Płyta fundamentowa do samodzielnego montażu - kompletny przewodnik 2025
Zastanawiasz się nad budową domu, ale wizja tradycyjnych ław fundamentowych spędza Ci sen z powiek? Co powiesz na coś rewolucyjnego i zaskakująco dostępnego? Płyta fundamentowa do samodzielnego montażu to innowacyjne rozwiązanie, które pozwala wykonać solidny fundament dla Twojego budynku nawet bez zatrudniania wyspecjalizowanej ekipy. Brzmi jak marzenie, prawda? Warto przyjrzeć się tej opcji bliżej, by zrozumieć jej potencjał i dowiedzieć się, jak działa w praktyce.
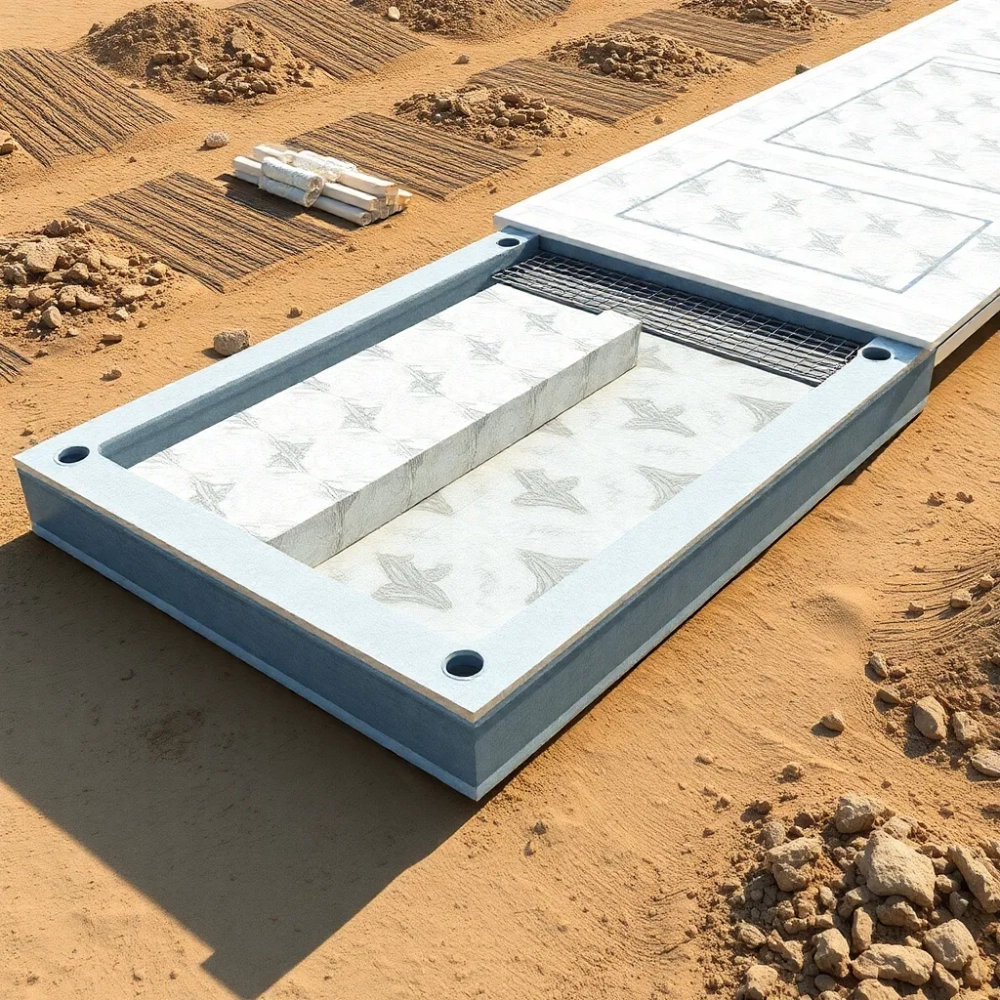
Analizując rynek nowoczesnych rozwiązań fundamentowych, zauważamy wyraźny trend w kierunku systemów prefabrykowanych. Choć brakuje scentralizowanej, ogólnej metaanalizy obejmującej wszystkie dostępne produkty i ich wdrożenia w skali makro, zbiory danych od dostawców i niezależne testy rynkowe rysują pewien obraz. Zestawiając ze sobą informacje o popularności, deklarowanych parametrach termoizolacyjnych oraz logistyce dostaw, można wyciągnąć ciekawe wnioski.
Typ Płyty (Izolacja) | Przewodność cieplna (λ) [W/(mK)] | Typowa grubość izolacji [cm] | Orientacyjna cena netto za m² (materiał) [PLN] | Minimalny czas przygotowania gruntu [dni] |
---|---|---|---|---|
EPS 150 | 0.036 - 0.038 | 20-30 | 180 - 250 | 3-5 |
EPS 200 | 0.034 - 0.036 | 20-30 | 200 - 280 | 3-5 |
XPS | 0.032 - 0.034 | 20-30 | 250 - 350 | 3-5 |
Powyższe zestawienie ilustruje, że choć warianty izolacyjne różnią się parametrami termicznymi i kosztem, generalna specyfika przygotowania podłoża czy zakres typowych grubości izolacji pozostają podobne. W praktyce oznacza to, że wybór konkretnego typu materiału izolacyjnego – czy to EPS o różnej gęstości, czy też XPS – wpłynie głównie na finalne parametry energetyczne fundamentu oraz bezpośredni koszt zakupu samego materiału termoizolacyjnego stanowiącego rdzeń płyty. Jest to kluczowe dla projektu termomodernizacyjnego budynku.
Dane te pokazują jasno, że postawienie na rozwiązanie systemowe, nawet jeśli mówimy o montażu w systemie DIY, wiąże się z konkretnymi parametrami fizycznymi i kosztami. Aspekty takie jak współczynnik przewodności cieplnej (lambda) izolacji fundamentu bezpośrednio przekładają się na energooszczędność przyszłego budynku. Zrozumienie tych różnic pozwala na świadomy wybór produktu optymalnie dopasowanego do wymagań projektowych i oczekiwań co do przyszłych kosztów ogrzewania czy chłodzenia. Wykres poniżej może przybliżyć relacje kosztów materiału izolacyjnego w zależności od jego typu, co jest często pierwszym krokiem w budżetowaniu tego typu inwestycji.
Płyta fundamentowa DIY - zalety i wady rozwiązania
Rozwiązania budowlane rozwijają się w zaskakującym tempie, a jednym z najbardziej intrygujących trendów jest możliwość samodzielnego wykonania fundamentu w postaci płyty. Tradycyjne ławy fundamentowe, wymagające głębokich wykopów i zazwyczaj sporych ekip budowlanych, powoli ustępują miejsca systemom, które obiecywują uproszczenie procesu. Zaletą numer jeden jest tu niewątpliwie potencjalna oszczędność. Eliminacja kosztów pracy wyspecjalizowanej firmy wykonawczej może stanowić znaczący ubytek w budżecie całej inwestycji, często rzędu kilkudziesięciu procent kosztu fundamentu.
Kolejną kluczową zaletą jest aspekt termoizolacyjny. Płyty fundamentowe, zwłaszcza te systemowe przeznaczone do DIY, są projektowane jako fundamenty izolowane. Oznacza to, że warstwa izolacji termicznej, często wykonana ze styropianu EPS o wysokiej gęstości lub XPS, stanowi integralną część fundamentu już na etapie wylewania betonu. To znacznie poprawia bilans energetyczny budynku. Minimalizuje to mostki termiczne w miejscu połączenia fundamentu ze ścianami nośnymi parteru, co jest częstym problemem przy tradycyjnych rozwiązaniach.
Systemy montaż płyty fundamentowej DIY charakteryzują się także często szybszym czasem realizacji w porównaniu do tradycyjnych fundamentów. Ograniczenie zakresu prac ziemnych – najczęściej do usunięcia wierzchniej warstwy humusu i wyrównania terenu – znacząco przyspiesza pierwszy etap budowy. Dodatkowo, prefabrykowane elementy, takie jak szalunki styropianowe czy kosze zbrojeniowe dostarczane w zestawie, ułatwiają i przyspieszają pracę na placu budowy. Czas to pieniądz, a krótszy czas budowy oznacza szybsze przejście do kolejnych etapów i potencjalnie niższe koszty finansowania projektu.
Jednak, jak to zwykle bywa w życiu, medal ma dwie strony. Samodzielny montaż, choć atrakcyjny cenowo, wymaga od inwestora pewnej wiedzy technicznej i precyzji. Pomyłki na etapie układania izolacji, montażu zbrojenia czy betonowania mogą mieć poważne konsekwencje dla trwałości i stabilności całego budynku. "Panie, niby proste, ale jak się coś sknoci na starcie, to potem płacz i zgrzytanie zębów" – takie głosy słychać czasem na forach budowlanych i trzeba się z nimi liczyć.
Wada może być również kwestia dostępu do specjalistycznego sprzętu. O ile podstawowe narzędzia budowlane są powszechnie dostępne, o tyle transport i rozładunek ciężkich elementów betonowych (choć w systemach DIY mowa głównie o betonie dostarczanym gruszką), zagęszczarka wibracyjna do gruntu czy pompa do betonu to już elementy, które trzeba wynająć. Koszt wynajmu tego typu maszyn, choć rozłożony na krótki czas, może być znaczący i trzeba go uwzględnić w kalkulacji. Nie mówiąc już o odpowiedzialności, która spoczywa na barkach samodzielnego wykonawcy.
Szczególnej uwagi wymaga odpowiednie przygotowanie podłoża pod płytę. Musi być ono idealnie równe, odpowiednio zagęszczone i pozbawione wszelkiej materii organicznej czy elementów niewłaściwie przepuszczalnych. Niewłaściwie przygotowane podłoże może skutkować osiadaniem płyty w przyszłości, a to już jest poważny problem konstrukcyjny. Zapewnienie odpowiedniego spadku terenu wokół przyszłej płyty fundamentowej w celu odprowadzenia wód opadowych również wymaga przemyślenia i starannego wykonania. "A co jak ziemia siądzie po zimie?" – słuszne pytanie, które zadaje wielu DIY-owców. Dlatego przygotowanie podbudowy jest absolutnie kluczowe.
Zimne realia logistyki także potrafią być wyzwaniem. Transport dużych elementów izolacyjnych, worków cementu, piasku, czy dostawa betonu na mały plac budowy w ograniczonej zabudowie może nastręczać trudności. Potrzeba miejsca na składowanie materiałów, sprawna komunikacja z dostawcami i często koordynacja dostaw w bardzo krótkim czasie (np. w przypadku betonu towarowego) wymaga niezłej organizacji i umiejętności planowania. To nie jest praca dla kogoś, kto działa impulsywnie i "na czuja". Precyzyjny plan działania to podstawa sukcesu.
Analizując koszty, warto pamiętać, że choć cena samego materiału systemu płytowego może wydawać się wyższa niż tradycyjnych materiałów na ławy, należy spojrzeć na całość. Całościowy koszt wykonania ław, łącznie z kopaniem, szalowaniem, zbrojeniem, betonowaniem i późniejszym ocieplaniem (które jest osobnym etapem), może okazać się wyższy lub porównywalny. System DIY eliminuje pewne etapy i integruje izolację od razu, co w ogólnym rozrachunku, przy sprawnym montażu, może przynieść oszczędność, szczególnie w przypadku budynków energooszczędnych, gdzie wymagana jest wysoka jakość izolacji termicznej od poziomu gruntu. Myśląc o kosztach, zawsze patrzymy na TCO (Total Cost of Ownership), nie tylko na cenę materiału.
W przypadku rozwiązań system płyt fundamentowych, producent dostarcza często kompletny zestaw elementów wraz ze szczegółową instrukcją montażu. To niewątpliwie ułatwienie. Dostęp do gotowych kształtek izolacyjnych, często z precyzyjnie wyciętymi kanałami na instalacje poziome, upraszcza proces i minimalizuje ryzyko błędów wykonawczych związanych z cięciem materiału na placu budowy. Gotowe schematy zbrojenia oraz systemy szalunkowe zintegrowane z izolacją sprawiają, że nie trzeba "cudować" i wymyślać koła na nowo, co jest kuszące dla osób bez doświadczenia. W zasadzie postępuje się według "książki kucharskiej", którą dostarczył producent systemu.
Wielu producentów oferuje wsparcie techniczne dla osób decydujących się na płytę fundamentową do samodzielnego montażu. Konsultacje telefoniczne, dostęp do dokumentacji technicznej, a nawet wizyty na placu budowy (choć często dodatkowo płatne) mogą pomóc rozwiać wątpliwości i uniknąć poważnych pomyłek. To element, który zdecydowanie wpływa na zwiększenie szans powodzenia projektu DIY. W końcu nikt nie jest omnibus, a popełnienie kosztownego błędu na tak wczesnym etapie budowy jest czymś, czego każdy chciałby uniknąć jak ognia. Dostęp do wiedzy eksperckiej jest tu na wagę złota.
Podsumowując (choć w tym rozdziale nie miałem tego robić ;)), główne zalety to potencjalna oszczędność na robociźnie, zintegrowana izolacja termiczna i szybszy czas realizacji. Wady to konieczność posiadania wiedzy technicznej, odpowiedzialność, potrzeba wynajmu sprzętu i wymagająca logistyka. Czy warto? To zależy od umiejętności, zasobów i odwagi inwestora. Zawsze należy zrobić solidne rozeznanie. Powiedzieć, że jest to proste jak bułka z masłem, byłoby nadużyciem, ale jest to na pewno opcja warta rozważenia dla osób z zacięciem do majsterkowania i odpowiednią determinacją.
Decyzja o wyborze fundamentu z płyty bez udziału ekipy powinna być poprzedzona rzetelną analizą własnych możliwości i lokalnych warunków gruntowych. Choć technologia systemów płytowych do samodzielnego montażu upraszcza wiele aspektów, nie zastąpi to podstawowego zrozumienia zasad budowlanych i szacunku dla procesów fizycznych. Warto też poszukać opinii innych DIY-owców, którzy mają za sobą podobne doświadczenia. Internet pełen jest historii z placów budowy, zarówno tych z happy endem, jak i tych mniej optymistycznych. Uczenie się na cudzych błędach jest mądrzejsze niż popełnianie własnych.
Dodatkowo, niektóre systemy płyt fundamentowych oferują warianty z wbudowanymi kanałami na instalację ogrzewania podłogowego wodnego lub elektrycznego. To rozwiązanie typu "wszystko w jednym", które integruje kolejny etap prac budowlanych z wykonaniem fundamentu. Takie podejście dodatkowo skraca czas realizacji całego projektu i upraszcza koordynację prac. Koszt takiego rozwiązania jest naturalnie wyższy, ale zysk w postaci zredukowania liczby ekip i skrócenia harmonogramu może być nieoceniony. Wyobraź sobie, że fundament i ogrzewanie na parterze masz zrobione za jednym zamachem!
Etapy samodzielnego montażu płyty fundamentowej krok po kroku
Decyzja zapadła – montaż płyty fundamentowej DIY stanie się Twoim udziałem. Gratulacje! To odważny krok. Aby przedsięwzięcie zakończyło się sukcesem, kluczowe jest ścisłe przestrzeganie określonej procedury. Budowa fundamentu to nie improwizacja, to symfonia precyzyjnych działań. Pominięcie nawet jednego etapu może zagrażać stabilności konstrukcji i trwałości całego budynku. Zatem, do dzieła! Oto typowa sekwencja kroków, którą należy przejść.
Pierwszy i absolutnie fundamentalny krok to usunięcie humusu, czyli wierzchniej, urodzajnej warstwy gleby. Zawiera ona dużo materii organicznej i jest podatna na zmiany objętości pod wpływem wilgoci i mrozu, co jest wrogiem każdego stabilnego fundamentu. Grubość usuwanej warstwy zależy od specyfiki gruntu na działce, ale zazwyczaj wynosi od 20 do 50 cm. Upewnij się, że usuwasz ją dokładnie na całej powierzchni przyszłej płyty fundamentowej oraz nieco poza jej obrys, pozostawiając co najmniej metrowy pas roboczy. Bez solidnej, stabilnej bazy nic nie zbudujesz trwale. "Fundamenty to podstawa, dosłownie i w przenośni" – mówią starzy budowlańcy.
Następnie należy przygotować podbudowę z kruszywa. Najczęściej stosuje się żwir lub kruszywo łamane o uziarnieniu 0/31.5 lub 0/63 mm. Warstwa kruszywa pełni funkcję drenażową i stabilizującą. Powinna być ułożona na odpowiednią grubość, zgodną z projektem (często 20-40 cm), a co najważniejsze, musi być bardzo starannie zagęszczona. Do tego celu niezbędna jest zagęszczarka wibracyjna o odpowiedniej mocy. Kruszywo układa się warstwami (np. po 10-15 cm), a każdą warstwę intensywnie zagęszcza. Nie ma drogi na skróty – tylko perfekcyjnie zagęszczone kruszywo zapewni odpowiednią nośność. Sprawdzenie zagęszczenia za pomocą sondy lub płyty dynamicznej jest wysoce zalecane.
Po wykonaniu i zagęszczeniu podbudowy z kruszywa, konieczne jest wyrównanie jej powierzchni i ułożenie warstwy wyrównawczej. Może to być chudy beton (np. B10) lub zagęszczony piasek stabilizowany cementem (tzw. podsypka cementowo-piaskowa). Grubość tej warstwy to zazwyczaj kilka centymetrów (3-10 cm). Jej celem jest stworzenie równej i stabilnej płaszczyzny do ułożenia izolacji termicznej i przeciwwilgociowej. Nawet najlepiej zagęszczone kruszywo nie da idealnie gładkiej powierzchni, a gładka baza jest kluczowa dla prawidłowego ułożenia paneli izolacyjnych bez mostków termicznych. Pomyśl o tym jak o podkładzie pod idealny makijaż – musi być gładki.
Kolejny krytyczny etap to wykonanie izolacji przeciwwilgociowej poziomej. Na wyrównanej warstwie układa się folię hydroizolacyjną o odpowiedniej grubości i wytrzymałości (zwykle co najmniej dwie warstwy folii budowlanej 0.5 mm lub jedna warstwa dedykowanej folii EPDM/PVC). Folia musi być układana ze znacznym zakładem (min. 15-20 cm), a połączenia muszą być starannie uszczelnione, np. taśmą klejącą przeznaczoną do folii hydroizolacyjnych. Izolacja ta zapobiega kapilarnemu podciąganiu wilgoci z gruntu do konstrukcji płyty i ścian budynku. Przeciekająca folia to gwarantowany problem w przyszłości – wilgoć to cichy zabójca konstrukcji.
Teraz czas na układanie izolacji termicznej. W przypadku systemów płyty fundamentowej do samodzielnego montażu, jest to zazwyczaj warstwa lub kilka warstw płyt ze styropianu EPS o wysokiej gęstości (np. EPS 150, EPS 200) lub z polistyrenu ekstrudowanego (XPS). Płyty układa się ciasno, z minimalnymi szczelinami, najlepiej na "mijankę" w dwóch warstwach, aby wyeliminować mostki termiczne na łączeniach. Specjalne kształtki na krawędzie płyty tworzą zintegrowany szalunek tracony, który również jest częścią izolacji termicznej krawędzi. Staranność na tym etapie decyduje o skuteczności izolacji całego fundamentu. Jak to mówią, "diabeł tkwi w szczegółach", a w tym przypadku w szczelinach między płytami.
Po ułożeniu izolacji, przychodzi moment na montaż zbrojenia. Zbrojenie płyty fundamentowej wykonuje się zazwyczaj z prętów stalowych połączonych w siatki lub dostarczanych w postaci gotowych koszy zbrojeniowych, zwłaszcza w systemach DIY. Zbrojenie musi być ułożone na dystansach (plastikowych lub betonowych "grzybkach"), aby zapewnić mu odpowiednią otulinę betonową, zarówno od dołu, jak i od góry. Minimalna otulina wynosi zwykle 3-5 cm. Rodzaj i średnica prętów, a także rozstaw siatek, są ściśle określone w projekcie konstrukcyjnym płyty i tych wytycznych nie wolno modyfikować samowolnie. Stal ma tu konkretne zadanie: przenosić siły rozciągające i zapobiegać pękaniu betonu. Bez odpowiedniego zbrojenia płyta nie spełni swojej funkcji nośnej.
Na tym etapie często montuje się również przejścia instalacyjne przez płytę. Dotyczy to przede wszystkim rur kanalizacyjnych, doprowadzenia wody, elektryczności czy gazu. Przejścia te muszą być uszczelnione, a rury zabezpieczone w odpowiednich tulejach ochronnych przed uszkodzeniem podczas betonowania. Niezwykle ważne jest precyzyjne zaplanowanie i wykonanie tych przejść przed wylaniem betonu, ponieważ po jego związaniu jakakolwiek korekta staje się ogromnym problemem lub jest wręcz niemożliwa. "Co miało być pod płytą, musi być tam PRZED płytą" – ta zasada jest prosta i brutalna zarazem.
Ostatni kluczowy etap to betonowanie. Beton towarowy dostarczany jest na plac budowy betonomieszarką (popularnie zwaną "gruszką"). Typ betonu (klasa wytrzymałości, konsystencja) jest określony w projekcie. Beton wylewa się na przygotowane zbrojenie, starając się rozprowadzać go równomiernie po całej powierzchni. Konieczne jest wibrowanie betonu w celu usunięcia pęcherzy powietrza i dokładnego wypełnienia przestrzeni wokół zbrojenia i izolacji. Do wibrowania używa się wibratorów wgłębnych (buławowych) lub listw wibracyjnych. Brak wibracji to słaby, porowaty beton i zbrojenie, które nie jest odpowiednio otulone – proszenie się o kłopoty. Poziomowanie powierzchni wykonuje się za pomocą łat i zacieraczek, dążąc do uzyskania idealnie równej i gładkiej powierzchni, która będzie podłogą na parterze.
Po betonowaniu, płyta wymaga odpowiedniej pielęgnacji, czyli zapewnienia jej optymalnych warunków do wiązania i twardnienia. Przez pierwsze dni, zwłaszcza w ciepłe i wietrzne dni, beton należy regularnie polewać wodą lub przykrywać folią budowlaną, aby zapobiec zbyt szybkiemu odparowaniu wody. Proces wiązania betonu trwa kilka tygodni, ale wstępną wytrzymałość osiąga po kilku dniach (zazwyczaj po 7 dniach osiąga około 70% docelowej wytrzymałości). Nie wolno dopuścić do przedwczesnego wyschnięcia lub przemarznięcia świeżego betonu. Cierpliwość jest tu cnotą. "Beton lubi wilgoć, a nie słońce i wiatr" – to jedna z podstawowych zasad pielęgnacji.
Samodzielny montaż płyty fundamentowej to proces wymagający zaangażowania, precyzji i zrozumienia podstawowych zasad sztuki budowlanej. Każdy z powyższych etapów ma kluczowe znaczenie dla finalnego efektu i trwałości Twojego przyszłego domu. Choć można go zrealizować samemu, nie oznacza to, że jest to łatwa bułka z masłem. "Trzeba wiedzieć co i jak, i co najważniejsze – DLACZEGO tak" – mówił kiedyś pewien doświadczony majster, a miał rację. Podejście z pokorą do procesu i dokładne studiowanie instrukcji oraz projektu to najlepsza strategia.
Rodzaje płyt fundamentowych do samodzielnego montażu - wybór materiału
Decydując się na fundament z płyty bez udziału ekipy, stajesz przed koniecznością wyboru konkretnego typu rozwiązania dostępnego na rynku. Nie jest to opcja "one-size-fits-all". Producenci oferują różne warianty, które różnią się między sobą przede wszystkim materiałem zastosowanym do izolacji termicznej oraz obecnością dodatkowych elementów wzmacniających. Zrozumienie tych różnic jest kluczowe dla podjęcia świadomej decyzji, dopasowanej do potrzeb projektowych, warunków gruntowych i oczywiście budżetu. Przecież nikt nie chce przedobrzyć, ani tym bardziej nie docenić wymagań konstrukcyjnych czy termicznych.
Podstawowy podział rodzajów płyt na fundament do samodzielnego montażu opiera się na tym, czy w konstrukcji płyty zastosowano dodatkową warstwę wzmacniającą z płyty włókno-cementowej na wierzchu izolacji, czy też jej nie ma. Ta warstwa, o grubości kilku milimetrów, ma za zadanie rozkładać punktowe obciążenia i chronić delikatniejszą izolację podczas transportu materiałów po placu budowy czy podczas samego procesu zbrojenia i betonowania. Jej obecność zwiększa sztywność całego systemu, ale naturalnie podnosi również koszt i wagę elementów.
Warianty wykonane z dodatkową warstwą wzmacniającą z płyty włókno-cementowej to rozwiązania premium, zapewniające większą odporność i ułatwiające prace na placu budowy. W tej kategorii znajdziemy produkty różniące się rodzajem i gęstością materiału izolacyjnego pod spodem. Dostępne są płyty ze styropianu (EPS 150), ze styropianu (EPS 200) oraz ze styropianu XPS, wszystkie z dodatkową warstwą wzmacniającą z płyty włókno-cementowej. Gęstość styropianu (określona cyfrą, np. 150, 200) wpływa na jego wytrzymałość na ściskanie i izolacyjność termiczną – im wyższa liczba, tym styropian jest gęstszy, mocniejszy i zazwyczaj ma nieco lepszą izolacyjność (niższą lambdę). XPS (polistyren ekstrudowany) ma z natury wyższą gęstość i lepszą izolacyjność niż EPS, a także jest bardziej odporny na wilgoć, co czyni go często wyborem numer jeden dla najbardziej wymagających zastosowań lub w trudnych warunkach gruntowych.
Drugą grupę stanowią rozwiązania bez dodatkowej warstwy wzmacniającej z płyty włókno-cementowej, określane często jako warianty "light" lub ekonomiczne. Tutaj również mamy podział w zależności od zastosowanego materiału izolacyjnego: płyty fundamentowe do samodzielnego montażu ze styropianu (EPS 150) bez dodatkowej warstwą wzmacniającą z płyty włókno-cementowej – wariant "light 150", ze styropianu (EPS 200) bez dodatkowej warstwą wzmacniającą z płyty włókno-cementowej – wariant "light 200", oraz ze styropianu XPS bez dodatkowej warstwą wzmacniającą z płyty włókno-cementowej – wariant "light XPS". Rozwiązania te są lżejsze i zazwyczaj tańsze. Wymagają jednak większej ostrożności podczas transportu i montażu, aby nie uszkodzić powierzchni izolacji. Są dobrym wyborem, gdy zależy nam na maksymalizacji oszczędności, a plac budowy umożliwia ostrożne obchodzenie się z materiałami.
Wybór między EPS a XPS zależy przede wszystkim od wymagań dotyczących izolacyjności termicznej i wytrzymałości na ściskanie. EPS (Expanded Polystyrene) to spieniony polistyren, lekki i stosunkowo tani materiał izolacyjny, powszechnie stosowany w budownictwie. EPS 150 ma deklarowaną wytrzymałość na ściskanie przy 10% odkształceniu na poziomie 150 kPa (kilopaskali), a EPS 200 odpowiednio 200 kPa. To kluczowe parametry, biorąc pod uwagę obciążenie, jakie będzie spoczywać na izolacji pod płytą fundamentową. Dla standardowych budynków mieszkalnych o niewielkim obciążeniu punktowym, EPS 150 może być wystarczający. W przypadku cięższych konstrukcji lub tam, gdzie przewidziane są duże obciążenia (np. ciężkie ściany murowane w piwnicy), EPS 200 lub XPS może okazać się lepszym wyborem. Pamiętaj, że to projektant decyduje o minimalnych wymaganiach.
XPS (Extruded Polystyrene) to polistyren ekstrudowany. Charakteryzuje się jednolitą strukturą zamkniętokomórkową, co przekłada się na lepszą izolacyjność termiczną (niższa lambda) i znacznie wyższą odporność na nasiąkanie wodą niż w przypadku EPS. Standardowe płyty XPS do zastosowań fundamentowych mają wytrzymałość na ściskanie często w przedziale 300-700 kPa, co czyni je idealnym rozwiązaniem do obciążonych konstrukcji oraz w trudnych warunkach gruntowych, gdzie poziom wód gruntowych może być wysoki. Chociaż jest droższy od EPS, jego lepsze parametry izolacyjne i odporność na wilgoć mogą przełożyć się na niższe koszty ogrzewania w przyszłości i dłuższą trwałość izolacji. Czasem warto wydać więcej na starcie, żeby potem spać spokojnie.
Obecność dodatkowej warstwy wzmacniającej z płyty włókno-cementowej w systemach prefabrykowanych znacznie ułatwia proces budowy. Chroni delikatną izolację termiczną przed przypadkowym uszkodzeniem mechanicznym. Zabezpieczenie izolacji podczas intensywnych prac związanych z transportem i układaniem zbrojenia jest niezwykle ważne. Upuszczenie ciężkiego elementu zbrojeniowego czy przejazd taczką z betonem po niezabezpieczonej powierzchni izolacji EPS mógłby łatwo ją uszkodzić, tworząc potencjalny mostek termiczny. Warstwa włókno-cementowa działa jak solidna tarcza, minimalizując takie ryzyko. Warianty bez tej warstwy wymagają więc bezwzględnie większej precyzji i delikatności ze strony wykonawcy.
Dodatkowym czynnikiem, który warto rozważyć przy wyborze rodzaju płyty, jest system łączenia poszczególnych elementów. Dobrzy producenci oferują systemy, w których płyty izolacyjne są profilowane (np. na pióro i wpust), co zapewnia lepsze połączenie i minimalizuje powstawanie mostków termicznych na styku elementów. Systemy bez takiego profilowania wymagają jeszcze dokładniejszego klejenia lub pianowania spoin, aby uzyskać ciągłą i szczelną izolację. W systemach DIY, gdzie liczy się szybkość i minimalizacja błędów, prefabrykowane, dopasowane elementy są ogromnym plusem. Myśląc "samodzielnie", myślisz też "uproszczenie".
Oprócz materiału izolacyjnego, rodzaje płyt fundamentowych do samodzielnego montażu różnią się również sposobem wykonania szalunku. W większości systemów DIY szalunek jest tracony i stanowi integralną część izolacji termicznej obwodowej płyty. Najczęściej wykonany jest ze styropianowych kątowników lub gotowych formatek, które precyzyjnie określają kształt i wysokość płyty. Dobrze zaprojektowany system szalunkowy ułatwia równe wylanie betonu i zapewnia estetyczne wykończenie krawędzi fundamentu. Nie trzeba martwić się demontażem i utylizacją tradycyjnego szalunku drewnianego.
Kolejnym aspektem, który może różnicować dostępne systemy, jest sposób dostarczania zbrojenia. Niektórzy producenci dostarczają zbrojenie w postaci prętów do samodzielnego gięcia i wiązania na placu budowy, inni zaś oferują gotowe kosze zbrojeniowe, które wystarczy ułożyć we wskazanych miejscach. Gotowe kosze zbrojeniowe znacznie przyspieszają i upraszczają ten etap prac, co jest niewątpliwie dużą zaletą dla amatora. Precyzja wykonania zbrojenia jest krytyczna dla nośności płyty, dlatego gotowe, certyfikowane kosze są kuszącą opcją. "Jeśli nie jesteś pewien, czy umiesz spleść kosz zbrojeniowy idealnie, nie ryzykuj" – to kolejna cenna rada.
Wreszcie, warto zwrócić uwagę na dostępne grubości płyt. Termoizolacyjność i nośność płyty fundamentowej zależą od jej grubości. Standardowo grubość izolacji termicznej pod płytą waha się od 20 do 30 cm, a grubość samej płyty betonowej od 15 do 25 cm. Producenci oferują różne warianty grubości, które należy dopasować do wymagań termicznych budynku (zgodnie z obowiązującymi przepisami i przyszłymi oczekiwaniami co do kosztów ogrzewania) oraz do przewidzianego obciążenia konstrukcji. Nie oszczędzaj na grubości izolacji, jeśli budujesz dom energooszczędny – to inwestycja, która szybko się zwraca w rachunkach.
Analizując dostępne na rynku systemy płyt fundamentowych, widać wyraźnie, że opcje z dodatkową warstwą wzmacniającą z płyty włóknocementowej są bardziej solidne i mniej podatne na uszkodzenia mechaniczne, choć droższe. Warianty bez tej warstwy ("light") wymagają większej uwagi podczas montażu, ale pozwalają na redukcję kosztów. Wybór między EPS a XPS zależy od oczekiwań co do izolacyjności i odporności na wilgoć. Kluczowe jest, aby każdy wybrany element, od rodzaju izolacji po system zbrojenia, był zgodny z projektem i certyfikowany. Tylko w ten sposób możemy mieć pewność, że płyta fundamentowa do samodzielnego montażu będzie stabilna, ciepła i trwała. "Budując samemu, musisz być dwa razy bardziej pewien, że wszystko robisz dobrze" – a wybór odpowiednich materiałów to połowa sukcesu.
Niezbędne narzędzia i przygotowanie podłoża pod płytę DIY
Powiedzieć, że budowa domu zaczyna się od fundamentów, to truizm, ale jakże prawdziwy. W przypadku płyty fundamentowej do samodzielnego montażu, sukces przedsięwzięcia w ogromnym stopniu zależy od pedantycznego przygotowania gruntu oraz posiadania odpowiednich narzędzi. To jak pieczenie ciasta – nawet najlepsze składniki nie dadzą rady, jeśli masz nieodpowiednie przybory i spieprzasz przygotowanie blachy. Nie oszukujmy się, samodzielne wykonanie fundamentu wymaga zaangażowania, siły mięśni i przede wszystkim precyzji. Bez solidnej podbudowy i sprawnych rąk nic tu nie zdziałasz.
Pierwszym i najważniejszym narzędziem, które będzie Ci potrzebne, jest odpowiedni sprzęt do robót ziemnych. Niekoniecznie od razu koparka (choć do usunięcia większej ilości humusu jest nieoceniona), ale na pewno szpadle, łopaty, taczki do ręcznego usuwania ziemi i kruszywa. Jeśli usunięcie humusu wymaga głębszego kopania, wynajem minikoparki na dzień lub dwa to dobra inwestycja, która zaoszczędzi Ci masę czasu i wysiłku. Pamiętaj o wytyczeniu obrysu przyszłej płyty zgodnie z projektem budowlanym za pomocą palików i sznurka – dokładność na tym etapie procentuje później. "Kopiesz nie tam, gdzie chcesz, ale tam, gdzie projekt każe" – to zasada numer jeden.
Do przygotowania podbudowy z kruszywa niezbędna będzie zagęszczarka wibracyjna. Nie wystarczy ją pożyczyć od sąsiada "na chwilę". Potrzebna jest solidna maszyna, najlepiej o masie co najmniej 150-200 kg, do efektywnego zagęszczania grubej warstwy kruszywa. Wynajem takiej zagęszczarki to standardowa praktyka na budowie. Pamiętaj, że zagęszcza się warstwowo, a nie "na raz". Sprawdzenie stopnia zagęszczenia – na przykład lekką płytą dynamiczną – jest wysoce zalecane, aby mieć pewność, że podbudowa jest solidna i nie będzie osiadać. Osiadanie gruntu pod płytą to scenariusz z budowlanych koszmarów, który kończy się często rysami na ścianach budynku.
Do ułożenia i wyrównania warstwy podsypki cementowo-piaskowej lub chudego betonu przydadzą się łaty murarskie, poziomica (najlepiej długa i libelka), oraz zacieraczka. Chodzi o uzyskanie idealnie równej powierzchni, na której położysz izolację termiczną. Każdy garbek czy wgłębienie na tym etapie będzie skutkować nierównością w warstwie izolacji, a to prosta droga do mostków termicznych. Równa płaszczyzna to podstawa, jak idealnie prosty tor kolejowy dla gładkiej jazdy pociągu.
Przy układaniu izolacji termicznej i przeciwwilgociowej potrzebne będą nożyk do cięcia materiałów izolacyjnych (np. styropianu czy XPS), miarka, kątownik i klej lub pianka niskoprężna do uszczelniania połączeń płyt izolacyjnych. Układanie folii hydroizolacyjnej wymaga precyzji przy łączeniu arkuszy na zakład i uszczelnianiu spoin dedykowaną taśmą. Ważne, aby folia nie została uszkodzona podczas kolejnych etapów prac – każdy, nawet najmniejszy otwór, to potencjalna droga dla wilgoci. Czasem warto przykleić górną folię do izolacji termicznej, żeby nie przesuwała się podczas chodzenia po niej.
Montaż zbrojenia wymaga giętarki do prętów (jeśli zbrojenie nie jest dostarczane w gotowych koszach), nożyc do cięcia stali, drutu wiązałkowego i wiązarki do zbrojenia (ręcznej lub automatycznej). Zbrojenie musi być ułożone na dystansach (podkładkach dystansowych), aby zapewnić mu odpowiednią otulinę betonową. Nigdy nie kładź zbrojenia bezpośrednio na izolacji czy podbudowie – stal bez otuliny betonowej nie spełni swojej funkcji i może rdzewieć. Zbrojenie to krwiobieg płyty, musi być ułożony idealnie, bo inaczej cała konstrukcja choruje.
Najbardziej wymagającym etapem pod względem sprzętu jest betonowanie. Potrzebny będzie beton towarowy dostarczony betonomieszarką oraz sprzęt do jego rozprowadzenia i zagęszczenia. Do rozprowadzania betonu przyda się taczka (do niewielkich ilości lub poprawiania) lub pompa do betonu (przy większych kubaturach, ułatwiająca transport betonu z gruszki na płytę). Zagęszczenie betonu wymaga wibratorów – najczęściej buławowych (do zanurzania w masie betonowej) lub listw wibracyjnych (do pracy na powierzchni). Prawidłowe zawibrowanie betonu jest krytyczne dla jego wytrzymałości i szczelności. Bez wibratora beton będzie jak ser szwajcarski – pełen dziur i osłabiony.
Do wykończenia powierzchni płyty, czyli jej zacierania, potrzebne będą łaty wibracyjne lub zwykłe, a także zacieraczki – ręczne (pacę) lub mechaniczne (np. typu "helikopter") do dużych powierzchni. Celem jest uzyskanie idealnie równej i gładkiej powierzchni, która w przyszłości będzie podłogą w budynku. Pamiętaj, że zacieranie wykonuje się, gdy beton zacznie wstępnie wiązać i przestanie się zapadać pod pacą – ani za wcześnie, ani za późno. To wymaga pewnego wyczucia czasu, które przychodzi z doświadczeniem lub jest opisane w instrukcji technicznej betonu.
Dodatkowo, warto mieć na placu budowy: taśmę mierniczą o długości co najmniej 50 m, młotek, gwoździe lub wkręty do mocowania elementów szalunkowych, piłę ręczną do cięcia drewna (np. na paliki), poziomnicę, niwelator optyczny lub laserowy do precyzyjnego wyznaczania poziomów, a także podstawowy sprzęt BHP: rękawice, okulary ochronne, kask (szczególnie przy pracy ze zbrojeniem) i obuwie ochronne. To nie jest "budowa na dziko" – zasady bezpieczeństwa obowiązują tak samo jak na profesjonalnym placu budowy.
Przygotowanie podłoża to kluczowy element procesu. Rozpoczyna się od precyzyjnego usunięcia humusu. Sprawdzenie geologiczne gruntu powinno być wykonane wcześniej przez specjalistę, który określi nośność gruntu rodzimego i ewentualną obecność wód gruntowych. Odpowiednie przygotowanie podbudowy z kruszywa, z jej starannym, wielowarstwowym zagęszczeniem, jest absolutnie krytyczne dla zapobiegania osiadaniom w przyszłości. Wyobraź sobie, że budujesz zamek z piasku – jeśli podstawa jest luźna, cała konstrukcja się zawali.
Warstwa wyrównawcza z chudego betonu lub podsypki piaskowo-cementowej musi być nie tylko równa, ale też stabilna. Upewnij się, że ma odpowiednią grubość i jest prawidłowo zagęszczona lub związana (w przypadku betonu). Na tej idealnie przygotowanej bazie dopiero można rozpocząć układanie izolacji termicznej i przeciwwilgociowej, mając pewność, że będą one pracować poprawnie. Każdy etap przygotowania podłoża musi być wykonany ze świadomością, że jest to fundament pod przyszły fundament, a jakość pracy na tym wczesnym etapie decyduje o wszystkim, co nastąpi później.
Oprócz sprzętu do robót ziemnych, zagęszczania i betonowania, nie zapomnij o narzędziach ręcznych: kielnie, pace, wiadra, szlifierka kątowa (z tarczą do cięcia metalu i betonu), młot udarowy (do ewentualnego skuwania betonu lub równania twardego podłoża) i drobne akcesoria. Warto mieć też pod ręką węża ogrodowego i dostęp do wody do pielęgnacji betonu. Im lepiej przygotujesz się pod względem sprzętowym i zaplanujesz każdy ruch, tym mniej nieprzewidzianych problemów pojawi się na placu budowy. Stare porzekadło mówi: "Kto nie planuje, ten planuje porażkę". W budownictwie to zasada złota.
Przygotowanie podłoża pod płytę DIY to proces wieloetapowy, wymagający nie tylko fizycznego wysiłku, ale przede wszystkim wiedzy i precyzji. Od usunięcia humusu, przez wykonanie i zagęszczenie podbudowy, po warstwę wyrównawczą i izolacje – każdy krok ma znaczenie. Posiadanie odpowiednich narzędzi i maszyn jest niezbędne do prawidłowego wykonania tych prac. Chociaż lista potrzebnego sprzętu może wydawać się długa i kosztowna (wynajem), jest to inwestycja w jakość i trwałość fundamentu. Nie próbuj zastępować profesjonalnego sprzętu improwizowanymi rozwiązaniami – to prosta droga do kosztownych błędów. W tym przypadku, brak kompromisów w kwestii narzędzi i przygotowania gruntu jest absolutną koniecznością. Pamiętaj, to Ty jesteś teraz budowlanym "chefem" i od Twojej precyzji zależy, czy danie (czyli dom) wyjdzie idealnie.