Wylanie Płyty Fundamentowej Krok po Kroku: Przewodnik 2025
Zaczynamy od samego początku budowy, czyli czegoś, bez czego żaden dom nie stanie stabilnie. Gdy mówimy o podstawie przyszłego budynku, często pojawia się termin Wylanie płyty fundamentowej. To kluczowy etap, polegający na stworzeniu monolitycznej, żelbetowej konstrukcji spoczywającej bezpośrednio na przygotowanym podłożu gruntowym pod całą powierzchnią rzutu budynku, która przenosi wszystkie obciążenia z góry w sposób równomierny, a w pewnych sytuacjach okazuje się najlepszym rozwiązaniem, wręcz zbawiennym dla przyszłych mieszkańców.
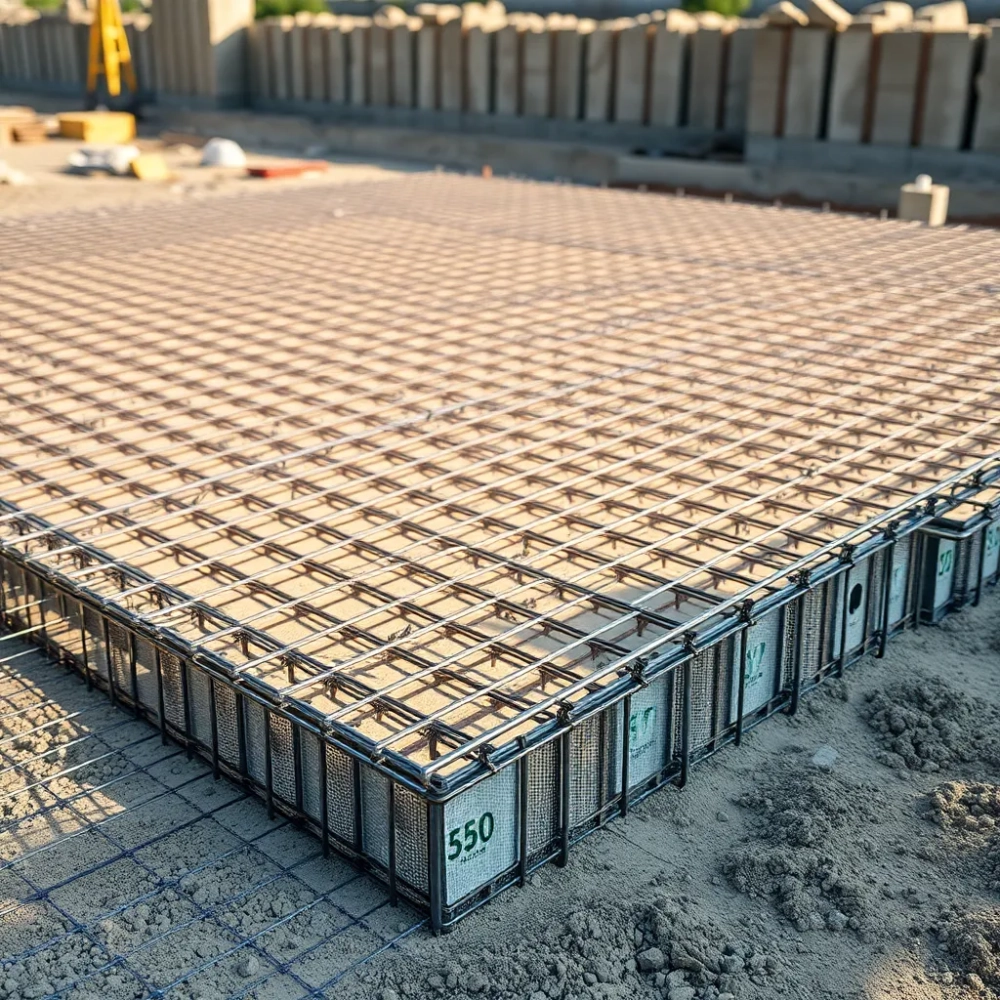
Wybór typu fundamentu to jedna z pierwszych i najważniejszych decyzji na placu budowy. Tradycyjne ławy fundamentowe przez lata dominowały, ale nowoczesne budownictwo coraz śmielej sięga po alternatywy. Płyta fundamentowa zyskuje na popularności nie bez powodu – jest uniwersalna i szybka w realizacji. Jej zastosowanie sprawdza się od małych domów jednorodzinnych, gdzie liczy się każdy dzień budowy, aż po budynki o skomplikowanych kształtach czy posadowione na trudnym gruncie.
Przy tradycyjnych fundamentach musimy pamiętać o głębokości przemarzania gruntu, która w Polsce bywa znaczna. Płytę, jeśli warunki pozwalają, można wykonać nieco płycej, nawet na głębokości około 50 cm poniżej terenu, co jest zgodne z krajowymi normami. Dzięki temu, że płyta rozkłada ciężar budynku na znacznie większą powierzchnię niż liniowe ławy, minimalizuje ryzyko osiadania i pęknięć, co czyni ją solidną bazą nawet na gruntach o niskiej nośności, a nawet tych podmokłych przy odpowiedniej izolacji.
Co ciekawe, wybetonowana i równa płyta fundamentowa służy jednocześnie jako gotowa podłoga na gruncie dla parteru, eliminując potrzebę dodatkowych prac. Można w niej nawet zintegrować system ogrzewania podłogowego, tworząc płytę fundamentową grzewczą, która akumuluje ciepło i oddaje je do pomieszczeń, co jest szczególnie atrakcyjne w domach energooszczędnych. Ta opcja to nie tylko komfort, ale też potencjalne oszczędności w przyszłej eksploatacji budynku.
Patrząc na wybór fundamentu z perspektywy praktyka, widzimy, że decyzja o płycie fundamentowej ma dalekosiężne konsekwencje. Przykładowo, skraca czas potrzebny na etap fundamentowania – często do zaledwie jednego tygodnia, w porównaniu do kilku tygodni wymaganych przy ławach, zwłaszcza na słabym gruncie. To wymierna korzyść dla inwestora, pozwalająca szybciej przejść do kolejnych etapów budowy.
Przygotowanie podłoża i samej płyty to proces wymagający precyzji, od projektu po wykonanie każdego detalu. W kolejnych sekcjach przyjrzymy się bliżej kluczowym etapom tego przedsięwzięcia, opierając się na zgromadzonych danych i doświadczeniu w branży. Zrozumienie tych kroków jest niezbędne, aby zapewnić trwałość i bezpieczeństwo całej konstrukcji.
Aspekt | Typowe wymagania/parametry (dla ok. 100m² domu parterowego) | Uwagi |
---|---|---|
Głębokość posadowienia | Ok. 50-80 cm poniżej terenu (w Polsce) | Zależne od strefy przemarzania i warunków gruntowych. |
Grubość płyty żelbetowej | 20-30 cm | W zależności od obciążeń z budynku i gruntu. Standardowo 25 cm dla domów jednorodzinnych. |
Klasa betonu | C20/25 (dawniej B25) lub C25/30 | Beton konstrukcyjny z atestem. |
Stopień wodoszczelności betonu | W8 | Zalecane, aby minimalizować ryzyko wnikania wody. |
Rodzaj zbrojenia dolnego | Siatka zgrzewana #10 co 15 cm (#Q257) lub pręty φ10-12 co 15-20 cm | Kierunki głównego i dodatkowego zbrojenia wg projektu. |
Rodzaj zbrojenia górnego | Siatka zgrzewana #8 co 15 cm (#Q188) lub pręty φ8-10 co 20-25 cm | Układana na "krzesłach" dystansowych, chroniąca przed pękaniem i uskokami. |
Grubość podbudowy z kruszywa | Minimum 10-20 cm zagęszczonego kruszywa (piasek, pospółka, tłuczeń) | Stanowi warstwę wyrównawczą i często drenażową. |
Grubość izolacji termicznej (XPS) | 10-20 cm | Układana pod płytą i/lub po jej obwodzie, zależnie od projektu energooszczędności. |
Szacowany czas realizacji (przy sprzyjającej pogodzie) | 4-7 dni (od początku wykopu do wylania betonu) | Znacznie krócej niż przy ławach. |
Szacowany koszt materiałów (na 100m²) | Ok. 200-350 PLN/m² (beton, stal, izolacja, kruszywo) | Zależny od lokalizacji, dostawców, grubości płyty/izolacji. |
Szacowany koszt robocizny (na 100m²) | Ok. 150-250 PLN/m² | Zależny od ekipy, złożoności rzutu budynku. |
Całkowity szacowany koszt (na 100m²) | Ok. 350-600 PLN/m² | Dla typowej płyty 25cm grubości z podstawową izolacją. |
Prezentowane dane rzucają światło na skalę przedsięwzięcia i specyfikę płyty fundamentowej. Widzimy wyraźnie, że choć czas realizacji jest imponująco krótki – często udaje się zamknąć fundament w jednym tygodniu – to wymaga to precyzyjnego planowania i wykorzystania specyficznych materiałów oraz technologii. Koszty, wyrażone na metr kwadratowy, obejmują szereg elementów, od kruszywa i izolacji, przez zbrojenie, aż po sam beton konstrukcyjny.
Znajomość tych szacunkowych wartości pomaga lepiej przygotować się na nadchodzące wyzwania budowlane. Odpowiednia podbudowa, właściwe zbrojenie i precyzyjnie dobrany beton to fundamenty (nomen omen!) sukcesu całego przedsięwzięcia. Przejdźmy teraz do szczegółowego omówienia kluczowych etapów realizacji płyty, które decydują o jej trwałości i funkcjonalności na lata.
Przygotowanie Płyty do Wylewania: Szalunek, Zbrojenie, Instalacje
Fundament każdego solidnego budynku nie powstaje ot tak, magicznie. To efekt skrupulatnych przygotowań, porównywalnych do prac snycerza rzeźbiącego precyzyjnie w drewnie – tyle że w większej skali i z użyciem ciężkiego sprzętu. Etap przygotowania płyty fundamentowej pod przyjęcie betonu to chwila prawdy dla całego projektu.
Zaczynamy od wytyczenia w terenie. Geodeta nanosi punkty zgodnie z projektem, określając obrys przyszłego domu, jego wysokość oraz kluczowe osie. Ten moment jest absolutnie krytyczny, pomyłka na tym etapie jest jak złe nuty w pierwszej sekundzie koncertu – potem jest tylko gorzej.
Następnie wykonuje się wykop pod płytę. Głębokość wykopu zależy od projektu, warunków gruntowych oraz wspomnianej wcześniej polskiej normy dotyczącej głębokości posadowienia, która zazwyczaj oscyluje wokół 50-80 cm. Z wykopu usuwa się warstwę humusu, a często sięga do nośnego gruntu rodzimego.
Dno wykopu musi być równe i odpowiednio zagęszczone. Często wykonuje się tak zwany chudy beton (np. B10, o grubości 5-10 cm) jako warstwę stabilizującą i wyrównawczą, która jednocześnie stanowi barierę kapilarną. To trochę jak kładzenie obrusu przed przyjęciem gości – porządkuje i przygotowuje scenę.
Kolejnym elementem jest podbudowa z kruszywa – warstwa piasku, pospółki lub tłucznia o grubości co najmniej 10-20 cm. Tę warstwę również trzeba solidnie zagęścić, najlepiej mechanicznym sprzętem wibracyjnym (np. zagęszczarka skoczkowa lub płytowa), co pozwala na usunięcie pustek i zapewnia równomierne oparcie dla przyszłej płyty. Wilgotność kruszywa jest ważna; zbyt suche nie zagęści się poprawnie.
Na zagęszczonej podbudowie lub chudym betonie układa się pierwszą warstwę hydroizolacji i termoizolacji. Najczęściej stosuje się folię budowlaną PE o grubości 0,3-0,5 mm jako warstwę poślizgową i wstępną barierę, a na niej układa się płyty z ekstrudowanego polistyrenu (XPS), materiału odpornego na wilgoć i ściskanie. Grubość XPS-u to zazwyczaj od 10 do 20 cm, a nawet więcej w przypadku domów pasywnych.
Połączenia płyt XPS muszą być szczelne, często wykonuje się je na zakład lub z użyciem pianki montażowej, aby uniknąć mostków termicznych. Izolacja termiczna układana jest nie tylko pod płytą, ale też po jej obwodzie – to klucz do zminimalizowania strat ciepła na styku z gruntem. Bez tej "czapki" i "szalika" fundamentu, dom będzie uciekało cenne ciepło.
Następnie przechodzimy do szalunku. Szalunek zewnętrzny to konstrukcja wyznaczająca obrys płyty i nadająca jej docelowe wymiary oraz wysokość. Może być wykonany z desek, sklejki szalunkowej lub systemowych elementów szalunkowych. Musi być sztywny i solidny, zdolny przenieść napór świeżego betonu, co jest siłą nie do zbagatelizowania – potrafi rozepchnąć słabą konstrukcję z łatwością.
Jednocześnie w obrębie przyszłej płyty montowane są wszystkie niezbędne instalacje – przewody wodociągowe, kanalizacyjne, elektryczne, telekomunikacyjne. Wszystkie rury i peszle muszą być poprowadzone zgodnie z projektem, we właściwych miejscach, pod odpowiednim spadkiem (zwłaszcza kanalizacja) i zabezpieczone przed uszkodzeniem w trakcie wylewania betonu. Często otula się je dodatkową warstwą izolacji lub piasku, aby umożliwić im niewielki ruch.
Punktem kulminacyjnym przygotowań jest ułożenie zbrojenia. Dla płyt fundamentowych najczęściej stosuje się zbrojenie podwójne: dolne i górne. Dolne zbrojenie układa się bezpośrednio na warstwie izolacji termicznej (czasem z dodatkowymi podkładkami betonowymi o grubości 2-3 cm) i stanowi ono główną "kość" przenoszącą obciążenia z płyty na grunt.
Typowe zbrojenie dolne to siatka zgrzewana (np. symbol #Q257, oznaczający pręty φ10 mm ułożone co 15 cm w obu kierunkach) lub pręty żebrowane φ10-12 mm układane ręcznie co 15-20 cm. Zbrojenie górne, najczęściej wykonane z cieńszych prętów (np. siatka #Q188 - φ8 mm co 15 cm lub pręty φ8-10 mm co 20-25 cm), zapobiega pękaniu płyty od góry i powstawaniu uskoków przy obciążeniu.
Zbrojenie górne musi być wyniesione na odpowiednią wysokość – zazwyczaj w środku grubości płyty lub w górnej jej części – za pomocą specjalnych kształtek, tak zwanych "krzesełków" lub "dystansów". Odległość między warstwami zbrojenia oraz odległość od krawędzi płyty do zbrojenia (otulina betonowa, typowo 2-3 cm) są kluczowe i muszą być zgodne z projektem.
Połączenia siatek zbrojeniowych muszą być wykonane na odpowiedni zakład, związany drutem wiązałkowym. Minimalny zakład to zazwyczaj 40-50 średnic pręta, co przy siatce z prętów 10 mm oznacza zakład około 40-50 cm. To zapewnia ciągłość konstrukcji i poprawne przenoszenie sił. Brak prawidłowego zakładu to błąd, który może osłabić płytę w kluczowych miejscach.
W miejscach przewidzianych na słupy konstrukcyjne lub ściany nośne o większym obciążeniu, zbrojenie płyty jest często lokalnie zagęszczane lub wzmacniane dodatkowymi prętami (np. strzemionami, czyli zamkniętymi prostokątnymi pętlami z prętów). Wszelkie przejścia instalacji przez płytę (tzw. przepusty) muszą być również odpowiednio zbrojone dookoła, aby uniknąć osłabienia betonu.
Przed samym wylewaniem betonu całe przygotowanie jest jeszcze raz dokładnie sprawdzane przez kierownika budowy. To ostatni moment na weryfikację poprawności ułożenia szalunków, czystości formy (bez liści, błota, czy śmieci!), poprawności ułożenia i związania zbrojenia, a także położenia wszystkich instalacji. Lepiej dwukrotnie sprawdzić niż raz pożałować, gdy beton stwardnieje i błędy będą niemożliwe do naprawienia bez kosztownych przeróbek.
Właściwe przygotowanie to absolutna podstawa. Nawet najlepszy beton nie uratuje płyty, jeśli jej "wnętrze" i "ramy" są wadliwe. Precyzja na tym etapie przekłada się bezpośrednio na trwałość i niezawodność fundamentu na dziesięciolecia. Cała ekipa musi pracować jak jeden organizm, od geodety po osoby układające izolację i wiążące zbrojenie.
Jak Prawidłowo Wylać Beton na Płytę Fundamentową
Nadszedł moment, na który wszyscy czekają i którego obawiają się jednocześnie – przyjazd betoniarki, a często wielu betoniarek, bo na wylanie płyty fundamentowej beton przyjeżdża się litrami, a nawet dziesiątkami metrów sześciennych! To jest moment, gdy cała logistyka i wcześniejsze przygotowania zostaną poddane próbie. Prawidłowe wylanie betonu to sztuka wymagająca szybkości, koordynacji i wiedzy.
Po pierwsze, beton. Jaki beton? Z tabeli wiemy, że najczęściej stosuje się beton klasy C20/25 lub C25/30. To nie jest zwykła mieszanka. To specjalnie zaprojektowany beton konstrukcyjny, który musi spełniać określone parametry wytrzymałościowe, ale też te robocze – plastyczność (klasa konsystencji S3-S4 jest typowa dla pompowania) oraz stopień wodoszczelności (np. W8). Beton zamówiony w wytwórni musi być dostarczony wraz z dokumentami potwierdzającymi jego klasę, skład i atest – to absolutny wymóg.
Logistyka dostaw jest kluczowa. Płyty fundamentowe, zwłaszcza te większe (100m², 150m² i więcej), wymagają zazwyczaj kilkunastu, a nawet kilkudziesięciu metrów sześciennych betonu. To oznacza, że na budowę przyjedzie kilka betoniarek jedna za drugą. Wytwórnia betonu musi być uprzedzona o dokładnym harmonogramie dostaw, aby uniknąć zbyt długich przerw, które mogłyby doprowadzić do powstawania tzw. zimnych spoin (miejsca, gdzie beton zaczyna wiązać, zanim przyjedzie kolejna partia – potencjalnie osłabiające konstrukcję).
Pogoda ma ogromne znaczenie. Nie powinno się wylewać betonu podczas silnych opadów deszczu, ponieważ może to wypłukać cement z mieszanki, osłabiając ją i pogarszając jej właściwości. Unikać należy także skrajnych temperatur – w upale (powyżej 25-30°C) beton zbyt szybko wiąże i trudniej go obrobić oraz pielęgnować, natomiast w mrozie (poniżej 5°C) proces wiązania praktycznie ustaje lub wymaga specjalnych, kosztownych zabiegów.
Sposób podawania betonu na płytę zależy od warunków i wielkości płyty. Przy małych obiektach lub dobrym dojeździe betoniarka może podawać beton bezpośrednio z rynny spustowej. Przy większych powierzchniach i w trudniejszym terenie konieczna jest pompa do betonu – urządzenie, które przez rurę potrafi przetransportować płynny beton na znaczną odległość i wysokość. Pompa kosztuje, ale jej użycie znacząco przyspiesza i ułatwia proces.
W momencie, gdy pierwsza porcja betonu dociera na miejsce, zaczyna się wyścig z czasem – czas wiązania betonu. Ekipa na płycie, uzbrojona w łopaty, grabie i wibratory do betonu, musi działać sprawnie i w porozumieniu. Beton podawany jest partiami, a pracownicy rozprowadzają go po powierzchni szalunku, dbając, by dotarł w każde miejsce, zwłaszcza wokół rur instalacyjnych i między prętami zbrojenia.
Jedną z najczęstszych bolączek na budowach bywa zły przepływ informacji – ekipa na płycie woła o więcej betonu, a tu przerwa, bo poprzednia betoniarka utknęła w korku. Trzeba mieć rękę na pulsie i być w stałym kontakcie z wytwórnią i kierowcami. To element logistycznej układanki, który potrafi podnieść ciśnienie.
Kluczowym elementem po rozprowadzeniu betonu jest jego poprawne zagęszczenie betonu. Bez tego kroku w mieszance pozostaną pęcherze powietrza, które osłabią strukturę betonu. Do zagęszczania stosuje się wibratory – buławowe (pogrążane), które wkłada się w masę betonu, listwy wibracyjne, które kładzie się na powierzchnię i przesuwa, lub wibratory powierzchniowe.
Wibracja musi być prowadzona systematycznie i krótko w danym punkcie. Zbyt długie wibrowanie może doprowadzić do segregacji kruszywa – cięższe cząstki opadną na dno, a lżejsze "wypłyną" na wierzch, co jest niepożądane. Celem jest usunięcie powietrza uwięzionego w mieszance i dokładne obleganie prętów zbrojeniowych przez beton.
Wylewając beton, ważne jest też, by na bieżąco kontrolować poziom i równość. Używa się do tego specjalnych łat do ściągania betonu, które przesuwa się po szalunku, zbierając nadmiar betonu i wyrównując powierzchnię. To wstępne wyrównywanie pozwala uzyskać założoną grubość płyty i przygotować grunt pod dalsze prace wykończeniowe na powierzchni.
Cały proces wylewania na dużej płycie to dynamiczna praca zespołowa. Jedni rozprowadzają beton, inni wibrują, jeszcze inni wstępnie wyrównują. Komunikacja między członkami ekipy jest tu na wagę złota. Czas jest ograniczony – gdy beton zacznie tracić plastyczność, jego obróbka staje się coraz trudniejsza.
Pamiętajmy, że beton po wylaniu zaczyna proces wiązania, który trwa przez wiele dni i tygodni. Bezpośrednio po wylaniu jest bardzo wrażliwy na czynniki zewnętrzne. To nie jest moment, żeby zostawić go samemu sobie. Dalsze kroki – zagęszczanie, wyrównywanie i pielęgnacja – są równie istotne.
Prawidłowe wylanie to gwarancja, że beton osiągnie projektowaną wytrzymałość i będzie stanowił solidną, monolitową bazę. Błędy popełnione na tym etapie – niedowibrowanie, zbyt długie przerwy w dostawach betonu, wylewanie podczas deszczu – mogą poważnie osłabić płytę, prowadząc w przyszłości do kosztownych problemów.
Zagęszczanie i Wyrównywanie Świeżego Betonu
Wyobraź sobie ciasto wylewane do formy – samo w sobie nie wypełni idealnie każdego zakamarka, a w środku mogą zostać pęcherze powietrza. Podobnie jest z betonem, tyle że tu konsekwencje są o wiele poważniejsze niż zakalec. Dlatego etapy zagęszczania i wyrównywania świeżo wylanego betonu na płycie fundamentowej są absolutnie kluczowe dla jego wytrzymałości i funkcjonalności.
Zacznijmy od zagęszczania. Jak już wspomniano, głównym celem jest usunięcie z mieszanki betonowej pęcherzy powietrza. Pory powietrzne stanowią defekty w strukturze, które znacząco obniżają wytrzymałość betonu na ściskanie. Zwiększają też jego nasiąkliwość, czyniąc go bardziej podatnym na degradację, na przykład przez mróz czy agresywne środowisko.
Wibracja sprawia, że cząstki betonu (cement, woda, piasek, żwir) układają się ciaśniej i równomiernie otaczają zbrojenie. Betoniarze stosują różne rodzaje wibratorów. Najczęściej spotykane na budowach są wibratory buławowe (inaczej pogrążane). Składają się z silnika (elektrycznego lub spalinowego) i długiego, elastycznego wału zakończonego "buławą" – stalową rurką, która wibruje z dużą częstotliwością.
Operator wibruje buławą, zanurzając ją pionowo w masę betonu na kilkanaście sekund, po czym powoli ją wyciąga. Ważne jest, aby nie dotykać buławą bezpośrednio zbrojenia lub szalunków – to może prowadzić do ich uszkodzenia lub przesunięcia. Buławę zanurza się na tyle głęboko, aby jej zasięg działania (zazwyczaj około 30-50 cm wokół buławy) zachodził na poprzednio wibrowane sekcje, zapewniając ciągłość zagęszczenia.
Na większych, bardziej płaskich powierzchniach stosuje się często listwy wibracyjne. To aluminiowe lub stalowe belki o długości kilku metrów, wyposażone w wibratory. Układa się je na powierzchni betonu i przesuwa, co jednocześnie wibruje i wstępnie wyrównuje powierzchnię. Są wydajne, ale wymagają równego oparcia (np. na szalunku lub tymczasowych prowadnicach).
Po dokładnym zagęszczeniu, na powierzchni betonu pojawia się cienka warstwa zaczynu cementowego – to dobry znak, świadczący o usunięciu powietrza. Następnie przechodzimy do wyrównywania. Celem jest uzyskanie gładkiej i równej powierzchni o założonej płaskości. Standardowo dla podłóg na gruncie tolerancje wynoszą około 3-5 mm odchyłki na 2 metrach długości – czyli mniej więcej tyle, ile wynosi grubość monety.
Pierwszym krokiem jest ściąganie nadmiaru betonu za pomocą łat do ściągania. Mogą to być proste drewniane lub aluminiowe belki. Prowadząc je po szalunku lub punktach referencyjnych, usuwa się nadmiar betonu, nadając płycie właściwą grubość i wstępną równość. To fizycznie wymagające zadanie, zwłaszcza na dużej powierzchni.
Po wstępnym ściągnięciu, często używa się tzw. łat spływowych lub desek zacierających (bull float), które pozwalają na wygładzenie większych nierówności i wgnieceń pozostawionych przez łaty ściągające. Ruchy są szerokie, okrężne lub posuwiste, mające na celu "zamknięcie" powierzchni i lekkie wgłębienie grubszego kruszywa.
Następnym etapem jest zacieranie, które wykonuje się, gdy beton zaczyna częściowo wiązać – w momencie, gdy po nadepnięciu na niego pozostaje ślad o głębokości nie większej niż 1-2 cm. Zacieranie zamyka pory na powierzchni betonu, zwiększając jego odporność na ścieranie i chłonność. Można to robić ręcznie za pomocą pacy zacieraczki lub mechanicznie – przy użyciu zacieraczek spalinowych lub elektrycznych, popularnie nazywanych "helikopterami".
"Helikopter" to maszyna z obracającymi się łopatkami, która pozwala na szybkie i efektywne wygładzenie dużych powierzchni. Operator prowadzi maszynę po betonie, uzyskując pożądany stopień gładkości. Często wykonuje się kilka "przejazdów" helikopterem, używając najpierw łopatek płaskich do wstępnego zacierania, a potem łopatek skośnych (finiszerek) do uzyskania bardzo gładkiej powierzchni, czasem niemal lustrzanej.
Warto pamiętać, że zacieranie to moment, gdy wilgoć z betonu paruje. W upalne lub wietrzne dni proces ten może być bardzo szybki, prowadząc do tzw. skurczu plastycznego i powstawania drobnych, powierzchniowych rys. Czasem konieczne jest lekkie zraszanie powierzchni mgiełką wodną lub stosowanie specjalnych preparatów opóźniających odparowywanie (tzw. curing compounds), choć klasyczna pielęgnacja świeżo wylanego betonu poprzez nawadnianie jest najpewniejsza.
Po zakończeniu prac wykończeniowych na powierzchni, kluczowa jest właściwa pielęgnacja betonu. To etap często niedoceniany, a absolutnie fundamentalny dla osiągnięcia pełnej wytrzymałości. Proces hydratacji (wiązania cementu z wodą) trwa przez wiele dni i wymaga stałej obecności wilgoci. Jeśli beton wyschnie zbyt szybko, nie osiągnie projektowanych parametrów.
Pielęgnacja polega na utrzymywaniu powierzchni betonu w stanie wilgotnym przez co najmniej 7 dni w umiarkowanych temperaturach. Najprostsza metoda to przykrycie płyty folią budowlaną lub matami jutowymi/geowłókniną i regularne ich polewanie wodą. Można też stosować specjalne preparaty tworzące na powierzchni warstwę ograniczającą parowanie.
Brak właściwej pielęgnacji to prosta droga do problemów – pęknięć powierzchniowych, pylenia (osłabienia wierzchniej warstwy betonu), a w skrajnych przypadkach niedostatecznej wytrzymałości całego elementu. Warto zainwestować czas i środki w ten etap, bo naprawa skutków zaniedbania jest zazwyczaj droga i kłopotliwa.
Podsumowując, proces wylewania, zagęszczania i wykańczania powierzchni płyty fundamentowej wymaga nie tylko odpowiedniego sprzętu i materiałów, ale przede wszystkim wiedzy, doświadczenia i zgrania ekipy. Od jakości tych prac zależy to, czy płyta będzie stanowiła solidne, trwałe i równe podłoże dla kolejnych etapów budowy przez dziesięciolecia. Błędy na tym etapie mogą okazać się "fundamentem" przyszłych problemów z wilgocią, stabilnością podłóg czy nawet konstrukcją ścian.