Warstwy płyty fundamentowej: Jakie są i za co odpowiadają?
Fundamenty to bez wątpienia kręgosłup każdego solidnego budynku. Kiedyś dominowały tradycyjne ławy, dziś coraz częściej architekci i inwestorzy sięgają po rozwiązanie, które oferuje szereg przewag, szczególnie na wymagających gruntach: płytę fundamentową. Ale czym tak naprawdę są te słynne `warstwy płyty fundamentowej` i dlaczego są one tak kluczowe? W skrócie, chodzi o stworzenie kompleksowej, wielowarstwowej struktury, której podstawowym zadaniem jest równomierne rozłożenie potężnych obciążeń z całej konstrukcji domu na grunt poniżej, zapewniając stabilność i izolację od podłoża.
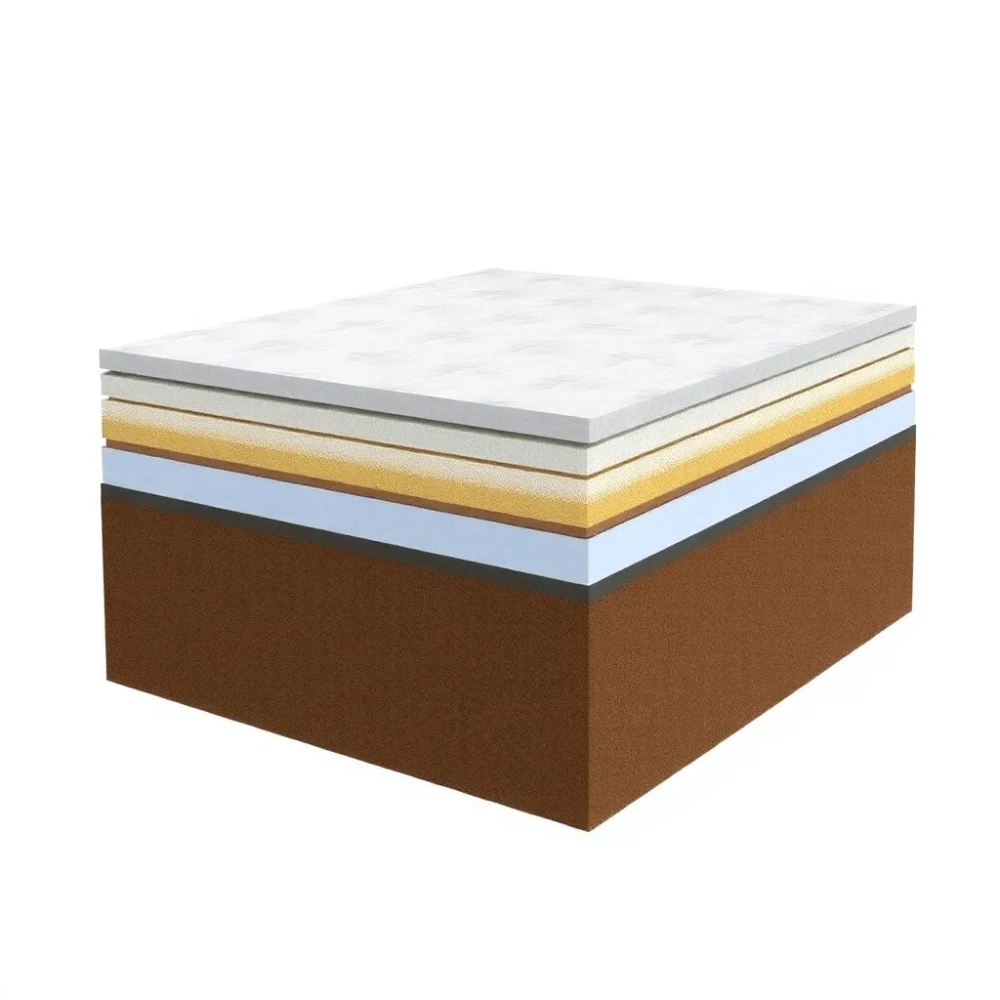
Gdy zagłębimy się w niuanse budowy, szybko staje się jasne, że każdy komponent ma swoją wagę, zarówno w sensie technicznym, jak i ekonomicznym. Przyjrzyjmy się przykładowym proporcjom kosztów i grubości, które charakteryzują typowe warstwy płyty fundamentowej w przeciętnym projekcie jednorodzinnym w Polsce. Te dane pomagają zrozumieć, gdzie koncentrują się nakłady i jakie elementy mają największy udział w całości.
Etap/Warstwa | Orientacyjny udział w kosztach materiałów i robocizny (%) | Typowa grubość/ilość |
Przygotowanie podłoża / Wykop | 10-15% | Zależna od projektu, min. 50 cm głębokości (Polska norma) |
Podsypka (żwir/piasek/kruszywo) | 15-20% | 20-40 cm |
Chudy beton | 5-8% | 8-15 cm |
Izolacja termiczna (XPS) | 12-18% | 10-30 cm lub więcej (w zależności od standardu energooszczędności) |
Izolacja przeciwwilgociowa (folie/papy) | 2-4% | Min. 2 warstwy folii 0.2 mm lub 1-2 warstwy papy |
Zbrojenie (stal) | 18-25% | Różna średnica i siatka, np. Ø12 co 15 cm (górna i dolna siatka) |
Beton konstrukcyjny (płyta żelbetowa) | 25-35% | 15-35 cm (najczęściej 20-25 cm dla domów jednorodzinnych) |
Analizując powyższe wartości, od razu widać, gdzie leży serce kosztów: w materiałach konstrukcyjnych, czyli betonie i stali, oraz w kluczowej izolacji termicznej. Podsypka również stanowi znaczący procent, co podkreśla wagę odpowiedniego przygotowania podłoża. Udział pracy wykonawców jest tutaj rozłożony, ale etapy takie jak przygotowanie podłoża, zbrojenie i samo wylanie betonu wymagają precyzji i doświadczenia, co oczywiście znajduje odzwierciedlenie w cenie robocizny. Pomyślcie o tym – każdy z tych elementów jest jak składnik ciasta: pominięcie jednego lub zastosowanie złych proporcji zepsuje całość.
Każdy centymetr grubości materiału, każdy pręt zbrojeniowy, każdy skrawek membrany izolacyjnej ma swoje niezastąpione miejsce w tej inżynierskiej układance. Ostateczny sukces posadowienia budynku na płycie fundamentowej zależy od pedantycznej dbałości o szczegóły na każdym etapie. To nie jest moment na oszczędzanie na jakości materiałów czy pośpieszne prace. Widziałem na własne oczy, jak próby cięcia kosztów na etapie fundamentów potrafiły mścić się latami w postaci pęknięć, zawilgocenia czy problemów z ogrzewaniem.
Przygotowanie podłoża i warstwy podkładowe
Fundamentem solidnego fundamentu, tak to właśnie działa w budownictwie, jest perfekcyjnie przygotowane podłoże. Ignorowanie tego etapu to proszenie się o kłopoty. Cały proces rozpoczyna się od geotechniki – badania gruntu, które jak rentgen pokazuje nam, z czym tak naprawdę mamy do czynienia pod powierzchnią.
W Polsce normy wymagają posadowienia fundamentów co najmniej 50 cm poniżej poziomu terenu ze względu na głębokość przemarzania, chociaż, jak słusznie zauważono, w innych krajach stosuje się głębokości rzędu 30 cm. Ta głębokość minimalizuje wpływ cykli zamarzania i rozmarzania wody w gruncie, które mogłyby „wypychać” fundament, powodując uszkodzenia.
Wykop pod płytę fundamentową powinien być wykonany z precyzją. To nie jest praca "na oko". Dno wykopu musi być równe i odpowiednio zagęszczone. W przypadku słabych gruntów, np. torfów czy namułów, często konieczna jest ich wymiana lub wzmocnienie metodami palowania czy kolumn FDC.
Na dno wykopu układa się pierwszą kluczową warstwę - geowłókninę separacyjną. Jej zadaniem jest oddzielenie rodzimego gruntu od materiału podsypki. Zapobiega to mieszaniu się warstw pod wpływem obciążeń i wody, co mogłoby pogorszyć nośność całej struktury.
Następny etap to wykonanie podsypki żwirowej lub z kruszywa łamanego. Jest to jedna z najgrubszych warstw pod płytą, jej miąższość zazwyczaj waha się między 20 a 40 cm, a w trudnych warunkach gruntowych może być nawet większa. Materiałem jest najczęściej piasek gruby, żwir płukany lub kruszywo o uziarnieniu np. 0/31.5 mm.
Cel tej warstwy jest wieloraki: przede wszystkim wyrównuje podłoże, działa jako warstwa odsączająca (drenażowa) w przypadku pojawienia się wody gruntowej i stanowi tzw. poduszkę, na której spoczywać będzie konstrukcja. Jej kluczową funkcją jest też przerwanie podciągania kapilarnego wody z głębszych warstw gruntu.
Podsypka musi być zagęszczona do określonego w projekcie stopnia (np. 98% wskaźnika Standard Proctora dla piasków). Używa się do tego zagęszczarek płytowych o odpowiedniej wadze lub walców wibracyjnych. Brak wystarczającego zagęszczenia to katastrofa w zarodku – osiadanie podsypki po czasie może doprowadzić do pęknięć w konstrukcji.
Sprawdzenie stopnia zagęszczenia przeprowadza się badaniami polowymi, np. sondą Proctora lub metodą DPL. Wynik musi potwierdzić, że osiągnięto wymaganą nośność i stabilność. Pomiar rzędnych podsypki za pomocą niwelatora laserowego zapewnia idealnie równy poziom przed przejściem do kolejnego kroku.
Na podsypce, po jej idealnym wypoziomowaniu i zagęszczeniu, wylewa się tzw. chudy beton (beton podkładowy, B10, B15 lub C8/10, C12/15). Warstwa ta ma zazwyczaj 8 do 15 cm grubości. Choć sama nie przenosi znaczących obciążeń, pełni niezwykle ważną funkcję technologiczną.
Chudy beton stanowi czystą, równą i stabilną bazę pod kolejne warstwy: izolacje i zbrojenie. Dzięki niemu można precyzyjnie układać izolacje przeciwwilgociową i termiczną, a także opierać na nim dystanse zbrojenia, zapewniając odpowiednią otulinę betonową prętów.
Wykonanie chudego betonu jest stosunkowo szybkie – zazwyczaj zajmuje jeden dzień roboczy dla przeciętnego domu. Materiał (beton) kosztuje orientacyjnie 250-350 zł/m³, a grubość warstwy i powierzchnia wykopu determinują potrzebną ilość.
Precyzja na etapie przygotowania podłoża i wykonania warstw podkładowych to inwestycja, która procentuje przez lata. Dobrze zagęszczona podsypka i równy chudy beton to fundament bez drżeń. Wiecie co? To jak malowanie obrazu – grunt musi być idealny, zanim nałożymy główne kolory. Bez tego całe dzieło będzie niedoskonałe, albo co gorsza, ulegnie destrukcji.
Kruszywo stosowane w podsypce musi być czyste, wolne od zanieczyszczeń organicznych i o odpowiednim uziarnieniu. Czasem stosuje się również warstwę piasku, szczególnie jako ostatnią wyrównującą warstwę przed chudym betonem, dla uzyskania gładkiej powierzchni. Pamiętajmy, że nawet najlepszy beton konstrukcyjny nie spełni swojej roli, jeśli posadowimy go na źle przygotowanym gruncie.
Koszt przygotowania podłoża, wliczając wykop, materiały na podsypkę (około 50-80 zł/tonę), zagęszczenie i chudy beton, może stanowić znaczącą część budżetu fundamentu. Mimo to, nie ma tu miejsca na półśrodki. To inwestycja w trwałość i bezpieczeństwo całego budynku.
Warto wspomnieć, że w zależności od typu gruntu, sposoby przygotowania mogą się różnić. Na gruntach gliniastych, mało przepuszczalnych, często wykonuje się dodatkowe drenaże opaskowe wokół płyty, aby odprowadzić nadmiar wody deszczowej czy gruntowej. Na gruntach piaszczystych drenaż naturalny jest lepszy, ale kluczowe staje się dokładne zagęszczenie.
Czas potrzebny na wykonanie wykopu i warstw podkładowych dla typowego domu jednorodzinnego to zazwyczaj 1-3 dni, w zależności od warunków gruntowych, wielkości domu i sprawności ekipy. Do tego dochodzi czas na ewentualne badania geotechniczne i zagęszczenia, które mogą zająć kolejny dzień. Dwa dni na osadzenie płyty na solidnym „dywanie” z kruszywa i betonu to czas dobrze zainwestowany.
Kluczowa rola izolacji: Termiczna i przeciwwilgociowa
Jeśli podsypka i chudy beton to stabilna platforma, to izolacje są niczym tarcza chroniąca budynek przed najgroźniejszymi wrogami: wilgocią i chłodem z gruntu. W systemie płyty fundamentowej pełnią one absolutnie fundamentalną rolę, często znacznie większą niż w tradycyjnych ławach.
Zacznijmy od izolacji przeciwwilgociowej. Jest ona układana bezpośrednio na warstwie chudego betonu. Jej zadaniem jest stworzenie bariery uniemożliwiającej kapilarne podciąganie wody z gruntu. Nawet jeśli zastosowaliśmy podsypkę odsączającą, wilgoć może występować w gruncie, a beton jest materiałem porowatym, łatwo ją wchłaniającym.
Do wykonania izolacji przeciwwilgociowej najczęściej stosuje się wytrzymałe folie budowlane z polietylenu, o grubości minimum 0.2 mm (200 mikronów). Zaleca się ułożenie co najmniej dwóch warstw takich folii, przesuniętych względem siebie, aby zminimalizować ryzyko nieszczelności. Alternatywnie, choć rzadziej w domach jednorodzinnych pod całą płytą, stosuje się papy termozgrzewalne.
Co kluczowe, arkusze folii muszą być układane na zakład minimum 10-15 cm, a wszystkie połączenia oraz miejsca przejść instalacji (rury, peszle) muszą być skrupulatnie sklejone specjalną taśmą butylową. Każda, nawet najmniejsza dziurka czy nieszczelność, będzie po latach kanałem dla wilgoci. To jest ten moment, gdzie precyzja i dokładność są ważniejsze od prędkości – brak tu miejsca na nonszalancję, to jak dziura w parasolu.
Dane mówią same za siebie: koszt dobrej folii przeciwwilgociowej to zaledwie kilka do kilkunastu złotych za metr kwadratowy. Biorąc pod uwagę, że jej niewłaściwe ułożenie może skutkować kosztownym zawilgoceniem ścian czy podłóg w przyszłości, oszczędzanie na tej warstwie jest ekonomicznym szaleństwem.
Druga, równie istotna warstwa, to izolacja termiczna. W przeciwieństwie do tradycyjnych fundamentów, gdzie izoluje się ściany fundamentowe, w płycie izolacja idzie „pod spodem”, często również na bocznych krawędziach. Chroni to całą powierzchnię podłogi na gruncie przed stratami ciepła.
Najczęściej stosowanym materiałem jest polistyren ekstrudowany, czyli XPS. Dlaczego XPS? Ponieważ charakteryzuje się bardzo niską nasiąkliwością (praktycznie zerową), wysoką wytrzymałością na ściskanie (jest układany pod ciężką płytą betonową) i doskonałymi parametrami termoizolacyjnymi (niski współczynnik lambda, typowo poniżej 0.035 W/(mK)).
Grubość izolacji termicznej pod płytą fundamentową zależy od standardu energetycznego budynku. W przypadku domów budowanych w standardzie warunków technicznych 2021 (WT 2021) minimalna grubość XPS pod podłogą na gruncie to często 10-15 cm. W domach energooszczędnych czy pasywnych stosuje się warstwy o grubości 20, 25, a nawet 30 cm, układane jedno- lub dwuwarstwowo (na mijankę, by zminimalizować mostki termiczne na połączeniach).
Pamiętacie tę scenę, gdy inżynier kładzie na placu budowy próbkę XPS i pokazuje, jak jest twarda? To nie show, to kluczowa cecha! Izolacja musi wytrzymać ciężar wylewanego betonu i obciążenia z budynku. Płyty XPS do tego celu mają zazwyczaj deklarowaną wytrzymałość na ściskanie ≥ 300 kPa (CS(10)300), a często nawet ≥ 400 kPa.
Koszt materiału izolacyjnego XPS waha się w zależności od grubości i producenta, ale orientacyjnie można przyjąć 200-400 zł/m³. Przy grubości 20 cm daje to koszt około 40-80 zł/m² samej izolacji termicznej. To znaczący element budżetu, ale spójrzmy na to z innej strony.
Dobra izolacja termiczna płyty fundamentowej to inwestycja, która zwraca się przez cały okres eksploatacji domu w postaci niższych rachunków za ogrzewanie i większego komfortu cieplnego. Brak ucieczki ciepła w dół sprawia, że podłoga na parterze jest przyjemnie ciepła, nawet bez dodatkowego ogrzewania podłogowego.
Ułożenie warstw izolacji wymaga równej i czystej powierzchni (stąd chudy beton). Płyty izolacyjne układane są szczelnie, z zakładkami lub na styk, a krawędzie zewnętrzne płyty fundamentowej również muszą być izolowane na pełnej wysokości, tworząc szczelną "wannę" termiczną i przeciwwilgociową.
Szczególnie ważne jest staranne połączenie izolacji pod płytą z izolacją pionową ścian zewnętrznych budynku. Właściwie zaprojektowany detal i pedantyczne wykonanie to jedyna gwarancja uniknięcia mostków termicznych i miejsc potencjalnego zawilgocenia na styku ściany z fundamentem.
Czasochłonność ułożenia izolacji, choć wymaga precyzji, jest umiarkowana. Dla typowego domu jednorodzinnego zajmuje to zazwyczaj 1-2 dni robocze. To etap, w którym można z dumą powiedzieć, że otacza się przyszły dom nieprzemakalnym i ciepłym płaszczem od dołu.
Podsumowując rolę izolacji: Izolacja przeciwwilgociowa i termiczna płyty fundamentowej to dwie siostry. Pierwsza chroni przed wodą, druga przed zimnem. Obie są niezbędne i obie wymagają bezkompromisowej staranności wykonania. Zaniedbanie którejkolwiek z nich może prowadzić do długotrwałych i kosztownych problemów. Nie ma na to innej rady, po prostu trzeba to zrobić porządnie.
Warstwa konstrukcyjna: Żelbet i zbrojenie płyty
Dochodzimy do samego rdzenia `płyty fundamentowej` – jej warstwy konstrukcyjnej, czyli żelbetu. To tutaj materiały spotykają się, tworząc monolityczną strukturę zdolną przenosić potężne obciążenia pionowe i poziome z całego budynku, a także naprężenia wynikające z warunków gruntowych.
Żelbet to genialne połączenie dwóch z pozoru prostych materiałów: betonu i stali. Beton doskonale radzi sobie ze ściskaniem, ale jest słaby na rozciąganie. Stal jest za to niezwykle wytrzymała na rozciąganie. Gdy połączymy je we właściwy sposób (zbrojenie umieszczone w betonie w miejscach występowania naprężeń rozciągających), otrzymujemy materiał o ogromnej wytrzymałości – żelbet właśnie.
Grubość konstrukcyjnej płyty żelbetowej w domach jednorodzinnych wynosi najczęściej od 15 do 35 cm. Standardem jest 20-25 cm, ale na bardzo słabych gruntach, przy dużych obciążeniach lub skomplikowanych rzutach budynku może być konieczna większa grubość.
Rodzaj betonu stosowanego na płytę fundamentową jest ściśle określony w projekcie. Zazwyczaj jest to beton klasy C20/25 lub C25/30. Cyfra po "C" oznacza minimalną wytrzymałość charakterystyczną na ściskanie (w tym przypadku 20 lub 25 MPa dla próbek walcowych i 25 lub 30 MPa dla próbek sześciennych) po 28 dniach dojrzewania. Skład mieszanki betonowej, w tym uziarnienie kruszywa (np. do 16 mm) i stosunek wodno-cementowy (w/c) są kluczowe dla uzyskania wymaganych parametrów.
Nie mniej ważna od betonu jest stal. Zbrojenie płyty fundamentowej projektuje się indywidualnie dla każdego budynku. Typowe rozwiązanie dla domów jednorodzinnych to siatki z prętów żebrowanych klasy A-IIIN lub A-500W, układane w dwóch płaszczyznach – górnej i dolnej.
Pręty zbrojeniowe mają zazwyczaj średnicę od Ø10 do Ø16 mm, a rozstaw siatki wynosi od 15x15 cm do 20x20 cm. Dokładne średnice i rozstawy zależą od obliczeń statycznych uwzględniających obciążenia z budynku, rozpiętości, otwory i warunki gruntowe.
Siatki zbrojeniowe łączy się drutem wiązałkowym lub specjalnymi klipsami. Kluczowe jest zapewnienie odpowiedniej otuliny betonowej – czyli minimalnej odległości zbrojenia od powierzchni betonu (zazwyczaj 2-3 cm od dołu i 3-4 cm od góry), chroniącej stal przed korozją i zapewniającej jej właściwą współpracę z betonem. Stosuje się do tego specjalne dystanse, plastikowe lub betonowe.
W niektórych projektach, oprócz siatek płaskich, stosuje się dodatkowe zbrojenie w postaci strzemion (pionowych prętów łączących siatki górną i dolną) lub prętów skupionych w miejscach występowania większych obciążeń, np. pod ścianami nośnymi lub słupami.
Koszt stali zbrojeniowej zależy od aktualnych cen na rynku, ale można przyjąć orientacyjnie 4-6 zł za kilogram (sama stal plus cięcie i gięcie). Ilość stali w płycie o grubości 25 cm dla domu o powierzchni 100-150 m² to zazwyczaj kilka ton.
Sam proces betonowania płyty fundamentowej to kulminacyjny moment. Beton jest najczęściej dostarczany na budowę betonowozami i podawany pompą do betonu. Wylewanie musi odbywać się w sposób ciągły na całej powierzchni płyty lub na fragmentach wydzielonych dylatacjami technologicznymi.
Po wylaniu betonu konieczne jest jego dokładne zagęszczenie, najczęściej za pomocą wibratorów do betonu (powierzchniowych – listwy wibracyjne, lub wewnętrznych – buławy wibracyjne). Wibrowanie usuwa pęcherze powietrza, co zwiększa wytrzymałość betonu i jego mrozoodporność.
Następnie powierzchnię betonu należy dokładnie zatrzeć i wygładzić, uzyskując gładką i równą posadzkę parteru. To właśnie ta idealnie równa powierzchnia jest jedną z głównych zalet płyty fundamentowej – jest od razu gotowa pod ułożenie warstw wykończeniowych podłogi.
Ostatnim, ale niezwykle ważnym etapem jest pielęgnacja betonu. Bezpośrednio po zatarciu należy zastosować środki do pielęgnacji (specjalne płyny natryskowe) lub przykryć powierzchnię folią budowlaną i regularnie ją zraszać wodą przez minimum 7-10 dni (a najlepiej dłużej, zwłaszcza w upały). Pielęgnacja zapobiega zbyt szybkiemu odparowywaniu wody z betonu, co jest przyczyną skurczu i powstawania rys skurczowych. Wiecie jak szybko wysycha gleba na słońcu? Z betonem jest podobnie, ale konsekwencje są dużo gorsze.
Pełną projektową wytrzymałość beton osiąga po 28 dniach, ale już po kilku dniach, po wstępnym związaniu, można ostrożnie po nim chodzić. Ciężkie prace, np. murowanie ścian nośnych, rozpoczyna się zazwyczaj po około 7-14 dniach, w zależności od zaleceń producenta betonu i warunków atmosferycznych.
Koszt warstwy konstrukcyjnej – żelbetu, obejmujący materiały (beton, stal) i robociznę (zbrojenie, betonowanie, pielęgnacja), stanowi największą część kosztu całej płyty. Precyzja na tym etapie, prawidłowe ułożenie zbrojenia (z zachowaniem otuliny i zakładów), odpowiednia klasa betonu i staranna pielęgnacja to gwarancja, że konstrukcja będzie bezpieczna i trwała przez dziesięciolecia.
Dodatkowe warstwy i elementy w zależności od specyfiki projektu
Choć standardowy pakiet `warstwy płyty fundamentowej` obejmuje podsypkę, chudy beton, izolacje i żelbet, nowoczesne projekty budynków energooszczędnych, pasywnych czy budowane w specyficznych warunkach często wymagają zastosowania dodatkowych elementów i warstw. To trochę jak dodawanie przypraw do dania – podnoszą jego jakość i dopasowują do indywidualnych potrzeb.
Jednym z coraz częściej spotykanych rozwiązań, zwłaszcza w domach energooszczędnych i pasywnych, jest zintegrowanie ogrzewania podłogowego bezpośrednio w konstrukcji płyty. Mówimy wtedy o tzw. płycie fundamentowej grzewczej. To rozwiązanie idealne, bo doskonale wykorzystuje naturalną zdolność betonu do akumulacji ciepła.
W takim systemie rury z tworzywa sztucznego (najczęściej PEX), którymi będzie krążyła woda grzewcza, układa się na zbrojeniu górnym (lub między siatkami zbrojeniowymi), wpuszczając je w beton konstrukcyjny. Typowy rozstaw rur to 10-20 cm. Układane są w pętlach, które następnie podłącza się do rozdzielaczy ciepła.
Kluczowym momentem podczas betonowania płyty grzewczej jest utrzymanie ciśnienia w rurach ogrzewania (ciśnienie próbne wodą lub powietrzem), co zapobiega ich zgnieceniu i pozwala od razu wykryć ewentualne nieszczelności. Rury muszą być też odpowiednio zamocowane do zbrojenia, aby nie przemieściły się w trakcie betonowania.
Płyta fundamentowa grzewcza działa jak wielki akumulator ciepła – nagrzewa się i oddaje ciepło do pomieszczenia przez długi czas, nawet po wyłączeniu źródła ciepła. Daje to stabilną temperaturę wewnątrz i jest idealnym rozwiązaniem w połączeniu z niskotemperaturowymi źródłami ciepła, takimi jak pompy ciepła.
Koszt instalacji samego ogrzewania podłogowego w płycie to orientacyjnie od 10 do 20 zł za metr kwadratowy (materiał – rury i złączki, bez rozdzielaczy i robocizny montażu rur przed betonowaniem). Ten koszt dodaje się do standardowego kosztu płyty, ale zyskujemy od razu gotową posadzkę z systemem grzewczym.
Innym elementem, który coraz częściej pojawia się w projektach, szczególnie w regionach o podwyższonym ryzyku występowania radonu, jest membrana przeciwradoowa. Radon to radioaktywny gaz szlachetny, który przenika z gruntu i może gromadzić się w budynkach, stanowiąc zagrożenie dla zdrowia.
Membrana przeciwradoowa to specjalna, gazoszczelna folia, którą układa się w warstwie izolacji przeciwwilgociowej (najczęściej na foliach PE). Musi być układana ze szczelnymi zakładami i sklejona dedykowanymi taśmami, a przejścia instalacyjne muszą być gazoszczelnie uszczelnione specjalnymi kołnierzami lub masami.
Stosowanie membrany przeciwradoowej jest standardem w wielu krajach i coraz częściej wymagane jest w Polsce w strefach o wyższej emisji radonu. Koszt takiej membrany to około 10-20 zł/m², w zależności od producenta i deklarowanej szczelności.
Dodatkowe elementy to także wszelkie przejścia instalacyjne przez płytę: kanalizacyjne, wodociągowe, elektryczne peszle, przepusty na rekuperację czy wentylację. Wszystkie te elementy muszą być zaplanowane i umieszczone w odpowiednich miejscach przed betonowaniem. Używa się do tego rur osłonowych (sleeves) lub specjalnych prefabrykowanych przejść, które szczelnie wbetonowuje się w płytę.
Wiecie co? Zaniedbanie umieszczenia nawet jednego peszla na kabel przed wylaniem betonu to prawdziwy koszmar – potem trzeba kuć twardy beton, co jest czasochłonne, kosztowne i osłabia płytę.
Często jako element "dodatkowy", choć w zasadzie niezbędny, traktuje się deskowanie zewnętrzne płyty. W przypadku płyt grzewczych czy energooszczędnych często stosuje się tzw. deskowanie tracone, wykonane z twardego styropianu lub XPS. Materiał ten zostaje na swoim miejscu po związaniu betonu, stanowiąc dodatkową izolację termiczną krawędzi płyty (tzw. izolacja opaskowa lub fasyjna). Koszt takiego rozwiązania jest wyższy niż tradycyjnego deskowania z drewna (które potem się usuwa), ale zapewnia lepsze parametry energetyczne na styku ściany zewnętrznej z fundamentem.
Czas realizacji budowy płyty fundamentowej z elementami dodatkowymi, takimi jak ogrzewanie podłogowe czy membrana radoochronna, jest nieco dłuższy niż w przypadku płyty standardowej. Układanie rur grzewczych czy membran przeciwradoowych wymaga czasu i pedantycznej precyzji. Może to dodać od 1 do 3 dni do standardowego czasu realizacji samej płyty.
Te "dodatki" mogą znacząco wpłynąć na ostateczny koszt `płyty fundamentowej`, podnosząc go nawet o kilkanaście czy kilkadziesiąt procent, w zależności od ich zakresu. Jednak są one często nieodzowne w przypadku projektów o podwyższonym standardzie energetycznym lub budowanych w miejscach ze specyficznymi wyzwaniami, jak np. podwyższony poziom radonu. Warto patrzeć na nie jak na inwestycję w komfort, zdrowie i przyszłe oszczędności eksploatacyjne budynku.