Hydroizolacja Pozioma Płyty Fundamentowej 2025
Każdy, kto kiedykolwiek zmagał się z uporczywą wilgocią w budynku, wie, że woda potrafi być bezwzględnym przeciwnikiem. Zaczyna się niewinnie – od lekkiego zawilgocenia, a kończy na zagrzybionych ścianach i kosztownych naprawach. Dlatego tak krytyczne znaczenie ma właściwie wykonana hydroizolacja pozioma płyty fundamentowej. Jej podstawowym celem jest stworzenie bariery, która skutecznie blokuje podciąganie wilgoci z gruntu do struktury budynku przez fundament.
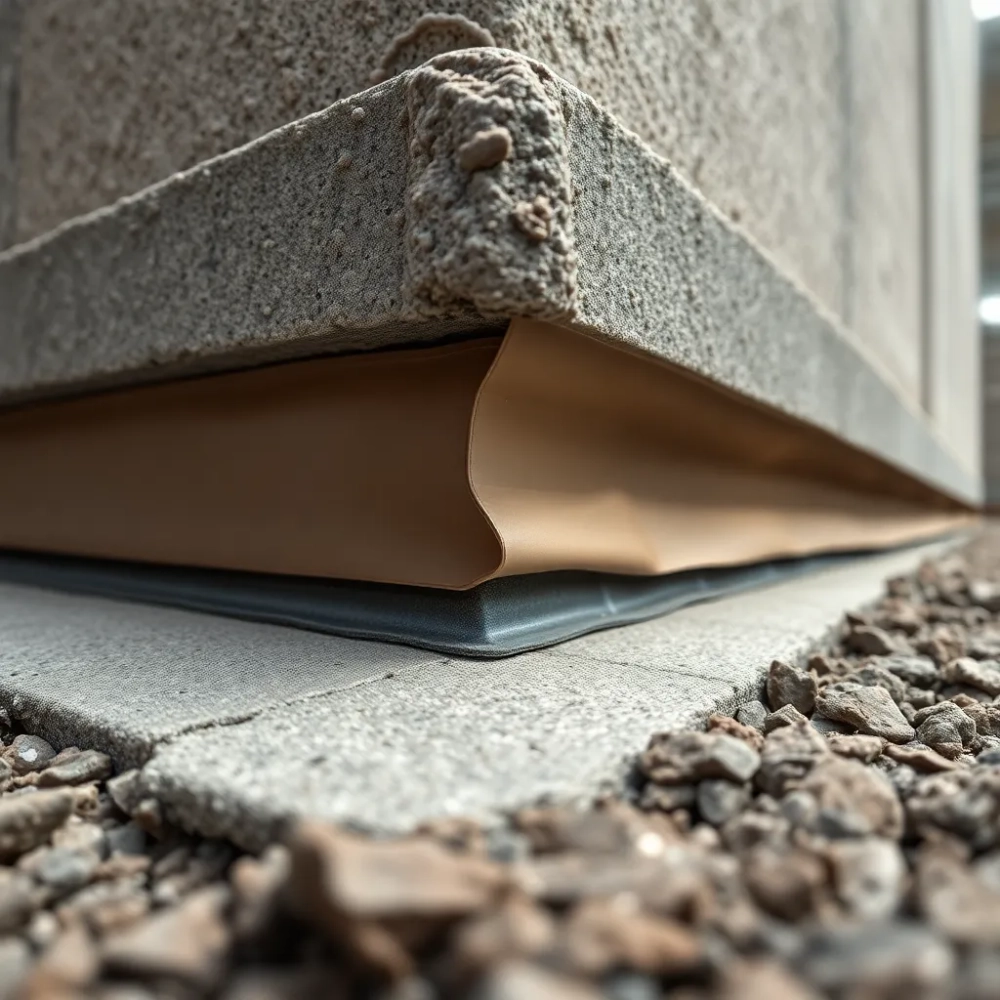
Patrząc analitycznie na różnorodność podejść do zabezpieczenia przed wilgocią pod płytą, można zauważyć pewne zależności między wyborem materiału a kluczowymi parametrami wykonania. Zestawienie pokazuje typowe charakteryki popularnych metod. Każda metoda, od mas bitumicznych po nowoczesne membrany, oferuje inny profil odporności, czasu aplikacji i optymalnych warunków środowiskowych.
Typ materiału | Podstawowa funkcja bariery | Typowa grubość warstwy | Orientacyjny czas schnięcia/wiązania (jednej warstwy) | Zalecana temperatura aplikacji | Orientacyjna żywotność bariery |
---|---|---|---|---|---|
Masy bitumiczne (KMB) | Bariera + uszczelnienie rys | 2-5 mm (sucha warstwa) | 24-72h | +5°C do +25°C | >25 lat |
Pap termozgrzewalna modyfikowana SBS | Bariera | 3-5 mm | natychmiast po zgrzaniu | powyżej +5°C | >30 lat |
Membrany FPO/PVC (syntetyczne) | Bariera + elastyczność | 1.2-2.0 mm | natychmiast po zgrzaniu szwów | +5°C do +35°C (zgrzewanie >20°C) | >40 lat |
Szlamy cementowe (uszlachetnione polimerami) | Bariera + oddychalność | 2-4 mm (sucha warstwa) | 24-48h (ruch pieszy) | +5°C do +30°C | >20 lat |
Analizując te dane, widzimy, że wybór technologii hydroizolacji poziomej płyty fundamentowej nie jest arbitralny, ale wynika ze specyfiki projektu i warunków panujących na budowie. Grubość warstwy, czas schnięcia, a co za tym idzie szybkość postępu prac, oraz wymagania temperaturowe to czynniki, które bezpośrednio wpływają na harmonogram i budżet inwestycji. Trwałość bariery to z kolei parametr kluczowy z punktu widzenia długoterminowego bezpieczeństwa i kosztów eksploatacji budynku, a różnice rzędu kilkunastu lat w przewidywanej żywotności mogą znacząco wpłynąć na całościową ocenę opłacalności.
Dlaczego hydroizolacja pozioma płyty fundamentowej jest niezbędna?
Wyobraźmy sobie dom jako organizm, którego fundament stanowi kręgosłup i stopy. Jeśli stopy stoją w kałuży, cały organizm prędzej czy później zacznie cierpieć. W budownictwie tą "kałużą" jest wilgoć gruntowa, a płyta fundamentowa, będąc bezpośrednio na niej oparta, jest narażona na jej podciąganie.
Nasiąkliwość betonu, mimo jego pozornej twardości, nie zerowa. Woda potrafi wnikać w mikropory i kapilary materiału, pokonując siły grawitacji w procesie podciągania kapilarnego. Może to sięgać nawet kilku metrów w górę, przenosząc wilgoć z gruntu do samej płyty, a następnie do wyższych partii konstrukcji i przegród pionowych, takich jak ściany.
Konsekwencje takiego stanu rzeczy są katastrofalne i wielopłaszczyznowe. Po pierwsze, wilgoć stanowi idealne środowisko do rozwoju pleśni i grzybów, które nie tylko niszczą materiały budowlane (np. wyprawę tynkarską, okładziny podłogowe), ale przede wszystkim negatywnie wpływają na jakość powietrza wewnętrznego. Lotne związki organiczne (LZO) i zarodniki uwalniane przez pleśń mogą powodować problemy zdrowotne, od alergii i astmy po poważniejsze schorzenia układu oddechowego. To nie jest komfortowe życie, delikatnie mówiąc; to powolne zatruwanie środowiska życia.
Ponadto, stała obecność wilgoci w betonie fundamentowym i ścianach prowadzi do degradacji materiałów. W okresach zimowych woda zamarzająca w porach rozszerza się, wywierając ciśnienie, które stopniowo kruszy strukturę betonu i spoin murarskich – to zjawisko tzw. destrukcji mrozowej. Osłabia to nośność elementów konstrukcyjnych, a w skrajnych przypadkach może prowadzić do pęknięć i konieczności kosztownych napraw strukturalnych.
Wilgoć przenosi również rozpuszczone w wodzie sole mineralne z gruntu, które krystalizując na powierzchniach, tworzą nieestetyczne wykwity solne (białe naloty). Choć często postrzegane jedynie jako problem wizualny, ich krystalizacja w porach materiału również powoduje naprężenia i jego niszczenie. Wykwity na styku posadzki z płytą i dolnych partii ścian mogą świadczyć o braku lub nieskuteczności poziomej izolacji płyty fundamentowej.
Wilgotne przegrody gorzej izolują termicznie. Współczynnik przewodzenia ciepła wilgotnych materiałów jest znacząco wyższy niż suchych. To oznacza, że fundament nasiąknięty wodą będzie stanowił mostek termiczny, przez który uciekać będzie ciepło z budynku zimą, a latem do wnętrza dostawać się będzie upał. Prowadzi to do zwiększenia zużycia energii na ogrzewanie i chłodzenie, co bezpośrednio przekłada się na wyższe rachunki. Szacuje się, że niekontrolowane podciąganie kapilarne może zwiększyć straty ciepła przez podłogę na gruncie nawet o 15-20% w stosunku do odpowiednio izolowanej konstrukcji. Energia uciekająca w grunt przez mokry fundament to dosłownie wyrzucanie pieniędzy w błoto.
Problemy z wilgocią wynikające z braku lub wady izolacji poziomej pod płytą fundamentową manifestują się również poprzez niszczenie wykończeń wewnętrznych. Panele podłogowe, drewniane deski czy parkiet mogą puchnąć, wypaczać się, pleśnieć i gnić. Płytki ceramiczne mogą odpadać, a klej i fuga mogą się kruszyć pod wpływem wilgoci i soli. Tynki i farby będą łuszczyć się, pękać i zmieniać kolor.
Koszt naprawy skutków zawilgocenia spowodowanego brakiem hydroizolacji poziomej płyty fundamentowej jest zazwyczaj wielokrotnie wyższy niż koszt jej wykonania na etapie budowy. Naprawa wymaga często odkopywania fundamentów, osuszania konstrukcji, wymiany uszkodzonych materiałów wykończeniowych i sanacji murów – to prace inwazyjne, czasochłonne i generujące znaczne wydatki. Studium przypadku z niewielkiego domu jednorodzinnego pokazało, że koszt osuszenia fundamentów, naprawy murów i wymiany posadzek w kilku pomieszczeniach wyniósł ponad 60 tys. zł, podczas gdy pierwotny koszt materiałów na hydroizolację płyty szacowano na około 4-5 tys. zł. Różnica powala na kolana i dobitnie pokazuje, że oszczędność w tym miejscu to "groszowa" oszczędność, która prowadzi do ogromnych problemów i kosztów w przyszłości.
Solidna hydroizolacja pozioma płyty fundamentowej to nie tylko kwestia komfortu, ale przede wszystkim trwałości, bezpieczeństwa i zdrowia mieszkańców. Jest to inwestycja, która chroni cały budynek przed jednym z najgroźniejszych wrogów – wodą. Jej obecność jest milczącym strażnikiem, który bezszelestnie odpiera ataki wilgoci z gruntu przez dziesięciolecia. Niewykonanie jej lub wykonanie jej wadliwie to jak pozostawienie otwartej furtki dla problemów, które narastają powoli, ale nieuchronnie. Pamiętajmy, że solidne wykonanie hydroizolacji pod płytą to podstawa, o której nie można zapomnieć.
Przygotowanie podłoża pod hydroizolację poziomą płyty fundamentowej
Zanim położymy choćby centymetr membrany czy milimetr masy bitumicznej, musimy upewnić się, że powierzchnia, na którą będziemy aplikować materiał izolacyjny, jest idealnie przygotowana. To jak malowanie – najlepsza farba nie pokryje dobrze brudnej i tłustej ściany. W przypadku hydroizolacji stawka jest znacznie wyższa niż tylko estetyka; mówimy o szczelności kluczowej bariery ochronnej.
Pierwszym krokiem jest upewnienie się, że beton płyty fundamentowej osiągnął odpowiedni stopień wytrzymałości i wilgotności. Proces hydratacji cementu, czyli dojrzewania betonu, trwa tygodniami, a nawet miesiącami. Minimalny czas potrzebny przed aplikacją wielu systemów izolacyjnych to zazwyczaj 7 do 28 dni od wylania, w zależności od typu betonu, warunków dojrzewania i zaleceń producenta hydroizolacji. Pośpiech tutaj jest absolutnie niewskazany, bo beton musi mieć szansę "oddać" część wilgoci technologicznej, która pozostała w nim po wymieszaniu. Nadmierna wilgoć w podłożu może uniemożliwić prawidłowe związanie lub adhezję niektórych materiałów izolacyjnych, powodując pęcherze, odspojenia lub spadek skuteczności.
Powierzchnia płyty fundamentowej musi być czysta. To wydaje się oczywiste, ale "czysta" w kontekście przygotowania pod hydroizolację oznacza coś więcej niż tylko pozbawioną dużych śmieci. Musi być wolna od kurzu, piasku, luźnych elementów betonu, olejów, smarów, resztek deskowania, farb czy jakichkolwiek innych substancji, które mogłyby zaburzyć przyczepność materiału hydroizolacyjnego. Proste zmiatanie miotłą zazwyczaj nie wystarczy. Często konieczne jest odkurzanie przemysłowymi odkurzaczami wyposażonymi w filtry HEPA, a w przypadku uporczywych zabrudzeń (np. oleju) – czyszczenie mechaniczne poprzez szlifowanie, frezowanie lub nawet śrutowanie powierzchni. Brzmi to drastycznie, ale usunięcie cienkiej warstwy "zanieczyszczonego" betonu powierzchniowego jest niezbędne do odsłonięcia czystego, nośnego podłoża, które zapewni solidne związanie izolacji.
Następna kwestia to równość i gładkość powierzchni. Duże nierówności, wystające kruszywa czy zagłębienia mogą stanowić punkty naprężeń w nałożonej warstwie hydroizolacji lub stworzyć miejsca, gdzie woda mogłaby potencjalnie przenikać. Powierzchnia powinna być na tyle równa, by materiał izolacyjny mógł być aplikowany w wymaganej, jednolitej grubości. Ostre krawędzie, zwłaszcza na połączeniach ściana-płyta czy wokół przejść rurowych, muszą być sfazowane lub zaokrąglone (wykonuje się tzw. fasetę lub zaokrąglenie o promieniu min. 4-5 cm), aby zapobiec mechanicznemu uszkodzeniu membrany czy ułatwić ciągłość nakładania powłoki płynnej lub szlamu. Betonowe "szpice" to cisi zabójcy hydroizolacji – potrafią przebić nawet grubą warstwę materiału pod niewielkim naprężeniem.
Wszelkie pęknięcia, raki (ubytki betonu), ubytki po drutach wiązałkowych czy inne defekty w płycie fundamentowej muszą zostać naprawione i wypełnione odpowiednimi, zazwyczaj szybkowiążącymi i hydroizolacyjnymi zaprawami lub szpachlówkami. Typowe wypełnienia ubytków powinny charakteryzować się dobrą przyczepnością do istniejącego betonu i odpornością na wilgoć. Głębokie raki mogą wymagać iniekcji żywicami. Ważne jest, aby powierzchnia po naprawie była zlicowana z resztą płyty.
Ostatnim, ale często kluczowym etapem przygotowania podłoża jest gruntowanie. Gruntowanie ma na celu zwiększenie przyczepności materiału hydroizolacyjnego do podłoża, związanie resztek pyłu, które mogły pozostać po czyszczeniu, oraz wyrównanie chłonności podłoża. Typ gruntu musi być dobrany do rodzaju stosowanej hydroizolacji – inne grunty stosuje się pod masy bitumiczne, inne pod szlamy cementowe, a jeszcze inne pod membrany syntetyczne lub masy poliuretanowe. Czas schnięcia gruntu jest krytyczny i zależy od warunków środowiskowych (temperatury i wilgotności powietrza); zazwyczaj wynosi od kilkudziesięciu minut do kilku godzin. Przystąpienie do aplikacji hydroizolacji na niedostatecznie suchy lub zbyt świeży grunt to prosty sposób na osłabienie całego systemu. Przykładowo, grunt pod masy KMB często schnie od 1 do 3 godzin w temperaturze 20°C, ale czas ten może wydłużyć się czterokrotnie w niższych temperaturach i wyższej wilgotności.
Kontrola jakości przygotowanego podłoża jest absolutnie konieczna przed przystąpieniem do dalszych prac. Obejmuje ona wizualną ocenę czystości i równości, a czasem pomiary wilgotności betonu (np. metodą karbidową CM lub przy użyciu higrometru elektronicznego z sondą w otworze w betonie). Dopuszczalny poziom wilgotności zależy od typu izolacji, ale dla wielu mas polimerowych czy żywicowych często wymagana wilgotność powierzchniowa nie powinna przekraczać 4-5% CM, a wilgotność względna w głębi <80% RH. Spełnienie tych warunków gwarantuje, że aplikowana hydroizolacja będzie miała szansę w pełni rozwinąć swoje właściwości i zapewnić trwałą ochronę przed wilgocią.
Materiały i techniki wykonania hydroizolacji poziomej płyty fundamentowej
Rynek budowlany oferuje szeroki wachlarz materiałów do wykonywania hydroizolacji poziomej płyty fundamentowej, a wybór konkretnego rozwiązania zależy od wielu czynników: od specyfiki obiektu i warunków gruntowych, przez harmonogram prac, po możliwości finansowe inwestora i doświadczenie ekipy wykonawczej. Każdy materiał ma swoje unikalne właściwości i wymagania dotyczące aplikacji.
Jednymi z najczęściej stosowanych materiałów są modyfikowane papy bitumiczne. Są to materiały rolowe, których warstwę hydroizolacyjną stanowi asfalt modyfikowany polimerami, takimi jak SBS (kauczuk syntetyczny, zwiększający elastyczność w niskich temperaturach) lub APP (tworzywo sztuczne, zwiększające odporność na wysokie temperatury). Papę najczęściej układa się metodą termozgrzewalną – dolna warstwa bitumiczna papy jest rozgrzewana palnikiem gazowym, co powoduje jej upłynnienie i sklejanie z przygotowanym podłożem. Wymaga to precyzji i doświadczenia, a także przestrzegania rygorystycznych zasad bezpieczeństwa przeciwpożarowego, jako że otwarty ogień jest obecny na budowie. Grubość takiej papy do zastosowań przeciwwilgociowych (typ A/T) wynosi zazwyczaj 3-4 mm, a w przypadku wymaganej izolacji przeciwwodnej (typ T/W) może przekraczać 4-5 mm. Rolki mają standardową szerokość około 1 metra i długość 5-7,5 metra. Papy wymagają zakładów (overlapping) minimum 10-15 cm na stykach podłużnych i 15-20 cm na stykach poprzecznych, które również muszą być starannie zgrzane, tworząc monolityczną powłokę. Wadą tej metody jest pracochłonność i konieczność użycia ognia; zaletą – sprawdzona trwałość i relatywnie niskie koszty materiału.
Alternatywą dla pap zgrzewalnych są papy samoprzylepne. Są to również materiały rolowe, ale warstwa bitumiczna aktywuje się i przyczepia do podłoża bez użycia ognia, zazwyczaj po usunięciu folii ochronnej i dociśnięciu rolki. Wymagają bardzo dokładnie przygotowanego i zagruntowanego podłoża oraz odpowiedniej temperatury aplikacji (zazwyczaj powyżej +5°C, a najlepiej powyżej +10°C do +15°C). Choć szybsze w instalacji i bezpieczniejsze pod względem pożarowym, są zazwyczaj droższe od pap zgrzewalnych, a ich przyczepność do nierównych lub słabo przygotowanych podłoży może być gorsza. Ich typowa grubość waha się od 1,5 do 2,5 mm. Zastosowanie pap samoprzylepnych pod płytą, która następnie jest zbrojona i zalewana betonem, wymaga często dodatkowego zabezpieczenia przed przebiciem przez zbrojenie lub gruz, np. w postaci geowłókniny ochronnej o gramaturze minimum 300 g/m². Geowłóknina ta pełni również funkcję drenażową i ochronną.
Inną popularną grupą materiałów są masy bitumiczne modyfikowane polimerami, tzw. masy KMB (grubowarstwowe powłoki bitumiczne). Są to materiały nakładane w postaci płynnej lub pasty na zimno, jedno- lub dwuskładnikowe. Aplikuje się je najczęściej szpachelką, pacą stalową lub metodą natrysku hydrodynamicznego w dwóch, rzadziej w trzech warstwach. Całkowita grubość suchej powłoki hydroizolacyjnej dla zastosowań przeciwwilgociowych to zazwyczaj 2-3 mm, a dla zastosowań przeciwwodnych (gdzie występuje ciśnienie hydrostatyczne wody) nawet 4-5 mm. Masy KMB wymagają gruntowania podłoża specjalnymi emulsjami bitumicznymi. Zaletą mas KMB jest bezspoinowość powłoki oraz łatwość formowania skomplikowanych kształtów i detali, takich jak przejścia rurowe czy naroża. Czas schnięcia jednej warstwy zależy od warunków otoczenia i wynosi od kilku do kilkudziesięciu godzin. Pełne związanie i uzyskanie parametrów hydroizolacyjnych zajmuje zazwyczaj kilka dni. Przykładowo, warstwa o grubości 3 mm może schnąć w optymalnych warunkach (20°C, 50% wilgotności) około 48 godzin, ale w chłodniejszych i wilgotniejszych warunkach czas ten może ulec znacznemu wydłużeniu. Wady to dłuższy czas aplikacji (konieczność schnięcia między warstwami) i wrażliwość na niskie temperatury w trakcie aplikacji (<5°C). Masy KMB często wzmacnia się w miejscach krytycznych (naroża, przejścia rurowe, pęknięcia) siatką z włókna szklanego lub polipropylenu wtapianą w świeżą warstwę.
Szlamy uszczelniające, inaczej hydroizolacje mineralne lub cementowe, to mieszanki cementu, wypełniaczy mineralnych i polimerów. Nakłada się je w formie płynnej zaprawy pędzlem, pacą lub natryskiem, zazwyczaj w 2-3 warstwach krzyżujących się. Totalna grubość suchej powłoki wynosi zazwyczaj 2-4 mm. Szlamy dzielą się na sztywne i elastyczne; pod płytę fundamentową stosuje się zazwyczaj szlamy elastyczne, które są w stanie mostkować niewielkie rysy (o rozwartości zazwyczaj do 0,2-0,5 mm). Są paroprzepuszczalne, co bywa zaletą w pewnych specyficznych zastosowaniach, choć w przypadku izolacji poziomej pod płytą na gruncie nie jest to parametr kluczowy, gdyż główny problem to woda w stanie ciekłym. Zaletą szlamów jest możliwość aplikacji na lekko wilgotne podłoża (choć bez stojącej wody) i dobra przyczepność do betonu. Wady to niższa odporność mechaniczna w porównaniu do mas bitumicznych czy membran, a także mniejsza zdolność do mostkowania szerszych rys. Czas schnięcia pierwszej warstwy to zazwyczaj kilka godzin, drugiej – kilkanaście do kilkudziesięciu. Pełne związanie następuje po kilku dniach. Koszt materiału na 1 m² dla szlamu o grubości 2,5 mm może wynosić około 30-50 zł, nie wliczając kosztów przygotowania podłoża i robocizny.
Nowoczesne materiały to membrany syntetyczne, takie jak FPO (elastyczne poliolefiny), PVC (polichlorek winylu) czy TPO (termoplastyczne poliolefiny). Są to materiały rolowe, układane na sucho, których szczelność zapewnia się poprzez zgrzewanie styków pasów gorącym powietrzem. Metoda ta wymaga specjalistycznego sprzętu (automatycznych zgrzewarek) i wyszkolonej ekipy. Membrany są bardzo elastyczne i odporne na przebicie (choć również wymagają często warstwy ochronnej), a ich szczelność w obrębie zgrzewów jest niezwykle wysoka. Standardowa grubość membrany FPO lub PVC do tego celu wynosi 1,2 - 2,0 mm. Są to rozwiązania droższe materiałowo i wykonawczo niż papy czy masy KMB, ale oferujące bardzo wysoką trwałość i niezawodność. Idealnie sprawdzają się w obiektach wymagających najwyższego stopnia zabezpieczenia, np. w piwnicach użytkowych lub na terenach z wysokim poziomem wód gruntowych. Rolki mogą być szerokie (np. 2 metry), co przyspiesza pokrycie dużych powierzchni, ale komplikuje układanie w małych, nieregularnych przestrzeniach. Wymagają precyzyjnego kotwienia mechanicznego na obwodzie lub dociążenia.
Przy wyborze materiału i techniki wykonania hydroizolacji pod płytą fundamentową kluczowe jest ścisłe przestrzeganie zaleceń producenta systemu. Różni producenci mają różne wytyczne dotyczące przygotowania podłoża, gruntowania, minimalnej grubości warstw, ilości warstw, czasów schnięcia międzywarstwowego oraz warunków środowiskowych podczas aplikacji. Ignorowanie tych zaleceń, np. układanie masy w zbyt niskiej temperaturze, aplikacja zbyt cienkiej warstwy, czy skracanie czasu schnięcia, jest najprostszą drogą do wady izolacji, która ujawni się po latach, gdy naprawa będzie znacznie trudniejsza i droższa. Wykonawca powinien posiadać odpowiednie doświadczenie w pracy z wybranym materiałem, co ma niebagatelne znaczenie dla jakości finalnego efektu.
W niektórych specyficznych przypadkach, na przykład przy betonach wodoszczelnych lub posadzkach przemysłowych z podwyższoną odpornością na wilgoć, stosuje się dodatek do betonu w postaci proszków lub płynów, które zmniejszają nasiąkliwość całej struktury (tzw. krystalizacja wgłębna). Jest to jednak zazwyczaj uzupełnienie, a nie substytut tradycyjnej izolacji, zwłaszcza gdy budynek narażony jest na działanie wody pod ciśnieniem. Ceny materiałów hydroizolacyjnych są bardzo zróżnicowane – orientacyjne ceny materiału na m² dla pap bitumicznych zgrzewalnych zaczynają się od ok. 15-25 zł, dla mas KMB od 20-40 zł (w zależności od grubości), dla szlamów od 30-50 zł, a dla membran syntetycznych mogą przekraczać 50-80 zł. Koszt robocizny to osobna kwestia i zależy od regionu, doświadczenia ekipy i stopnia skomplikowania projektu (ilości detali). Należy jednak zawsze pamiętać, że wybór i prawidłowe zastosowanie odpowiednich materiałów to fundament szczelnej konstrukcji.
Szczegóły i połączenia w hydroizolacji poziomej płyty fundamentowej
Powierzchnia płyty fundamentowej rzadko kiedy jest idealnie gładką, pozbawioną przeszkód płaszczyzną. Zawsze mamy do czynienia z elementami przechodzącymi przez płytę (rury instalacyjne, kanały), połączeniami z innymi elementami konstrukcyjnymi (ścianami) czy krawędziami i narożami. To właśnie te miejsca – detale i połączenia – stanowią największe wyzwanie w sztuce wykonywania hydroizolacji. Mówi się, że system hydroizolacyjny jest tak szczelny, jak szczelne jest jego najsłabsze ogniwo, a najsłabszym ogniwem zazwyczaj nie jest płaszczyzna, lecz właśnie szczegół.
Przejścia rurowe to klasyczny przykład newralgicznego punktu. Każda rura (kanalizacyjna, wodociągowa, elektryczna) przechodząca przez płytę fundamentową tworzy przerwę w ciągłości hydroizolacji. Konieczne jest precyzyjne i trwałe uszczelnienie wokół każdego takiego elementu. Metody różnią się w zależności od użytego materiału hydroizolacyjnego. Przy zastosowaniu pap bitumicznych, wokół rury należy zastosować specjalne kielichy lub kołnierze z papy, starannie zgrzewając je do powierzchni płyty i do samej rury, podciągając papę minimum 15-20 cm w górę po pionowej powierzchni rury. Inną metodą jest stosowanie specjalnych mankietów uszczelniających, które nasuwa się na rurę i trwale klei lub zgrzewa do hydroizolacji płyty. Przejścia rurowe wymagają często więcej niż jednej warstwy wzmacniającej i zastosowania specjalnych mas uszczelniających lub kitów w połączeniu z papą, aby wypełnić wszelkie mikroprzestrzenie.
W przypadku stosowania mas bitumicznych (KMB) lub szlamów uszczelniających, przejścia rurowe uszczelnia się poprzez staranne nałożenie masy lub szlamu wokół rury, zazwyczaj w kilku warstwach o zwiększonej grubości w tym miejscu. Konieczne jest zastosowanie taśm uszczelniających z włókna szklanego lub specjalnych mankietów z tkaniny polipropylenowej, które wtapia się w świeżą warstwę hydroizolacji w narożniku utworzonym przez rurę i płytę oraz na samej rurze. Mankiet taki powinien wystawać na co najmniej 10-15 cm na powierzchnię płyty. Połączenie musi być bezszwowe i elastyczne, aby wytrzymać ewentualne niewielkie ruchy rury czy skurcz betonu. Pamiętajmy o dokładnym oczyszczeniu powierzchni rury w miejscu styku z hydroizolacją.
Szczególnie istotne są połączenia hydroizolacji poziomej płyty fundamentowej z pionową hydroizolacją ścian (o ile występuje w strefie podziemnej) lub z warstwą hydroizolacji poziomej muru (izolacją przeciwwilgociową ścian fundamentowych lub przyziemia). Celem jest stworzenie ciągłej, szczelnej "wanny", która zapobiegnie bocznemu przenikaniu wilgoci oraz podciąganiu jej do murów ponad płytą. Hydroizolacja pozioma płyty powinna zostać wywinięta na pionową powierzchnię ściany fundamentowej na wysokość zgodną z projektem (zazwyczaj co najmniej 15-20 cm ponad poziom terenu lub posadzki), a następnie połączona lub zakończona w sposób umożliwiający szczelne połączenie z izolacją pionową ściany lub DPC (damp-proof course) muru. Klasyczne rozwiązanie to wywinięcie papy z płyty na ścianę i wklejenie jej pod papę izolacji poziomej muru, zapewniając zakład co najmniej 15 cm. Przy masach KMB lub szlamach, powłokę nakłada się w ciągły sposób z płyty na ścianę, formując w narożu tzw. fasetę (zaokrąglenie z zaprawy lub masy) w celu uniknięcia ostrego kąta i wzmacniając to miejsce taśmą uszczelniającą wtapianą w masę.
Inne krytyczne punkty to naroża wewnętrzne i zewnętrzne. Choć na płaskiej powierzchni płyty narożniki mogą wydawać się mniej problematyczne niż na styku płyty i ściany, każdy załamany kształt koncentruje naprężenia, zarówno termiczne (skutek zmian temperatury) jak i mechaniczne (np. skurcz betonu). Dlatego naroża wewnętrzne powinny być zaokrąglane fasetami, a naroża zewnętrzne fazowane, a następnie starannie wzmacniane. W przypadku pap, w narożach wewnętrznych układa się dodatkowe pasy papy (tzw. wyoblenia), a w narożach zewnętrznych docina i zgrzewa materiał z najwyższą precyzją. Masy KMB i szlamy wymagają wtopienia w naroża specjalnych, elastycznych taśm uszczelniających, które kompensują ruchy i gwarantują ciągłość powłoki w tym punkcie. Właściwe uformowanie tych detali to połowa sukcesu w osiągnięciu długotrwałej szczelności płyty fundamentowej.
Dylatacje i przerwy robocze w płycie fundamentowej (miejsca, gdzie betonowanie zostało przerwane) to absolutnie kluczowe miejsca, które wymagają specjalnego podejścia. Dylatacje celowo dzielą płytę na mniejsze pola, umożliwiając kontrolowany ruch betonu wynikający np. z jego skurczu czy zmian temperatury. Zwykła warstwa hydroizolacji uległaby w tym miejscu przerwaniu. Konieczne jest zastosowanie specjalistycznych systemów uszczelniających dylatacje. Najczęściej stosuje się specjalne taśmy dylatacyjne wklejane w elastyczną masę lub klej, mostkujące szczelinę. Taśmy te wykonane są z materiałów o dużej elastyczności (np. kauczuku EPDM lub modyfikowanego PVC) i mają szerokość pozwalającą na wklejenie ich części na każdym boku dylatacji, pozostawiając "pętlę" materiału w samej szczelinie dylatacyjnej, aby mogła kompensować ruchy. Inne rozwiązanie to stosowanie taśm pęczniejących (hydrofilowych), które umieszcza się w przerwie roboczej; pęcznieją one pod wpływem kontaktu z wodą, tworząc szczelne połączenie. Wybór systemu do dylatacji zależy od przewidywanej wielkości ruchów dylatacyjnych i ciśnienia wody. Błąd w uszczelnieniu dylatacji gwarantuje przeciek, bo szczelina dylatacyjna jest wręcz zaprojektowanym "wejściem" do środka konstrukcji.
Przy układaniu pap czy membran syntetycznych na płycie fundamentowej ważne jest również zabezpieczenie warstwy hydroizolacyjnej przed mechanicznym uszkodzeniem podczas kolejnych etapów budowy, np. podczas układania zbrojenia pod betonową posadzkę lub podczas prac instalacyjnych. Stosuje się w tym celu warstwę ochronną w postaci geowłókniny technicznej o wysokiej gramaturze (np. 500 g/m²) lub folię kubełkową (membranę wytłaczaną) rozłożoną na izolacji. Ta warstwa amortyzuje punktowe naciski i chroni przed przebiciem. Minimalna gramatura geowłókniny ochronnej stosowanej bezpośrednio na papie zgrzewalnej wynosi zazwyczaj 300 g/m², ale przy intensywnych pracach na płycie zaleca się wyższe gramatury (np. 500 g/m²). To niewielki dodatkowy koszt (np. 5-10 zł/m² za geowłókninę), który ratuje całą, dużo droższą warstwę hydroizolacji przed zniszczeniem.
Wykonanie detali i połączeń wymaga nie tylko wiedzy i doświadczenia, ale także czasu i precyzji. "Uproszczenie" tych elementów, oszczędność na materiałach do detali (np. użycie zwykłej papy zamiast mankietów uszczelniających przy rurze) czy pośpiech w ich wykonaniu zemści się w przyszłości. Dobra hydroizolacja to taka, w której każdy element, od rozległej płaszczyzny po najmniejsze przejście śruby kotwiącej, jest starannie zabezpieczony. Nadzór nad pracami w obrębie detali jest kluczowy i często wymaga od inspektora lub kierownika budowy dokładnego sprawdzenia każdego połączenia przed zaakceptowaniem warstwy hydroizolacyjnej jako zakończonej. Inwestycja w solidne, systemowe rozwiązania do detali i zatrudnienie ekipy z doświadczeniem w ich wykonywaniu to gwarancja szczelności izolacji poziomej płyty fundamentowej na lata.