Przekrój Płyty Fundamentowej: Warstwy i Budowa 2025
Zastanawiasz się, jak naprawdę wygląda płyta fundamentowa przekrój? Wyobraź sobie solidny, wielowarstwowy tort konstrukcyjny wmurowany głęboko w ziemię – to właśnie w skrócie jest jej budowa, od warstw kruszywa po zbrojony beton, a każda warstwa ma swoje ściśle określone zadanie, zapewniając stabilność i trwałość całego budynku.
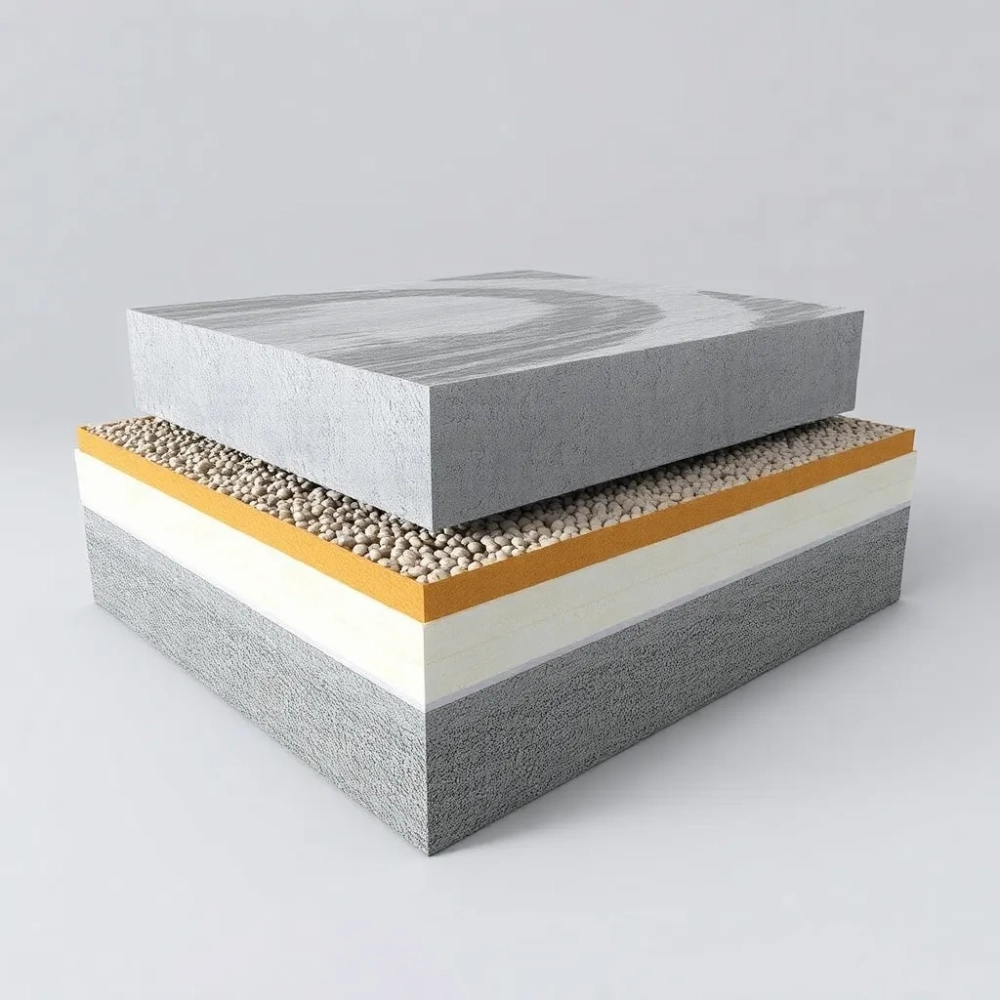
Przyglądając się bliżej temu, co kryje się pod powierzchnią, dostrzeżemy złożony system warstw, gdzie każdy milimetr ma znaczenie. Odpowiednie połączenie materiałów nośnych, izolacyjnych i hydroizolacyjnych tworzy przegrodę gotową przyjąć ciężar konstrukcji, jednocześnie chroniąc ją przed negatywnym wpływem gruntu i wilgoci.
Analizując typowe rozwiązania spotykane na placach budowy, możemy przedstawić ogólny obraz struktury płyty, choć finalny projekt zawsze powinien być dostosowany do konkretnych warunków i obciążeń.
Poniżej przedstawiamy zestawienie danych dotyczących przykładowego kosztu materiałów i czasu potrzebnego na realizację kluczowych etapów budowy takiej płyty dla standardowego domu jednorodzinnego o powierzchni około 100 m² zabudowy, co pozwoli lepiej zrozumieć skalę przedsięwzięcia.
Etap / Materiał | Szacunkowa Ilość | Przybliżony Koszt Materiałów (PLN) | Przybliżony Czas Wykonania (dni robocze) |
---|---|---|---|
Zdjęcie humusu i wykop (100 m², 30 cm) | ~30 m³ | 500 - 1500 (wywóz) | 1-2 |
Podbudowa piaskowo-żwirowa (100 m², 30 cm) | ~30 m³ | 1000 - 2500 | 1-2 (z zagęszczaniem) |
Izolacja przeciwwilgociowa (membrana PCV) | ~120 m² | 800 - 1500 | 0.5 |
Izolacja termiczna (XPS/EPS, 20 cm) | ~105 m² | 6000 - 10000 | 1-2 |
Zbrojenie (stal fi 12-16) | ~1.5 - 2.5 T | 8000 - 14000 | 1-2 |
Beton (C20/25 - C25/30, 100 m², 20 cm) | ~20 m³ | 6000 - 9000 | 0.5 - 1 (z pompowaniem) |
Razem (orientacyjnie) | - | 22300 - 38500 | 4-8 |
Dane przedstawione w tabeli dają pogląd na kluczowe elementy składowe kosztów materiałowych i czasu pracy, choć oczywiście nie uwzględniają wszystkich detali, jak choćby kosztów robocizny, wynajmu sprzętu czy drobniejszych materiałów.
Pamiętajmy, że podane kwoty są jedynie szacunkowe i mogą się znacznie różnić w zależności od lokalizacji, dostępności materiałów, specyfiki projektu oraz wybranego wykonawcy.
Analiza takich danych pozwala inwestorowi lepiej przygotować się finansowo i logistycznie do przedsięwzięcia, jakim jest wykonanie solidnej płyty fundamentowej.
Należy też podkreślić, że każdy z przedstawionych etapów wymaga precyzji i zgodności ze sztuką budowlaną, gdyż błędy na tym początkowym etapie mogą mieć katastrofalne skutki dla trwałości całego budynku.
Przygotowanie Gruntu i Wykonanie Podbudowy pod Płytę
Rozpoczęcie prac nad płytą fundamentową to moment zero dla każdego projektu budowlanego, a solidne fundamenty rodzą się nie w betonie, ale w dobrze przygotowanym gruncie.
Pierwszym, bezdyskusyjnie krytycznym krokiem jest dokładne badanie podłoża gruntowego, które ma na celu identyfikację jego nośności, poziomu wód gruntowych oraz obecności słabych, nienośnych warstw, takich jak torfy czy namuły – to trochę jak medyczne badanie pacjenta przed poważną operacją, żeby nie było niespodzianek.
Na tym etapie geolog pobiera próbki gruntu z różnych głębokości i lokalizacji, które następnie są analizowane w laboratorium pod kątem parametrów fizycznych i mechanicznych, a bez tej wiedzy wszelkie dalsze działania są czystą improwizacją na granicy błędu.
W zależności od wyników badań, projektant konstrukcji dobiera odpowiedni typ posadowienia, a w przypadku płyt fundamentowych kluczowe jest usunięcie wierzchniej, biologicznie czynnej warstwy, czyli humusu, zazwyczaj na głębokość od 20 do 30 centymetrów, co usuwa materiał organiczny, który uległby rozkładowi i spowodował nierównomierne osiadania, rujnując przyszłą podłogę.
Zdarza się, że grunt naturalny na danym terenie jest na tyle nośny i jednorodny (np. zbite piaski, żwiry), że po usunięciu humusu i odpowiednim wyrównaniu oraz zagęszczeniu można układać kolejne warstwy bezpośrednio na nim.
Jednak znacznie częściej niezbędne jest wykonanie stabilnej i nośnej podbudowy, która będzie równomiernie rozkładać obciążenia z płyty na szerszą powierzchnię gruntu oraz pełnić funkcje drenażowe – to swoisty amortyzator i filtr w jednym.
W tym celu dokonuje się wykopu o docelowej głębokości posadowienia, która jest ustalana w projekcie i zależy od m.in. strefy przemarzania gruntu dla danego regionu (w Polsce głębokość przemarzania waha się od 0.8 do nawet 1.4 metra, choć w przypadku płyt fundamentowych, dzięki izolacji termicznej pod i na płycie, możliwe jest posadowienie znacznie płyciej, często na głębokości zaledwie 30-50 cm poniżej poziomu terenu).
Na dnie wykopu układa się warstwę podsypki, która jest najczęściej wykonana ze żwiru, kruszywa łamanego (np. bazaltowego, granitowego) lub mieszaniny piasku i żwiru (tzw. pospółki) o określonej granulacji, np. od 0/31.5 mm do 0/63 mm w zależności od wymagań nośności i drenażu.
Grubość tej warstwy podsypki jest różna, ale typowo wynosi od 20 do 40 centymetrów, układana jest ona warstwami (np. 10-15 cm każda) i każda warstwa musi być solidnie zagęszczona mechanicznie, co jest kluczowe dla zapewnienia jej nośności i zminimalizowania przyszłych osiadań pod obciążeniem płyty i budynku.
Wskaźnik zagęszczenia, wyrażony jako stopień zagęszczenia IS lub Proctor (DPR/IPS), powinien być zgodny z wymaganiami projektowymi, a często wynosi co najmniej 0.98 IS dla warstw znajdujących się bezpośrednio pod płytą – to pokazuje precyzję, z jaką trzeba podejść do tego etapu, bo nawet minimalne niedociągnięcie może stać się piętą Achillesową konstrukcji.
Zagęszczanie najlepiej przeprowadzać przy optymalnej wilgotności materiału, ani za suchego (bo się nie zagęści), ani za mokrego (bo sprężystość wody utrudni zbicie ziaren), dlatego często warstwy podsypki są zraszane wodą przed użyciem zagęszczarki płytowej lub walca wibracyjnego.
Niektórzy wykonawcy stosują również warstwę chudego betonu (klasy C8/10) o grubości 5-10 cm bezpośrednio na zagęszczonej podbudowie kruszywowej – stanowi ona równe i stabilne podłoże dla dalszych prac, takich jak układanie izolacji termicznej i przeciwwilgociowej oraz zbrojenia, eliminując nierówności podbudowy i ułatwiając zachowanie wymaganych otulin betonu.
Podsumowując ten etap, możemy śmiało powiedzieć, że inwestycja w profesjonalne badanie gruntu i pedantyczne wykonanie podbudowy to nie wydatek, ale fundamentalna lokata, która procentuje stabilnością i brakiem problemów przez dekady.
Wykonanie podsypki z odpowiednią granulacją kruszywa i jej prawidłowe zagęszczenie wpływa także na skuteczność systemu drenażowego, umożliwiając swobodny przepływ wody opadowej i gruntowej pod płytą w kierunku drenażu obwodowego.
Czasem, na gruntach o niskiej nośności lub wysokim poziomie wód gruntowych, stosuje się dodatkowo geowłókniny lub geosiatki układane na dnie wykopu przed nasypaniem podsypki – mają one na celu separację warstw oraz wzmocnienie podłoża, co dodatkowo podnosi nośność konstrukcji pod przyszłą płytę fundamentową.
To przypomina wzmocnienie słabego podłoża siatką zbrojeniową, zanim zaczniemy budować na nim coś ciężkiego.
Dokładność wymiarowa wykopu i poziomu podbudowy jest krytyczna, ponieważ to one decydują o geometrycznym położeniu całej przyszłej płyty, a wszelkie odstępstwa mogą komplikować dalsze etapy prac, np. murowanie ścian.
Koszt materiałów na podbudowę, jak widzieliśmy w tabeli, stanowi znaczącą część budżetu, a cena kruszywa waha się np. od 40 do 80 PLN za tonę (w zależności od typu i dostawcy), co przy typowej gęstości nasypowej rzędu 1.6-1.7 T/m³ łatwo przeliczyć na kubiki – a przy dziesiątkach kubików potrzebnych pod średniej wielkości dom, szybko rośnie solidna kwota.
Ostatecznym sprawdzianem jakości wykonania podbudowy jest pomiar jej zagęszczenia metodami dynamicznymi (np. płyta dynamiczna VSS) lub statycznymi, co jest często wymagane przez inspektora nadzoru budowlanego – bez pozytywnego protokołu z takiego badania nie powinno się przechodzić do kolejnych etapów, a to sygnał dla inwestora, że każdy detal tego etapu jest ściśle kontrolowany.
Wiedza o gruncie i precyzja wykonania podbudowy to absolutne abecadło, bez którego solidna płyta fundamentowa pozostaje jedynie pobożnym życzeniem.
Wykonawca powinien również zadbać o odpowiednie zabezpieczenie wykopu przed deszczem i zamarzaniem, zwłaszcza jeśli prace mają trwać dłużej, aby uniknąć destabilizacji podłoża, które właśnie z takim mozołem przygotowano.
Prace ziemne wymagają użycia specjalistycznego sprzętu, od koparek, przez walce, po zagęszczarki wibracyjne, co także wpływa na koszt i czas realizacji tego etapu, a doświadczony operator koparki potrafi zdziałać cuda, minimalizując ilość urobku i precyzyjnie kształtując dno wykopu.
Błędy na etapie przygotowania gruntu i podbudowy są niezwykle trudne, a często niemożliwe do naprawienia po wylaniu płyty, dlatego to moment, w którym przysłowiowa "kropla potu" oszczędza "rzekę łez" i ogromne koszty w przyszłości.
Rola Izolacji Przeciwwilgociowej i Drenażu
Woda, ta sama, która jest źródłem życia, potrafi być największym wrogiem konstrukcji budowlanych, szczególnie tych posadowionych bezpośrednio na gruncie.
Dlatego absolutnie kluczowym elementem w przekroju płyty fundamentowej, tuż nad podbudową kruszywową (lub chudym betonem), jest skuteczna izolacja przeciwwilgociowa płyty fundamentowej, której zadaniem jest stworzenie nieprzepuszczalnej bariery oddzielającej wilgotne podłoże od betonu i izolacji termicznej płyty.
Najczęściej stosowanymi materiałami są folie z tworzyw sztucznych (np. grubości min. 0.5 mm), papy termozgrzewalne, a w bardziej wymagających warunkach geologicznych lub przy wysokim poziomie wód gruntowych, membrany bentonitowe lub specjalistyczne masy bitumiczne.
Materiał izolacyjny musi być ułożony starannie, tworząc szczelną "wannę", która obejmuje całą powierzchnię płyty, a jej brzegi muszą zostać wyprowadzone na ściany fundamentowe lub zewnętrzny obwód płyty powyżej poziomu gruntu docelowego – to kluczowy detal, bo nawet najmniejsza dziurka czy nieszczelność na połączeniu warstw jest jak nieszczelna tam, która w końcu puści.
Połączenia folii czy membrany (zakłady) muszą być solidnie zespolone, czy to przez zgrzewanie gorącym powietrzem, sklejanie specjalistycznymi taśmami (np. przy foliach PCV) czy zgrzewanie ogniem (przy papach termozgrzewalnych) – standardowy zakład powinien wynosić co najmniej 10-15 centymetrów, aby zapewnić pełną szczelność, nawet przy niewielkich ruchach gruntu czy osiadaniu konstrukcji.
Czasami pod izolację przeciwwilgociową układana jest dodatkowo geowłóknina ochronna, która zapobiega uszkodzeniu membrany przez ostre krawędzie kruszywa w podbudowie podczas kolejnych etapów prac – to niewielki koszt w porównaniu do ryzyka przebicia i konsekwencji zawilgocenia izolacji termicznej i samej płyty.
Problem wilgoci to nie tylko woda gruntowa, ale także opady atmosferyczne, które mogą gromadzić się wokół budynku, szczególnie na słabo przepuszczalnych gruntach gliniastych.
Tutaj do gry wchodzi system drenażu opaskowego, który ma za zadanie aktywnie odprowadzać nadmiar wody z otoczenia budynku, zanim zdąży ona naciskać na ściany fundamentowe czy próbować przedostać się pod płytę.
Drenaż obwodowy wykonuje się zwykle na poziomie ławy fundamentowej lub spodu płyty fundamentowej, a w przypadku płyt zazwyczaj układa się go wzdłuż zewnętrznego obwodu podsypki, na głębokości co najmniej 30-50 cm poniżej jej spodu, zapewniając grawitacyjny spadek w kierunku studzienek chłonnych lub kanalizacji deszczowej (o ile jest to zgodne z lokalnym prawem i możliwościami technicznymi).
System drenażowy składa się zazwyczaj z perforowanych rur drenarskich o średnicy 80-100 mm, ułożonych na warstwie przepuszczalnego kruszywa (np. żwiru płukanego frakcji 8/16 mm lub 16/32 mm) i zasypanych tym samym kruszywem do odpowiedniej wysokości (zazwyczaj około 20-30 cm nad rurą).
Całość obsypki kruszywowej musi być owinięta geowłókniną filtracyjną – to absolutna konieczność, która zapobiega zamuleniu porów kruszywa i perforacji rur przez drobne cząstki gruntu z otoczenia, co mogłoby szybko unieruchomić cały system – bez geowłókniny to trochę jak filtr do kawy bez papieru, wszystko przelatuje.
Minimalny spadek rur drenarskich w kierunku studzienek wynosi 0.5-1%, co może wydawać się niewiele, ale jest niezbędne do zapewnienia swobodnego spływu wody, a jego prawidłowe wykonanie wymaga precyzyjnego niwelacji.
Studzienki rewizyjne na każdym narożniku i na długich prostych odcinkach drenażu (nie rzadziej niż co 25-30 metrów) są niezbędne do regularnego płukania i inspekcji systemu – drenaż to nie instalacja bezobsługowa, trzeba o niego dbać, żeby działał efektywnie latami.
Skuteczny drenaż odciąża izolację przeciwwilgociową od ciągłego naporu wody, tworząc wokół fundamentu strefę o niższym poziomie wilgotności – to trochę jak zewnętrzny parasol dla wnętrza domu.
Na terenach o wysokim poziomie wód gruntowych, oprócz drenażu opaskowego, konieczne może być zastosowanie bardziej złożonych systemów, takich jak drenaż powierzchniowy (zbierający wodę z powierzchni terenu) lub systemy pomp drenażowych aktywnie odwadniających obszar fundamentu – to rozwiązania dla trudnych przypadków, gdzie standardowy drenaż grawitacyjny nie wystarczy.
W przypadku płyty fundamentowej dobrze wykonana izolacja przeciwwilgociowa i funkcjonalny drenaż są fundamentem zdrowego klimatu wewnętrznego, chroniąc budynek przed wilgocią podciągającą kapilarnie oraz naporem wody na konstrukcja płyty fundamentowej od spodu i z boków.
Zaniedbanie tego etapu może prowadzić do zawilgocenia ścian, powstawania pleśni, a w skrajnych przypadkach nawet do uszkodzeń konstrukcji przez cykle zamarzania i rozmarzania wody w materiałach budowlanych – to jak proszenie się o kłopoty, które drogo kosztują.
Koszt wykonania izolacji przeciwwilgociowej (materiał plus robocizna) dla domu 100 m² zabudowy to zazwyczaj kilka tysięcy złotych, natomiast koszt kompletnego systemu drenażowego (rury, kruszywo, geowłóknina, studzienki, robocizna) to wydatek rzędu kilku do kilkunastu tysięcy złotych, w zależności od długości obwodu drenażu i złożoności systemu odwodnienia – warto przeznaczyć te pieniądze, bo "suche" fundamenty to podstawa.
Mówiąc wprost, w walce z wilgocią nie ma miejsca na kompromisy; precyzja, właściwe materiały i solidne wykonanie to jedyna droga do spokoju ducha.
Kluczowa Izolacja Termiczna Płyty Fundamentowej
Współczesne budownictwo kładzie ogromny nacisk na efektywność energetyczną, a izolacja termiczna w przekroju płyty fundamentowej odgrywa w tym aspekcie rolę pierwszoplanową.
Płyta fundamentowa stanowi dużą powierzchnię przegrody oddzielającą wnętrze budynku od gruntu, który, nawet głęboko pod powierzchnią, utrzymuje stosunkowo niską i stabilną temperaturę (w okolicach 8-12°C w Polsce) przez cały rok – bez odpowiedniej izolacji cieplnej dochodziłoby do znacznych strat energii z ogrzewanych pomieszczeń do gruntu.
Wyobraź sobie tę płytę jako wielki radiator oddający ciepło w zimie i przyjmujący chłód w lecie – to niezbyt optymalna sytuacja dla naszego komfortu cieplnego i portfela, prawda?
Dlatego bezpośrednio na warstwie izolacji przeciwwilgociowej układa się płyty termoizolacyjne, które skutecznie minimalizują mostki termiczne i ograniczają przepływ ciepła, tworząc ciepły spód budynku.
Najczęściej stosowanymi materiałami do izolacji termicznej płyt fundamentowych są polistyren ekspandowany o zwiększonej twardości (EPS, np. o parametrze CS(10) >= 100 kPa) lub polistyren ekstrudowany (XPS) – oba materiały charakteryzują się dobrą izolacyjnością i odpornością na wilgoć, choć XPS ma zazwyczaj nieco lepsze parametry mechaniczne i jest mniej nasiąkliwy, co czyni go często pierwszym wyborem w trudniejszych warunkach.
Grubość warstwy izolacji termicznej zależy od wymagań energetycznych stawianych budynkowi (określonych w przepisach Prawie Budowlanym i warunkach technicznych, np. WT 2021, które narzucają współczynnik przenikania ciepła dla podłogi na gruncie poniżej 0.3 W/m²K) oraz od strefy klimatycznej, w której znajduje się budynek.
W praktyce oznacza to konieczność stosowania izolacji o znacznych grubościach, często wynoszących 20-30 cm EPS 100 lub 15-25 cm XPS pod płytą, a często dodaje się jeszcze warstwę 5-10 cm izolacji na wierzchu płyty, pod wylewką podłogową, co tworzy tzw. "ciepły fundament" i eliminuje mostki termiczne na połączeniu płyty ze ścianami.
Płyty izolacyjne układa się zazwyczaj w co najmniej dwóch warstwach o łącznej grubości docelowej, z przesunięciem spoin (układ na "mijankę"), co zapobiega powstawaniu pionowych kanałów, którymi mogłoby uciekać ciepło lub przedostawać się wilgoć.
Spoiny między płytami powinny być jak najściślej dopasowane, aby uniknąć nieszczelności, a producenci materiałów izolacyjnych oferują często płyty frezowane (na pióro i wpust), co dodatkowo poprawia szczelność połączeń – to drobny detal, który jednak ma znaczenie dla finalnej efektywności izolacji.
Na warstwie izolacji termicznej, tuż pod betonową płytą konstrukcyjną, często układa się kolejną warstwę folii budowlanej lub membrany – ma ona kilka funkcji: chroni izolację termiczną przed bezpośrednim kontaktem z wilgotnym betonem podczas wylewania, zapobiega "wyciekaniu" zaczynu cementowego między spoiny izolacji oraz pełni dodatkową rolę izolacji przeciwwilgociowej lub paroizolacyjnej, w zależności od specyfiki projektu.
W przypadku „ciepłej płyty fundamentowej”, gdzie izolacja termiczna stanowi dolne szalowanie i pozostaje na stałe pod betonem, dobór materiału izolacyjnego o odpowiedniej wytrzymałości na ściskanie jest absolutnie krytyczny – materiał musi wytrzymać ciężar mokrego betonu, zbrojenia oraz obciążenia w trakcie budowy, bez znaczącej deformacji, co mogłoby doprowadzić do pęknięć płyty betonowej (parametr CS(10) min. 100 kPa, a dla budynków z ciężkimi ścianami murowanymi często zaleca się nawet 150 kPa).
Koszt materiałów izolacyjnych stanowi znaczącą pozycję w budżecie budowy płyty, jak widać w tabeli – dla domu 100 m² może to być kwota rzędu 6000-10000 PLN, a w przypadku grubszej izolacji czy zastosowania XPS, nawet więcej, np. 15-20 tysięcy PLN.
Pomimo kosztu, dobrze wykonana izolacja termiczna zwraca się przez lata w postaci niższych rachunków za ogrzewanie i chłodzenie, poprawia komfort termiczny (ciepła podłoga) i jest zgodna ze współczesnymi standardami energooszczędnego budownictwa – to inwestycja w przyszłe oszczędności.
Ważne jest, aby wykonawca dokładnie docinał i dopasowywał płyty izolacyjne, szczególnie w miejscach przejść instalacyjnych (rury kanalizacyjne, przyłącza wody), aby minimalizować ryzyko powstawania mostków termicznych w tych newralgicznych punktach.
Zabezpieczenie izolacji przed uszkodzeniami mechanicznymi i promieniami UV (jeśli prace mają potrwać dłużej) jest równie ważne – to warstwa delikatna, która łatwo ulega degradacji.
W niektórych projektach stosuje się również warstwę keramzytu lub innego lekkiego kruszywa izolacyjnego pod płytą, jednak najczęściej spotykanym i najbardziej efektywnym rozwiązaniem jest układanie warstw EPS lub XPS bezpośrednio na przygotowanym podłożu – po prostu jest to prostsze i bardziej mierzalne pod kątem parametrów izolacyjności.
Zapewnienie ciągłości i odpowiedniej grubości izolacji termicznej pod płytą to nie fanaberia, a kluczowy element zapewniający zgodność z normami energetycznymi i komfort użytkowania budynku przez dekady.
Konstrukcja Żelbetowej Płyty Fundamentowej
Sedno płyty fundamentowej stanowi jej żelbetowy "kręgosłup" – to ta warstwa, która przenosi wszystkie obciążenia z konstrukcji budynku i równomiernie rozkłada je na przygotowane podłoże, będąc jednocześnie podłogą na gruncie.
Konstrukcja żelbetowa płyty fundamentowej składa się z dwóch głównych elementów: betonu i zbrojenia stalowego, które wspólnie tworzą kompozyt o wysokiej wytrzymałości na ściskanie (beton) i rozciąganie (stal).
Projektant konstrukcji dokładnie oblicza wymaganą klasę betonu oraz średnice i rozstaw prętów zbrojeniowych, biorąc pod uwagę przewidywane obciążenia (ciężar własny budynku, obciążenia użytkowe, śnieg, wiatr), warunki gruntowe, a także specyfikę układu konstrukcyjnego budynku (np. rozpiętości ścian nośnych).
Najczęściej stosowane klasy betonu dla płyt fundamentowych w domach jednorodzinnych to C20/25 lub C25/30 – oznaczenie C20/25 oznacza, że beton po 28 dniach twardnienia osiągnął minimalną wytrzymałość charakterystyczną na ściskanie 20 MPa dla próbek walcowych i 25 MPa dla próbek sześciennych, to standardowa wartość zapewniająca odpowiednią nośność.
W przypadku płyt, które będą stanowiły jednocześnie posadzkę np. garażu czy kotłowni, lub przy budynkach o skomplikowanej konstrukcji, mogą być wymagane wyższe klasy betonu.
Ważnym parametrem betonu dostarczanego na budowę jest jego konsystencja (klasa ścisłości), wyrażana np. jako S3 lub S4 – im wyższa klasa, tym beton bardziej płynny, co ułatwia jego układanie i zagęszczanie między gęstym zbrojeniem, jednak zbyt płynny beton może prowadzić do segregacji kruszywa i obniżenia wytrzymałości.
Zbrojenie płyty fundamentowej najczęściej stanowi podwójna siatka z prętów stalowych (np. gatunku B500SP, popularnie zwana stalą spawaną, lub prętów zgrzewanych) – jedna siatka umieszczana jest w dolnej części przekroju, a druga w górnej, co pozwala na przenoszenie naprężeń rozciągających powstających zarówno w wyniku zginania płyty pod obciążeniem, jak i np. od osiadania gruntu (co prawda minimalnego przy dobrej podbudowie, ale naprężenia i tak występują).
Typowe średnice prętów stosowanych w zbrojeniu głównym płyty to fi 12 lub fi 16 mm, układanych w siatce o oczkach np. 15x15 cm lub 20x20 cm, zgodnie z projektem – zdarzają się również pręty fi 10 lub fi 14, ale to fi 12 i fi 16 są standardem dla płyt w domach jednorodzinnych.
Pręty zbrojeniowe muszą być podniesione na specjalnych dystansach lub podkładkach (np. plastikowych "jeżykach" lub betonowych kostkach) tak, aby znajdowały się w odpowiedniej wysokości w przekroju płyty i były całkowicie otoczone betonem – minimalna otulina betonu, czyli warstwa betonu między powierzchnią pręta a zewnętrzną powierzchnią płyty, wynosi zazwyczaj 3-5 cm, chroni to stal przed korozją i zapewnia współpracę z betonem.
Górna siatka zbrojeniowa jest podpierana na specjalnych łącznikach dystansowych (tzw. "pajączkach" lub zbrojeniu poprzecznym), które utrzymują ją w odpowiedniej odległości od dolnej siatki, zapewniając wymaganą wysokość przekroju żelbetowego.
Układanie zbrojenia to precyzyjna praca, która wymaga odczytania rysunków zbrojeniowych i prawidłowego rozmieszczenia prętów, zakładów (miejsc połączenia prętów) oraz wszystkich dodatkowych elementów zbrojenia, takich jak zbrojenie krawędzi, wzmocnienia pod słupami czy ścianami nośnymi, czy też specjalne kosze zbrojeniowe wokół otworów instalacyjnych – każdy szczegół ma znaczenie.
Całość zbrojenia powinna być związana drutem wiązałkowym, co zapobiega przesunięciom prętów podczas betonowania – to nie jest element konstrukcyjny, ale organizacyjny, który utrzymuje zbrojenie w zaplanowanej pozycji.
Grubość samej żelbetowej płyty fundamentowej dla standardowego domu jednorodzinnego waha się zazwyczaj od 15 do 25 centymetrów, w zależności od obciążeń i rozpiętości – ta grubość wynika bezpośrednio z obliczeń statycznych i zapewnia sztywność konstrukcji.
Betonowanie płyty to etap, który wymaga dobrej organizacji – beton dostarczany jest najczęściej z betoniarni za pomocą betonowozów i podawany na miejsce wylewania za pomocą pompy do betonu, co pozwala na szybkie i równomierne wypełnienie całego szalunku i szczelin między zbrojeniem.
Podczas betonowania niezwykle ważne jest prawidłowe zagęszczenie betonu za pomocą wibratorów buławowych – wibracja usuwa pęcherzyki powietrza uwięzione w mieszance betonowej, co zapobiega powstawaniu raków (pustek w betonie) i zapewnia pełne otoczenie zbrojenia, podnosząc finalną wytrzymałość i trwałość elementu – niedostateczne zagęszczenie betonu to prosty przepis na słaby fundament.
Powierzchnia wylanej płyty powinna zostać wyrównana i zatarta (np. mechanicznie zacieraczkami talerzowymi), aby uzyskać gładką i równą powierzchnię, która w przyszłości będzie stanowić podkład pod posadzki właściwe.
Po związaniu betonu, czyli po kilku godzinach od wylewania, rozpoczyna się kluczowy etap pielęgnacji betonu – przez pierwsze dni beton musi być chroniony przed zbyt szybkim wysychaniem (np. przez zraszanie wodą, przykrycie folią budowlaną, matami słomianymi lub użycie preparatów do pielęgnacji betonu), co zapobiega pęknięciom skurczowym i zapewnia osiągnięcie projektowanej wytrzymałości, proces hydratacji cementu wymaga wody, nie można mu jej odebrać zbyt wcześnie.
Na całkowite związanie betonu i osiągnięcie pełnej wytrzymałości (tzw. wytrzymałość normowa po 28 dniach) trzeba odczekać, choć dalsze prace budowlane, takie jak murowanie ścian, można często rozpocząć już po kilku dniach, gdy beton osiągnie wystarczającą wytrzymałość wczesną (np. 50-70% wytrzymałości normowej, w zależności od wytycznych projektowych i warunków atmosferycznych).
Całkowity koszt wykonania żelbetowej płyty fundamentowej to połączenie kosztów materiałów (beton, stal – patrz tabela, to znaczące pozycje) oraz kosztów robocizny (szalowanie, układanie zbrojenia, betonowanie, zacieranie, pielęgnacja), wynajmu sprzętu (pompa do betonu, wibratory, zacieraczki) i transportu.
Analizując przekrój budowy płyty fundamentowej na etapie konstrukcji żelbetowej, widzimy warstwę o ogromnej odpowiedzialności – to ona dźwiga cały dom, a jej solidność jest bezpośrednim odzwierciedleniem jakości materiałów, precyzji zbrojenia i poprawności betonowania i pielęgnacji.
Zdarza się, że na tym etapie wykonuje się już przepusty instalacyjne przez płytę (np. dla rur kanalizacyjnych, przyłączy wody czy elektryczności), wstawiając specjalne tuleje ochronne, które zostaną uszczelnione po przejściu instalacji, co ułatwia późniejszą pracę hydraulikom czy elektrykom.
Poprawność wykonania zbrojenia często jest sprawdzana przez inspektora nadzoru lub kierownika budowy przed samym betonowaniem, a po wylaniu betonu często pobiera się próbki do badań laboratoryjnych, aby potwierdzić, że dostarczony beton spełnia wymagania projektowej klasy – to standardowe procedury kontrolne, które dają pewność co do jakości finalnego elementu.
Z perspektywy inwestora, widząc tę warstwę, wie, że przeszedł kolejny milowy krok, który na lata zdefiniuje trwałość jego domu.