EPS pod płytę fundamentową w 2025 roku: Rodzaje, parametry i zastosowanie
Gdy stajemy przed wyzwaniem budowy własnego domu, myśli biegną do widocznych elementów: ścian, dachu, okien. Rzadziej zastanawiamy się nad tym, co kryje się tuż pod stopami, a to właśnie podstawa jest absolutnie kluczowa. Wybór odpowiedniej izolacji termicznej pod płytę fundamentową to nie tylko techniczna decyzja, to inwestycja w komfort i ekonomię na lata. W praktyce EPS pod płytę fundamentową stanowi jedno z najpopularniejszych i często najbardziej efektywnych rozwiązań, oferując niezawodną barierę przed chłodem gruntu.
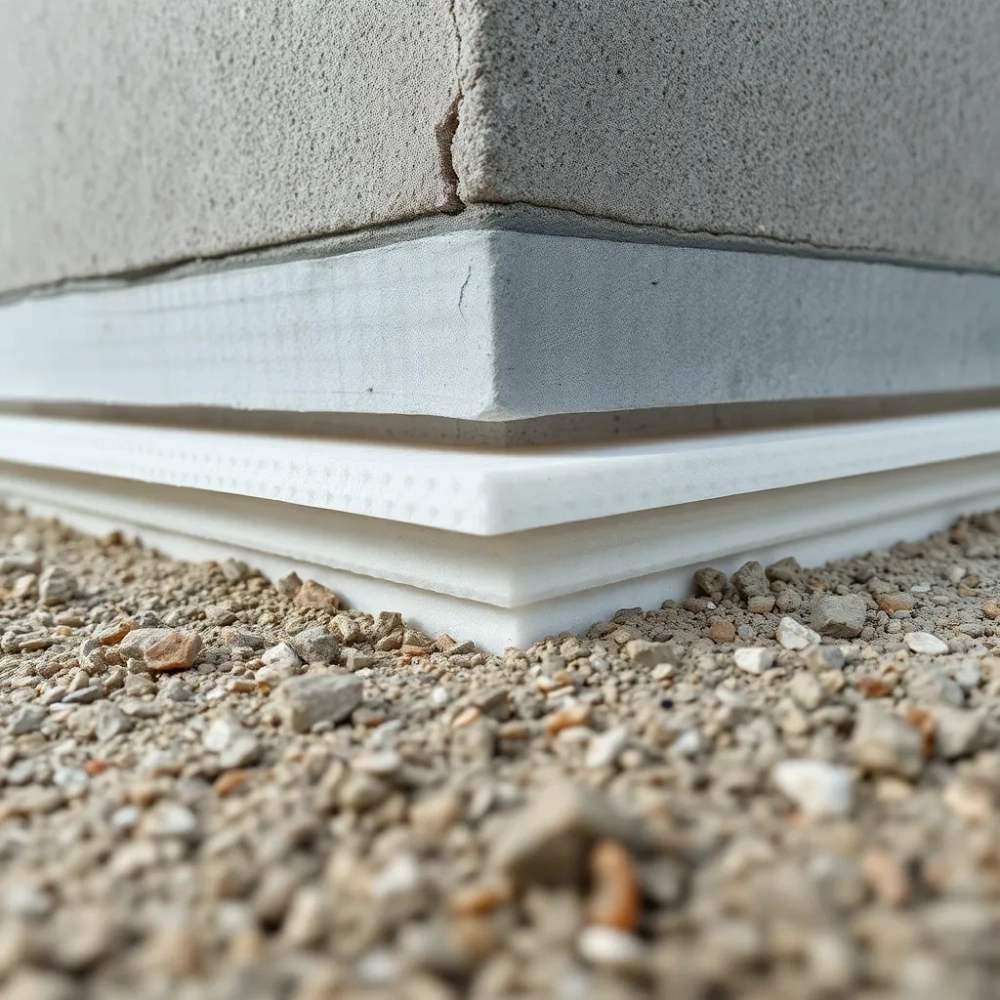
Analizując dane z różnorodnych badań i testów porównawczych dotyczących materiałów izolacyjnych stosowanych pod płyty fundamentowe, można wyciągnąć kilka kluczowych wniosków. Spójrzmy na zestawienie podstawowych parametrów dwóch głównych graczy na tym rynku:
Parametr | EPS (polistyren ekspandowany) | XPS (polistyren ekstrudowany) |
---|---|---|
Typowa wytrzymałość na ściskanie (przy 10% odkształceniu, kPa) | CS(10)100 do CS(10)200 (100-200 kPa) | CS(10)300 do CS(10)700 (300-700 kPa) |
Średni współczynnik przewodzenia ciepła λ (W/mK) | 0.036 - 0.040 | 0.030 - 0.035 |
Absorpcja wody (długoterminowa dyfuzja, WL(T)) | Typowo WL(T)3 do WL(T)5 (< 3% do < 5%) | Typowo WL(T)0.7 (< 0.7%) |
Struktura komórkowa | Zamknięta, ale z przestrzeniami między kulkami | Praktycznie w 100% zamknięta |
Orientacyjny Koszt (Wskaźnik, EPS100 = 1.0) | 1.0 (EPS100) - 1.5 (EPS200) | 1.8 - 2.5 (XPS300) |
Co te liczby tak naprawdę oznaczają dla kogoś, kto buduje dom? Oznaczają przede wszystkim odpowiedź na pytanie o trwałość, efektywność energetyczną i ostatecznie – o koszty inwestycji. Wytrzymałość na ściskanie determinuje, czy materiał wytrzyma ciężar budynku bez znaczącego odkształcenia przez dekady. Współczynnik lambda mówi nam wprost, jak dobrze materiał izoluje – im niższa wartość, tym mniejsza ucieczka ciepła. Absorpcja wody zaś to wskaźnik odporności na wilgoć gruntową, która jest wrogiem numer jeden izolacji termicznej, ponieważ woda przewodząc ciepło niweluje jej działanie. Te kluczowe parametry decydują o tym, który materiał jest odpowiedni w danej sytuacji i ile go potrzebujemy, aby osiągnąć zamierzony cel izolacyjny.
Parametry i właściwości styropianu pod płytą fundamentową
Kiedy mówimy o styropianie, czy też poprawniej polistyrenie ekspandowanym (EPS), który ma znaleźć się pod olbrzymią, ciężką płytą fundamentową, nie mówimy o byle jakim "zwykłym" styropianie używanym do ocieplenia fasady czy podłogi na piętrze. Tu w grę wchodzą specyficzne, podwyższone wymagania, które musi spełnić materiał pracujący w ekstremalnych warunkach: pod ogromnym obciążeniem, w środowisku potencjalnie wilgotnym i narażonym na zmienne temperatury gruntu.
Pierwszym i absolutnie kluczowym parametrem jest wytrzymałość na ściskanie, określana normą PN-EN 13163 symbolem CS(10)XX, gdzie XX to minimalna wartość naprężenia ściskającego w kPa, przy którym materiał ulegnie 10% odkształceniu. Dla płyt fundamentowych stosuje się styropian o parametrach CS(10)100 (czyli wytrzymałość 100 kPa) lub CS(10)150, CS(10)200. Co to oznacza w praktyce? 100 kPa to równowartość około 10 ton nacisku na metr kwadratowy. Wyobraźcie sobie średniej wielkości samochód osobowy – 100 kPa to nacisk wywierany przez dziesięć takich samochodów stojących na powierzchni jednego metra kwadratowego izolacji. Wasz dom waży znacznie więcej, ale jego ciężar rozkłada się na znacznie większej powierzchni płyty fundamentowej, dlatego odpowiednie dobranie klasy CS(10) jest fundamentem trwałości całej konstrukcji.
Kolejnym vitalnym aspektem jest nasiąkliwość, czyli odporność materiału na wchłanianie wody. Woda w gruncie jest wszechobecna, zwłaszcza w trudnych warunkach gruntowo-wodnych. Standardowe płyty EPS stosowane pod fundament powinny charakteryzować się niską nasiąkliwością, określaną w normach jako WL(T) – nasiąkliwość wodą przy długotrwałym zanurzeniu. Dla dobrego styropianu fundamentowego wartość ta nie powinna przekraczać WL(T)3 lub WL(T)5, co oznacza, że po długim czasie zanurzenia wchłonie mniej niż 3% lub 5% wody objętościowo. Niska nasiąkliwość jest krytyczna, ponieważ woda w porach materiału nie tylko pogarsza jego właściwości termoizolacyjne (woda przewodzi ciepło znacznie lepiej niż powietrze), ale też, zamarzając, może fizycznie uszkodzić strukturę materiału.
Odporność na przemarzanie, choć ściśle powiązana z nasiąkliwością, zasługuje na osobne podkreślenie. Materiał znajdujący się poniżej poziomu gruntu zero, nawet w dobrze izolowanym budynku, jest narażony na ujemne temperatury panujące w gruncie w okresie zimowym. Styropian o niskiej nasiąkliwości minimalizuje ryzyko uszkodzeń wynikających z cyklicznego zamarzania i rozmarzania wody w jego strukturze. Zatem wysoka nasiąkliwość = niska mrozoodporność. To prosta, brutalna zasada.
Współczynnik przewodzenia ciepła lambda (λ) to esencja izolacyjności termicznej. Im niższa wartość λ wyrażona w W/mK, tym lepiej materiał izoluje. Dobry styropian fundamentowy z reguły ma lambdę na poziomie 0.036 - 0.038 W/mK. Dla porównania, nieizolowany grunt ma lambdę rzędu 1.5 - 2.0 W/mK. Widzicie różnicę? Stosując warstwę 20-30 cm styropianu, obniżamy przenikalność cieplną podłogi na gruncie (współczynnik U) do wartości znacznie poniżej 0.2 W/m²K, spełniając z nawiązką aktualne, rygorystyczne przepisy budowlane dotyczące energooszczędności.
Ostatni, ale nie mniej ważny aspekt to bioodporność. Styropian, jako materiał syntetyczny, jest zasadniczo odporny na ataki pleśni, grzybów i mikroorganizmów obecnych w gruncie. Jest też nieatrakcyjny dla gryzoni jako źródło pożywienia, choć same tunele mogą przez niego przebiegać. Ta właściwość zapewnia, że izolacja zachowa swoje parametry przez długi czas eksploatacji, nie ulegając biodegradacji w wilgotnym środowisku gruntowym.
Podsumowując parametry: wybierając styropian pod płytę fundamentową, szukajmy przede wszystkim wysokiej wytrzymałości na ściskanie (minimum CS(10)100, a najlepiej wyżej dla cięższych budynków), bardzo niskiej nasiąkliwości (WL(T)3 lub lepiej), niskiego współczynnika lambda (ok. 0.036 W/mK) i potwierdzonej bioodporności. Tylko taki materiał sprosta specyficznym wymaganiom fundamentu i będzie skutecznie izolował przez cały cykl życia budynku, często znacznie dłużej niż myślimy, mówiąc o "latach" – tu mówimy o dekadach.
EPS100 vs XPS300: Który wybrać pod płytę fundamentową?
Dyskusja na temat wyboru między EPS100 a XPS300 pod płytą fundamentową przypomina nieco debatę między wyborem solidnego samochodu terenowego a potężną ciężarówką – oba są mocne, ale zaprojektowane do nieco innych zadań i warunków. Zrozumienie różnic między tymi dwoma popularnymi materiałami jest kluczowe, by podjąć trafną decyzję, która posłuży nam przez dziesięciolecia bez przykrych niespodzianek.
Podstawową różnicą, jak sugerują oznaczenia, jest wspomniana już wytrzymałość na ściskanie. EPS100 oznacza, że styropian ma minimalną wytrzymałość na ściskanie 100 kPa przy 10% odkształceniu. XPS300, polistyren ekstrudowany, chwali się wartością 300 kPa przy tym samym odkształceniu. To trzy razy więcej! Co to znaczy w kontekście płyty fundamentowej? Płyta fundamentowa rozkłada ciężar budynku na całej swojej powierzchni. Lekki dom szkieletowy lub parterowy dom murowany bez ciężkich stropów międzykondygnacyjnych wywiera na izolację znacznie mniejszy nacisk niż kilkupiętrowa kamienica czy nawet dom jednorodzinny z pełnym poddaszem użytkowym i masywnymi ścianami murowanymi na wszystkich kondygnacjach.
Dla lżejszych konstrukcji, gdzie obciążenie na metr kwadratowy fundamentu mieści się komfortowo w granicach kilkudziesięciu kPa, zastosowanie EPS100 jest w pełni uzasadnione technicznie i ekonomicznie. Nie ma sensu przewymiarowywać izolacji w zakresie wytrzymałości, jeśli 100 kPa jest wystarczające z solidnym zapasem bezpieczeństwa. Inwestor oszczędza, a materiał spełnia swoją rolę.
Jednak w przypadku budynków cięższych, na przykład z betonowymi stropami prefabrykowanymi lub monolitycznymi, z grubymi ścianami murowanymi, albo w sytuacji, gdy mamy do czynienia z lokalnymi, punktowymi większymi obciążeniami (np. słupy konstrukcyjne wspierające duże rozpiętości), 100 kPa może okazać się niewystarczające w dłuższej perspektywie. Co prawda statycy i konstruktorzy projektując płytę uwzględniają rozkład obciążeń, ale odkształcenie izolacji o 10% pod wpływem obciążenia może prowadzić do niekorzystnych naprężeń w płycie betonowej, a w skrajnych przypadkach do jej pęknięć. W takich sytuacjach XPS300, oferujący trzykrotnie wyższą wytrzymałość, jest po prostu wyborem rozsądnym, zapewniającym niezbędny margines bezpieczeństwa.
Różnica w strukturze materiału również odgrywa rolę. XPS ma bardziej jednorodną, zamkniętokomórkową strukturę dzięki procesowi ekstruzji, co skutkuje z reguły niższą nasiąkliwością (WL(T) typowo poniżej 1%) oraz nieco lepszym współczynnikiem lambda w porównaniu do EPS o podobnej gęstości. Ta niższa nasiąkliwość sprawia, że XPS bywa preferowany w warunkach bardzo wysokiego poziomu wód gruntowych lub słabo zdrenowanych gruntów, gdzie ryzyko długotrwałego kontaktu z wodą jest wysokie.
Ale co z kosztem? To jest często decydujący czynnik. Styropian EPS pod płytę fundamentową w klasie 100 kPa jest zazwyczaj znacznie tańszy niż XPS300, często nawet dwukrotnie lub więcej na metr kwadratowy przy tej samej grubości. Różnica w cenie maleje, gdy porównujemy EPS o wyższej wytrzymałości (np. EPS150, EPS200), które cenowo zbliżają się do XPS, ale wciąż z reguły są tańsze.
Decyzja między EPS100 a XPS300 nie jest więc kaprysem, a świadomym wyborem opartym na analizie obciążeń budynku, warunków gruntowo-wodnych na działce oraz, oczywiście, budżetu inwestycji. Dla standardowego domu jednorodzinnego na stabilnym gruncie, EPS100 o odpowiedniej grubości zazwyczaj w zupełności wystarczy, zapewniając i izolację, i niezbędną nośność. Dla cięższych konstrukcji, zwłaszcza na trudniejszych gruntach, dopłata do XPS300 to często koszt warty poniesienia dla spokoju ducha i długoterminowej stabilności fundamentu. A wiecie, stabilny fundament to podstawa całego sukcesu. To jak wybór dobrych butów do biegania maratonu – niby każde coś tam izolują, ale tylko odpowiednie pozwolą dotrzeć do celu bez kontuzji.
Pamiętajmy też, że grubość izolacji ma olbrzymi wpływ na końcowy efekt izolacyjności. Czasem lepiej jest zainwestować w grubszą warstwę EPS100 (np. 30 cm) niż w cieńszą warstwę XPS300 (np. 15 cm) za podobną cenę, jeśli obciążenia na to pozwalają i warunki gruntowe nie są ekstremalne. Kluczem jest zawsze projektant, który oceni obciążenia i warunki, rekomendując optymalne rozwiązanie materiałowe i grubość izolacji.
Dostępne na rynku wymiary standardowych płyt EPS pod fundament to zazwyczaj 1000x500 mm, dostępne w grubościach od 50 mm nawet do 250-300 mm w pojedynczych panelach. Często układa się je dwu- lub trójwarstwowo na mijankę, aby zredukować mostki termiczne na stykach płyt. Ceny mogą się wahać w zależności od producenta, regionu i grubości, ale orientacyjnie metr sześcienny styropianu EPS100 może kosztować w granicach 250-350 PLN, podczas gdy metr sześcienny XPS300 to już koszt 500-700 PLN i więcej. Przeliczając to na metr kwadratowy izolacji o grubości 20 cm, mówimy o różnicy rzędu kilkudziesięciu złotych na metrze kwadratowym, co przy płycie 100-metrowego domu daje już kilka tysięcy złotych oszczędności lub dodatkowego wydatku. Ważne jest, by ta decyzja nie była podyktowana wyłącznie ceną, ale rzetelną analizą potrzeb konstrukcyjnych i izolacyjnych. Możemy jednak śmiało stwierdzić, że dla większości typowych domów jednorodzinnych, EPS pod płytę fundamentową o klasie CS(10)100, ułożony w odpowiedniej grubości, stanowi optymalne połączenie ceny i parametrów, zapewniając wysoki komfort cieplny i niezbędną trwałość.
Zastosowanie EPS pod płytami fundamentowymi dla różnych typów budynków
Gdy przyglądamy się różnorodności współczesnego budownictwa, szybko staje się jasne, że uniwersalne podejście do wyboru materiałów izolacyjnych pod płytę fundamentową jest po prostu niemożliwe. Od leciutkich konstrukcji drewnianych, które stają się coraz popularniejsze, przez klasyczne domy murowane, aż po masywne budynki wielopiętrowe czy hale przemysłowe – każde z tych typów budynków charakteryzuje się zupełnie inną wagą i, co za tym idzie, innymi wymaganiami dotyczącymi wytrzymałości podłoża, w tym warstwy termoizolacji.
Zacznijmy od budynków "lekkich". Mówimy tutaj przede wszystkim o domach szkieletowych, zarówno drewnianych, jak i stalowych, oraz o niewielkich, parterowych budynkach murowanych z lekkimi dachami i bez ciężkich stropów monolitycznych. Waga takiej konstrukcji, rozłożona na dużej powierzchni płyty fundamentowej, generuje relatywnie niewielkie obciążenie jednostkowe na podłożu. W takich przypadkach EPS pod płytę fundamentową o klasie wytrzymałości na ściskanie CS(10)100, co odpowiada 100 kPa, jest z reguły w pełni wystarczający. Dlaczego? Ponieważ rzeczywiste obciążenia występujące pod płytą w typowym domu szkieletowym rzadko przekraczają kilkadziesiąt kPa. Nawet z zapasem, 100 kPa jest wartością, która gwarantuje, że izolacja nie ulegnie trwałemu odkształceniu przekraczającemu 10% przez cały okres eksploatacji, a często i dłużej. W tym segmencie budownictwa, EPS100 stanowi złoty środek między niezbędnymi parametrami a kosztami, co jest nie bez znaczenia przy budowie o ograniczonym budżecie.
Sytuacja zmienia się diametralnie w przypadku budynków "ciężkich". Do tej kategorii zaliczamy domy piętrowe z ciężkimi stropami (np. żelbetowymi), budynki wielokondygnacyjne murowane, a także obiekty użyteczności publicznej czy niewielkie hale, gdzie na płycie mogą dodatkowo pojawiać się znaczne obciążenia użytkowe (np. składowany towar, ciężkie maszyny). W takich przypadkach obciążenia na fundament mogą znacznie przekroczyć próg 100 kPa, zwłaszcza w obszarach pod ścianami nośnymi, słupami konstrukcyjnymi czy w narożnikach. Stosowanie EPS100 w takich warunkach byłoby ryzykownym błędem, mogącym prowadzić do stopniowego osiadania płyty w miejscach o najwyższym nacisku i, w konsekwencji, do uszkodzenia samej konstrukcji budynku. Właśnie tutaj królują materiały o wyższej wytrzymałości na ściskanie, takie jak EPS150, EPS200, a najczęściej XPS300 (lub wyższe klasy XPS jak 500 czy 700 dla bardzo dużych obciążeń). XPS300, z wytrzymałością 300 kPa, oferuje trzykrotnie większy zapas nośności w stosunku do EPS100, co w zupełności wystarcza dla większości cięższych domów jednorodzinnych i mniejszych obiektów niemieszkalnych. To jak porównanie kładzenia delikatnej kostki brukowej na ścieżce ogrodowej (gdzie EPS100 to jakby stabilizowany piasek pod spodem) z budową autostrady, która wymaga podbudowy z kruszyw zdolnych przenieść gigantyczne obciążenia (gdzie XPS reprezentuje ten wyższy poziom nośności).
Co ciekawe, nawet w przypadku lżejszych budynków, niektórzy projektanci decydują się na zastosowanie XPS300 przynajmniej w obszarach najbardziej obciążonych lub wokół krawędzi płyty, łącząc go z EPS100 w mniej krytycznych strefach. Taki hybrydowy system pozwala optymalnie wykorzystać zalety obu materiałów – wyższą wytrzymałość XPS tam, gdzie jest naprawdę potrzebna, i korzystniejszą cenę EPS tam, gdzie wystarczają jego parametry. Jednak z punktu widzenia wykonawczego jest to bardziej skomplikowane i wymaga precyzyjnego planowania i montażu.
Grubość izolacji to kolejny aspekt związany z typem budynku. Standardowe domy jednorodzinne wymagają zazwyczaj warstwy izolacji EPS lub XPS o grubości 20-30 cm, aby spełnić obecne standardy energetyczne dla podłogi na gruncie (U < 0.2 W/m²K). Jednak w przypadku budynków pasywnych lub niskoenergetycznych, gdzie dąży się do minimalizacji wszelkich strat ciepła, grubość ta może wzrosnąć do 30-40 cm, a nawet więcej. Niezależnie od grubości, zasada wyboru materiału ze względu na wytrzymałość pozostaje taka sama – decyduje o niej przede wszystkim ciężar budynku.
Analizując potrzeby izolacyjne dla konkretnego typu budynku, zawsze należy kierować się projektem budowlanym opracowanym przez uprawnionego projektanta. To on na podstawie obliczeń statycznych, charakterystyki gruntu i wymagań termoizolacyjnych, wskaże odpowiedni materiał izolacyjny (EPS lub XPS), jego klasę wytrzymałości i wymaganą grubość. Stosowanie EPS pod płytę fundamentową o niewystarczającej wytrzymałości, nawet jeśli parametry termoizolacyjne by się zgadzały dla danej grubości, jest po prostu proszeniem się o kłopoty konstrukcyjne. Podobnie, stosowanie przewymiarowanego XPS tam, gdzie w zupełności wystarczyłby EPS100, generuje niepotrzebne koszty, choć z technicznego punktu widzenia błędem nie jest.
Montaż i układ warstw izolacji EPS pod płytą fundamentową
Choć wybór odpowiedniego materiału izolacyjnego, jakim jest EPS pod płytę fundamentową, oraz jego parametrów i grubości to połowa sukcesu, druga połowa, równie krytyczna, to jego prawidłowy montaż. Nawet najlepszy materiał, jeśli zostanie źle ułożony, nie spełni swojej funkcji, a my, jako inwestorzy, stracimy pieniądze i będziemy mierzyć się z problemami przez lata. Proces budowy płyty fundamentowej z izolacją termiczną jest wieloetapowy i wymaga precyzji na każdym kroku, przypominając układanie warstw pysznego ciasta – każda ma swoją rolę i musi znaleźć się na właściwym miejscu we właściwym czasie.
Zaczynamy od przygotowania terenu. Po zdjęciu warstwy humusu i wyrównaniu podłoża, kluczowym etapem jest wykonanie tzw. podbudowy z kruszywa. Zazwyczaj stosuje się do tego celu żwir lub kruszywo łamane o frakcji np. 0/31.5 mm. Warstwa ta ma kluczowe znaczenie dla drenażu i rozłożenia ciężaru, a także jako warstwa kapilarnie przerywająca podciąganie wody z gruntu. Standardowa grubość takiej podbudowy to 20-30 cm, ale może być większa w zależności od projektu i warunków gruntowych. Niezwykle ważne jest solidne zagęszczenie tej warstwy przy użyciu mechanicznych zagęszczarek, do momentu uzyskania wymaganego w projekcie wskaźnika zagęszczenia. Słabe zagęszczenie podbudowy to jeden z częstszych błędów, który w przyszłości może skutkować osiadaniem całej płyty. To trochę jak budowanie zamku z piasku na mokrym piasku – nawet najładniejszy zamek i tak się zapadnie.
Na tak przygotowaną i zagęszczoną podbudowę wysypuje się warstwę piasku wyrównawczego o grubości zazwyczaj 5-10 cm. Jego rola polega na stworzeniu idealnie płaskiej powierzchni, na której układana będzie kolejna warstwa. Wyrównanie piasku za pomocą listew i poziomicy jest absolutnie kluczowe – wszelkie nierówności przełożą się na warstwę izolacji, a następnie na naprężenia w płycie betonowej. Gładkie podłoże dla izolacji to podstawa, żeby płyty styropianu lub XPS leżały równo i nie miały punktowych naprężeń.
Następnie na warstwie piasku układana jest izolacja przeciwwilgociowa. Najczęściej jest to gruba folia polietylenowa (PE) o grubości co najmniej 0.3-0.5 mm. Jej zadaniem jest zapobieganie podciąganiu kapilarnemu wilgoci z gruntu do warstwy termoizolacji i samej płyty betonowej. Folię układa się z dużymi zakładami (min. 15-20 cm), które starannie skleja się taśmą odporną na wilgoć. Szczególną uwagę należy zwrócić na uszczelnienie folii wokół wszelkich przejść instalacyjnych (rury wod-kan, przepusty elektryczne), które muszą być poprowadzone przez płytę. Nieszczelna folia to ukryty mostek wilgotnościowy, który może negatywnie wpływać na właściwości izolacyjne przez lata.
Dopiero na tak przygotowanej, szczelnej warstwie przeciwwilgociowej układana jest izolacja termiczna – EPS pod płytę fundamentową lub XPS, w zależności od projektu. Płyty układa się zazwyczaj w dwóch lub więcej warstwach "na mijankę", tzn. tak, aby spoiny płyt w jednej warstwie nie pokrywały się ze spoinami w warstwie sąsiedniej. Minimalizuje to ryzyko powstania mostków termicznych na stykach płyt. Grubość pojedynczych płyt EPS do zastosowań fundamentowych to najczęściej 100, 150 lub 200 mm, co pozwala łatwo uzyskać wymaganą w projekcie łączną grubość np. 200, 250 lub 300 mm, układając odpowiednią liczbę warstw. Płyty powinny być ciasno spasowane, a wszelkie szczeliny wokół instalacji czy przy krawędziach starannie wypełnione pianką poliuretanową niskoprężną.
Montaż płyt termoizolacyjnych wymaga dokładności i ostrożności. Chodzenie po ułożonej izolacji powinno być ograniczone do minimum, a w razie potrzeby używać się desek rozkładających ciężar. Krawędzie izolacji są równie ważne – często stosuje się specjalne kształtki EPS/XPS w kształcie litery "L" lub po prostu pionowe paski materiału wzdłuż obwodu płyty, aby zaizolować krawędź płyty, która stykać się będzie bezpośrednio z gruntem po wyjęciu deskowania. Niedostateczne zaizolowanie krawędzi to potężny mostek termiczny, który może zniweczyć wysiłek włożony w izolację całej powierzchni.
Po ułożeniu i zabezpieczeniu warstwy termoizolacji przechodzi się do zbrojenia płyty. Na izolacji układane są odpowiednie przekładki lub krzesełka dystansowe, na których następnie umieszczane są siatki zbrojeniowe lub pręty stalowe według rysunków konstrukcyjnych. Ważne, aby zbrojenie było prawidłowo zdystansowane od warstwy izolacji. Na koniec układa się deskowanie wokół obwodu płyty, a następnie przystępuje do betonowania.
Samo betonowanie również wymaga uwagi, aby nie uszkodzić ułożonej izolacji, zwłaszcza przy zrzucaniu betonu z dużej wysokości. Płynna masa betonowa łatwo wlewa się w wszelkie szczeliny, tworząc zimne mostki, dlatego precyzyjne ułożenie folii przeciwwilgociowej i dokładne spasowanie płyt izolacyjnych jest tak istotne. Po wylaniu betonu i jego zagęszczeniu, powierzchnia płyty jest często zacierana mechanicznie na gładko, co pozwala na bezpośrednie układanie posadzki wewnątrz budynku bez konieczności wykonywania dodatkowych wylewek wyrównujących. To spory plus płyt fundamentowych.
Pamiętajmy, że każdy etap montażu izolacji termicznej pod płytą fundamentową jest istotny. Odpowiednie przygotowanie podbudowy, precyzyjne ułożenie folii, staranne spasowanie płyt styropianu pod płytą fundamentową czy XPS, zabezpieczenie krawędzi – wszystkie te czynności składają się na trwałość i skuteczność izolacji termicznej na dziesięciolecia. Zaniedbanie któregokolwiek z tych elementów może prowadzić do kosztownych problemów w przyszłości. Warto więc dopilnować, aby ekipa wykonawcza przykładała należytą wagę do każdego z tych kroków. Z naszego doświadczenia wynika, że inwestycja w solidne wykonanie tej warstwy zwraca się stokrotnie w niższych rachunkach za ogrzewanie i braku problemów z wilgocią.
Poniżej prosty przykład wizualizacji wpływu grubości izolacji na U-value podłogi na gruncie (przy stałej lambdzie EPS 0.036 W/mK, zgodnie z normą PN-EN ISO 13370 dla płyty grzewczej).
Jak widać na wykresie, zwiększenie grubości izolacji termicznej ma bezpośrednie przełożenie na obniżenie współczynnika przenikalności cieplnej U. Przejście z 10 cm na 20 cm niemal dwukrotnie poprawia izolacyjność, a dalsze zwiększanie grubości przynosi kolejne, choć już nieco mniejsze, zyski. Dlatego projektowana grubość izolacji termicznej pod płytą fundamentową jest tak samo ważna jak wybór samego materiału, czy to EPS, czy XPS. Nie chodzi tylko o spełnienie minimalnych przepisów, ale o realny komfort i niższe koszty ogrzewania przez lata.