Płyta fundamentowa pod garaż drewniany: Kompletny przewodnik 2025
Decyzja o budowie garażu drewnianego to pierwszy krok, ale zaraz za nim pojawia się kluczowe pytanie: jaki fundament zapewni konstrukcji nie tylko trwałość, ale i stabilność na lata? Często rozważanym i zyskującym na popularności rozwiązaniem jest Płyta fundamentowa pod garaż drewniany. Jej prawidłowe wykonanie jest niezbędne, aby uniknąć problemów w przyszłości.
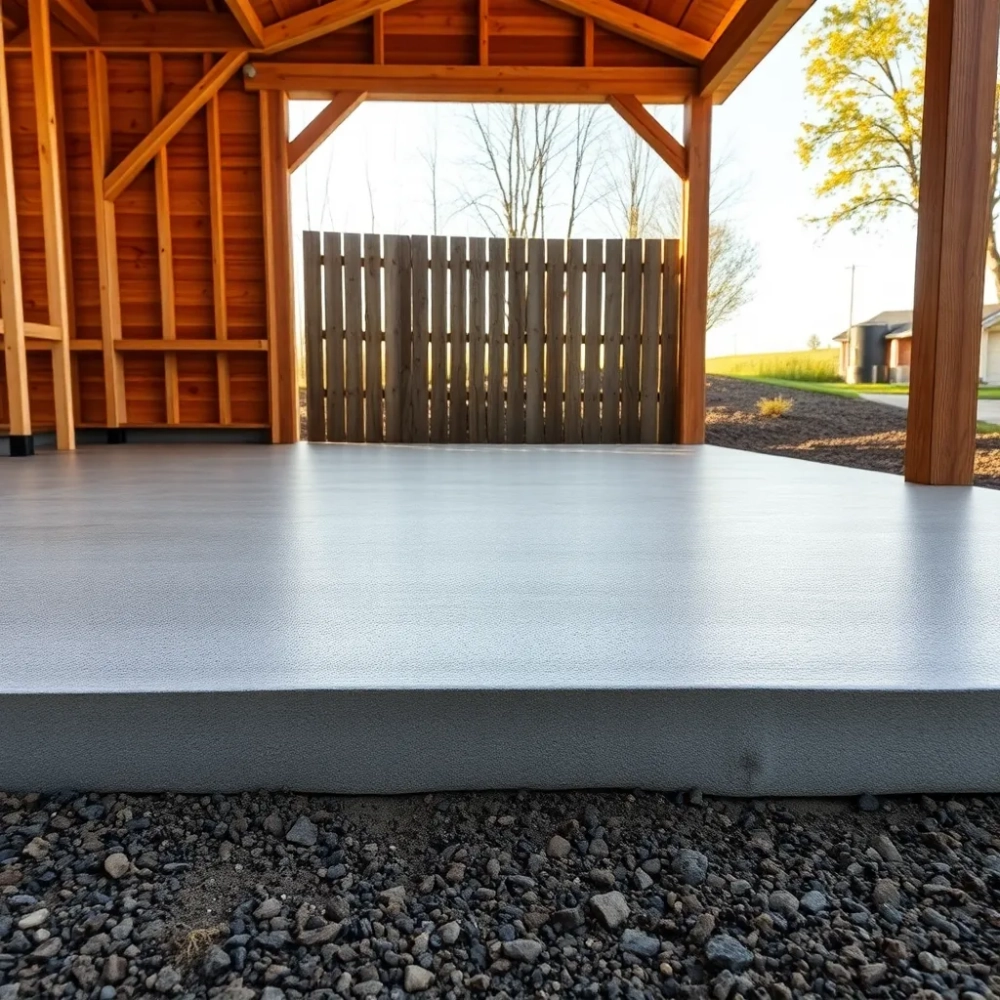
- Stabilność i nośność gruntu: decyduje o typie fundamentu.
- Obciążenie konstrukcji: drewniane garaże są lżejsze, ale wciąż wymagają solidnego wsparcia.
- Planowane użytkowanie: czy garaż będzie tylko schowkiem, czy warsztatem z ciężkimi narzędziami?
- Poziom wód gruntowych: wysoki poziom preferuje rozwiązania minimalizujące głębokie wykopy.
- Koszt całkowity projektu: płyta może być konkurencyjna cenowo dla mniejszych budynków.
Te elementy współgrają ze sobą, wpływając na ostateczną decyzję. Dla garaży drewnianych, często relatywnie lekkich, płyta fundamentowa pod garaż stanowi idealne rozwiązanie rozkładające ciężar na dużej powierzchni. Jest to szczególnie cenne w przypadku gruntów o niższej nośności, gdzie punktowe obciążenia od ław fundamentowych mogłyby prowadzić do nierównomiernego osiadania konstrukcji.
Odpowiednie zaprojektowanie i wykonanie płyty wymaga jednak szczegółowej wiedzy na temat specyfiki danego terenu i właściwości używanych materiałów. Zaniedbanie któregokolwiek z tych etapów może prowadzić do pęknięć, zawilgocenia, a w konsekwencji do uszkodzenia całej konstrukcji garażu. Dlatego tak ważne jest podejście metodyczne, krok po kroku, oparte na solidnych fundamentach wiedzy budowlanej.
Przygotowanie terenu i wymagania gruntowe pod płytę
Pierwszy rzut oka na pusty plac budowy pod przyszły garaż może nie mówić wiele, ale pod tą powierzchnią kryje się historia – historia gruntu, od której zależy powodzenie całego przedsięwzięcia. Pominięcie tego etapu to jak budowanie domu na ruchomych piaskach; prędzej czy później natura upomni się o swoje, pokazując nam nasz błąd w postaci rys na posadzce czy skrzypiących drzwi garażowych. Serio, nie lekceważcie matki ziemi!
Kluczowym etapem przygotowania terenu jest wykonanie badań geotechnicznych. No wiem, brzmi nudno, ale bez nich nie wiemy, z czym tak naprawdę mamy do czynienia pod powierzchnią. Geotechnik pobierze próbki gruntu z różnych głębokości i powie nam, czy mamy do czynienia z nośnym piaskiem, kapryśną gliną, torfem, czy może zmurszałą skałą. Każdy typ gruntu wymaga innego podejścia i to właśnie od tych informacji zależy projekt płyty fundamentowej i to, czy w ogóle płyta będzie najlepszym rozwiązaniem.
Przy gruntach spoistych, jak gliny i iły, problemem bywa zmienność objętości w zależności od nawodnienia. Potrafią pęcznieć, gdy są mokre i kurczyć się, gdy wysychają, co może prowadzić do niepożądanych ruchów fundamentu. Grunty luźne, jak piaski i żwiry, są z reguły stabilniejsze, ale ich nośność też ma granice, a przepuszczalność wpływa na kwestie odprowadzania wody opadowej.
Jeśli badania wykażą słabej jakości grunt, np. torf czy nasypy niekontrolowane, konieczne może być jego usunięcie i zastąpienie materiałem o lepszych parametrach, na przykład pospółką lub kruszywem stabilizowanym mechanicznie. Grubość takiej wymiany podłoża może wynosić od kilkudziesięciu centymetrów do nawet kilku metrów, w zależności od warunków. To generuje dodatkowe koszty, ale jest absolutnie niezbędne do zapewnienia stabilności solidna podstawa pod garaż.
Przygotowanie terenu to także zdjęcie warstwy humusu, czyli żyznej wierzchniej warstwy gleby. Humus jest nieprzepuszczalny i ściśliwy, dlatego musi zostać usunięty z całej powierzchni planowanej płyty i pasa wokół niej. Zazwyczaj wystarczy usunięcie 20-30 cm, ale zależy to od lokalnych warunków.
Po usunięciu humusu i ewentualnej wymianie gruntu, teren należy wyrównać i odpowiednio zagęścić. Zagęszczanie gruntu to kluczowy krok, który zapobiega jego późniejszemu osiadaniu pod ciężarem konstrukcji. Wykorzystuje się do tego zagęszczarki wibracyjne, a kontrolę stopnia zagęszczenia przeprowadza się np. poprzez badanie płytą dynamiczną. Parametr zagęszczenia powinien odpowiadać wymaganiom projektowym, często określany jest jako odpowiedni stopień Proctora lub wskaźnik zagęszczenia Is. Np. dla piasków wymagane zagęszczenie to często Is > 0.97.
Odpowiednie przygotowanie terenu obejmuje także ukształtowanie jego spadków. Powinny one umożliwiać odprowadzenie wody opadowej z powierzchni przyszłej płyty fundamentowej na zewnątrz, z dala od fundamentów. Zastoiny wody wokół płyty to prosta droga do problemów z wilgocią i potencjalnego przemarzania gruntu pod płytą.
Odwodnienie terenu może być również konieczne w przypadku wysokiego poziomu wód gruntowych. Może to polegać na wykonaniu drenażu opaskowego wokół płyty lub drenażu podłogowego pod całą powierzchnią fundamentu. Projekt odwodnienia musi uwzględniać specyfikę lokalizacji, rodzaj gruntu oraz docelowe miejsce odprowadzenia zebranej wody, np. do studni chłonnej, rowu melioracyjnego czy kanalizacji deszczowej (po uzyskaniu zgód).
Nie można zapomnieć o wytyczeniu obrysu przyszłej płyty. Odbywa się to przy użyciu sznurków i palików, bazując na osiach konstrukcyjnych budynku z projektu. Precyzyjne wytyczenie jest fundamentalne dla zachowania wymiarów i geometrii płyty, co z kolei wpływa na poprawne posadowienie na niej konstrukcji garażu. Błąd na tym etapie będzie później trudny do naprawienia.
Uśredniając koszty samych badań geotechnicznych, w zależności od lokalizacji i zakresu, mogą one wynieść od kilkuset do kilku tysięcy złotych. W przypadku konieczności wymiany gruntu, koszty robocizny i materiału (pospółki, kruszywa) mogą sięgać od 50 do 150 zł za metr sześcienny wymienionego gruntu, nie licząc kosztów wywozu gruntu rodzimego. Drenaż opaskowy to wydatek rzędu 50-100 zł/metr bieżący, w zależności od użytych materiałów i głębokości posadowienia.
Sumienność na etapie przygotowania gruntu procentuje przez lata. Zapewnia, że ciężar garażu zostanie równomiernie rozłożony, a fundament nie będzie narażony na szkodliwe działanie wody czy zmienność warunków gruntowych. To baza, bez której nawet najlepszy projekt i najdroższe materiały nie zagwarantują trwałości konstrukcji. Mówiąc prosto – nie ma co oszczędzać na solidnym przygotowaniu terenu.
Pamiętajmy, że dla garażu drewnianego, często o niewielkich rozmiarach (np. 6x5 m), waga konstrukcji będzie znacznie mniejsza niż w przypadku garażu murowanego czy domu jednorodzinnego. Pozwala to na pewne optymalizacje, ale podstawowe zasady fizyki i geotechniki pozostają niezmienne. Zawsze konsultujmy się ze specjalistą, jeśli mamy wątpliwości co do charakterystyki gruntu na naszej działce. To nie jest miejsce na "jakoś to będzie".
Projektowanie płyty fundamentowej i potrzebne materiały
Przejście od piaszczystego lub gliniastego wykopu do gładkiej, gotowej na przyjęcie ścian płyty fundamentowej to skok technologiczny wymagający precyzyjnego planowania. Tutaj nie ma miejsca na improwizację "na oko" czy "mniej więcej". Mówimy o projektowaniu konstrukcji, która przez dziesięciolecia będzie znosić obciążenia statyczne od garażu, zmienne obciążenia od śniegu i wiatru, a także siły wynikające z rozszerzalności cieplnej i pracy gruntu. Projektowanie płyty fundamentowej to zadanie dla inżyniera z uprawnieniami.
Projektant, na podstawie wyników badań geotechnicznych i planowanej wielkości oraz ciężaru garażu (który dla konstrukcji drewnianej o wymiarach np. 6x5 m, może ważyć kilka ton bez wyposażenia), określi kluczowe parametry płyty. Grubość płyty jest jednym z najważniejszych. Dla garażu drewnianego często wystarczająca okazuje się grubość od 15 do 25 cm, ale ostateczna decyzja zawsze zależy od obliczeń projektowych, uwzględniających nośność gruntu i obciążenia. Czasami, na gruntach o bardzo niskiej nośności, konieczne może być zastosowanie płyty grubszej lub z dodatkowymi żeberkami wzmacniającymi.
Inżynier dobierze także odpowiednie zbrojenie płyty. Standardowo stosuje się siatki z prętów stalowych układane w dwóch warstwach – dolnej i górnej. Średnica prętów i wielkość oczek siatki (np. pręty o średnicy 8, 10, 12 mm, siatka o oczku 15x15 cm lub 20x20 cm) zależą od wielkości i obciążeń płyty. Minimalne zbrojenie często wynosi φ8 co 15-20 cm. Naroża i krawędzie płyty mogą wymagać dodatkowego wzmocnienia. Zapomnijcie o jednej siatce ułożonej "gdzieś pośrodku" – zbrojenie musi być ułożone precyzyjnie, na odpowiednich podkładkach dystansowych zapewniających wymaganą otulinę betonową.
Oprócz zbrojenia konstrukcyjnego, projekt musi uwzględniać również inne warstwy wchodzące w skład konstrukcji płyty fundamentowej. Zazwyczaj pod betonem układa się warstwę chudego betonu (beton B7.5-B10) o grubości kilku centymetrów, która stanowi równe i czyste podłoże do dalszych prac, przede wszystkim do układania izolacji i zbrojenia. Koszt metra sześciennego betonu chudego to około 200-250 zł.
Niezbędne materiały budowlane na płytę fundamentową obejmują więc: kruszywo na warstwę podbudowy (jeśli konieczna wymiana gruntu), piasek, cement (jeśli beton jest mieszany na budowie, choć częściej stosuje się beton gotowy z betoniarni), pręty stalowe i/lub siatki zbrojeniowe, drut wiązałkowy do łączenia zbrojenia, podkładki dystansowe, szalunki (deski, płyty OSB, sklejka lub systemowe), folię budowlaną lub membranę do izolacji przeciwwilgociowej (koniecznie o dużej grubości, min. 0.3 mm, często nawet 0.5-1.0 mm, o wysokiej odporności na rozdarcie) oraz materiały izolacyjne (np. styrodur XPS lub płyty PIR) o odpowiedniej grubości.
Zużycie betonu na płytę fundamentową o wymiarach 6x5 m i grubości 20 cm wyniesie około 6 m³. Koszt betonu konstrukcyjnego klasy C20/25 (dawne B25) to około 350-450 zł/m³, co daje kwotę 2100-2700 zł za sam beton. Zużycie stali zbrojeniowej to zazwyczaj od 60 do 120 kg na metr sześcienny betonu, co dla 6 m³ betonu daje 360-720 kg stali. Przy cenie około 4-5 zł/kg, koszt zbrojenia wyniesie od 1440 do 3600 zł. Koszty szalunków, folii, dystansów i drutu wiązałkowego to kolejne kilkaset złotych. Do tego dochodzi cena styroduru XPS – dla tej samej powierzchni i izolacji o grubości 10 cm, potrzeba 30 m² materiału, co przy cenie ok. 40-60 zł/m² daje 1200-1800 zł.
Ważnym elementem projektu jest również zaplanowanie wszystkich przejść instalacyjnych (np. rury do rozprowadzenia instalacji elektrycznej, wody, kanalizacji, jeśli będą w garażu). Rury te muszą być osadzone w płycie przed betonowaniem, w odpowiednich otulinach (np. rury ochronne z PCV), aby beton ich nie uszkodził i aby była możliwość przyszłego przeciągnięcia przewodów. Dobry projekt to taki, który przewiduje wszystkie tego typu detale.
Projektant powinien również określić sposób pielęgnacji betonu po betonowaniu – jak długo i jak intensywnie należy go podlewać lub przykrywać, aby zapewnić mu odpowiednie warunki dojrzewania i uzyskać zakładaną wytrzymałość. Pielęgnacja betonu w pierwszych dniach po wylaniu jest absolutnie krytyczna dla jego końcowej jakości i trwałości wykonanie płyty fundamentowej.
Dokumentacja projektowa powinna zawierać rysunki wykonawcze z dokładnymi wymiarami, rzędnymi wysokościowymi, schematem zbrojenia z rozmieszczeniem i średnicami prętów, detalami konstrukcyjnymi oraz specyfikację techniczną, określającą wymagane parametry betonu (klasa wytrzymałości, klasa konsystencji, klasa ekspozycji) i stali zbrojeniowej. Warto też, aby zawierała wskazówki dotyczące izolacji przeciwwilgociowej i termicznej, a także metodyki prowadzenia robót.
Całkowity koszt materiałów na typową płytę fundamentową o powierzchni 30 m² (6x5m) bez uwzględnienia kosztu przygotowania terenu (humus, wymiana gruntu) i robocizny może wynieść od 5 000 do 10 000 zł, w zależności od grubości płyty, zbrojenia i izolacji. Zatrudnienie inżyniera do wykonania projektu to wydatek rzędu 500-1500 zł, co w skali całego przedsięwzięcia jest niewielką kwotą, a daje gwarancję poprawności technicznej i pozwala uniknąć kosztownych błędów na etapie realizacji. Bez dobrego projektu płycie fundamentowej pod garaż drewniany grożą poważne problemy.
Podsumowując, zaprojektowanie płyty fundamentowej to proces inżynierski, który wymaga wiedzy o gruncie, obciążeniach i materiałach budowlanych. Projekt musi być szczegółowy i obejmować wszystkie niezbędne elementy, od geometrii płyty po detale zbrojenia i izolacji. Inwestycja w dobry projekt zwróci się wielokrotnie w postaci trwałości i bezpieczeństwa garażu.
Etapy wykonania płyty fundamentowej krok po kroku
Pożądany efekt – idealnie gładka, równa i solidna płyta – nie bierze się znikąd. To suma kolejnych, precyzyjnie wykonanych kroków, niczym skomplikowany taniec budowlańców na placu boju z betonem i stalą. Pominięcie choćby jednego kroku albo wykonanie go niedbale, mści się później latami w postaci spękań, wilgoci czy osiadania. Przygotujcie się na rzetelną opowieść o tym, jak tchnąć życie w ten betonowy twór. Mówimy tu o etapy budowy fundamentu od A do Z.
Krok pierwszy, po badaniach geotechnicznych i zdjęciu humusu (o czym była mowa wcześniej), to ponowne dokładne wytyczenie obrysu płyty na przygotowanym gruncie. Służy do tego najczęściej sprzęt geodezyjny (niwelator, teodolit), który pozwala przenieść punkty i osie z projektu z dużą dokładnością. W narożnikach i wzdłuż boków wbija się paliki i rozciąga sznurki, wyznaczając zewnętrzne krawędzie przyszłego szalunku.
Następnie, na wyrównanym i zagęszczonym gruncie, układa się warstwę podbudowy, jeśli była wymagana wymiana gruntu, lub bezpośrednio na gruncie nośnym warstwę filtracyjną (np. z piasku lub pospółki o grubości kilkunastu cm), która zapobiegnie podciąganiu kapilarnemu wilgoci z gruntu do płyty. Warstwę tę należy również odpowiednio zagęścić mechanicznie. Pamiętajmy o nadaniu jej minimalnego spadku, jeśli projekt tego wymaga dla odwodnienia podposadzkowego.
Kolejny etap to ułożenie warstwy chudego betonu (tzw. chudziak) o grubości 5-10 cm. Po rozłożeniu, beton ten jest zacierany do równej powierzchni. Jego rola jest, jak już wspomniano, stworzenie czystej i stabilnej płaszczyzny pod dalsze prace. Chudziak po wylaniu wymaga pielęgnacji – lekkiego polewania wodą w upalne dni, aby nie popękał.
Na zastygniętym chudziaku układa się izolację przeciwwilgociową poziomą. Najczęściej jest to gruba folia budowlana (np. typu ATEST, grubość min. 0.3-0.5 mm) lub specjalistyczna membrana hydroizolacyjna. Arkusze folii powinny zachodzić na siebie na zakład co najmniej 15-20 cm i być sklejone specjalną taśmą. Izolacja musi być wywinięta do góry na krawędziach płyty i zabezpieczona, tworząc szczelną "wannę". Ma to fundamentalne znaczenie dla ochrony garażu przed wilgocią z gruntu. To izolacja przeciwwilgociowa płyty na najwyższym poziomie.
Jeżeli projekt przewiduje izolację termiczną pod płytą, to teraz jest moment na jej ułożenie. Stosuje się do tego płyty z twardego polistyrenu ekstrudowanego (XPS) lub płyty PIR, odporne na nacisk i wilgoć. Grubość izolacji pod płytą to często od 10 do 20 cm, w zależności od wymagań termicznych i specyfiki projektu. Płyty izolacyjne układa się szczelnie, na mijankę, aby zminimalizować mostki termiczne.
Teraz nadchodzi czas na montaż szalunków, czyli formy, która nada płycie ostateczny kształt i wymiary. Szalunki mogą być wykonane z desek drewnianych, płyt OSB lub sklejki, ale najwygodniejsze w użyciu są systemowe szalunki z tworzywa sztucznego. Szalunki ustawia się wzdłuż wyznaczonych wcześniej linii i stabilizuje za pomocą pionowych stempli i poziomych rozporów, tak aby beton napierający na ściany szalunku nie odkształcił ich. Górna krawędź szalunku wyznacza docelowy poziom górnej powierzchni płyty.
Wewnątrz szalunku układa się zbrojenie, zgodnie ze schematem z projektu. Pręty i siatki zbrojeniowe układa się na specjalnych podkładkach dystansowych (tzw. żabki lub denka z tworzywa sztucznego), które zapewniają wymaganą otulinę betonową – czyli odległość stali od krawędzi betonu. Dla płyty fundamentowej wynosi ona zazwyczaj 3-5 cm od spodu i 3 cm od góry. Dolne i górne zbrojenie musi być połączone strzemionami lub prętami dystansowymi, aby zachować stałą odległość między siatkami podczas betonowania. Całe zbrojenie wiąże się drutem wiązałkowym. Montaż zbrojenia musi być bardzo staranny – źle ułożona stal nie spełni swojej funkcji konstrukcyjnej.
Po ułożeniu zbrojenia i ewentualnym zamontowaniu przejść instalacyjnych (rur, peszli), następuje kluczowy moment – betonowanie płyty. Beton zamówiony z betoniarni (klasy minimum C20/25) jest transportowany betonomieszarką i wylewany do szalunku. Warto upewnić się, że beton ma odpowiednią konsystencję (klasa S3-S4), aby łatwo rozpływał się wokół zbrojenia. Świeży beton musi być zagęszczony wibratorem pogrążalnym lub listwą wibracyjną. Zagęszczanie eliminuje puste przestrzenie i pęcherze powietrza, zwiększając wytrzymałość betonu. Górną powierzchnię betonu ściąga się łatą, wyrównując do poziomu szalunku, a następnie zaciera, uzyskując gładką powierzchnię, gotową na ułożenie posadzki garażowej.
Bezpośrednio po betonowaniu, zwłaszcza w cieplejsze dni, należy rozpocząć pielęgnację betonu. Polega ona na regularnym polewaniu powierzchni wodą (co najmniej przez 3-7 dni) lub przykryciu płyty folią lub matami słomianymi, aby zapobiec zbyt szybkiemu odparowywaniu wody, które mogłoby prowadzić do skurczu i powstawania rys. Pełną wytrzymałość beton uzyskuje po 28 dniach, ale obciążenie konstrukcyjne garażu można rozpocząć zazwyczaj po 7-14 dniach, w zależności od warunków atmosferycznych i klasy betonu.
Demontaż szalunków można przeprowadzić po 2-3 dniach, gdy beton uzyska wstępną wytrzymałość, która pozwoli na utrzymanie kształtu krawędzi płyty. Po zdjęciu szalunków, krawędzie płyty można zabezpieczyć np. preparatem bitumicznym.
Koszt robocizny za wykonanie płyty fundamentowej pod garaż drewniany jest bardzo zróżnicowany i zależy od regionu, wielkości ekipy i stopnia skomplikowania terenu. Można się spodziewać wydatku rzędu 100-250 zł/m². Dla płyty 30 m² daje to kwotę 3000-7500 zł za samą robociznę, bez materiałów i badań. Łączny koszt materiałów i robocizny dla płyty 30 m² bez specyficznych problemów z gruntem może wynieść od 8 000 do 17 000 zł.
Proces wykonania płyty wymaga dokładności, cierpliwości i przestrzegania reżimu technologicznego. Każdy etap ma swoje znaczenie, a pominięcie lub niedociągnięcie w jednym, wpływa na jakość całości. Studzimy zapał do pośpiechu – lepiej poczekać jeden dzień dłużej, niż spieszyć się i żałować latami. Solidnie wykonana płyta to fundament spokoju na długie lata użytkowania garażu.
Prawidłowa izolacja przeciwwilgociowa i termiczna płyty
Moglibyśmy wylać beton, ułożyć zbrojenie i uznać, że fundament gotowy, prawda? Otóż nie! To byłby jakoby deser bez głównego dania, lub co gorsza, obiad, który zatruje nam życie. Prawidłowa izolacja płyty fundamentowej pod garaż drewniany to nie opcja, to konieczność. Drewno, jak wiemy, nie lubi wilgoci, a wilgotna posadzka w garażu to przepis na grzyba, pleśń, przyspieszone niszczenie konstrukcji drewnianej i nieprzyjemny zapach. Ochrona przed wilgocią i chłodem to klucz do zdrowego i trwałego garażu.
Zacznijmy od izolacja przeciwwilgociowa płyty. Jej głównym zadaniem jest odcięcie betonu płyty fundamentowej od wilgoci pochodzącej z gruntu. Nawet na dobrze przepuszczalnym gruncie i przy niskim poziomie wód gruntowych, zjawisko podciągania kapilarnego jest realnym zagrożeniem. Woda z gruntu może unosić się w porach materiałów budowlanych (np. betonu) na wysokość nawet kilkudziesięciu centymetrów! Standardowo stosuje się do tego celu grubą folię polietylenową lub specjalistyczne membrany bitumiczne lub PVC.
Jak już wspomniano w poprzednim rozdziale, izolację poziomą układamy zazwyczaj na warstwie chudego betonu. Grubość folii powinna wynosić minimum 0.3-0.5 mm, a najlepiej więcej (np. 0.8-1.0 mm dla pewności). Folia musi być ułożona na całej powierzchni płyty i koniecznie wywinięta na boki na wysokość górnej krawędzi płyty. Zakłady folii, wynoszące minimum 15-20 cm, muszą być starannie sklejone specjalistyczną taśmą klejącą do folii, tworząc szczelną "nieckę". Wszelkie przejścia instalacyjne (rury, peszle) muszą być dodatkowo uszczelnione za pomocą opasek lub specjalnych mankietów samoprzylepnych wokół rur, zapobiegając przedostawaniu się wody w tych miejscach.
Dlaczego tak ważne są te zakłady i szczelne sklejenie? Nawet najmniejsza nieszczelność pozwoli wilgoci wedrzeć się pod płytę, skąd będzie mogła powoli migrować w górę, powodując zawilgocenie betonu. A wilgotny beton nie jest dobrym sąsiadem dla konstrukcji drewnianej. W skrajnych przypadkach może to prowadzić do zagrzybienia podłogi i dolnych partii ścian garażu.
Oprócz izolacji poziomej pod płytą, warto rozważyć także izolację pionową krawędzi płyty. Po zdjęciu szalunków, zewnętrzną powierzchnię pionową krawędzi płyty można zabezpieczyć masą bitumiczną lub gruntem asfaltowym. Chroni to beton na krawędzi przed bezpośrednim kontaktem z wilgotnym gruntem zewnętrznym i stanowi dodatkową barierę przeciwwilgociową. To prosty krok, który znacząco poprawia trwałość krawędzi fundamentu.
Przejdźmy teraz do izolacja termiczna fundamentu. Czy garaż drewniany, często traktowany jako budynek nieogrzewany, wymaga izolacji termicznej fundamentu? To zależy od przeznaczenia i specyfiki projektu. Jeśli garaż ma służyć jedynie jako schowek na samochód czy narzędzia, gdzie temperatura zimą może spadać poniżej zera, pełna izolacja termiczna pod płytą nie jest krytycznie niezbędna, choć i tak warto ją rozważyć dla komfortu. Jeśli jednak planujemy wykorzystywać garaż jako warsztat, w którym będziemy spędzać czas, lub jeśli jest on połączony z budynkiem mieszkalnym, izolacja termiczna staje się bardzo ważna.
Izolacja termiczna pod płytą minimalizuje straty ciepła przez posadzkę do gruntu. Pozwala to na utrzymanie wyższej temperatury wewnątrz garażu przy mniejszym nakładzie energii (jeśli garaż jest ogrzewany) oraz ogranicza zjawisko przemarzania gruntu pod płytą, które w przypadku gruntów wysadzinowych może prowadzić do podnoszenia i pękania płyty. Stosuje się do niej, jak już wspomniano, materiały odporne na wilgoć i ściskanie, takie jak polistyren ekstrudowany XPS lub płyty PIR. Grubość izolacji zależy od wymagań termoizolacyjnych – dla garażu może to być od 5 do 15 cm, dla budynków mieszkalnych zazwyczaj więcej (np. 15-20 cm).
Płyty izolacyjne XPS lub PIR układamy na warstwie chudziaka lub hydroizolacji, dbając o szczelne połączenie krawędzi. Mogą być układane w jednej lub dwóch warstwach "na mijankę", aby uniknąć mostków termicznych na styku płyt. Pamiętajmy, że izolacja termiczna, jeśli jest układana pod całą płytą, musi mieć wystarczającą wytrzymałość na ściskanie, aby przenosić obciążenia od płyty i konstrukcji na grunt.
W przypadku braku pełnej izolacji termicznej pod płytą, bezwzględnie konieczne jest zastosowanie izolacji termicznej obwodowej, czyli ocieplenie pionowych krawędzi płyty do głębokości strefy przemarzania gruntu lub co najmniej 50-60 cm poniżej poziomu terenu. Izolacja obwodowa z płyt XPS (o grubości np. 5-10 cm) chroni krawędź płyty przed wychłodzeniem i zmniejsza ryzyko wysadzania mrozowego gruntu pod krawędziami, co mogłoby skutkować pęknięciami w płycie. Izolację tę mocuje się do krawędzi płyty i obsypuje gruntem. Górna część izolacji powinna być wyprowadzona powyżej poziomu terenu (ok. 20-30 cm) i zabezpieczona np. siatką i tynkiem.
Koszt materiałów izolacyjnych jest znaczący. Folia hydroizolacyjna o grubości 0.5 mm to wydatek rzędu 5-10 zł/m². Specjalistyczne membrany mogą być droższe. Styrodur XPS o grubości 10 cm to, jak już wspomniano, około 40-60 zł/m². Dla płyty 30 m² pełna izolacja termiczna (30 m²) może kosztować 1200-1800 zł, a obwodowa (powiedzmy 22 mb krawędzi x 0.6m głębokości x 5cm grubości, daje to ok. 0.66 m³ materiału, co przelicza się na koszt ok. 300-500 zł) to mniejszy wydatek, ale nadal istotny element całości.
Pamiętajmy, że wilgoć i chłód to główni wrogowie konstrukcji drewnianych. Dobrze wykonana prawidłowa izolacja fundamentów to inwestycja w długowieczność naszego garażu, minimalizująca ryzyko drogich remontów w przyszłości. Nikt chyba nie chce, żeby po kilku latach deski zaczęły gnić od spodu, prawda? Lepiej dmuchać na zimne, czyli izolować, niż potem naprawiać.
Analizując koszty typowych materiałów dla płyty fundamentowej 6x5m (30 m²) o grubości 20 cm, bez kosztów przygotowania terenu (po zdjęciu humusu) i robocizny, możemy przyjąć następujący przykładowy zestaw:
Materiał | Ilość jednostek | Jednostka miary | Cena jednostkowa (przybliżona) | Koszt całkowity |
---|---|---|---|---|
Chudy beton (C8/10) | 3.0 | m³ | 220 zł/m³ | 660 zł |
Beton konstrukcyjny (C20/25) | 6.0 | m³ | 400 zł/m³ | 2400 zł |
Stal zbrojeniowa (np. fi10 co 15cm, 2 siatki) | 500 | kg | 4.50 zł/kg | 2250 zł |
Podkładki dystansowe + drut wiązałkowy | 1 | kpl | 150 zł/kpl | 150 zł |
Folia izolacyjna (0.5 mm) | 40 | m² | 7 zł/m² | 280 zł |
Taśma do folii | 2 | rolki | 25 zł/rolka | 50 zł |
Izolacja termiczna (XPS 10 cm pod całością) | 30 | m² | 50 zł/m² | 1500 zł |
Szalunki (wynajem lub materiał na stracone/deski) | 1 | kpl | 500 zł/kpl | 500 zł |
ORIENTACYJNY KOSZT MATERIAŁÓW | 7790 zł |
Powyższa tabela przedstawia jedynie szacunkowe koszty samych materiałów, zakładając stosunkowo proste warunki gruntowe i standardowe materiały na płytę. W rzeczywistości mogą się one różnić w zależności od cen rynkowych, regionu, specyfikacji projektu (np. większa grubość płyty, gęstsze zbrojenie, inna grubość izolacji) oraz tego, czy wykorzystujemy systemowe szalunki na wynajem, czy własne deski. Zazwyczaj koszt robocizny stanowi znaczący udział w całkowitym koszcie wykonania płyty, często dorównując kosztom materiałów lub je przewyższając.
Zilustrować rozkład orientacyjnych kosztów budowy takiej płyty (przygotowanie terenu, materiały, robocizna) może prosty wykres, pokazujący proporcje wydatków. Pamiętajcie, że to tylko przykład, a w realnym projekcie każda składowa może ulec zmianie, często drastycznie, jeśli napotkamy niespodziewane problemy, np. z gruntem.