odpowiadam bez wahania: tak. Czy to drogie? Zobaczmy.
W płytach fundamentowych najczęściej spotykamy polistyren – ale nie byle jaki. Królują tu dwie odmiany: polistyren ekspandowany (EPS), często o podwyższonej wytrzymałości na ściskanie, i polistyren ekstrudowany (XPS). Oba są tworzywami piankowymi, lekkimi, ale w przypadku fundamentu muszą być wyjątkowo odporne na obciążenia i wilgoć. XPS, ten o charakterystycznym, gładkim boku i zazwyczaj intensywnym kolorze (różowym, niebieskim, zielonym), ma lepsze parametry techniczne – niższą nasiąkliwość (zwykle poniżej 1%) i znacznie wyższą wytrzymałość na ściskanie (od 300 kPa do nawet 700 kPa). To właśnie jego używa się częściej pod płytami, choć wysokiej jakości EPS oznaczony literami "Fundament" lub "Parking" (nasiąkliwość poniżej 3%, wytrzymałość min. 100 kPa) również znajduje zastosowanie, zwłaszcza w warstwie wierzchniej, nad tą bardziej wytrzymałą.
Grubość izolacji to kluczowy parametr, który bezpośrednio wpływa na jej efektywność, czyli na współczynnik przenikania ciepła U dla całej przegrody. Obecne przepisy (WT 2021) wymagają dla podłogi na gruncie współczynnika U nie większego niż 0.30 W/(m²K), a w praktyce projektuje się płyty fundamentowe o U znacznie poniżej 0.15 W/(m²K), nierzadko dochodząc do poziomu 0.08-0.10 W/(m²K) w budownictwie pasywnym. Aby to osiągnąć, potrzeba sporej grubości izolacji. Standardem stało się minimum 20 cm, a w przypadku budynków o podwyższonych wymaganiach energetycznych czy pasywnych – nawet 25 cm, 30 cm, a sporadycznie więcej. Tę grubość zazwyczaj układa się w dwóch, a czasem nawet trzech warstwach, stosując tzw. mijankowe łączenie płyt, aby zminimalizować mostki termiczne na spoinach. Myk polega na tym, by spoiny w jednej warstwie nie pokrywały się ze spoinami w warstwie sąsiedniej – prosta zasada, wielki efekt izolacyjny.
Ułożenie izolacji wymaga gładkiej i równej powierzchni poniżej – tu właśnie wchodzi w grę wspomniana wcześniej idealnie wypoziomowana podsypka i warstwa folii hydroizolacyjnej. Płyty termoizolacyjne układa się na styk, ściśle do siebie dociskając, czasem nawet szlifując krawędzie, by połączenia były jak najciaśniejsze. Każda szczelina to potencjalny mostek termiczny. To trochę jak układanie gigantycznych puzzli, gdzie precyzja jest cnotą. W praktyce często stosuje się płyty izolacyjne z frezowanymi krawędziami (np. na pióro-wpust), co dodatkowo ułatwia szczelne połączenie. Typowe wymiary płyt to 125 cm x 60 cm, co przyspiesza prace, ale i tak wymaga cierpliwości i wprawy ekipy. Pamiętajmy, że cena dobrego XPS-u to od 350 do nawet 500 zł za metr sześcienny, więc warstwa o grubości 20 cm to już kilkadziesiąt złotych na metrze kwadratowym samej tylko izolacji materiałowej, bez kosztów robocizny. Lecz jest to inwestycja, która zwraca się przez lata w niższych kosztach ogrzewania.
Ciekawostką jest, że w niektórych systemach budowy ciepłych płyt fundamentowych, część izolacji układa się... na płycie betonowej, tuż pod wylewką jastrychową, gdzie znajduje się ogrzewanie podłogowe. Chodzi o to, by ciepło z ogrzewania podłogowego było kierowane do góry, do pomieszczenia, a nie "uciekało" w głąb płyty i dalej do gruntu. To rozwiązanie rzadsze, ale w pewnych konfiguracjach termicznych może być optymalne. Klasyczny układ to jednak 100% izolacji pod płytą konstrukcyjną. Decyzja o układzie warstw izolacji w przekroju płyty fundamentowej zależy od specyfiki projektu i obliczeń energetycznych.
Polistyren na tym etapie musi być chroniony. Przed czym? Przed promieniami UV, które degradują jego strukturę (biały EPS żółknie i kruszeje), a także przed uszkodzeniami mechanicznymi podczas kolejnych prac – układania zbrojenia, chodzenia po nim czy transportu materiałów. Z tego powodu często stosuje się tymczasową warstwę ochronną, np. chudziak (bardzo cienką wylewkę z chudego betonu B7.5 - B10) lub po prostu wytrzymałą folię budowlaną, rozłożoną bezpośrednio na izolacji termicznej przed przystąpieniem do zbrojenia. Warto o tym pomyśleć, bo uszkodzona izolacja to straty ciepła i pieniędzy. Grubość takiego "chudziaka" na izolacji termicznej to zazwyczaj zaledwie 5-10 cm, ale jej rolą jest tylko ochrona i stworzenie równego podłoża dla zbrojenia.
Podsumowując, warstwa izolacji termicznej jest absolutnie fundamentalna dla koncepcji "ciepłej" płyty. Jej prawidłowy dobór pod względem materiału, grubości i sposobu ułożenia to inwestycja, która procentuje przez cały okres eksploatacji budynku. Nie jest to miejsce na kompromisy czy oszczędności, które szybko okażą się pozorne. To tutaj "szczelność" w rozumieniu cieplnym nabiera realnego znaczenia, tworząc ciepły fundament domu, niczym dobrze ocieplone "stopy" całego budynku. Bez solidnej, odpowiednio grubej i prawidłowo ułożonej izolacji, nawet najlepiej wykonana reszta płyty fundamentowej będzie jedynie solidną konstrukcją, ale nigdy ciepłą. A przecież chcemy, żeby nasz dom był ciepły, prawda? Komfort cieplny to nie luksus, to standard, którego można oczekiwać od nowoczesnego budownictwa, a ciepła płyta fundamentowa jest jednym z jego kluczowych elementów.
Dobór odpowiedniej izolacji to również kwestia jej reakcji na ogień i innych parametrów bezpieczeństwa, choć w przypadku izolacji podziemnej nie są one tak krytyczne jak np. dla elewacji czy dachu. Niemniej, atesty i deklaracje właściwości użytkowych powinny być standardem przy zakupie materiału. Zwracajmy uwagę na współczynnik przewodzenia ciepła Lambda (λ) - im niższy, tym lepsza izolacja. Dobrej jakości XPS ma λ na poziomie 0.033-0.035 W/mK, podczas gdy specjalistyczny EPS Fundament to zazwyczaj λ=0.036-0.038 W/mK. Różnice wydają się niewielkie, ale w kontekście kilkudziesięciu centymetrów grubości mają realne przełożenie na finalny współczynnik U płyty. Nie dajmy się zwieść "promocjom" na materiały o podejrzanie dobrych parametrach - fizyka budowli bywa bezlitosna i nie oszuka się jej metrem mierzącym grubość na budowie, ale laboratoryjnie sprawdzając Lambdę.
Zbrojona Płyta Betanowa – Konstrukcja Właściwa
Gdy warstwy izolacji termicznej i hydroizolacji leżą szczelnie ułożone na przygotowanej podsypce, nadchodzi moment na to, co laicy często utożsamiają z całym fundamentem: wylewanie betonu. To ta masywna warstwa, w której spoczywa stalowe zbrojenie, przejmuje i rozprowadza wszelkie obciążenia z budynku, przenosząc je na niższe warstwy aż do gruntu. Zbrojona płyta betonowa to kręgosłup konstrukcyjny fundamentu. Bez niej, cała misteryjnie ułożona izolacja i przygotowane podłoże byłyby jak elegancki talerz bez tortu.
Materiałem bazowym jest oczywiście beton lub żelbet, czyli beton wzmocniony stalą. Najczęściej stosuje się beton klasy wytrzymałości na ściskanie C25/30, który charakteryzuje się minimalną wytrzymałością 25 MPa w teście walcowym i 30 MPa w teście sześciennym po 28 dniach dojrzewania. Czasami, dla budynków o większych obciążeniach lub w specyficznych warunkach, może być konieczne użycie betonu wyższej klasy, np. C30/37. Ważne, by beton był klasy ekspozycji odpowiedniej dla środowiska gruntowego, np. XF1 dla ochrony przed zamarzaniem. Beton powinien być dostarczony z betoniarni jako mieszanka gotowa (tzw. "towarowy") z certyfikatem zgodności, co daje pewność jego parametrów. Mieszanie betonu "na budowie" przy tak ważnej konstrukcji to praktyka absolutnie niezalecana i ryzykowna.
Sercem zbrojonej płyty jest stalowe zbrojenie. To ono przejmuje siły rozciągające, na które beton jest słabo odporny, a które występują w konstrukcji płyty pod wpływem obciążeń. Projektant konstrukcyjny określa średnice i rozstaw prętów, tworząc siatkę zbrojeniową dostosowaną do konkretnego projektu budynku i obciążeń. Najczęściej stosuje się stal żebrowaną klasy B500SP (popularnie nazywana stalą fi). Standardowe zbrojenie płyty fundamentowej składa się zazwyczaj z dwóch siatek: dolnej i górnej, ułożonych w pewnej odległości od siebie (określonej przez tzw. strzemiona lub specjalne dystanse). Dolna siatka przyjmuje obciążenia pozytywne (gięcie w dół), a górna negatywne (gięcie w górę, np. na krawędziach lub pod ścianami). Typowy rozstaw prętów wynosi 15-20 cm w obu kierunkach, a średnice to fi 10, fi 12 lub fi 14 mm, w zależności od obciążeń i grubości płyty. Im większe obciążenia, tym gęstsza i grubsza siatka. Ilość stali na metr sześcienny betonu w płycie fundamentowej waha się zwykle od 50 do 100 kg. Na przykład, płyta 15 cm o standardowym zbrojeniu dwoma siatkami fi 12 co 15 cm wymaga około 70 kg stali na m³ betonu. Ta stal musi być solidnie połączona (drutem wiązałkowym) w miejscach krzyżowania się prętów i ułożona na odpowiedniej wysokości od dolnej i górnej powierzchni płyty (otulina betonowa minimum 2-3 cm) za pomocą plastikowych lub betonowych dystansów.
Grubość samej płyty betonowej zależy od wielkości i konstrukcji budynku, a także od warunków gruntowych i obciążeń. Standardowo wynosi od 15 cm (dla mniejszych budynków jednorodzinnych, w dobrych warunkach gruntowych) do 20-25 cm (dla większych domów, piętrowych, czy na słabszych gruntach). Grubość płyty jest wynikiem precyzyjnych obliczeń statycznych wykonywanych przez projektanta konstrukcji. Należy bezwzględnie przestrzegać grubości i sposobu zbrojenia wskazanych w projekcie. Zmniejszenie grubości o kilka centymetrów "na oko" lub zastosowanie cieńszych prętów zbrojeniowych to prosty sposób na późniejsze pęknięcia lub ugięcia płyty. Jak to mówią na budowie, "projekt to świętość, a stal to mięśnie betonu".
Wylewanie betonu to kluczowy, a zarazem najbardziej dynamiczny moment. Mieszanka betonowa dostarczana jest zwykle gruszkami betoniarkami i pompowana bezpośrednio w deskowanie. Beton musi być rozłożony równomiernie na całej powierzchni i, co najważniejsze, starannie zagęszczony za pomocą wibratorów pogrążalnych (tzw. buław), co pozwala usunąć pęcherzyki powietrza i zapewnić szczelność oraz jednorodność struktury betonu. Nieodpowiednie wibrowanie to jedna z głównych przyczyn słabszej wytrzymałości betonu i powstawania tzw. raków betonowych (ubytków materiału). Należy pamiętać o równomiernym i ciągłym betonowaniu całej płyty – niedopuszczalne są przerwy technologiczne bez odpowiedniego zaplanowania i wykonania styków roboczych, które w przypadku płyt fundamentowych są raczej unikane. Idealnie, płyta powinna być betonowana w jednym cyklu.
Po wylaniu i wyrównaniu powierzchni betonu (np. za pomocą listwy wibracyjnej lub ręcznie), następuje proces pielęgnacji betonu. Jest to równie ważne jak samo wylewanie. Świeży beton nie może zbyt szybko wyschnąć, ponieważ może to prowadzić do skurczu, pęknięć i obniżenia jego wytrzymałości. Pielęgnacja polega na utrzymaniu betonu w stanie wilgotnym przez co najmniej 7 dni, a najlepiej dłużej. Można to robić poprzez polewanie powierzchni wodą (zwłaszcza w upalne dni), przykrywanie matami nasiąkliwymi i stałe ich nawilżanie, stosowanie specjalistycznych preparatów do pielęgnacji betonu (np. emulsji tworzących powłokę zapobiegającą odparowywaniu wody) lub przykrywanie folią budowlaną. Zaniedbanie pielęgnacji to jak zostawienie noworodka bez opieki – może przeżyć, ale na pewno nie rozwinie się w pełni sił. Prawidłowa pielęgnacja gwarantuje osiągnięcie przez beton projektowanej wytrzymałości. Odporność betonu na ściskanie bada się po 28 dniach dojrzewania, na podstawie próbek pobranych podczas betonowania i przechowywanych w kontrolowanych warunkach.
W skład samej płyty betonowej mogą wchodzić dodatkowe elementy, np. wspomniane wcześniej rury ogrzewania podłogowego (tzw. jastrych zespolony lub "płyta grzewcza" jako część konstrukcyjna fundamentu), czy punkty wyprowadzenia instalacji pionowych. Planowanie tych elementów i ich precyzyjne umiejscowienie jest kluczowe przed betonowaniem. Należy pamiętać o odpowiednich zakończeniach rur osłonowych dla przejść instalacyjnych przez płytę, zabezpieczających przewody i pozwalających na ich dylatację względem betonu. Często stosuje się również wkładki styropianowe lub z wełny mineralnej wokół przejść kominowych lub w miejscach, gdzie będą stawać ciężkie punkty obciążeń (np. słupy konstrukcyjne), co ma zapobiec spękaniom w tych rejonach. To takie drobne detale, które jednak mają ogromny wpływ na końcową jakość i bezproblemową eksploatację.
Grubość zbrojenia, klasy betonu, sposób jego wylewania i pielęgnacji – wszystkie te elementy muszą być ściśle zgodne z projektem. Odstępstwa bez zgody projektanta są niedopuszczalne i mogą prowadzić do poważnych problemów konstrukcyjnych w przyszłości. Pamiętajmy, że naprawa płyty fundamentowej jest niezwykle trudna i kosztowna. Warto inwestować w dobrą ekipę z doświadczeniem w wykonywaniu ciepłych płyt fundamentowych. Betonowanie płyty to często spektakl precyzji i tempa, gdzie czas odgrywa kluczową rolę, bo beton po prostu czekać nie lubi. Od zamówienia, przez dostawę, po wylanie i pierwsze etapy pielęgnacji, wszystko musi być zgrane niczym w orkiestrze pod batutą doświadczonego majstra.
W przypadku budynków energooszczędnych lub pasywnych, grubość izolacji termicznej i betonowej płyty są ze sobą ściśle powiązane poprzez obliczenia mostków termicznych na krawędziach i wymagany współczynnik U. Im lepsza izolacja, tym "cieplejsza" płyta, co bezpośrednio przekłada się na niższe zapotrzebowanie na energię. Pamiętajmy, że warstwy w płycie fundamentowej tworzą synergiczny system – każdy element wspiera pozostałe w osiągnięciu końcowego celu. Dobrze wykonana płyta betonowa to gwarancja, że dom nie tylko będzie stał stabilnie, ale także będzie efektywnie zarządzał energią, dostarczając komfortu przez lata. To nie tylko podstawa w sensie fizycznym, ale i ekonomicznym – oszczędność na ogrzewaniu zaczyna się już na tym etapie.
Betonowanie płyty wymaga również odpowiedniego deskowania. Często stosuje się szalunki systemowe, ale równie dobrze sprawdza się deskowanie z impregnowanych desek lub płyt OSB/sklejki, podparte i wzmocnione tak, aby utrzymać ciężar płynnego betonu bez odkształceń. Zabezpieczenie deskowania przed "ucieczką" mleczka cementowego, np. poprzez zastosowanie folii kubełkowej czy taśm uszczelniających, jest istotne dla uzyskania gładkich krawędzi i uniknięcia strat spoiwa. Pamiętajmy, że każdy litr "ucieczkowego" mleczka cementowego to osłabienie betonu na krawędzi. Takie szczegóły odróżniają fachową robotę od partactwa. Demontaż deskowania następuje zazwyczaj po osiągnięciu przez beton minimalnej wytrzymałości, co w przypadku betonu C25/30 i typowych warunków temperaturowych (powyżej +5°C) trwa zwykle 2-3 dni. W niższych temperaturach proces ten wydłuża się.
Podczas wylewania i zacierania powierzchni betonu, niezwykle ważne jest również precyzyjne ustalenie poziomów. Płyta fundamentowa często pełni od razu rolę podłogi parteru, więc jej górna powierzchnia musi być idealnie równa i wypoziomowana. W przypadku płyt z wbudowanym ogrzewaniem podłogowym, wykończenie powierzchni często ogranicza się do zatarcua jej "na ostro", gdyż gładka wylewka cementowa (jastrych) będzie wykonana później. Jeśli płyta ma stanowić docelowe podłoże pod np. płytki ceramiczne, wymaga idealnego zatarcia na gładko (np. mechanicznie za pomocą zacieraczki). Różnica w poziomach na całej powierzchni płyty nie powinna przekraczać kilku milimetrów, np. +/- 5 mm na całej powierzchni, choć dla poszczególnych pomieszczeń czy mniejszych odcinków tolerancje są jeszcze bardziej restrykcyjne.
Aspektem, o którym często zapomina się podczas ekscytacji betonowaniem, są przerwy dylatacyjne. W większych płytach lub tam, gdzie występują zmiany w obciążeniach czy geometryczne, konieczne może być wykonanie przerw dylatacyjnych, które zapobiegną powstawaniu rys skurczowych betonu. Przerwy te mogą być konstrukcyjne, sięgające pełnej grubości płyty i wypełniane specjalistycznymi materiałami, lub powierzchniowe, nacinane w świeżym betonie. Ich rozmieszczenie i wykonanie zawsze muszą wynikać z projektu konstrukcyjnego. Pominięcie dylatacji może doprowadzić do niekontrolowanych spękań betonu, co jest koszmar każdego inwestora. Dobry projektant i doświadczona ekipa zadbają o te szczegóły. To właśnie te pozornie nieważne szczegóły decydują o jakości i trwałości konstrukcji na lata.
Podsumowując część o zbrojonej płycie betonowej – to solidna, masywna warstwa, która wymaga precyzyjnego wykonania od początku do końca. Od doboru odpowiedniej klasy betonu i stali, przez precyzyjne ułożenie zbrojenia, właściwe betonowanie i zagęszczanie, po kluczową pielęgnację i wykonanie dylatacji. To wszystko składa się na konstrukcję, która przeniesie obciążenia z budynku i zapewni mu stabilność na dziesięciolecia. Nie ma tu miejsca na "chałupnictwo" – to inżynieria w praktyce, gdzie każdy błąd może drogo kosztować w przyszłości. Warto pamiętać, że w przeciwieństwie do tradycyjnych ław i ścian fundamentowych, płyta fundamentowa jest monolityczna i jej ewentualne naprawy są ekstremalnie trudne, a często wręcz niemożliwe bez ingerencji w całą konstrukcję. Dlatego tak ważne jest jej prawidłowe wykonanie za pierwszym razem.
Izolacja Obwodowa i Detale na Krawędzi Płyty Fundamentowej
Skoro mamy już przygotowany grunt, ułożoną podsypkę, szczelną hydroizolację i potężną, zbrojoną płytę betonową opatuloną od dołu solidną warstwą izolacji termicznej, mogłoby się wydawać, że praca przy fundamencie dobiegła końca. Nic bardziej mylnego! Ciepła płyta fundamentowa charakteryzuje się jeszcze jednym, absolutnie kluczowym elementem, który wieńczy dzieło termoizolacji – izolacją obwodową. To nic innego jak "kołnierz" otulający pionowe krawędzie płyty i stanowiący jej naturalne przedłużenie termiczne powyżej poziomu terenu. Jeśli izolacja pod płytą jest termicznym "spodem", to izolacja obwodowa jest "bokiem", który nie pozwala zimnu wedrzeć się od strony gruntu przylegającego do zewnętrznej krawędzi płyty.
Dlaczego jest to tak ważne? Krawędź płyty betonowej, tam gdzie styka się bezpośrednio z gruntem lub cokołem budynku, to potencjalne pole minowe dla mostków termicznych. Beton sam w sobie jest materiałem o znacznie gorszych właściwościach izolacyjnych niż np. polistyren. Bez odpowiedniego otulenia, zimno z gruntu bocznego "wdzierałoby się" do płyty betonowej, tworząc na jej obwodzie strefę niższą temperaturę, co mogłoby prowadzić do strat ciepła i, w skrajnych przypadkach, kondensacji pary wodnej wewnątrz przegrody. Izolacja obwodowa rozwiązuje ten problem, tworząc ciągłą, szczelną otulinę termiczną na całej wysokości bocznej krawędzi płyty. W efekcie, krawędź płyty ma temperaturę zbliżoną do temperatury wnętrza budynku, a mostek termiczny jest zredukowany do minimum. Jest to szczególnie istotne w przypadku budynków energooszczędnych i pasywnych, gdzie minimalizacja mostków termicznych jest priorytetem. W projekcie każdej ciepłej płyty fundamentowej izolacja obwodowa zajmuje należne jej miejsce.
Materiałem stosowanym do izolacji obwodowej jest niemal wyłącznie polistyren ekstrudowany (XPS). Dlaczego akurat on? Z prostej przyczyny: musi pracować w trudnym środowisku. Jest stale lub okresowo narażony na kontakt z wilgocią gruntową, a nawet wodą. XPS, dzięki swojej zamkniętokomórkowej strukturze, charakteryzuje się wyjątkowo niską nasiąkliwością – zwykle poniżej 1%, a nawet 0.5%. W przeciwieństwie do EPS, który nasiąkając, traci swoje właściwości izolacyjne i jest podatny na cykle zamarzania-rozmarzania w obecności wody, XPS zachowuje swoje parametry termiczne i mechaniczne w warunkach zawilgocenia. Jest również znacznie bardziej wytrzymały mechanicznie i odporny na ściskanie, co ma znaczenie, gdy grunt osiada lub przylega bezpośrednio do izolacji. Właśnie ta wodoodporność czyni go niezastąpionym w tej roli.
Grubość izolacji obwodowej jest zazwyczaj taka sama jak grubość izolacji pod płytą, lub niewiele mniejsza, tak aby stworzyć jednolitą otulinę termiczną. Spotkamy więc grubości od 10 do 20 cm, a w budownictwie pasywnym nawet do 25-30 cm. Płyty XPS do izolacji obwodowej często mają frezowane krawędzie (pióro-wpust) ułatwiające szczelne połączenie i układa się je pionowo lub poziomo wzdłuż obwodu płyty fundamentowej, na zewnątrz jej krawędzi. Wysokość, na jaką powinna sięgać izolacja obwodowa, zależy od poziomu posadowienia budynku i docelowego poziomu terenu. Zazwyczaj izolacja ta sięga od spodu płyty aż powyżej poziomu terenu, często o kilka-kilkanaście centymetrów, tworząc termoizolacyjny cokół budynku. Ważne, by stykała się szczelnie z izolacją ułożoną pod płytą, tworząc ciągłą barierę.
Detale na krawędzi płyty to cała lista drobnych, ale krytycznych punktów, które wymagają uwagi. Wszelkie przejścia instalacyjne przez pionową krawędź płyty (np. rury kanalizacyjne wyprowadzone na zewnątrz, przyłącza wody, energii elektrycznej) muszą być starannie zaizolowane. Wokół takich przejść tworzą się naturalne mostki termiczne. Należy stosować specjalne "ciepłe przejścia", czyli kołnierze uszczelniająco-izolacyjne, które szczelnie otulają rurę przechodzącą przez izolację obwodową i płytę, wypełniając ewentualne szczeliny pianą lub masami uszczelniającymi. Pamiętajmy o prawidłowym wykonaniu tych punktów, gdyż nieszczelności termiczne i hydroizolacyjne w tych miejscach to proszenie się o kłopoty.
Poziom izolacji obwodowej powyżej terenu wymaga odpowiedniego zabezpieczenia przed uszkodzeniami mechanicznymi (np. podczas koszenia trawy) oraz przed działaniem promieni UV. Stosuje się w tym celu tynk cokołowy wzmocniony siatką zbrojącą, specjalne panele elewacyjne cokołowe, płytki klinkierowe czy inne materiały wykończeniowe. Ważne, aby te materiały były mrozoodporne i nienasiąkliwe. Warstwa zbrojonej zaprawy klejowej z zatopioną siatką elewacyjną nałożona na XPS cokołowy, a następnie tynk cienkowarstwowy to najpopularniejsze i wystarczające zabezpieczenie. Warto jednak pamiętać o dylatacji pomiędzy izolacją obwodową (cokołem) a fasadą budynku, aby uniknąć pęknięć wynikających z ruchów materiałów i obciążeń. Standardowo wykonuje się poziomą dylatację o grubości kilku milimetrów (np. 5-10 mm), wypełnioną elastycznym materiałem (np. pianką poliuretanową) i zabezpieczoną listwą dylatacyjną.
Innym ważnym detalem jest sposób połączenia izolacji obwodowej z izolacją pionową ścian zewnętrznych, jeśli te są projektowane jako murowane. Idealnie, izolacja ścian powinna nachodzić na izolację cokołową, tworząc ciągłą otulinę bez przerw. W przypadku izolacji obwodowej powyżej poziomu gruntu, styropian cokołowy powinien być wykonany z twardego XPS-u o gładkiej powierzchni, odpornego na uszkodzenia, sięgającego np. 30-50 cm ponad teren. Całość powinna być oczywiście przykryta materiałem wykończeniowym. Czasem stosuje się tzw. "fartuch" z membrany kubełkowej (folii hydroizolacyjnej tłoczonej) na zewnętrznej powierzchni izolacji obwodowej pod poziomem gruntu. Ta dodatkowa warstwa chroni XPS przed bezpośrednim kontaktem z wilgotnym gruntem i potencjalnymi uszkodzeniami podczas zasypywania wykopu.
Poprawne wykonanie detali na krawędzi płyty i zapewnienie ciągłości izolacji obwodowej jest równie, a nawet bardziej, ważne dla końcowej efektywności energetycznej, co grubość izolacji pod płytą. Dlaczego? Bo mostki termiczne na krawędziach potrafią "przeskoczyć" nawet solidną izolację na powierzchni. Ich wpływ na całkowite straty ciepła jest często niedoceniany. To jak mieć świetny sweter, ale dziurawe rękawy. Stracimy ciepło przez rękawy. Detale na krawędzi płyty fundamentowej to właśnie te "rękawy". Należy zwrócić na nie szczególną uwagę na etapie projektu i wykonania, a ekipa budowlana powinna być świadoma ich znaczenia i mieć doświadczenie w prawidłowym wykonywaniu takich połączeń. Często na projektach budowlanych pojawiają się szczegółowe rysunki pokazujące sposób rozwiązania izolacji obwodowej i detali w kluczowych punktach, np. na narożach budynku, wokół przyłączy, czy pod drzwiami tarasowymi.
Koszt izolacji obwodowej z materiałem i robocizną to zazwyczaj dodatkowe kilkadziesiąt złotych na metr bieżący obwodu budynku. Wydaje się to niewiele w skali całej inwestycji, ale jej pominięcie lub niewłaściwe wykonanie to gwarancja problemów z mostkami termicznymi i potencjalnego przemarzania krawędzi płyty w przyszłości. Pamiętajmy też o starannym zasypaniu wykopu wokół fundamentu. Powinien być on zasypany materiałem przepuszczalnym, np. pospółką czy piaskiem, co ułatwi odprowadzenie wody od krawędzi płyty i nie spowoduje nadmiernego obciążenia izolacji obwodowej gruntem spoistym. Grunt ten należy zagęścić warstwami, aby uniknąć późniejszego osiadania wokół budynku, co mogłoby prowadzić do uszkodzenia cokołu czy chodników. Niewłaściwe zasypanie wykopu wokół płyty fundamentowej to kolejny przykład pozornie mało znaczącego etapu, który może przynieść długofalowe problemy.
W przypadku budynków z ogrzewaniem podłogowym wbudowanym w płytę fundamentową, izolacja obwodowa odgrywa podwójnie ważną rolę. Pomaga zatrzymać ciepło nie tylko w budynku, ale i w samej płycie, zwiększając jej efektywność jako akumulatora ciepła i elementu grzewczego. Brak solidnej izolacji obwodowej w takim przypadku prowadzi do znaczących strat ciepła "w bok", do gruntu przylegającego, co obniża temperaturę krawędzi płyty i zwiększa koszty ogrzewania. Warto zatem, mówiąc o ciepłej płycie fundamentowej przekrój, zawsze podkreślać, że izolacja nie kończy się pod spodem – ona "zawija się" i chroni płytę również z boków. Bez tego "ciepłego kołnierza" inwestycja w grubą izolację pod płytą jest jak kupowanie zimowego płaszcza bez rękawów – niby coś daje, ale daleko mu do pełnej funkcjonalności. Solidna izolacja obwodowa to świadectwo dbałości o szczegóły i zrozumienia zasad fizyki budowli, która finalnie przekłada się na komfort i niższe koszty eksploatacji dla mieszkańców.
Detale dotyczące samej formy krawędzi płyty mogą być różne, np. prosta pionowa ściana betonowa z doklejoną izolacją, lub krawędź z ukośnym ścięciem, co ułatwia odprowadzanie wody od cokołu. Czasem w krawędzi płyty wykonuje się specjalne gniazda pod montaż elementów konstrukcyjnych ścian. Każdy z tych detali wymaga precyzyjnego deskowania i wibrowania betonu, aby uniknąć pustek i zapewnić pełne wypełnienie formy. Nadzór budowlany powinien szczególną uwagę zwrócić na prawidłowość wykonania krawędzi, wibrowanie betonu w tym miejscu i staranne ułożenie izolacji obwodowej na styku z płytą i poniżej terenu. Należy też pamiętać o konieczności odpowiedniego wzmocnienia zbrojenia w krawędzi płyty, np. przez zagęszczenie strzemion lub dodatkowe pręty, co wynika z analizy naprężeń w tej strefie, szczególnie narażonej na obciążenia krawędziowe i koncentrację naprężeń. Bez tych wzmocnień krawędź płyty może ulec wykruszeniu lub pęknięciu.
Drenaż opaskowy, jeśli został wykonany na etapie przygotowania gruntu, powinien znajdować się poniżej poziomu izolacji obwodowej (na poziomie spodu podsypki lub nieco niżej). Woda, która mogłaby dostać się w rejon krawędzi płyty, przesiąka przez materiał zasypki (np. żwir) i trafia do rur drenażowych, skąd jest odprowadzana. Taki system "odwadniający" dodatkowo zabezpiecza izolację obwodową przed stałym przebywaniem w wodzie. To jest synergię działania różnych warstw i elementów konstrukcji: podsypka filtracyjna, izolacja przeciwwilgociowa (wywinięta w górę na krawędzi), izolacja termiczna obwodowa z XPS, a w razie potrzeby – drenaż opaskowy. Całość tworzy system chroniący płytę przed wilgocią i zimnem z gruntu. Ostatnim akcentem jest listwa startowa lub okapnik montowany w dolnej części fasady ponad cokołem, który ma za zadanie odprowadzać wodę spływającą po elewacji i zapobiegać jej zaciekaniu na cokół. Niby drobiazg, a ma wpływ na estetykę i trwałość wykończenia. Podsumowując, krawędź ciepłej płyty to nie tylko prosta linia zakończenia betonu, ale skomplikowany system warstw i detali, wymagający staranności i wiedzy wykonawczej.