Podbudowa pod płytę fundamentową: Kompletny Przewodnik
Zaczynamy od fundamentów, dosłownie i w przenośni. Zanim budynek wzbije się w górę, zanim pojawią się ściany i dach, wszystko zaczyna się od tego, co niewidoczne, a absolutnie kluczowe: podbudowa pod płytę fundamentową. Czym jest w skrócie? To nic innego jak starannie przygotowana warstwa, a częściej system warstw, umieszczona bezpośrednio pod żelbetową płytą, mająca za zadanie równomierne rozłożenie obciążeń z budynku na grunt, zapobieganie osiadaniu i zapewnienie stabilnego, trwałego posadowienia.
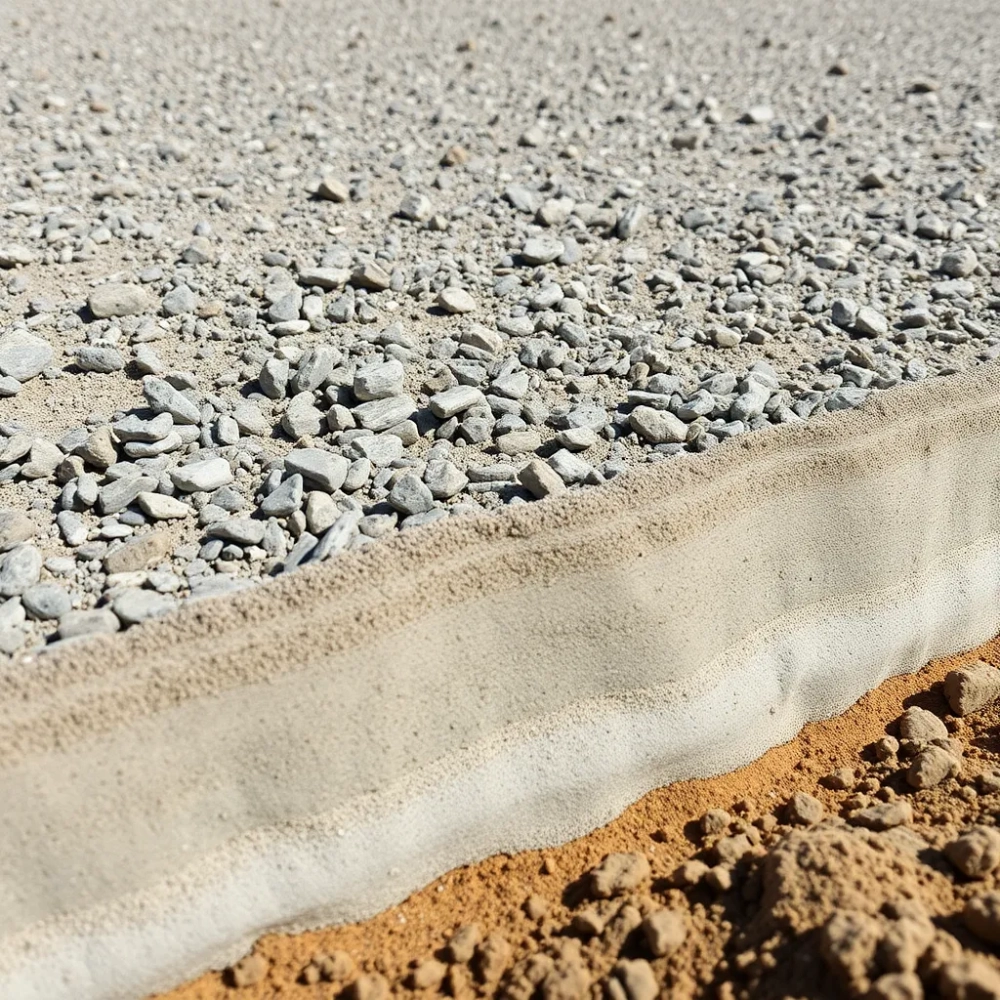
Patrząc na proces budowy domu, można by pomyśleć, że wylanie betonu na ziemię to bułka z masłem. Cóż, praktyka brutalnie weryfikuje takie myślenie. Poniżej przedstawiamy dane zebrane na hipotetycznym przykładzie budowy jednorodzinnego domu o powierzchni 150 m², pokazujące orientacyjny udział różnych kosztów w przygotowaniu terenu i wykonaniu samej podbudowy, abstrahując na razie od kosztu samej płyty żelbetowej.
Element | Orientacyjny koszt jednostkowy | Szacunkowa ilość | Łączny orientacyjny koszt |
---|---|---|---|
Badania geotechniczne | 2000 - 4000 PLN (za projekt) | 1 projekt | 2000 - 4000 PLN |
Usunięcie humusu i niwelacja | 20 - 40 PLN/m² | 150 - 200 m² | 3000 - 8000 PLN |
Zakup kruszywa (np. 0/31.5 mm) | 60 - 100 PLN/tona | 40 - 60 ton | 2400 - 6000 PLN |
Transport kruszywa | 8 - 15 PLN/tona/km (zależnie od odległości) | 40 - 60 ton | 320 - 900 PLN (przy 10 km) |
Robocizna - układanie i zagęszczanie | 15 - 25 PLN/m² | 150 - 200 m² | 2250 - 5000 PLN |
Analizując powyższe, staje się jasne, że etap przygotowania podłoża i podbudowy to znaczący wydatek, który potrafi pochłonąć nawet kilkanaście procent całkowitych kosztów stanu zero. Wartość tę mogą dodatkowo winduje konieczność wymiany gruntu, stabilizacji chemicznej czy budowa rozbudowanego systemu drenażu, co pokazuje, że ignorowanie lub bagatelizowanie tego etapu to prosta droga do problemów finansowych i technicznych w przyszłości.
Te pozornie prozaiczne koszty składają się na skomplikowany proces, który wymaga precyzji, odpowiednich materiałów i rzetelnego wykonania. Każdy z tych elementów ma bezpośredni wpływ na długowieczność i stabilność konstrukcji. To inwestycja, która zwraca się w postaci spokoju ducha przez lata użytkowania budynku, a próba szukania tu oszczędności bywa zazwyczaj wyjątkowo kosztowną lekcją pokory wobec praw fizyki i geotechniki.
Przygotowanie terenu i podłoża pod podbudowę
Zaczynamy naszą opowieść od placu budowy. Wiele inwestorów widzi tu tylko przestrzeń, na której stanie dom marzeń, ale dla nas, specjalistów, to otwarta księga geologiczna i teren do rzetelnego przygotowania. Pierwszym, absolutnie krytycznym krokiem jest badanie gruntu - nie ma mowy o budowie bez profesjonalnego raportu geotechnicznego, który powie nam, co "siedzi" pod przyszłą płytą fundamentową. Wyobraźmy sobie, że fundament postawiony zostanie na iłach wysadzinowych lub słabonośnych nasypach, skutki mogą być opłakane i bardzo kosztowne w naprawie.
Kiedy już znamy rodzaje i parametry gruntu, przechodzimy do fizycznego przygotowania terenu. To obejmuje usunięcie roślinności, drzew, krzewów oraz, co niezwykle ważne, ściągnięcie warstwy humusu, czyli urodzajnej ziemi wierzchniej. Humus jest nieodpowiedni jako podłoże pod konstrukcję ze względu na jego organiczny charakter i zmienną objętość w zależności od wilgotności. Standardowo usuwa się od 20 do 40 cm tej warstwy, choć precyzyjna głębokość zależy od jej faktycznej grubości, potwierdzonej choćby podczas badań geotechnicznych, które czasami wykonuje się z wyprzedzeniem.
Kolejnym etapem jest wytyczenie obrysu przyszłej płyty i wykonanie wykopu do projektowanej rzędnej. Głębokość wykopu zależy od poziomu posadowienia, który jest ustalany na podstawie wspomnianego raportu geotechnicznego i analizy warunków gruntowych. Często wystarczy usunąć humus, ale w przypadku gruntów nienośnych lub organicznych, konieczna może być głębsza interwencja, polegająca na usunięciu nieodpowiedniego gruntu i zastąpieniu go materiałem konstrukcyjnym, na przykład pospółką lub kruszywem. To właśnie w tym momencie zapada kluczowa decyzja o zakresie robót ziemnych, która ma fundamentalne znaczenie dla stabilności przyszłej konstrukcji.
Następnie przystępujemy do wyrównania i wstępnego zagęszczenia podłoża gruntowego pod przyszłą podbudowę. Podłoże to musi być stabilne i jednolite. Jeżeli grunt rodzimy, pozostały po usunięciu słabych warstw, jest odpowiedniej jakości (np. zagęszczone piaski, gliny zwarte), wystarczy go wyrównać i odpowiednio zagęścić za pomocą walca lub zagęszczarki wibracyjnej, często kontrolując stopień zagęszczenia np. sondą dynamiczną. Celem jest uzyskanie minimalnej wymaganej nośności, często określanej w projekcie geotechnicznym lub konstrukcyjnym na podstawie norm.
Jeśli badania wykażą obecność gruntów słabonośnych lub istnieje ryzyko występowania lokalnych zagłębień z nieodpowiednim materiałem, może być konieczna wymiana gruntu w określonym zakresie. Ten proces polega na wybraniu gruntu do wymaganej głębokości i zastąpieniu go materiałem dobrze zagęszczalnym, takim jak piasek gruby, pospółka, mieszanki kruszyw. Grubość wymienianej warstwy może wynosić od kilkudziesięciu centymetrów do nawet kilku metrów w skrajnych przypadkach, a to znacząco wpływa na koszt inwestycji, jak pokazały nasze przykładowe dane w tabeli. Zagęszczenie tego nowo ułożonego materiału jest równie ważne jak gruntu rodzimego.
Czasem spotykamy się z terenami, gdzie wymiana gruntu na dużą skalę jest nieopłacalna lub technicznie trudna. W takich sytuacjach stosuje się metody wzmacniania podłoża, np. kolumny DSM (Deep Soil Mixing), kolumny betonowe czy pale. Są to zaawansowane techniki, które "przewiercają" się przez słabe warstwy, opierając się na mocniejszych poziomach gruntu lub tworząc kompozytowy, bardziej nośny materiał. Decyzja o ich zastosowaniu zapada na etapie projektowania i jest poprzedzona bardzo szczegółowymi badaniami geotechnicznymi. To pokazuje, że przygotowanie podłoża to nie tylko "kopanie dziury", ale złożony proces inżynierski.
Po wyrównaniu i zagęszczeniu docelowej rzędnej podłoża pod podbudowę, często rozkłada się warstwę geowłókniny. Materiał ten pełni kilka istotnych funkcji: separuje grunt rodzimy (lub grunt wymieniony) od materiałów przyszłej podbudowy, zapobiegając mieszaniu się warstw. Dzięki temu warstwy konstrukcyjne podbudowy zachowują swoje projektowane właściwości i granulację. Geowłóknina pełni również funkcję filtracyjną, umożliwiając odpływ wody, a jednocześnie zatrzymując drobne cząstki gruntu, co jest szczególnie ważne w przypadku gruntów spoistych lub drobnoziarnistych.
Równość powierzchni po geowłókninie jest kluczowa dla dalszych prac. Musi być ona płaska i zgodna z projektem, bez lokalnych zagłębień czy garbów. Precyzja na tym etapie rzutuje na jednorodność grubości warstw podbudowy i ostatecznie na jakość wykonania płyty fundamentowej. Można powiedzieć, że przygotowanie terenu i podłoża to fundament pod fundament, a każde niedociągnięcie w tej fazie będzie miało długofalowe konsekwencje dla całej konstrukcji. Ignorowanie zaleceń geotechnika to gra w rosyjską ruletkę z własnym domem.
Materiały i ich właściwości dla poszczególnych warstw podbudowy
Kiedy podłoże gruntowe jest już odpowiednio przygotowane i zagęszczone, pora na "serce" naszej opowieści, czyli same warstwy podbudowy pod płytę fundamentową. Wybór i właściwości materiałów wchodzących w skład podbudowy są absolutnie kluczowe dla jej funkcji nośnej i trwałości. Nie jest to przypadkowy zbiór kamieni czy piasku, ale starannie dobrany system, często składający się z kilku warstw, z których każda ma swoją specyficzną rolę i wymagania.
Typowa struktura podbudowy zaczyna się od warstwy nośnej, najczęściej wykonanej z kruszywa łamanego. Jest to materiał o ostrych, krawędziastych ziarnach, który po zagęszczeniu klinuje się, tworząc stabilną i sztywną matę. Frakcja kruszywa jest niezwykle ważna – często stosuje się kruszywo o frakcji 0/31.5 mm lub 0/63 mm. Kruszywo 0/31.5 mm dobrze się klinuje i jest stosowane jako warstwa zasadnicza. Właściwości takiego kruszywa to przede wszystkim wysoka wytrzymałość na ściskanie i ścieranie, mrozoodporność (kluczowa cecha!), oraz niski stopień rozdrabniania. Musi być to kruszywo o udokumentowanym pochodzeniu, spełniające wymagania norm budowlanych.
Grubość warstwy kruszywa łamanego zależy od obliczeń projektowych i obciążeń, ale w budownictwie jednorodzinnym typowo wynosi od 20 do 30 cm, choć w przypadku słabszych gruntów i większych obciążeń może być znacznie grubsza, osiągając nawet 50-60 cm w jednej lub kilku warstwach. Każda taka warstwa jest układana i intensywnie zagęszczana, co omówimy szerzej w kolejnym rozdziale. Dobrze zagęszczone kruszywo charakteryzuje się wysokim modułem odkształcenia (np. Ev2 > 80-100 MPa, zależnie od wymagań) i minimalną dalszą odkształcalnością pod obciążeniem, co gwarantuje stabilność pod płytą.
Na warstwie nośnej z kruszywa łamanego, często układa się cieńszą warstwę wyrównawczą, np. z pospółki lub piasku gruboziarnistego, o frakcji do 8 mm. Warstwa ta ma za zadanie stworzyć idealnie równą powierzchnię pod kolejne warstwy lub bezpośrednio pod chudy beton czy hydroizolację. Choć jej nośność jest mniejsza niż warstwy zasadniczej z kruszywa, jest łatwiejsza w precyzyjnym wyrównaniu i zagęszczeniu do odpowiedniej rzędnej. Jej grubość zazwyczaj mieści się w przedziale 5-10 cm i również wymaga starannego zagęszczenia.
Kolejną typową warstwą, zwłaszcza w przypadku płyt na gruncie, jest tzw. chudy beton (beton podkładowy). Nie jest to element konstrukcyjny przenoszący obciążenia w rozumieniu żelbetu, ale warstwa technologiczna. Jej główne funkcje to stworzenie sztywnego i równego podłoża pod ułożenie hydroizolacji poziomej (membrany, folii PVC, papy termozgrzewalnej) i przyszłego zbrojenia płyty fundamentowej. Bez tej warstwy, folia łatwo uległaby uszkodzeniu przez ostre krawędzie kruszywa podczas układania zbrojenia i betonowania, a rozkładanie siatki czy prętów byłoby znacznie utrudnione. Standardowo stosuje się chudy beton klasy C8/10 lub C10/12, o grubości 10 do 15 cm.
Hydroizolacja pozioma, układana na chudym betonie, to kolejny kluczowy element systemu podbudowy pod płytę fundamentową. Jej celem jest odcięcie kapilarnego podciągania wody z gruntu do konstrukcji płyty. W zależności od wymagań projektowych i warunków wodnych na działce, stosuje się różne materiały – od grubych folii polietylenowych (choć ich trwałość i skuteczność bywają dyskusyjne w dłuższej perspektywie), przez papy termozgrzewalne (jedna lub dwie warstwy), aż po specjalistyczne membrany bitumiczne lub z PVC. Dobór materiału i sposób jego ułożenia (np. zakładów, wywinięć na obrys płyty) jest podyktowany projektem i powinien być wykonany z najwyższą starannością, bo przebicie hydroizolacji to niemal pewny problem z wilgocią w przyszłości.
Czasem pod chudym betonem, a nad warstwą kruszywa, stosuje się dodatkowo folię kubełkową lub drugą warstwę geowłókniny. Folia kubełkowa tworzy pustkę powietrzną, ułatwiając drenaż, natomiast geowłóknina jak już wspomniano, poprawia filtrację i separację. Wszystko to ma na celu zapewnienie suchości i stabilności podbudowy. To trochę jak ubieranie się na cebulkę - każda warstwa ma swój cel, a pominięcie którejś może osłabić cały system. Właściwy dobór właściwych materiałów jest tak samo ważny, jak ich rzetelne ułożenie i zagęszczenie, o czym za moment.
Układanie i zagęszczanie warstw podbudowy
Sama obecność właściwych materiałów na budowie to dopiero połowa sukcesu; drugą i wcale nie mniej ważną połową jest sposób ich ułożenia i, przede wszystkim, zagęszczenia. Układanie warstw podbudowy pod płytę fundamentową wymaga metodycznego podejścia. Materiał jest dowożony na plac budowy i rozprowadzany równomiernie na przygotowanym podłożu. Kluczowe jest kontrolowanie grubości każdej układanej warstwy już na etapie jej rozrzucania. Nadmierna grubość utrudnia skuteczne zagęszczenie na całej głębokości warstwy, prowadząc do nierównomiernej nośności, która jest wrogiem stabilnej płyty.
Zagęszczanie to proces, w którym dzięki mechanicznemu działaniu (naciskowi i wibracji) zmniejszamy objętość gruntu lub kruszywa, usuwając z niego powietrze i wodę. Celem jest ułożenie ziaren jak najbliżej siebie, zwiększając ich wewnętrzne tarcie i klinowanie. Tylko poprawnie wykonana podbudowa, czyli dobrze zagęszczona, będzie w stanie przenieść projektowane obciążenia bez nadmiernych osiadań. Wykorzystuje się do tego różnego rodzaju sprzęt: zagęszczarki wibracyjne (stopowe, płytowe) dla mniejszych powierzchni lub cienkich warstw oraz walce wibracyjne o różnej masie dla większych obszarów i grubszych warstw. Im cięższy sprzęt i silniejsza wibracja, tym skuteczniejsze zagęszczenie osiągniemy, ale musi być on dobrany do rodzaju zagęszczanego materiału i grubości warstwy.
Każda warstwa podbudowy, czy to kruszywo, czy piasek, jest układana w odpowiednich grubościach, zazwyczaj nie przekraczających 20-30 cm (choć zależy to od sprzętu i materiału), a następnie zagęszczana aż do uzyskania wymaganego stopnia zagęszczenia. Jak to się kontroluje w praktyce? Najczęściej wykonuje się badania nośności podbudowy, np. badanie płytą VSS (obciążenie statyczne), które mierzy odkształcenie podłoża pod zadanym obciążeniem. Wynikiem jest moduł odkształcenia Ev1 (przy pierwszym obciążeniu) i Ev2 (przy drugim obciążeniu) oraz ich stosunek Ev2/Ev1, świadczący o sprężystości. Projekt budowlany lub geotechniczny określa minimalne wymagane wartości tych parametrów (np. Ev2 > 80-100 MPa i Ev2/Ev1 < 2.2), które muszą zostać osiągnięte na powierzchni zagęszczonej warstwy. Czasem stosuje się też sondę dynamiczną.
Nie można pominąć wilgotności materiału podczas zagęszczania. Zarówno zbyt suchy, jak i zbyt mokry materiał będzie się gorzej zagęszczał. Dla kruszyw optymalna wilgotność ułatwia przemieszczanie się ziaren i ich ułożenie, natomiast nadmiar wody działa jak smar lub poduszka, uniemożliwiając prawidłowe klinowanie. Fachowcy "czują" materiał i wiedzą, kiedy wymaga on delikatnego zroszenia. W przypadku gruntów spoistych (np. gliny), istnieje optymalna wilgotność, przy której można osiągnąć maksymalną gęstość objętościową. Zazwyczaj określa się ją w badaniu Proctora. Stąd, kontrola i ewentualna korekta wilgotności to część procesu zagęszczania, zwłaszcza przy wykorzystaniu gruntu rodzimego do podbudowy lub jego wymianie.
Precyzja w rzędnych to kolejny aspekt, o którym nie wolno zapomnieć. Po zagęszczeniu każdej warstwy, a zwłaszcza warstwy docelowej (pod chudy beton lub hydroizolację), jej powierzchnia musi być wyrównana do projektowanej rzędnej z niewielką tolerancją, np. +/- 1-2 cm. Osiągnięcie tej precyzji wymaga doświadczenia i umiejętnego operowania sprzętem do rozprowadzania (spycharki, równiarki) oraz ręcznego korygowania. Wszelkie odchylenia rzutują na grubości kolejnych warstw i finalnej płyty, co może wpłynąć na jej właściwości konstrukcyjne i zużycie betonu, a to już prosta matematyka przekładająca się na koszty, jak te, które zobaczyliśmy w tabeli na początku.
Podsumowując, układanie i zagęszczanie warstw podbudowy to nie "wsyp i rozjedź". To metodyczny proces wymagający kontroli grubości warstw, doboru odpowiedniego sprzętu wibracyjnego, utrzymania optymalnej wilgotności materiału i, co najważniejsze, weryfikacji efektów zagęszczenia za pomocą badań polowych. Tylko ścisłe przestrzeganie tych zasad i wymagań projektowych gwarantuje uzyskanie stabilnego podłoża dla płyty fundamentowej, minimalizując ryzyko nierównomiernego osiadania, które jest prawdziwym koszmarem każdego inwestora i konstruktora. "Acha, to tylko kruszywo" - to zdanie, które u prawdziwego specjalisty wywołuje jedynie pobłażliwy uśmiech i myśl o kosztownych pomyłkach.
Funkcje dodatkowe: drenaż i termoizolacja w podbudowie
Podbudowa pod płytę fundamentową to nie tylko warstwy kruszyw i betonu podkładowego służące przenoszeniu obciążeń. Nowoczesne budownictwo stawia przed nią dodatkowe, kluczowe funkcje związane z komfortem użytkowania i energooszczędnością. Mówimy tu przede wszystkim o ochronie przed wilgocią i mrozem za pomocą systemów drenażowych oraz o zapewnieniu odpowiedniej izolacji termicznej, często integrowanej bezpośrednio w układzie podbudowy lub pod płytą.
Zacznijmy od drenażu. Woda w gruncie to potencjalny problem dla każdego fundamentu. Podsiąkanie kapilarne, wysoki poziom wód gruntowych czy po prostu wody opadowe przenikające w głąb ziemi mogą prowadzić do nawodnienia warstw podbudowy, a w skrajnych przypadkach do występowania ciśnienia hydrostatycznego pod płytą. Mokre kruszywo traci swoje właściwości nośne, a w zimie grozi to wysadzaniem mrozowym – woda zamarzając, zwiększa objętość, co może "wypychać" konstrukcję do góry. System drenażu ma za zadanie aktywne odprowadzanie nadmiaru wody z obszaru podbudowy i bezpośrednio wokół fundamentu.
Najczęściej stosowanym rozwiązaniem jest wykonanie warstwy drenującej bezpośrednio pod warstwą nośną podbudowy (np. z grubszego kruszywa o jednorodnej frakcji, np. 8/16 mm, 16/32 mm, które ma duże pory) lub na samej granicy podłoża gruntowego. W tej warstwie umieszcza się rury drenażowe – specjalne, perforowane rury otoczone obsypką filtracyjną (żwir, otoczaki) i często owinięte geowłókniną, zapobiegającą zamulaniu otworów perforacyjnych przez drobne cząstki gruntu. Rury te układa się ze spadkiem, kierując wodę do studzienek kontrolnych i dalej poza obrys budynku, np. do studni chłonnej, rowu melioracyjnego czy kanalizacji deszczowej (jeśli lokalne przepisy na to pozwalają).
Geowłókniny w systemach drenażowych pełnią kluczową rolę jako filtry. Oddzielają kruszywo drenujące i rury od drobnych cząstek gruntu spoistego, zapobiegając ich migracji i zapychaniu systemu. Prawidłowo zaprojektowany i wykonany drenaż jest polisą na życie dla fundamentu w trudnych warunkach wodnych. Jego brak w miejscu, gdzie poziom wód gruntowych jest wysoki lub grunt jest słabo przepuszczalny (np. gliny), może prowadzić do nieodwracalnych uszkodzeń konstrukcji fundamentu na przestrzeni lat. Wykonanie takiego drenażu generuje dodatkowe koszty, np. rury drenażowe to wydatek rzędu 5-15 PLN/mb, studzienki kontrolne kilkaset złotych sztuka, a materiał obsypki (kruszywo płukane) to dodatkowe 60-100 PLN/tona.
Drugim istotnym elementem dodatkowym, coraz częściej spotykanym, jest termoizolacja płyty fundamentowej. Ma ona na celu zminimalizowanie strat ciepła do gruntu, który zimą stanowi olbrzymi "odbiornik" ciepła z budynku, a latem potencjalnie pomaga w jego chłodzeniu, ale ogólny bilans energetyczny dla dobrze zaizolowanego budynku w naszej strefie klimatycznej skłania do izolowania podłogi na gruncie. Tradycyjnie izolację układa się na chudym betonie, bezpośrednio pod płytą konstrukcyjną. Stosuje się materiały o wysokiej wytrzymałości na ściskanie i niskim współczynniku przenikania ciepła λ (Lambda).
Klasycznym wyborem są płyty z polistyrenu ekstrudowanego XPS lub styropianu fundamentowego EPS o bardzo niskiej nasiąkliwości i dużej gęstości. Grubość izolacji zależy od wymagań projektowych i standardów energetycznych (np. warstwa 20 cm XPS o λ ok. 0.035 W/mK lub 30 cm EPS o λ ok. 0.036 W/mK to często spotykane rozwiązania dla domów energooszczędnych, podczas gdy dla pasywnych potrzeba jej jeszcze więcej, np. 40 cm). Płyty te muszą mieć odpowiednią wytrzymałość na ściskanie (np. minimum 300-500 kPa) aby przenieść obciążenia z płyty i budynku. Koszt takich materiałów to orientacyjnie 400-700 PLN/m³ zależnie od typu i producenta.
Interesującą alternatywą, na którą zwrócono uwagę w materiale źródłowym, jest zastosowanie lekkiego betonu w systemie podbudowy, który pełni jednocześnie funkcję nośną i izolacyjną. Lekkie betony produkowane są np. z kruszyw keramzytowych, porowatego szkła (np. foam glass) lub na bazie specjalnych spoiw i wypełniaczy, uzyskując dużo niższe gęstości i znacznie lepsze parametry termoizolacyjne niż tradycyjny beton. Takie rozwiązanie upraszcza nieco proces budowy, redukując liczbę warstw, ale wymaga zastosowania specjalistycznych materiałów i technologii betonowania.
Ocieplenie płyty fundamentowej za pomocą lekkiego betonu oznacza, że nie potrzebujemy już osobnej warstwy XPS/EPS o znacznej grubości, choć precyzyjne właściwości izolacyjne zależą od konkretnego rodzaju lekkiego betonu (jego λ może wynosić od 0.08 W/mK dla tych o najlepszych właściwościach izolacyjnych do 0.3-0.5 W/mK dla mniej izolacyjnych, ale bardziej wytrzymałych typów). Wadą może być zazwyczaj niższa wytrzymałość mechaniczna niż tradycyjnego betonu konstrukcyjnego (wymaga przemyślanego projektowania grubości płyty konstrukcyjnej nad lekkim betonem) i często wyższy koszt materiału. Mimo to, w specyficznych projektach, takie rozwiązanie może być uzasadnione ekonomicznie i technicznie, oferując solidne, jednorodne podłoże gruntowe z wbudowaną izolacją. Decyzja o wyborze izolacji to kolejny kluczowy punkt na etapie projektowania podbudowy.