Szalowanie płyty fundamentowej krok po kroku 2025
Zanurzenie się w świat solidnych fundamentów budzi dreszczyk emocji – wszak to one stanowią kręgosłup każdej trwałej konstrukcji. Kiedy mowa o posadowieniu budynku na płycie, kluczową rolę odgrywa płyta fundamentowa szalunek. To on, niczym precyzyjna forma cukiernicza, nadaje mokremu betonowi pożądany kształt i pozwala uzyskać idealnie płaską, stabilną powierzchnię, stanowiącą solidną bazę dla przyszłego domu.
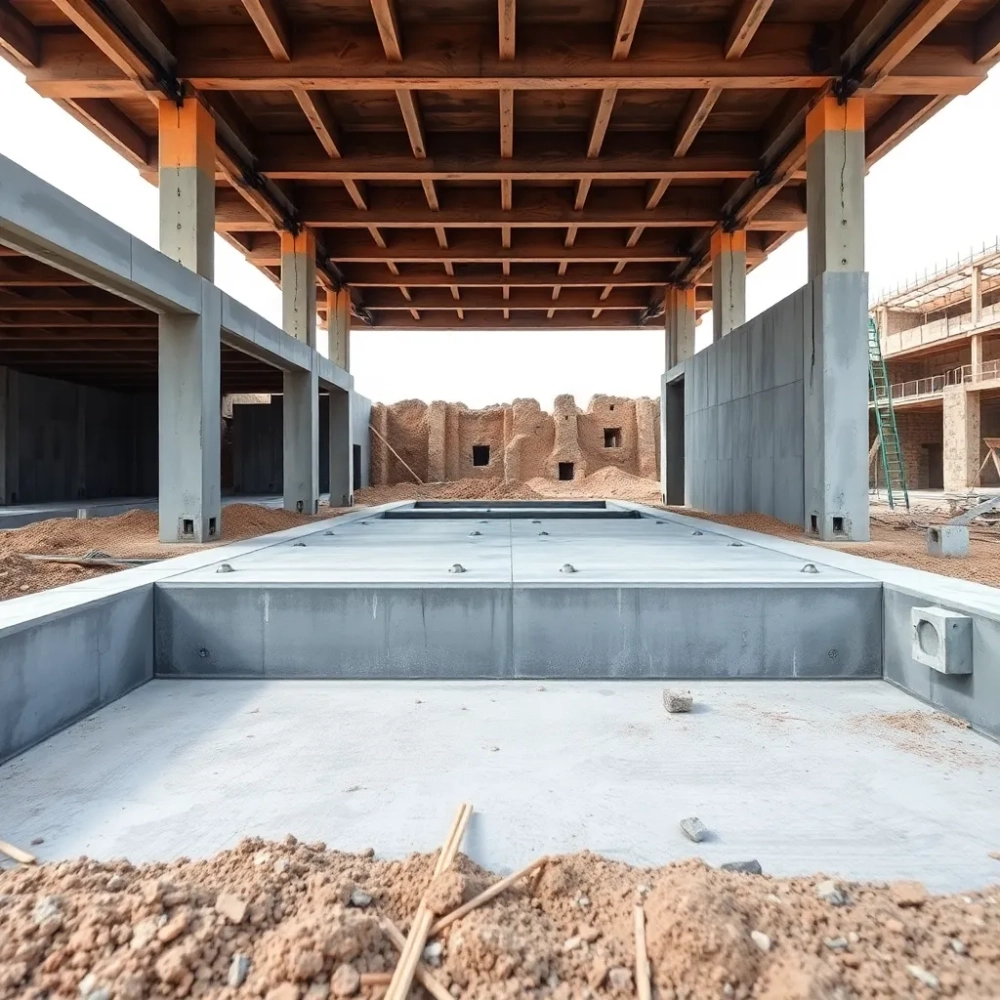
Analizując różnorodne metody i systemy wykorzystywane do tworzenia szalunków płyt fundamentowych, często natrafiamy na porównania kluczowych parametrów decydujących o efektywności i opłacalności inwestycji. Poniżej przedstawiamy dane syntetyzujące podejście do trzech typowych opcji, pozwalające na szybką ocenę ich potencjału w praktyce budowlanej. Przyjrzyjmy się bliżej tym wskaźnikom.
System Szalunkowy | Orientacyjny Koszt materiałów (PLN/m²) | Orientacyjny Czas Montażu (osobogodziny/m²) | Stopień Reużywalności (skala 1-5) | Wpływ na Izolacyjność Cieplną |
---|---|---|---|---|
Tradycyjne deskowanie drewniane | 50 - 120 (zależnie od rodzaju drewna i grubości) | 0.5 - 1.5 | 1 - 2 (często jednorazowy) | Neutralny (wymaga osobnej izolacji) |
Systemowe szalunki panelowe (stal/aluminium/tworzywo) | 150 - 400 (amortyzacja kosztu zakupu/wynajmu) | 0.2 - 0.6 | 4 - 5 (wielokrotne użycie) | Neutralny (wymaga osobnej izolacji) |
Szalunek tracony (np. z płyt XPS/styropianowych) | 80 - 180 (zależnie od grubości izolacji) | 0.3 - 0.7 | 1 (pozostaje w konstrukcji) | Pozytywny (integruje izolację termiczną) |
Powyższe dane ukazują wyraźne różnice między popularnymi rozwiązaniami, co ma bezpośrednie przełożenie na proces decyzyjny na etapie projektowania i planowania prac. Wybór systemu szalunkowego pod szalowanie płyty fundamentowej to nie tylko kwestia ceny materiału czy tempa montażu, ale często także strategiczna decyzja wpływająca na kolejne etapy budowy i końcowy bilans energetyczny budynku. To tak jakbyśmy wybierali odpowiednie narzędzie do skomplikowanej operacji – każde ma swoje zalety i wady, a właściwy wybór zależy od specyfiki "pacjenta", czyli naszej przyszłej płyty.
Przygotowanie terenu i wytyczenie obrysu pod szalunek
Sukces w budowie zaczyna się od dokładnego przygotowania, a w przypadku płyty fundamentowej jest to absolutna podstawa, od której nie ma odwrotu. Pierwszym krokiem jest usunięcie humusu, czyli warstwy żyznej gleby, często na głębokość 20-30 cm, a czasami więcej, jeśli grunt rodzimy tego wymaga. Musimy dotrzeć do stabilniejszego podłoża, wolnego od roślinności i wszelkich organicznych zanieczyszczeń, które mogłyby osiąść pod wpływem obciążenia i spowodować nierówności w przyszłości.
Następnie teren musi zostać wyrównany. Precyzja tutaj jest kluczowa; najlepiej użyć niwelatora optycznego lub laserowego, aby uzyskać powierzchnię płaską jak stół bilardowy w idealnym świecie. Pamiętajmy, że wszelkie nierówności na tym etapie przełożą się na większe zużycie materiału na podsypkę, a co gorsza, mogą wpływać na nośność podłoża i potencjalne osiadanie płyty. Czystość placu to nie kaprys architekta, lecz techniczna konieczność.
Kiedy grunt jest już odpowiednio przygotowany, czas na wytyczenie obrysu przyszłej płyty, co fachowo nazywamy geodezyjnym palikowaniem. To jest ten moment, kiedy wizja z papieru materializuje się na ziemi w postaci sznurków i palików. Geodeta, niczym detektyw, przenosi projektowane osie budynku na plac budowy, uwzględniając kąty proste i odległości z dokładnością do milimetra – błędy w tym miejscu są niewybaczalne i drogo kosztują na dalszych etapach. Obrys płyty jest szerszy niż ściany budynku, często o kilkanaście do kilkudziesięciu centymetrów, aby zapewnić stabilne podparcie dla szalunku i ułatwić późniejsze prace.
Kolejnym niezbędnym etapem jest wykonanie podsypki. Najczęściej stosuje się warstwę zagęszczonego piasku lub pospółki o grubości 15-30 cm, która służy jako warstwa wyrównująca i mrozoochronna. Zagęszczenie podsypki jest absolutnie krytyczne – często wymaga to użycia ciężkiego sprzętu, takiego jak zagęszczarka wibracyjna, do momentu uzyskania odpowiedniego wskaźnika nośności. Podsypka stanowi miękkie posłanie dla warstwy chudego betonu lub styropianu w przypadku technologii płyty izolowanej, dlatego jej jakość ma bezpośredni wpływ na równomierne obciążenie gruntu.
Przed rozpoczęciem budowy samego szalunku, na przygotowanym i zagęszczonym podłożu, często układa się cienką warstwę chudego betonu (tzw. "chudziak") o grubości 5-10 cm. Jej głównym zadaniem jest stworzenie czystej i równej platformy roboczej, która zapobiega mieszaniu się betonu właściwej płyty z podłożem. Jest to także bariera dla wilgoci i zapewnia stabilną płaszczyznę do precyzyjnego układania izolacji termicznej i przeciwwilgociowej, co jest nieocenioną wartością w kontekście trwałości konstrukcji. Kto próbował układać folię hydroizolacyjną na piasku, ten wie o czym mowa.
Dokładne wytyczenie obrysu szalunku pod płytę fundamentową wymaga zastosowania specjalistycznych narzędzi i przestrzegania ścisłych tolerancji. Niewielkie odchylenia na tym etapie kumulują się i mogą prowadzić do poważnych problemów konstrukcyjnych lub konieczności kosztownych poprawek. Często stosuje się "ławy drutowe" ustawione poza przyszłym obrysem płyty, na których oznacza się osie budynku – pozwalają one odtworzyć pierwotne linie, nawet po usunięciu sznurków czy tymczasowych palików roboczych, zapewniając niebywałą precyzję nawet w trudnych warunkach. To sprytne rozwiązanie, które ratuje nerwy i czas.
Kolejnym szczegółem, który często umyka mniej doświadczonym ekipom, jest zaplanowanie wszelkich przejść instalacyjnych już na etapie przygotowania podłoża. Rury kanalizacyjne, przepusty elektryczne czy inne media, które mają przebiegać pod płytą lub przez nią, muszą być uwzględnione i prawidłowo ułożone lub zabezpieczone przed zalaniem betonem. Pomyłka tutaj oznacza konieczność kucia gotowej płyty, co jest koszmarem każdej budowy – potrafi zniszczyć całą strukturę zbrojenia i osłabić konstrukcję. Lepiej myśleć kilka kroków do przodu, prawda?
Ostatnim, lecz równie ważnym elementem przygotowania terenu, jest wykonanie drenażu, jeśli jest on przewidziany w projekcie z uwagi na wysoki poziom wód gruntowych lub specyfikę gruntu (np. gliniasty, nieprzepuszczalny). Odpowiednie odwodnienie zapobiega napieraniu wody na płytę od spodu i zmniejsza ryzyko przemarzania gruntu pod nią, co mogłoby prowadzić do podnoszenia się płyty. Nierzadko zdarzają się przypadki uszkodzeń konstrukcji spowodowanych siłami wyporu wody lub ekspansją zamarzniętej wody gruntowej, dlatego ten aspekt nie może być lekceważony. Drenaż to taka polisa ubezpieczeniowa dla naszego fundamentu.
Wybór materiału i systemu szalunkowego do płyty
Decyzja o wyborze konkretnego systemu szalunkowego to moment, w którym teoria spotyka się z praktyką i często z portfelem inwestora. Na rynku dostępnych jest kilka podstawowych typów, każdy z własnym zestawem wad i zalet, które należy przeanalizować pod kątem specyfiki danego projektu i dostępnych zasobów. To jak wybór samochodu – sportowy, terenowy czy kombi? Każdy służy do czegoś innego.
Najbardziej tradycyjnym i często najtańszym w zakupie materiałem do wykonania szalunku jest drewno. Deski o grubości 25-32 mm, podparte stemplami i ryglami, tworzą klasyczną formę. Zalety? Łatwość adaptacji do niestandardowych kształtów i stosunkowo niski koszt zakupu materiału. Wady? Jest to proces pracochłonny, wymaga doświadczenia w ciesielstwie, a drewno po użyciu jest często jednorazowe lub jego wartość recyklingowa jest niewielka. Poza tym szczelność takiego szalunku bywa problematyczna, jeśli deski są źle dopasowane lub wyschnięte, a idealna gładkość powierzchni trudniejsza do uzyskania. No i to zużycie drewna – dla planety to niezbyt optymistyczny wybór na dłuższą metę, prawda?
W opozycji do tradycyjnego drewna stoją systemowe szalunki panelowe, wykonane najczęściej ze stali, aluminium lub specjalistycznego tworzywa sztucznego, z poszyciem ze sklejki szalunkowej lub tworzywa. Ich główną zaletą jest szybkość i łatwość montażu dzięki modułowej konstrukcji i systemowym połączeniom. Elementy są produkowane z wysoką precyzją, co gwarantuje równe krawędzie i gładką powierzchnię płyty. Systemy te są zaprojektowane do wielokrotnego użytku – nawet kilkaset razy w przypadku dobrych systemów. "Wielokrotny użytek" to słowo klucz w kontekście opłacalności przy większych projektach lub dla firm budowlanych. Jednakże, wymagają one zazwyczaj inwestycji w zakup całego systemu lub wynajmu, co generuje znaczne koszty początkowe, chociaż przy wielu realizacjach szybko się zwracają.
Kolejną opcją, zyskującą na popularności, jest szalunek tracony, najczęściej wykonany ze specjalnych bloków z twardego styropianu (XPS) lub innego materiału izolacyjnego, które po zalaniu betonem pozostają w konstrukcji. Ta metoda ma kapitalną zaletę: łączy funkcję szalunku z izolacją termiczną płyty, co jest zgodne z nowoczesnymi wymogami energooszczędnego budownictwa. Eliminuje to potrzebę późniejszego układania izolacji pod płytą lub na jej krawędziach, oszczędzając czas i pracę. Koszt może być porównywalny z tradycyjnym szalunkiem, ale pamiętajmy, że płacimy tu już za gotową warstwę izolacji. Montaż jest często bardzo szybki i intuicyjny – niczym układanie dużych klocków Lego. Minusem może być ograniczona elastyczność w tworzeniu bardzo skomplikowanych kształtów, choć producenci oferują wiele kształtek specjalnych, które znacząco ułatwiają ten proces.
Wybór odpowiedniego systemu szalunkowego zależy od wielu czynników. Po pierwsze, budżet inwestora – choć szalunek systemowy wydaje się droższy na początku, przy większej liczbie metrów kwadratowych płyty (powyżej np. 200-300 m²) wynajem lub zakup elementów może być bardziej ekonomiczny niż ciągłe kupowanie drewna. Po drugie, skala projektu – przy małym domku jednorodzinnym drewno lub szalunek tracony mogą być optymalnym wyborem, podczas gdy przy hali przemysłowej o powierzchni tysięcy metrów kwadratowych systemy modułowe są bezkonkurencyjne pod względem szybkości i efektywności. Po trzecie, kształt płyty – bardzo nieregularne, łukowe formy łatwiej wykonać w szalunku drewnianym lub specjalnie profilowanych systemach, niż w szalunku traconym z gotowych bloków. To trochę jak wybór pędzla – inny do detali, inny do tła.
Innym ważnym aspektem jest dostępność materiałów i ekip budowlanych z doświadczeniem w danym systemie. Nie ma sensu wybierać zaawansowanego szalunku systemowego, jeśli w okolicy brak firm, które potrafią go profesjonalnie zmontować. Podobnie, praca z szalunkiem traconym wymaga pewnej wiedzy na temat prawidłowego łączenia i uszczelniania elementów izolacyjnych. Warto zasięgnąć opinii wykonawców specjalizujących się w danym typie szalowania płyt fundamentowych, aby poznać realia pracy z konkretnym materiałem. Czasami "ekonomiczniej" znaczy po prostu "szybciej i prościej" dla ekipy na placu budowy.
Warto również zastanowić się nad przyszłością – czy planujemy budować inne obiekty, gdzie moglibyśmy wykorzystać ten sam system szalunkowy? Jeśli tak, inwestycja w zakup systemu panelowego może okazać się bardzo opłacalna w perspektywie kilku lat i kolejnych budów. Dobrej jakości panele szalunkowe, odpowiednio konserwowane, potrafią służyć przez dziesięciolecia. To element, który może stać się "aktywami" naszej firmy budowlanej lub źródłem dochodu z wynajmu. Strategiczne myślenie jest w cenie, dosłownie.
Nie bez znaczenia pozostaje również wpływ na środowisko i możliwości recyklingu. Drewno z rozbiórki szalunków jest często spalone lub trafia na wysypisko, choć teoretycznie mogłoby zostać przetworzone. Systemowe panele metalowe lub tworzywowe, po zużyciu, mogą być przetopione i użyte ponownie, wpisując się w ideę gospodarki obiegu zamkniętego. Szalunek tracony, jako integralna część płyty, nie generuje odpadów na tym etapie budowy, co jest jego ekologiczną zaletą. Wybierając materiał, warto wziąć pod uwagę ten aspekt, bo przecież budujemy nie tylko dla siebie, ale i dla przyszłych pokoleń.
Cena wynajmu systemów szalunkowych waha się, ale orientacyjnie możemy przyjąć od kilku do kilkunastu złotych za metr kwadratowy powierzchni szalowanej na dobę, w zależności od systemu, okresu wynajmu i regionu kraju. Do tego dochodzi często koszt transportu i ewentualnych elementów specjalnych. W przypadku zakupu, ceny dobrych systemów zaczynają się od kilkuset złotych za metr kwadratowy i mogą sięgać nawet powyżej tysiąca złotych za m² panelu. Deski szalunkowe kosztują natomiast kilkaset złotych za metr sześcienny, co po przeliczeniu na metry kwadratowe szalowanej powierzchni daje nam widełki podane w tabeli wcześniej, ale doliczyć trzeba odpady i zużycie. Liczby mają znaczenie, oj mają.
Podsumowując, wybór materiału i systemu szalunkowego dla płyty fundamentowej wymaga przemyślanej analizy wielu zmiennych. Nie ma jednej uniwersalnej odpowiedzi. To złożony proces, który powinien uwzględniać budżet, skalę i kształt projektu, dostępność materiałów i specjalistycznych ekip, a także plany na przyszłość i aspekt ekologiczny. Dobrze podjęta decyzja na tym etapie przekłada się na płynność prac, koszty budowy i w ostatecznym rozrachunku na jakość wykonanego fundamentu. Czasem taniej jest zainwestować trochę więcej na początku, żeby potem spać spokojnie. To inwestycja, która naprawdę się opłaca.
Montaż szalunku - kluczowe etapy i zasady
Sam proces montażu szalunku pod płytę betonową przypomina trochę składanie olbrzymiego modelu, ale z tą różnicą, że pomyłki bolą znacznie bardziej niż w przypadku modeli z plastiku. To etap, gdzie teoria z projektu staje się namacalną konstrukcją, która musi wytrzymać olbrzymie napory świeżego betonu. Pierwszym krytycznym krokiem jest ustalenie poziomu górnej krawędzi płyty fundamentowej. Najczęściej robi się to, montując po obwodzie płyty specjalne listwy lub belki, które posłużą jako linia odniesienia. Precyzja tych listew determinuje finalny poziom posadzki, więc mierzymy i sprawdzamy wielokrotnie.
Następnie rozpoczyna się budowa ścianek szalunku. W przypadku deskowania tradycyjnego polega to na pionowym wbijaniu palików lub kotwieniu słupków i poziomym przybijaniu do nich desek jedna nad drugą. Deski muszą ściśle przylegać do siebie, aby zminimalizować ucieczkę zaczynu cementowego (mleczka) podczas betonowania. Używa się gwoździ lub wkrętów, pamiętając o solidnym połączeniu wszystkich elementów. Ta praca wymaga ręcznej precyzji i doświadczenia ciesielskiego, a czasem niezłej krzepy – pamiętajmy, że siły działające na taki szalunek są znaczące.
W przypadku systemowych szalunków panelowych, montaż jest szybszy. Gotowe panele łączy się ze sobą za pomocą klamr, zamków lub sworzni, tworząc szczelną i sztywną ścianę szalunku. Producenci systemów oferują różnorodne akcesoria ułatwiające połączenia narożne, tworzenie elementów łukowych czy adaptację do różnych wysokości. Kluczowe jest przestrzeganie instrukcji producenta systemu, ponieważ każdy ma swoje unikalne rozwiązania. Montaż tych systemów często przypomina układanie dużych puzzli, ale z dużą precyzją.
Szczególnie ważne w montażu jest zapewnienie stabilności szalunku, co osiąga się poprzez odpowiednie podparcie i rozparcie. Od zewnątrz ścianki szalunku podpierane są skośnymi podporami (stemplami) opierającymi się o grunt lub inne stabilne punkty. Gęstość i wytrzymałość tych podpór zależy od wysokości szalunku i przewidywanego nacisku betonu – wyższy beton generuje większe siły. Od wewnątrz szalunek musi być rozparty, aby ściany nie zbiegły się pod wpływem ciężaru wylewanego betonu. Najczęściej używa się rozpór (krawędziaków drewnianych lub metalowych profili) umieszczonych w górnej części szalunku. "Rozparcie" to takie wsadzenie kijka między dwie rzeczy, żeby się nie złożyły – proste, ale jakże kluczowe!
Niezwykle ważnym elementem montażu są ściągi, które spinają przeciwległe ściany szalunku. To one przejmują większość naporu poziomego od wylewanego betonu, zapobiegając wybrzuszeniu się szalunku. Ściągi mogą być wykonane z gwintowanych prętów z nakrętkami i podkładkami (do systemów panelowych) lub ze specjalnych drutów szalunkowych przechodzących przez otwory w deskach i oplatających rygle zewnętrzne. Ich prawidłowe rozmieszczenie i dokręcenie jest absolutnie krytyczne dla zachowania prostoliniowości ścian szalunku. Przyjmuje się, że rozstaw ściągów dla ścian o wysokości ok. 30-40 cm w tradycyjnym szalunku drewnianym wynosi typowo 60-80 cm, ale precyzyjny rozstaw zależy od grubości desek, przekroju rygli i przewidywanej prędkości betonowania.
Kolejnym etapem jest montaż narożników. W szalunku drewnianym narożniki są wzmocnione dodatkowymi palikami i deskami ryglującymi, aby zapobiec rozepchnięciu. W systemach panelowych stosuje się specjalne narożnikowe elementy systemowe. Narożniki są miejscami szczególnie narażonymi na koncentrację naprężeń, więc ich solidność jest nie do przecenienia. Źle zabezpieczony narożnik potrafi pęknąć i rozlać beton, a uwierzcie mi, sprzątanie tego to istna katastrofa.
Przed ułożeniem zbrojenia i zalaniem betonem, do wnętrza szalunku należy wprowadzić wszelkie elementy, które mają być zatopione w płycie, takie jak rury kanalizacyjne, przepusty wentylacyjne, puszki elektryczne czy kotwy do słupów konstrukcyjnych. Muszą być one solidnie zamocowane do szalunku lub zbrojenia, aby nie przesunęły się podczas wibracji betonu. Planowanie lokalizacji tych elementów z wyprzedzeniem jest absolutnie konieczne – brak takiego przepustu oznacza konieczność kucia, co osłabia strukturę płyty i jest bardzo pracochłonne. Taka improwizacja na budowie rzadko kończy się dobrze.
Powierzchnia szalunku stykająca się z betonem powinna być przed betonowaniem dokładnie oczyszczona z wszelkich zanieczyszczeń (ziemia, pył, wióry drewniane) i zabezpieczona środkiem antyadhezyjnym. Środek antyadhezyjny (np. olej szalunkowy) tworzy cienką warstwę, która zapobiega przywieraniu betonu do szalunku, ułatwiając jego późniejszy demontaż i pozostawiając gładką powierzchnię betonu. Zapominając o tym, ryzykujemy "zerwanie" fragmentów betonu podczas rozszalowywania lub pozostawienie trudnych do usunięcia resztek na szalunku. Czysty szalunek to połowa sukcesu przy rozszalowywaniu.
Podczas całego procesu montażu, a zwłaszcza przed wylaniem betonu, kluczowa jest kontrola. Sprawdzamy poziom górnej krawędzi szalunku w wielu punktach, mierzymy wymiary zewnętrzne i wewnętrzne, kontrolujemy prostość ścian i prawidłowe usztywnienie oraz rozparcie. To jest ostatni dzwonek, żeby skorygować wszelkie błędy. Solidnie wykonany montaż szalowania pod płytę jest gwarancją uzyskania płyty o projektowanych wymiarach i kształcie, która będzie mogła pełnić swoją funkcję konstrukcyjną bez zarzutu. Trochę jak ostatnia przymiarka garnituru przed ważnym wyjściem – musi leżeć idealnie.
Zapewnienie stabilności i szczelności szalunku płyty fundamentowej
Wyobraźmy sobie, że wylewamy tony płynnego betonu do konstrukcji, która nie jest wystarczająco solidna – skutek byłby opłakany, przypominający powódź na placu budowy. Zapewnienie stabilności i szczelności szalunku płyty to kluczowy element, który decyduje o powodzeniu całego przedsięwzięcia. Napór betonu w stanie płynnym jest olbrzymi, zwłaszcza w dolnych partiach szalunku, rośnie wprost proporcjonalnie do wysokości wylewania i gęstości mieszanki betonowej. Jest jak parcie wody, tylko znacznie potężniejsze z uwagi na ciężar materiału.
Stabilność szalunku uzyskuje się przede wszystkim poprzez system podpór i rozparć, o których wspominaliśmy wcześniej. Podpory zewnętrzne (stemple, odciągi) muszą być zakotwiczone w sposób uniemożliwiający przesunięcie. W przypadku dużych płyt i wysokich szalunków, obliczenia wytrzymałościowe podpór i ściągów powinny być wykonane przez konstruktora. Nie można improwizować – system podparcia musi być w stanie przenieść pełne obciążenie od świeżego betonu, które może sięgać nawet 25-30 kN na metr kwadratowy powierzchni szalunku na wysokości 1 metra. To ogromne siły, jakbyśmy chcieli zatrzymać małą ciężarówkę gołymi rękami!
Ściągi, przebijające się przez wnętrze szalunku, odgrywają rolę spinającą i są najczęstszym punktem krytycznym, jeśli chodzi o siły rozciągające. Wykonuje się je zazwyczaj ze stali o wysokiej wytrzymałości na rozciąganie. Muszą być odpowiednio dociągnięte przed betonowaniem, ale nie przetężone, co mogłoby uszkodzić szalunek. Ich rozstaw i średnica są kluczowe i zależą od wysokości szalunku, rozstawu rygli (elementów poziomych usztywniających ścianki szalunku) i specyfiki systemu szalunkowego. Typowe ściągi mają średnicę 15-20 mm i są rozmieszczone w siatce o rozstawie np. 80x80 cm lub 100x60 cm, ale to tylko orientacyjne wartości – wszystko zależy od konkretnych obciążeń i specyfiki konstrukcji szalunku.
Szczelność szalunku jest równie ważna jak jego stabilność. Nieszczelności powodują ucieczkę zaczynu cementowego, czyli najdrobniejszych, najbardziej aktywnych cząstek betonu. Skutkuje to powstaniem tzw. "raków", czyli pustych przestrzeni z widocznym kruszywem, lub porowatej, słabej struktury betonu w miejscach przecieków. Taki beton ma znacznie obniżoną wytrzymałość i jest podatny na penetrację wilgoci oraz korozję zbrojenia. Trochę jak sito zamiast pełnego wiadra – to, co ważne, po prostu wycieka.
Aby zapewnić szczelność, wszystkie połączenia między elementami szalunku muszą być starannie wykonane. W szalunku drewnianym deski powinny być szczelnie do siebie dopasowane, najlepiej na tzw. felc (zakładkę) lub na pióro i wpust. Szczeliny, jeśli są, można uszczelnić listwami dociskowymi, specjalnymi taśmami uszczelniającymi, pianką poliuretanową (ostateczność!) lub masami uszczelniającymi. W systemach panelowych szczelność zapewniają precyzyjne połączenia systemowe, ale miejsca łączeń paneli i wszelkie przejścia na śruby czy ściągi również wymagają kontroli i często dodatkowego uszczelnienia.
Szczególną uwagę należy zwrócić na połączenie szalunku ze spodem. Jeśli płyta wylewana jest na chudziaku, szalunek opiera się bezpośrednio na nim, a ewentualne szczeliny u dołu mogą być minimalne. Jeśli natomiast szalunek stoi bezpośrednio na podsypce lub warstwie izolacji (w przypadku szalunku traconego), połączenie musi być idealnie szczelne, aby zapobiec wypłynięciu zaczynu pod szalunek. Używa się do tego specjalnych uszczelek, klinów dociskowych lub po prostu bardzo precyzyjnie docina i dopasowuje dolne elementy. Brak szczelności na dole jest jak dziura w dnie łódki – zatopienie murowane.
W przypadku szalunków traconych z materiałów izolacyjnych (np. XPS), szczelność na połączeniach bloków i w narożnikach jest zapewniana poprzez system zamków (np. typu pióro-wpust) oraz często przez dodatkowe sklejenie lub uszczelnienie tych połączeń dedykowanymi klejami lub piankami. Przejścia rur i instalacji przez ścianki szalunku traconego muszą być starannie dopasowane i uszczelnione, aby zimny beton nie dostał się do wnętrza konstrukcji izolacyjnej i nie stworzył mostków termicznych, a przede wszystkim nie wypłynął. Tutaj każdy detal ma znaczenie.
Podczas betonowania kluczowe jest również zachowanie odpowiedniej prędkości podawania betonu i prawidłowe wibrowanie. Zbyt szybkie wylewanie betonu lub niewłaściwe wibrowanie może gwałtownie zwiększyć napór na szalunek i doprowadzić do jego uszkodzenia lub wybrzuszenia. Wibrator należy wprowadzać pionowo i wyciągać powoli, upewniając się, że beton równomiernie wypełnia całą przestrzeń, a powietrze jest skutecznie usuwane, ale jednocześnie nie przemieszczać nadmiernie szalunku. Fachowe betonowanie to sztuka, która wymaga wyczucia i doświadczenia, ale też solidnego szalunku jako fundamentu tej sztuki. Nie zapominajmy o sile drgań, które też potrafią narobić bigosu.
Kontrola prawidłowości wykonania szalunku przed betonowaniem
Chwila poprzedzająca wylanie betonu na płytę fundamentową to moment najwyższego napięcia i ostatnia szansa na weryfikację, czy wszystko zostało wykonane zgodnie ze sztuką i projektem. To jest trochę jak kontrola przedstartowa promu kosmicznego – nie ma miejsca na pomyłki, bo konsekwencje są poważne. Pierwszym i absolutnie fundamentalnym elementem kontroli jest sprawdzenie wymiarów geometrycznych szalunku. Mierzymy długość, szerokość oraz przekątne płyty, porównując je z wartościami podanymi w projekcie. Tolerancje powinny być ścisłe, np. ±1-2 cm dla wymiarów zewnętrznych i wewnętrznych, oraz analogicznie dla przekątnych, aby upewnić się, że bryła budynku wzniesiona na tej płycie będzie prosta i w odpowiednich miejscach.
Równie ważna jest kontrola poziomu górnej krawędzi szalunku w wielu punktach. Używamy niwelatora laserowego lub optycznego, aby upewnić się, że szalunek jest idealnie wypoziomowany i znajduje się na właściwej rzędnej (wysokości nad poziomem morza lub innym punkcie odniesienia). Odchylenia od poziomu powinny być minimalne, rzędu kilku milimetrów na metr, a maksymalnie 1-2 cm na całej powierzchni płyty. Precyzja na tym etapie przekłada się bezpośrednio na minimalizację konieczności wylewania warstw wyrównujących na gotowej płycie, co oszczędza czas i materiał.
Sprawdzamy pionowość ścianek szalunku, szczególnie przy jego zewnętrznych krawędziach. Ścianki powinny być proste i pionowe, chyba że projekt przewiduje inne pochylenie (co zdarza się niezwykle rzadko przy płytach fundamentowych). Weryfikujemy to pionem murarskim lub poziomicą z libellą do pomiaru pionowości. Nawet niewielkie pochylenie ścianek szalunku oznacza, że finalna płyta będzie miała nierówne, ukośne krawędzie, co może utrudniać dalsze prace, np. murowanie ścian.
Kolejnym krytycznym punktem jest kontrola stabilności szalunku i poprawności jego usztywnienia. Fizycznie oglądamy i sprawdzamy wszystkie podpory zewnętrzne, upewniając się, że są solidnie zakotwione i prawidłowo ustawione. Weryfikujemy poprawność rozparcia wewnętrznego i dokręcenie ściągów, które spinają przeciwległe ściany. Patrzymy, czy nie ma żadnych widocznych słabych punktów, czy elementom drewnianym (deskom, stemplom) nie grozi złamanie lub wyboczenie pod naporem betonu. Można delikatnie docisnąć ścianki szalunku, aby sprawdzić ich sztywność – nie powinny się uginać pod średnim naciskiem dłoni. To chwila na inspekcję wizualną i dotykową.
Szczelność szalunku to kolejny punkt obowiązkowej kontroli. Dokładnie oglądamy wszystkie połączenia między elementami szalunku (deski, panele, bloki izolacyjne). Poszukujemy wszelkich szczelin, przez które mógłby wyciekać zaczyn cementowy. Miejsca styku szalunku z podłożem, narożniki oraz przejścia instalacyjne są szczególnie narażone na nieszczelności i wymagają szczególnej uwagi. Ewentualne szczeliny należy bezzwłocznie uszczelnić przed betonowaniem – np. taśmą, pianką lub specjalistycznymi kitami. Lepiej zrobić to teraz, niż płakać nad rakiem w gotowej płycie.
Niezbędna jest również kontrola wnętrza szalunku przed wylaniem betonu. Musi być on czysty – usunięte wszelkie trociny, ziemia, kamienie czy inne zanieczyszczenia, które mogłyby osłabić strukturę betonu lub stworzyć puste przestrzenie. Sprawdzamy, czy zbrojenie jest prawidłowo ułożone (rozstaw prętów, zakładka, strzemiona, rozmieszczenie w stosunku do krawędzi szalunku, oparcie na podkładkach dystansowych). Weryfikujemy położenie i zamocowanie wszelkich elementów zatopionych w betonie, takich jak rury czy kotwy. To chwila na sprawdzenie detali, które po zalaniu będą już niedostępne. Diabeł tkwi w szczegółach, a w betonie w ich braku.
Formalne przekazanie szalunku do betonowania przez kierownika budowy lub inną osobę odpowiedzialną jest często ostatnim krokiem kontrolnym. Dokonuje się pisemnego odbioru, potwierdzającego zgodność wykonania szalunku z projektem i sztuką budowlaną. Taki dokument jest potwierdzeniem, że wszelkie niezbędne kontrole zostały przeprowadzone i szalunek jest gotowy do przyjęcia betonu. To formalność, która jednak ma swoje znaczenie w przypadku późniejszych dyskusji czy potencjalnych roszczeń.
W przypadku szalunku traconego, kontrola obejmuje również sprawdzenie prawidłowości montażu izolacji termicznej i hydroizolacji, jeśli są one częścią systemu lub układane są pod szalunkiem. Sprawdzamy ciągłość izolacji, szczelność połączeń między płytami lub blokami, prawidłowe uszczelnienie połączenia hydroizolacji z szalunkiem oraz zabezpieczenie hydroizolacji przed uszkodzeniami mechanicznymi np. podczas chodzenia po niej. Integralność tej warstwy jest kluczowa dla przyszłego komfortu użytkowania budynku i jego bilansu energetycznego. Zimna lub mokra posadzka to nic przyjemnego, a korygowanie tego po fakcie to ogromny kłopot i koszt.
Wreszcie, ostatnia chwila przed wjazdem betonomieszarek, to inspekcja wizualna całego obrysu szalunku raz jeszcze. Czy wszystko wygląda solidnie? Czy nie ma luźnych elementów? Czy zespół betonujący ma świadomość planowanej prędkości wylewania betonu i sposobu wibrowania? Ta ostatnia, całościowa ocena często wychwytuje drobiazgi, które umknęły podczas szczegółowej kontroli poszczególnych elementów. Lepiej dmuchać na zimne i sprawdzić siedem razy, niż raz pozwolić na katastrofę.
Właściwie przeprowadzona kontrola szalunku przed betonowaniem jest kluczowym elementem procesu budowy, który minimalizuje ryzyko wad wykonawczych, oszczędza czas i pieniądze, a przede wszystkim zapewnia trwałość i stabilność płyty fundamentowej. Zaniedbania na tym etapie potrafią odbić się czkawką przez długie lata, a naprawy fundamentu należą do najtrudniejszych i najdroższych. Lepiej więc poświęcić te kilkadziesiąt minut, a nawet kilka godzin na rygorystyczną kontrolę, niż ponosić konsekwencje niedbalstwa.
Każdy metr bieżący szalunku powinien być sprawdzony z uwagą. Czy podpory stoją stabilnie na podłożu? Czy nie ma ryzyka, że się zapadną lub przewrócą? Czy ściągi przechodzą przez odpowiednie miejsca i są prawidłowo zabezpieczone na końcach? Czy poszycie szalunku (deski, sklejka, panele) jest w dobrym stanie i nie ma uszkodzeń? Te proste pytania pomagają wykryć potencjalne słabe punkty, zanim wylejemy beton i utwardzimy nasze błędy na wieczność.
Czasami kierownik budowy lub inspektor nadzoru inwestorskiego może zażądać dodatkowych testów, na przykład próby obciążenia fragmentu szalunku, aby upewnić się co do jego wytrzymałości. Choć rzadkie w przypadku typowych płyt jednorodzinnych, przy dużych, niestandardowych konstrukcjach może to być uzasadnione. Podsumowując, kontrola szalunku to nie tylko formalność, to niezbędny element zarządzania ryzykiem na budowie. Bez niej, szansa na sukces jest jak rzut monetą, a przecież nie chcemy stawiać przyszłości naszego domu na szali, prawda?
--- Podsumowanie występowania frazy powiązanych z frazą: Płyta fundamentowa szalunek * Płyta fundamentowa szalunek: 1 wystąpień * szalowanie płyty fundamentowej: 1 wystąpień * szalunek pod płytę betonową: 1 wystąpień * szalunek płyty: 1 wystąpień * szalowania pod płytę: 1 wystąpień