Prefabrykowana Płyta Fundamentowa - Nowoczesne Rozwiązanie Budowlane 2025
Gdy stajemy przed wyzwaniem budowy domu czy obiektu komercyjnego, etap posadowienia jest fundamentem dosłownie i w przenośni. Tradycyjne metody często kojarzą się z długotrwałymi pracami ziemnymi, skomplikowanym szalowaniem i wylewaniem betonu wprost na placu budowy – procesem żmudnym i zależnym od pogody. Ale co jeśli istnieje rozwiązanie, które radykalnie skraca ten czas, jednocześnie oferując niezrównaną precyzję i trwałość? To właśnie wprowadza do gry Prefabrykowana płyta fundamentowa – gotowe rozwiązanie inżynieryjne, które transformuje proces tworzenia podstaw dla każdej budowli w szybki i kontrolowany montaż.
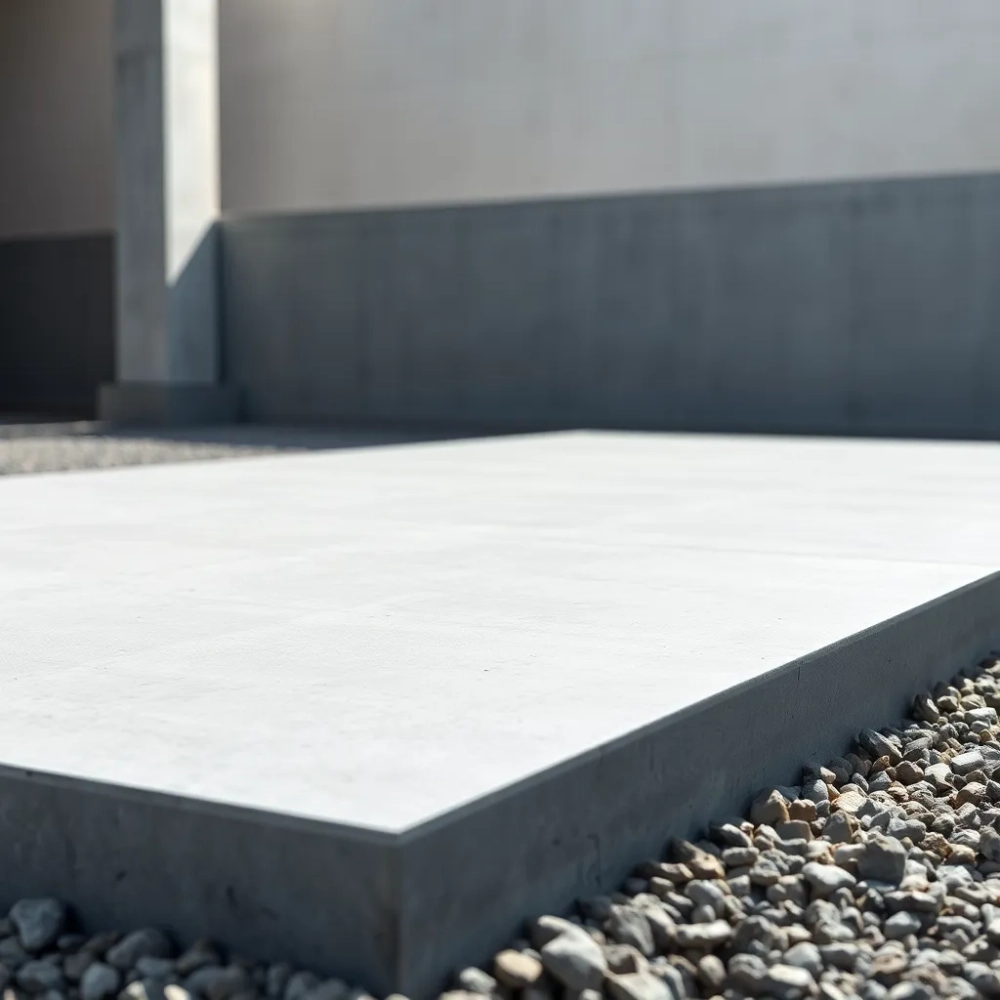
Aby w pełni docenić skalę innowacji, przyjrzyjmy się, jak różne metody posadowienia wypadają w praktyce. Poniższe zestawienie porównuje kluczowe wskaźniki, dając pogląd na to, co zyskujemy, decydując się na krok w stronę prefabrykacji.
Aspekt | Tradycyjny Ławy i Ściany Fundamentowe | Tradycyjna Płyta Monolityczna | Prefabrykowana Płyta Fundamentowa |
---|---|---|---|
Typowy czas wykonania (etap posadowienia dla 100m² domu) | 3-5 tygodni | 2-4 tygodnie | 3-7 dni |
Zapotrzebowanie na prace 'mokre' na placu | Bardzo wysokie (wylewanie betonu w wykopach i szalunkach) | Wysokie (wylewanie całej płyty) | Niskie (jedynie zaprawa w spoinach, jeśli występuje) |
Wymagania co do warunków atmosferycznych podczas głównych prac | Duża zależność (deszcz, mróz mogą zatrzymać prace) | Duża zależność (deszcz, mróz mogą zatrzymać prace) | Niska zależność (montaż mniej wrażliwy na opady; produkcja w hali) |
Precyzja wykonania (szczególnie płaskości powierzchni pod ściany) | Umiarkowana do Wysokiej (zależy od ekipy i szalowania) | Wysoka (przy dobrej ekipie i wibracji) | Bardzo Wysoka (fabryczne tolerancje, typowo +/- 5 mm) |
Potencjał integracji z izolacją termiczną | Możliwe, ale często skomplikowane detale (mostki termiczne) | Możliwe (izolacja pod lub na płycie), detale na krawędziach wymagają uwagi | Wysoki (izolacja często integralną częścią prefabrykatu) |
Minimalizacja prac ziemnych (głębokość wykopu do poziomu posadowienia) | Zwykle poniżej strefy przemarzania, ok. 1-1.4 m | Możliwe na mniejszej głębokości, jeśli grunt nośny jest płytko | Często minimalna, przygotowanie jedynie podłoża nośnego na poziomie 'zero' lub blisko niego |
Powyższe porównanie to coś więcej niż tylko suche dane; to obraz fundamentalnej zmiany paradygmatu w budownictwie. Zastosowanie prefabrykowanej płyty fundamentowej przenosi kluczowe, czasochłonne i wrażliwe na błędy etapy z placu budowy do kontrolowanej hali produkcyjnej. Efekt? Fundament, który nie tylko powstaje w rekordowo krótkim czasie, ale charakteryzuje się powtarzalną, fabryczną jakością, niezależną od kaprysów pogody czy dostępności wysoce specjalistycznych ekip "mokrych" na placu.
Zalety i Korzyści Płyt Fundamentowych Prefabrykowanych
Myśląc o innowacyjnych rozwiązaniach w budownictwie, często zapominamy o jego samym fundamencie. A to właśnie tu, w tej pozornie prozaicznej materii, technologia prefabrykacji przynosi rewolucyjne zmiany.
Prefabrykowana płyta fundamentowa jest jaskrawym przykładem takiego postępu, łącząc w sobie to, co najlepsze z dwóch światów: wrodzoną solidność konstrukcji betonowej z niespotykaną dotąd szybkością realizacji. Jest to rozwiązanie, które wykracza poza prostą alternatywę dla tradycyjnych ław czy płyt monolitycznych, oferując cały pakiet korzyści.
Pierwszą i najczęściej wymienianą zaletą jest ekspresowe tempo prac. Gdy tradycyjne fundamenty wymagają tygodni na wykop, szalowanie, zbrojenie, wylewanie i wiązanie betonu, płyta prefabrykowana jest montowana w ciągu zaledwie kilku dni, a nierzadko nawet w jeden dzień roboczy dla standardowego domu jednorodzinnego.
Wyobraź sobie, że w poniedziałek teren budowy jest jeszcze pusty, a w piątek masz gotowy fundament, gotowy do dalszych etapów budowy. To skrócenie czasu posadowienia przekłada się bezpośrednio na przyspieszenie całej inwestycji, redukując koszty pośrednie, takie jak wynajem sprzętu czy koszty dozoru.
Równie ważna, a w niektórych projektach nawet kluczowa, jest jakość i precyzja wykonania, które gwarantuje produkcja w kontrolowanych warunkach fabrycznych. Elementy są odlewane w stalowych formach z użyciem betonu o ściśle określonych parametrach, wibrowane i pielęgnowane w optymalnych warunkach.
To zapewnia jednolitą strukturę betonu, precyzyjne umiejscowienie zbrojenia (często przygotowywanego na zautomatyzowanych liniach) oraz idealnie płaską powierzchnię górną, która jest gotowa do bezpośredniego murowania ścian czy układania kolejnych warstw izolacji i podłogi.
Standardowa odchyłka w płaskości takiej płyty to często zaledwie +/- 5 mm na dużej powierzchni, co jest trudne do osiągnięcia wylewając beton na placu budowy, nawet przez najlepszą ekipę. Ta precyzja minimalizuje późniejsze prace wyrównujące, oszczędzając czas i materiały na dalszych etapach budowy.
Płyta prefabrykowana jest również często projektowana jako element systemu zintegrowanego z izolacją termiczną. Izolacja obwodowa (tzw. "spódnica" lub izolacja upstandu krawędziowego) oraz izolacja pod płytą (np. gruba warstwa XPS lub PIR o grubości 100-300 mm) mogą być montowane fabrycznie lub projektowo zintegrowane, co eliminuje mostki termiczne i znacznie poprawia charakterystykę energetyczną budynku od samego początku.
Dla domów energooszczędnych, pasywnych, a także budynków z ogrzewaniem podłogowym na całej powierzchni, jest to ogromna zaleta, pozwalająca uzyskać bardzo niskie współczynniki przenikania ciepła U już na etapie fundamentu (np. U<0.15 W/(m²K)).
Integracja instalacji również jest prostsza. Kanały i przepusty na rury kanalizacyjne, wodne, elektryczne czy rekuperacyjne mogą być precyzyjnie zaplanowane i wbudowane w element prefabrykowany już na etapie produkcji.
Na placu budowy oznacza to koniec z kuciem w świeżym betonie czy improwizowanym układaniem rur; wszystko ma swoje miejsce zgodnie z projektem, gotowe do podłączenia.
Warto wspomnieć o zmniejszeniu ilości prac "mokrych" na placu. Ogranicza się je do przygotowania podłoża i ewentualnie fugowania połączeń między elementami prefabrykowanymi.
To oznacza mniejsze zużycie wody na budowie, mniej betonu do wylewania (a co za tym idzie, mniejszy ślad węglowy związany z transportem betonu) oraz czystszy i bardziej uporządkowany plac budowy, co wpływa na bezpieczeństwo pracy i ogólną estetykę.
Minimalizacja robót ziemnych to kolejna korzyść. Często posadowienie na prefabrykowanej płycie fundamentowej wymaga jedynie przygotowania równego podłoża nośnego, co pozwala ograniczyć głębokość wykopu w porównaniu do tradycyjnych ław fundamentowych.
Ma to znaczenie szczególnie w trudnych warunkach gruntowych lub na działkach o wysokim poziomie wód gruntowych, gdzie głębokie wykopy generowałyby dodatkowe koszty na zabezpieczenie czy odwodnienie.
W kontekście zrównoważonego budownictwa, produkcja prefabrykatów w hali pozwala na lepszą kontrolę zużycia surowców, recykling odpadów poprodukcyjnych oraz minimalizację strat materiałów, które często występują na tradycyjnym placu budowy.
Podsumowując, zalety prefabrykowanej płyty fundamentowej to symfonia szybkości, precyzji, jakości i potencjału termoizolacyjnego, które wspólnie tworzą nowoczesne, efektywne i ekologiczne posadowienie dla szerokiej gamy budynków. To inwestycja w spokój i pewność solidnych fundamentów.
Wybór tej technologii to decyzja strategiczna, która wpływa nie tylko na najniższą warstwę budynku, ale rzutuje na cały harmonogram, budżet i ostateczną jakość energetyczną i strukturalną powstającej nieruchomości. Nie jest to tylko alternatywa, to krok naprzód.
Przygotowanie podłoża, precyzyjny transport i doświadczona ekipa montażowa to klucz do sukcesu, ale sam element prefabrykowany jest już gotowym, sprawdzonym produktem opuszczającym bramy fabryki.
Dzięki tej standaryzacji i kontroli produkcji, inwestor zyskuje pewność parametrów, co jest bezcenne w obliczu rosnących wymagań dotyczących jakości wykonania w budownictwie.
Redukcja mostków termicznych jest szczególnie ważna w dobie rosnących cen energii i dążenia do budowania obiektów o niemal zerowym zapotrzebowaniu na energię pierwotną.
Integracja izolacji termicznej w płycie fundamentowej jest rozwiązaniem eleganckim i wysoce efektywnym, znacznie łatwiejszym do poprawnego wykonania niż skomplikowane systemy izolacji przy tradycyjnych ławach i ścianach fundamentowych.
Proces Produkcji i Montażu Płyty Fundamentowej Prefabrykowanej
Prześledźmy ścieżkę płyty fundamentowej prefabrykowanej – od koncepcji projektowej aż po jej finalne miejsce na placu budowy. To proces, który w dużej mierze przypomina produkcję przemysłową z dokładnością zegarka, a nie tradycyjną pracę rzemieślniczą na wolnym powietrzu.
Wszystko zaczyna się od indywidualnego projektu. Każda prefabrykowana płyta fundamentowa jest "szyta na miarę" pod konkretny budynek i konkretne warunki gruntowe działki. Projektanci określają dokładne wymiary, grubość płyty (typowo od 180 mm do nawet 300 mm w zależności od obciążeń), rozmieszczenie i specyfikację zbrojenia, lokalizację wszelkich przepustów i rur instalacyjnych, a także detale krawędziowe.
Projekt uwzględnia obciążenia od konstrukcji budynku, rodzaj gruntu, strefę przemarzania i wymagania termoizolacyjne. Na tej podstawie powstaje dokumentacja techniczna dla fabryki.
W hali produkcyjnej pierwszy etap to przygotowanie formy. Do produkcji płyt fundamentowych używa się zazwyczaj precyzyjnych stalowych form, które gwarantują powtarzalność wymiarową i gładkość powierzchni elementów. Formy są starannie czyszczone i przygotowywane przed każdym odlewem.
Następnie w formie układane jest zbrojenie. W nowoczesnych zakładach prefabrykacji zbrojenie często tworzone jest na zautomatyzowanych liniach, co zapewnia niezwykłą dokładność gięcia i spawania elementów. Układane jest w formie zgodnie z projektem, podpierane dystansami, aby zapewnić odpowiednie otulenie betonem (minimalna grubość otuliny betonu w elementach zewnętrznych wynosi zazwyczaj 25-40 mm).
Jednym z kluczowych etapów jest produkcja betonu. Betoniarnia w zakładzie prefabrykacji działa pod ścisłą kontrolą jakości. Stosowane są mieszanki betonowe o ściśle określonym składzie, wysokiej wytrzymałości (np. beton klasy C30/37 lub C35/45) i odpowiedniej konsystencji. Dodatki chemiczne zapewniają optymalne właściwości betonu, takie jak płynność, odporność na mróz czy szybkie wiązanie.
Beton jest transportowany do formy i wylewany, a następnie starannie wibrowany – mechanicznie lub stołem wibracyjnym – aby usunąć pęcherze powietrza i zagęścić masę. Wibracja jest kluczowa dla uzyskania wysokiej wytrzymałości i mrozoodporności betonu.
Po wylaniu i wstępnym związaniu betonu, elementy przechodzą proces pielęgnacji (dojrzewania) w kontrolowanych warunkach temperatury i wilgotności. Może to odbywać się w specjalnych komorach grzewczych, które przyspieszają proces utwardzania betonu, pozwalając na szybsze rozformowanie elementu i przygotowanie formy do kolejnego odlewu.
Kontrola jakości towarzyszy każdemu etapowi produkcji. Od sprawdzenia zgodności projektu ze specyfikacją, przez jakość użytych materiałów (cement, kruszywo, stal), parametry świeżej i stwardniałej mieszanki betonowej (badania wytrzymałości na ściskanie kostek sześciennych), po finalne sprawdzenie wymiarów gotowego elementu i położenia wbudowanych detali (np. gwintów, kotew, przepustów).
Gotowa płyta, po uzyskaniu wymaganej wytrzymałości, jest magazynowana do czasu transportu. Do transportu wykorzystuje się specjalistyczne samochody niskopodwoziowe. Elementy o dużych wymiarach wymagają często transportu ponadnormatywnego i specjalnych pozwoleń.
Transport na plac budowy jest logistycznie skomplikowany i wymaga koordynacji. Elementy są często dostarczane w kolejności, w jakiej będą montowane, aby zminimalizować potrzebę ich przesuwania na ograniczonej przestrzeni placu.
Montaż na placu budowy zaczyna się od przygotowania podłoża. Teren musi być starannie wyrównany do projektowanego poziomu posadowienia i odpowiednio zagęszczony. Często stosuje się warstwę pospółki lub chudego betonu jako podkład, na którym układana jest np. warstwa izolacji termicznej.
Na tak przygotowanym podłożu, za pomocą ciężkiego dźwigu (typowa płyta o wymiarach 10x12 m może ważyć kilkadziesiąt ton; element ściany prefabrykowanej do upstandu może ważyć 5-15 ton), płyty są precyzyjnie osadzane na miejscu. Kluczowe jest zachowanie odpowiedniej płaskości i poziomu całej konstrukcji.
Jeśli płyta składa się z kilku segmentów, są one łączone na placu budowy. Połączenia między elementami mogą być zalewane specjalną zaprawą o wysokiej wytrzymałości i minimalnym skurczu. W zależności od projektu, mogą występować również połączenia mechaniczne, np. na bazie śrub lub spawane blachy montażowe.
Rury instalacyjne, które były wbudowane w płytę lub wyprowadzone poza jej obrys, są na tym etapie łatwo dostępne do podłączenia z systemami wewnętrznymi budynku i zewnętrznymi przyłączami. Często przed zalaniem spoin, sprawdzana jest szczelność systemu kanalizacyjnego.
Cały proces montażu typowej płyty fundamentowej dla domu jednorodzinnego, od przyjazdu pierwszego transportu po ułożenie ostatniego elementu i ewentualne fugowanie, trwa zazwyczaj od jednego do maksymalnie kilku dni, zależnie od skomplikowania projektu i wielkości budynku.
Ta szybkość montażu to jedna z głównych przewag prefabrykacji, pozwalająca rozpocząć budowę ścian, a następnie dachu i reszty konstrukcji, znacznie szybciej niż w przypadku metod tradycyjnych. To jak postawienie gigantycznego klocka Lego, który jest perfekcyjnie wykonanym elementem konstrukcyjnym.
Rodzaje i Elementy Składowe Prefabrykowanej Płyty Fundamentowej
Mówiąc o prefabrykowanej płycie fundamentowej, mamy na myśli najczęściej gotowy, monolityczny lub segmentowy element betonowy tworzący płaskie posadowienie budynku. Jednakże, system prefabrykowanego fundamentu może składać się z wielu współpracujących komponentów, dopasowanych do specyficznych potrzeb projektu.
Głównym elementem jest oczywiście sama płyta. Jest to betonowy panel z zatopionym zbrojeniem, odlewany w fabryce z precyzyjnie dobranych mieszanek betonu o wysokich parametrach. Jej grubość i konfiguracja zbrojenia są kalkulowane indywidualnie pod obciążenia od budynku i właściwości gruntu.
Płyta może być jednolita lub składać się z kilku segmentów łączonych na placu budowy. Segmentacja jest konieczna przy bardzo dużych obiektach lub w przypadku ograniczeń transportowych.
Integralną częścią wielu nowoczesnych prefabrykowanych płyt fundamentowych jest izolacja termiczna. Najczęściej stosuje się twarde płyty izolacyjne, takie jak polistyren ekstrudowany (XPS) lub poliizocyjanurat (PIR), o wysokiej wytrzymałości na ściskanie i niskim współczynniku przewodzenia ciepła.
Izolacja ta może być ułożona pod całą płytą (tzw. "ciepła płyta fundamentowa") oraz jako izolacja pionowa na krawędzi płyty, tworząc tzw. "upstand" lub "spódnicę", która eliminuje mostek termiczny na styku ściany fundamentowej z gruntem. Typowe grubości izolacji wynoszą od 100 mm do 250 mm lub więcej w przypadku budynków pasywnych.
Zbrojenie wewnątrz płyty to kluczowy element konstrukcyjny, zapewniający jej wytrzymałość na zginanie i ścinanie. Stosuje się wysokiej jakości stal zbrojeniową (np. klasy A-IIIN), ułożoną w formie siatek lub prętów zgodnie z projektem. Dokładność ułożenia zbrojenia w prefabrykacie, często osiągana dzięki zautomatyzowanym procesom, jest znacznie wyższa niż przy zbrojeniu na placu budowy.
Elementy pomocnicze wbudowane w płytę obejmują różnego rodzaju przepusty i kanały instalacyjne. Mogą to być rury osłonowe na kable elektryczne, przepusty na rury wodne czy kanalizacyjne, które są zatopione w betonie dokładnie w miejscach wskazanych w projekcie.
Minimalizuje to konieczność późniejszego kucia w gotowej płycie i znacznie ułatwia prace instalacyjne na placu budowy.
Na krawędziach prefabrykowanych płyt mogą być także fabrycznie wbudowane elementy montażowe. Mogą to być kotwy (np. gwintowane), które ułatwiają szybkie mocowanie ścian prefabrykowanych, konstrukcji stalowych czy innych elementów budowlanych do fundamentu.
Czasami stosuje się również zintegrowane profile lub blachy, służące jako baza do montażu stolarki okiennej i drzwiowej na poziomie "zero", co poprawia szczelność i izolacyjność detalu.
Choć "płaskie" panele stanowią trzon systemu, dostawcy rozwiązań prefabrykowanych często oferują także inne elementy fundamentowe wykonane w tej technologii, które mogą być stosowane w połączeniu z płytą lub jako alternatywa w specyficznych przypadkach.
Wymienione "elementy: – płaskie – w formie słupów – formie stoposłupów – kielichowe – z wyprowadzonymi kotwami montażowymi lub bez – z możliwością wykonania dodatkowej izolacji w formie powłoki bitumicznej" opisują szerszą gamę prefabrykowanych elementów konstrukcji nośnych, które *mogą* być posadowione na prefabrykowanej płycie lub stanowić jej wsparcie.
Przykładowo, prefabrykowane stopy fundamentowe lub kielichy (do osadzania słupów) mogą być stosowane tam, gdzie wymagane jest punktowe przeniesienie bardzo dużych obciążeń, choć w typowym budynku jednorodzinnym płyta fundamentowa przenosi obciążenia równomiernie na całej powierzchni. Płyta prefabrykowana może być również fundamentem pod takie elementy.
Powłoka bitumiczna, jako opcja dodatkowej izolacji, jest stosowana na zewnętrznych powierzchniach płyty lub jej krawędziach (upstandach) w celu zapewnienia wodoszczelności i ochrony betonu przed wilgocią gruntową. Jest to dodatkowe zabezpieczenie, stosowane w zależności od warunków gruntowych i projektu.
Podsumowując, prefabrykowana płyta fundamentowa to zaawansowany technologicznie produkt, który jest znacznie więcej niż tylko "płytą betonu". To kompleksowy element, często integrujący zbrojenie, izolację, przepusty instalacyjne i punkty montażowe, zaprojektowany i wykonany z najwyższą precyzją, stanowiący gotową bazę dla całej dalszej budowy. To mistrzowskie dzieło inżynierii betonowej.
Różnorodność elementów składowych i opcji konfiguracji sprawia, że technologia ta jest elastyczna i może być dostosowana do wielu typów budynków i warunków gruntowych. Kluczem jest ścisła współpraca z producentem na etapie projektowania, aby wykorzystać pełen potencjał prefabrykacji.
Nowoczesne płyty prefabrykowane mogą być nawet wyposażone w systemy kapilarne czy rury ogrzewania podłogowego zatopione już w betonie, co dodatkowo przyspiesza prace na budowie i optymalizuje system grzewczy.
Cała ta złożoność elementów i procesu produkcji przekłada się na produkt końcowy o wyższej, bardziej przewidywalnej jakości niż rozwiązania tworzone w mniej kontrolowanych warunkach na placu budowy. To siła industrializacji w służbie budownictwa.
Kiedy Warto Wybrać Prefabrykowaną Płytę Fundamentową?
Decyzja o wyborze technologii fundamentowej to jeden z kluczowych momentów w procesie inwestycyjnym. Kiedy zatem prefabrykowane płyty fundamentowe stają się nie tylko opcją, ale wręcz optymalnym, a czasem nawet jedynym rozsądnym wyborem? Tekst w danych wejściowych podaje prostą odpowiedź: są idealne "dla projektów budowlanych wymagających efektywności i trwałości". Rozwińmy to, bo "efektywność" i "trwałość" w budownictwie to pojęcia pojemne.
Przede wszystkim, prefabrykacja shines brightest, gdy czas jest kluczowy. Jeśli harmonogram budowy jest bardzo napięty – czy to ze względu na zobowiązania inwestora, sezon budowlany, czy pilną potrzebę oddania obiektu do użytku – szybkość montażu płyty prefabrykowanej (mierzoną w dniach, nie tygodniach) jest nie do przecenienia. W projektach komercyjnych, gdzie każdy dzień opóźnienia generuje straty, jest to argument ważący najwięcej.
Pomyślmy o sieciach handlowych, magazynach czy obiektach produkcyjnych – szybkość uruchomienia działalności gospodarczej na nowej lokalizacji jest wprost proporcjonalna do tempa budowy. Tu prefabrykacja fundamentu staje się akceleratorem całego przedsięwzięcia.
Po drugie, w przypadku projektów o wysokich wymaganiach dotyczących precyzji wykonania. Wspomniana wcześniej fabryczna dokładność prefabrykatów (tolerancja wymiarowa rzędu milimetrów) jest trudna do osiągnięcia na placu budowy przy metodach tradycyjnych. Jest to kluczowe w budynkach, gdzie wymaga się idealnie równej i poziomej posadzki – np. w halach przemysłowych z posadzkami wysokoregałowymi, na których precyzja ruchu wózków widłowych ma znaczenie, czy w obiektach z technologiami wymagającymi stabilnego i równego podłoża, jak serwerownie.
Trwałość rozumiana jako jakość materiału i wykonania również odgrywa rolę. Beton o wysokich parametrach, odlewany i pielęgnowany w kontrolowanych warunkach, oraz precyzyjnie ułożone zbrojenie, dają fundament, który jest mniej podatny na wady wykonawcze i zapewnia długowieczność konstrukcji.
Warto wybrać prefabrykowaną płytę fundamentową w trudnych warunkach gruntowych. Choć sama płyta nie zastąpi głębokiego posadowienia na palach w przypadku bardzo słabych gruntów, jej stosunkowo niewielka głębokość posadowienia (minimalny wykop) i równomierny rozkład obciążeń na dużej powierzchni mogą być korzystne na gruntach o umiarkowanej nośności, ale np. niejednorodnych, czy zlokalizowanych płytko pod powierzchnią gruntu.
Jest to też świetne rozwiązanie na działkach z wysokim poziomem wód gruntowych, gdzie tradycyjne głębokie wykopy byłyby kosztowne i skomplikowane z uwagi na konieczność odwodnienia.
Domy energooszczędne i pasywne to kolejny obszar, gdzie prefabrykowana płyta fundamentowa z zintegrowaną izolacją termiczną sprawdza się znakomicie. Umożliwia ona łatwe osiągnięcie bardzo niskich współczynników przenikania ciepła dla przegrody fundamentowej, co jest krytyczne dla bilansu energetycznego budynku.
Eliminacja mostków termicznych na styku fundamentu ze ścianą parteru jest znacznie prostsza i bardziej efektywna w przypadku "ciepłej" płyty prefabrykowanej, gdzie izolacja jest integralną częścią elementu.
Projekty z rozbudowanym systemem ogrzewania podłogowego to również idealny kandydat na prefabrykowaną płytę. Rury grzewcze mogą być precyzyjnie umieszczone i zatopione w górnej warstwie betonu już na etapie produkcji w fabryce. To nie tylko przyspiesza prace na placu, ale także zapewnia optymalne rozłożenie rur i efektywność systemu grzewczego.
Czystość i organizacja placu budowy. Jeśli inwestorowi zależy na minimalizacji bałaganu, redukcji ilości "mokrych" prac i odpadów na placu budowy, prefabrykacja jest oczywistym wyborem. Zamiast żwirowania, szalowania, zbrojenia, wylewania i czyszczenia betoniarki, mamy przede wszystkim operacje dźwigowe i montażowe, które generują nieporównywalnie mniej nieporządku.
Wreszcie, przewidywalność kosztów. Chociaż początkowy koszt zakupu prefabrykowanej płyty może wydawać się wyższy niż tradycyjnego rozwiązania (np. 400-700 zł/m² netto w zależności od grubości, izolacji i skomplikowania, wliczając projekt i montaż, podczas gdy tradycyjnie może to być 250-450 zł/m² samego materiału i robocizny w sprzyjających warunkach), całkowity koszt projektu może być niższy. Składają się na to oszczędności wynikające z szybszej budowy (mniej roboczodni, szybsze zakończenie inwestycji), mniejszych prac ziemnych, redukcji prac wykończeniowych posadzki (bo powierzchnia jest idealnie równa) oraz mniejszych strat materiałowych.
Podsumowując, prefabrykowana płyta fundamentowa jest rozwiązaniem, które powinno być rozważone, gdy kluczowe są: czas realizacji, wysoka precyzja, specyficzne warunki gruntowe (ale nie ekstremalnie trudne), wysokie wymagania termoizolacyjne, chęć zminimalizowania prac "mokrych" na placu budowy oraz optymalizacja całego procesu budowlanego pod kątem efektywności i przewidywalności.
To technologia dla wymagających inwestorów, którzy widzą wartość w industrializacji procesu budowlanego i stawiają na jakość potwierdzoną kontrolą fabryczną, a nie tylko kunsztem ekipy budowlanej na placu.
Warto pamiętać, że decyzja o wyborze prefabrykowanej płyty powinna być poprzedzona dokładną analizą warunków gruntowych i specyficznych wymagań projektowych przez doświadczonego projektanta konstrukcji, najlepiej w ścisłej współpracy z przedstawicielem producenta płyt prefabrykowanych.
To gwarantuje, że rozwiązanie będzie optymalnie dopasowane i wykorzysta wszystkie swoje zalety, zapewniając trwałe i solidne posadowienie na długie lata. Nie jest to rozwiązanie uniwersalne do zastosowania wszędzie bez namysłu, ale tam gdzie pasuje, zmienia zasady gry.
Mówiąc wprost – jeśli zależy Ci na tempie, jakości klasy premium i czystości na placu budowy, prefabrykowana płyta fundamentowa powinna znaleźć się na szczycie listy Twoich rozważań. To fundament budowany na miarę XXI wieku.
Precyzja pozwala na uniknięcie wielu późniejszych problemów i dodatkowych kosztów związanych z nierównościami czy niedokładnościami. Warto o tym pamiętać przy kalkulacji opłacalności wyboru tej technologii.